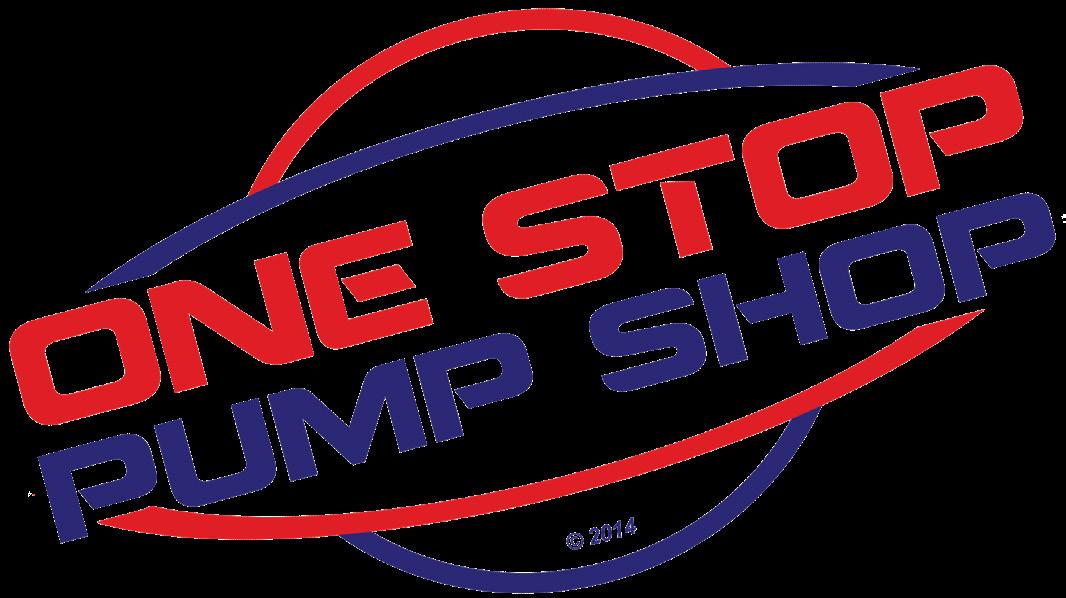
13 minute read
Landscape & External Works
Landscape & External Works GREAT, “OLD FASHIONED” SERVICE …….
Pump Technology Ltd., founded in 1992, is recognized as one of the UK’s leading independent pumps and pumping system specialists focusing on drainage, wastewater and sewage applications.
Advertisement
A true “One Stop Pump Shop” for specifiers and engineers, the company boasts a long serving, experienced team who will be able to discuss just about any pump solution requirement with customers. Ultimate pumping performance and reliability is reliant on correct pump selection and Pump Technology pride themselves on their, right-first-time, ethos. The team say they believe that their main tool is the telephone and, when it comes to understanding an application and having confidence in any purchase, talking always wins!
Avoiding the hassle of wrongly specified items, returns and confusion over missing accessories all contribute to being able to keep prices competitively low
Pump Technology say that this is what makes them a true market leader. They are recommended by the leading manufactures such as KSB, Lowara, Ebara, Dab, Flygt, Jung Pumpen, Saniflo etc. for the selection and supply of their equipment and hold possibly the largest and most varied stock of pumps in the UK. Orders placed before 3.30pm will be packed for next working day delivery with options for am and weekend shipping. Customers close enough to the warehouse in Aldermaston, Berkshire can always call in. Customers are learning that one call will identify a broken pump for replacement, ideally like for like, or if that model is superseded an equivalent for pumping performance and fit.

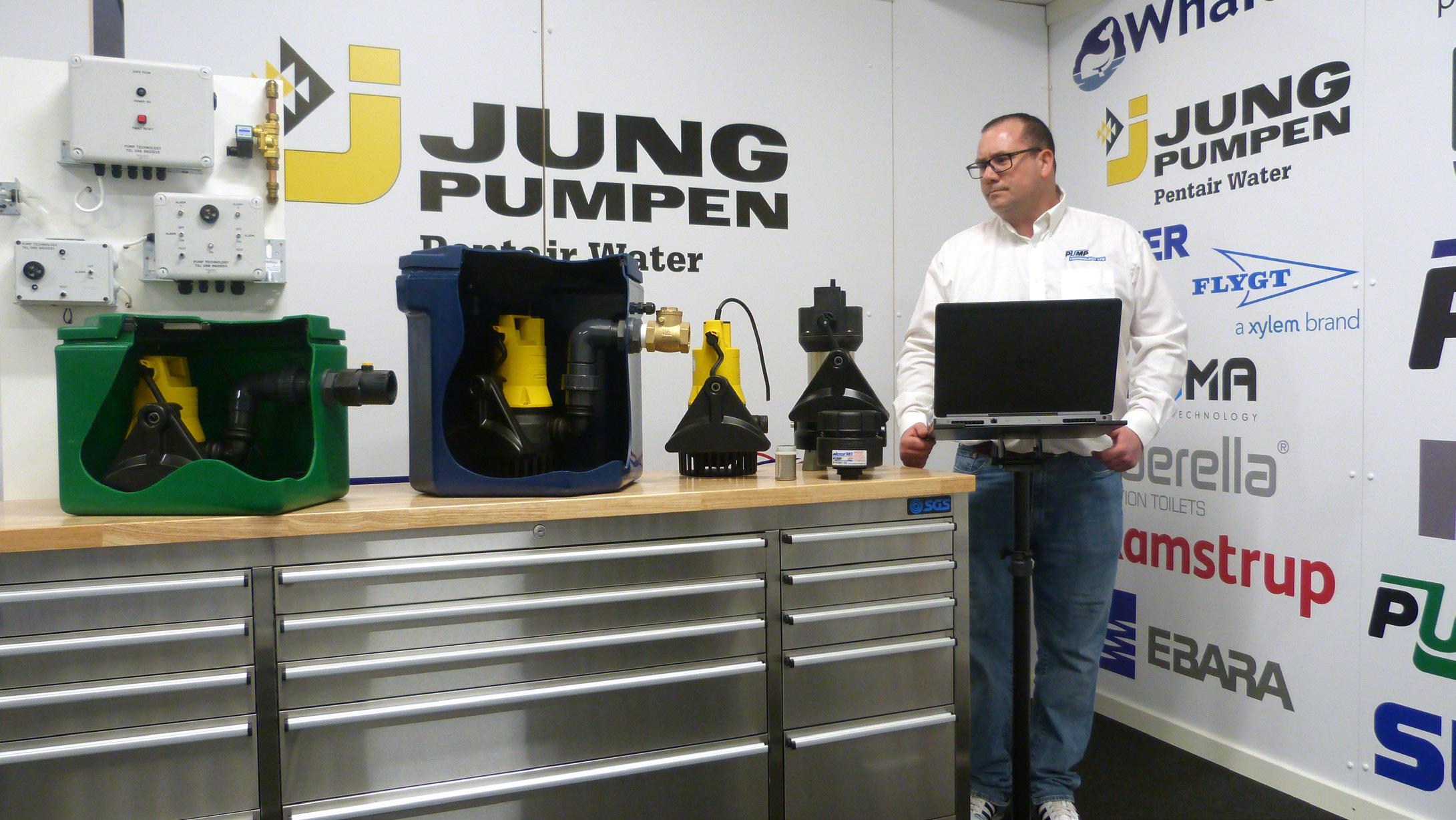
For new applications, typically pumping stations for basements, house extensions, garden rooms, warehouse, offices, public houses, local flooding solutions, emergency onsite pumps, the team will be happy to discuss and recommend suitable and always cost-effective solutions.
Additionally, the Pump Technology engineers will be happy to provide training for all of their products in their online showroom. This includes being able to remotely show customers the products they want to order and explaining about future applications or product solutions, exactly how they work and are maintained.
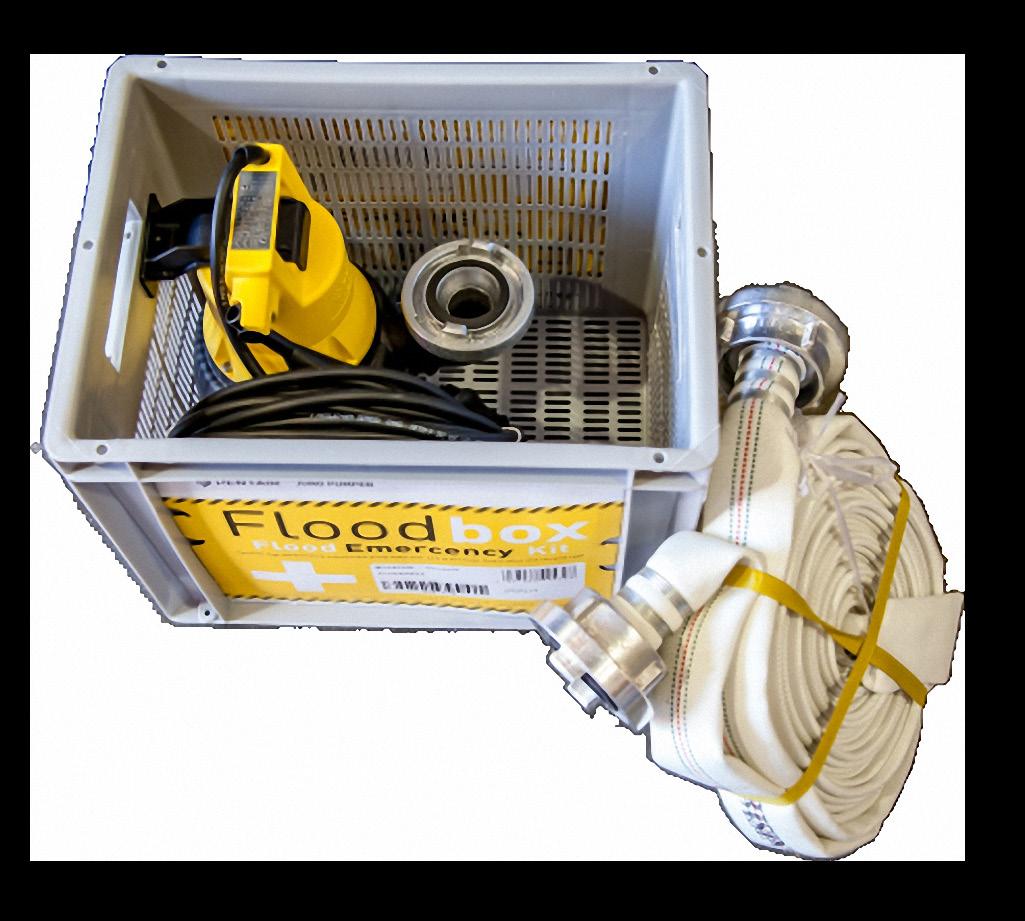
Current popular products include the MiniMatic below ground pumping station for house extensions and garden rooms. This consists of a 60L below ground tank with a single free-standing submersible sewage pump, high level alarm and cover with full installation and maintenance details.
Also, particularly at this time of year, the Floodbox, which is a “Self-contained”, emergency flood package for areas such as patios, warehouse floors, door-ways etc. is proving popular with house and business owners
More Information: Pump Technology Ltd 0118 9821 555 www.pumptechnology.co.uk
Landscape & External Works DURA PRODUCTS ANNOUNCE LIFE CYCLE ASSESSMENT RESULTS
Sustainable construction innovators, Dura Products, has today confirmed its sustainability credentials with the release of new Life Cycle Assessments (LCAs) for its Durakerb, Duradrain and Durachannel products.
The Life Cycle Assessment (LCA) – conducted by independent sustainable consultancy Fishwick Environmental Ltd – reveals that Dura Products’ DuraKerb – a revolutionary, lightweight and environmentallyfriendly kerbstone – has a carbon footprint of just 1.06kg of carbon dioxide (CO2) per kg. In addition, its Duradrain heavy duty combined kerb and drainage system (CKD) comes in at just 1.47 per kg. The final product to undergo the same analysis is Durachannel, a heavyduty linear surface drainage system, which has a carbon footprint of 1.71 per kg.
The company has long advocated the benefits of its plastic kerbs, thanks to their high recycled content and lightweight composition. Today’s announcement further demonstrates how the products are helping the construction industry embrace a dramatically lower environmental footprint over concretebased alternatives. Strategy for expansion and carbon reduction
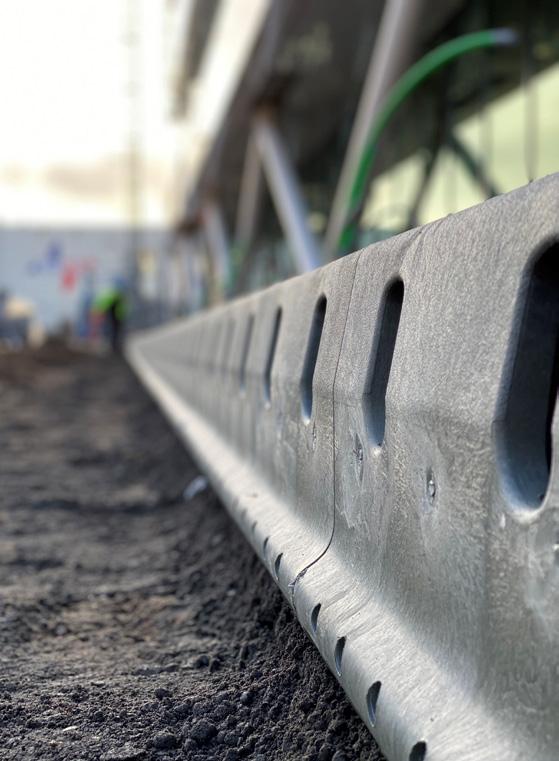
The publication of Dura Products LCAs follows the company’s new strategy for expansion and wider carbon reduction. With the demand for green construction fueling Dura Products impressive growth, the company has outlined its commitment to ensuring the environmental benefits of its systems are upheld at every stage of the product’s lifecycle – from sourcing, production, transportation and installation, through to its end of life.
Underpinning the strategy, the company commits to always using recycled polymer when manufacturing its products, ensuring it continues to divert waste from landfill and reduce demand for virgin plastic. This pledge is crucial in ensuring carbon emissions don’t increase as the company expands.
Dura Products also strives to make sure its systems arrive on-site using as little energy as possible. From making sure all available trailer space is used to transport goods to stocking products locally in emerging territories, the company is taking strides to reduce the impact of long-haul transportation. This is, in turn, aiding availability and accessibility to ensure businesses across Europe and beyond can reap the environmental benefits afforded by the Dura Products range. Another factor responsible for emissions is transportation due to the use of heavy goods vehicles (HGV) when delivering materials to customers. Dura Products’ systems are comprised of recycled plastic making them significantly lighter compared to the traditional concrete equivalent. This saves the environment from carbon during transport as the product is limited in load size by volume, rather than weight.
Further efficiencies are also being made through appropriate partnership management. The strategy outlined by Dura Products states that for already developed markets, its partners take fully packed loads to split and support projects locally. For example, Irish supplier Killeshal Precast generally hold over 2,000 units of stock at any time. This strategy is replicated for all partners in the UK and across Mainland Europe to ensure growth within a sustainable life cycle.
For new markets, Dura Products will initially supply direct from the works on a projectto-project basis, but with a long-term goal of holding stock locally. This is achieved by collaborating with like-minded distributors that share the same ethos and technical expertise to help generate interest and demand in the respective region. For the past two years, the company has been working with Peleg RWS in Israel to introduce the concept of sustainable combined kerb and drainage solutions and is now close to securing its first approval in Jerusalem. The low carbon strategy for supply and supporting projects will then be adopted as the company expands into new markets.
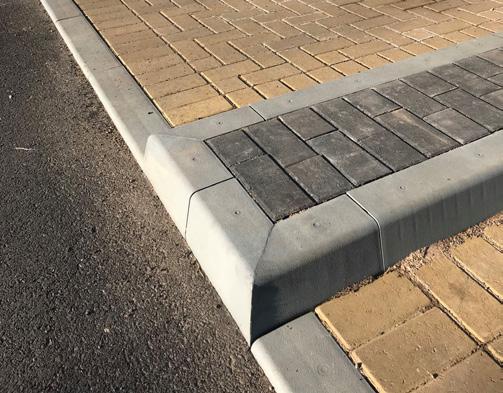
Steve Bennett, Managing Director of Dura Products, commented: “As the construction industry strives to lessen its impact on the planet, we’re seeing an increased demand for our eco-friendly kerbing and drainage systems. While this is great news, we must evaluate our products over their full life cycle using accurate and independently verified data. Proper coordination and monitoring of our carbon footprint will enable our business to expand, without devaluing the environmental benefits of using our products.”
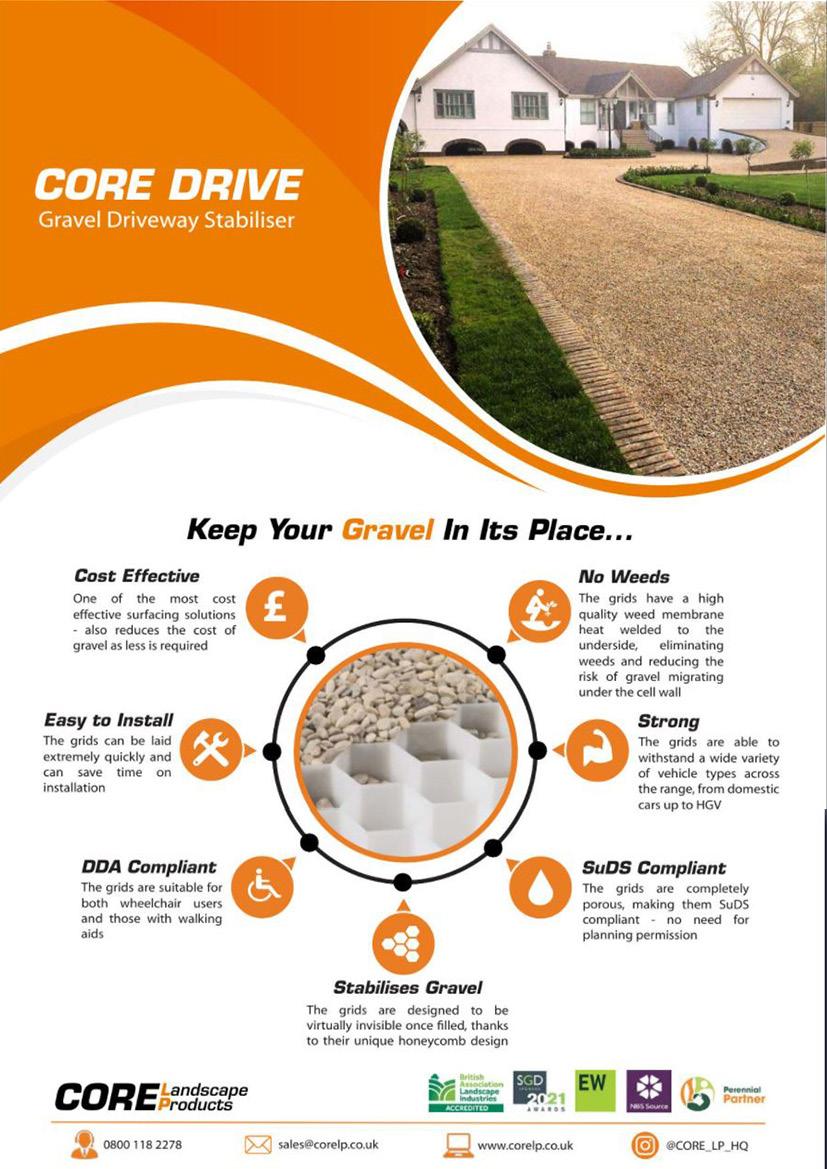
Landscape & External Works Protecting classic cars with SterlingOSB Zero
Bindloss Dawes architects in Somerset is experienced in the design of a great variety of buildings, from high-end retail premises to beach houses in the Caribbean and all sorts in between. The desire to create thoughtful architecture that complements and enhances existing surroundings, with quality, technology and sustainability at the core, sees Bindloss Dawes employing a diverse range of materials.
A current project is the design and installation of a workshop and garages for an avid classic car collector in the grounds of a Grade 2 listed property in Somerset. When specifying materials, the architects originally considered plywood for the structural elements “but the contractors wanted to use SterlingOSB Zero as they insisted it is stronger than ply! As a big fan of OSB, we naturally agreed”, explains Oliver Bindloss, Joint Principal. He continues, “The finished building will be divided into a car maintenance area, complete with a car lift, which will accommodate the restoration of two to three cars at a time, and a garage area which will house the owner’s series of 1960s classic Porsches behind glass doors. The garage section will benefit from a dehumidifier to maintain the condition of the leather upholstery while keeping the chill off the engines in winter.” Check out The Porsche Barn on Instagram to follow the project’s progress. @theporschebarn Oriented Strand Board (OSB) is formed of cross-directional strands of timber, bonded with resin adhesives and mechanically pressed to create a structurally engineered board. The SterlingOSB Zero range from West Fraser is stronger than ply, with no knots, voids or de-lamination. The boards are designed to speed up the build process and are available in a wide range of grades, thicknesses and sheet sizes. For structural use in dry or humid load bearing situations, SterlingOSB Zero OSB3 is the board of choice.
developer-update.co.uk
When undertaking dry lining, SterlingOSB Zero StrongFix quickly provides secure anchorage areas. Along with its many practical attributes, the Sterling OSB Zero range has strong environmental credentials. All West Fraser panel products produced in the UK are net carbon negative and manufactured in mills that have obtained the coveted environmental ISO 14001 accreditation. Responsibly sourced, the panels are FSC certified and created from locally grown timber, cutting embodied carbon from transportation. Sterling OSB Zero is also the first OSB product to be made in the UK with zero added formaldehyde, ensuring an even ‘greener’ board that meets all standards with ease. Samples of SterlingOSB Zero, and West Fraser’s other construction panels, can be ordered on the website. Head to the website to download a selection of tools including a fully-interactive guide to all West Fraser products and a checklist to make sure you have everything you need for your build. For further information, call 01786 812 921 or visit Uk.westfraser.com

Client: Fiona Smedley Style: Grade II listed barn renovation Location: Derby, UK Build time: 2 years
The Grade II listed barns and farmhouse at Elms Farm, Derbyshire, are packed full of history.
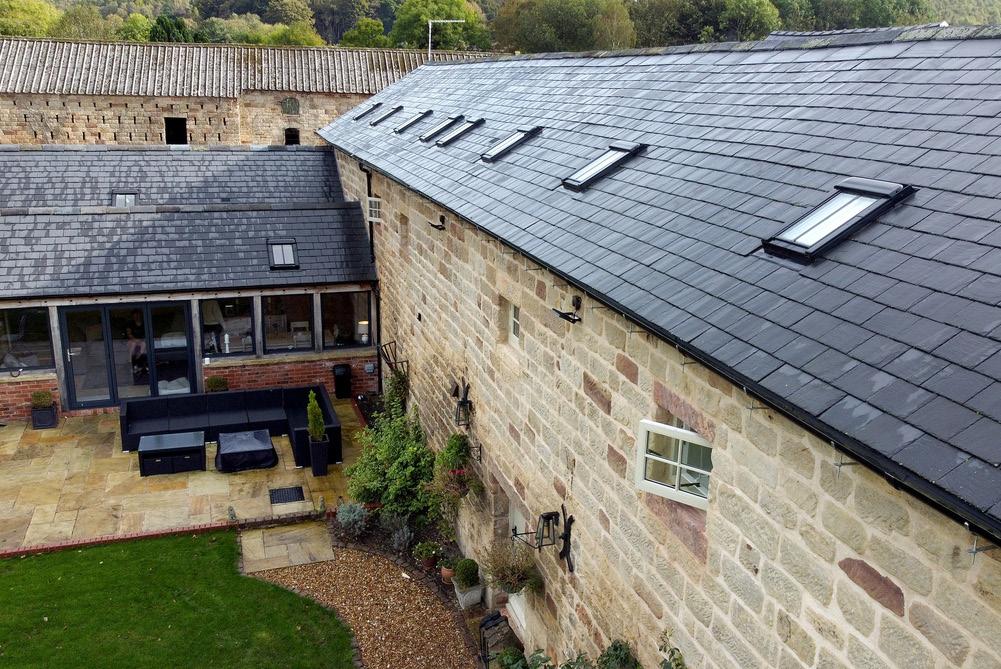
Originally built in 1775, the barns are the former home of the Little Eaton Brewery Company, owned by Officers, and were used as a malthouse and granary before later becoming a working farm. Now, what was once the granary stands the home of Fiona Smedley and her husband John, who transformed the barn into the unique and rustic property it is today, all while ensuring the essence of its history remained. Fiona’s father had bought the barns and farmhouse in the 1980s and ran the site as a farm until he retired in 2017. It was then that he passed on the former malthouse and granary to Fiona and her brother, who took on the buildings with the aim of turning them into homes two years on. Fiona and John worked with local architect, Paul Gaughan Building Consultants to draw up the plans for the granary, which was being used as a barn at the time. After a few tests to analyse the conditions of the groundworks, all legal checks and necessary approvals were granted without any major changes to the initial architectural drawings. When builder Ken Tansley from Interbuild Ltd was first introduced to the site back in May 2017, the barn was still full of old farming machinery, cow partitioning, and even had ducks and chickens living in a part of it. “It was a typical old barn when we first started. We needed to rip a lot out of the building, dig out the floors, do some repointing, and the roof needed to be redone. With it being a listed building, all this preparation and rebuilding work had to be done very carefully and by the book. As the build went on, the architects’ drawings did have to be slightly amended, as is the way with many renovations, but fortunately everything went pretty smoothly and there weren’t any major problems or changes.” Light and heat were two large factors that had to be taken into consideration during the planning stages. The barn had little-to-no insulation, and what would become the second floor had no access to natural daylight – two common issues to tackle in a normal barn conversion, but a Grade II listed property would need extra care and compliance. To accommodate this, many of the upstairs’ original beams, which the owners had hoped to keep, had to be covered for insulation, and fifteen roof windows were drawn into the
plan to bring natural daylight into the top floor rooms.
Ken first heard of Keylite when visiting Buildbase Derby, and soon got in contact with Keylite’s National Brand Development Manager, Tom
Jarvis. “Tom was fantastic, he came out to Elms Farm to meet us and even bought a sample. It was an easy sell due to the price and the fact that all the flashing and add-ons came with the windows as standard, which again saved us on time and price. That, and the homeowners knew they could also get a wide range of blinds from Keylite as well. The team and I work quite regularly on listed buildings, which meant drawing out the specifications and dealing with local conservation and listed building authorities was a straightforward process. “Usually, roof windows can pose an issue for listed buildings, as they sit higher than the roof tiles and therefore cause compliancy issues, as well as being an eyesore. However, another huge selling point for Keylite is that the windows are recessed as standard – meaning they sit lower in the roof, enhancing the overall appearance, and improving the thermal performance of the window.”
Two years on, the Barn at Elms Farm has been transformed into a beautiful rural home. Having stayed true to the building’s long history, homeowner Fiona has worked to ensure as much of the original structure is incorporated into her home as possible. “The barn has such a long heritage, and having grown up on the farm, it’s been such a huge part of my own history too. We’ve kept many of the old original beams uncovered, particularly downstairs, and tried to incorporate as many of the inside stone walls as we can without plastering or covering them up. “The stone floor that you can see has always been here and was actually what used to cover my old horse’s stable! We took the stone up, installed underfloor heating throughout the property, cleaned it up and laid them all down again.” The L shaped building consists of a lounge, three bedrooms with en-suites, and a sunroom, which used to be an old pigsty, looking out into the garden. The sunroom, true to its name, invites a plethora of natural daylight and warmth thanks to the bifold doors and two Keylite roof windows.
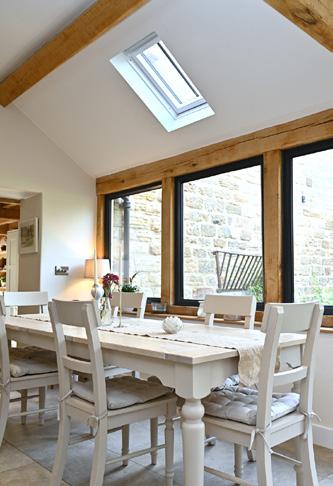

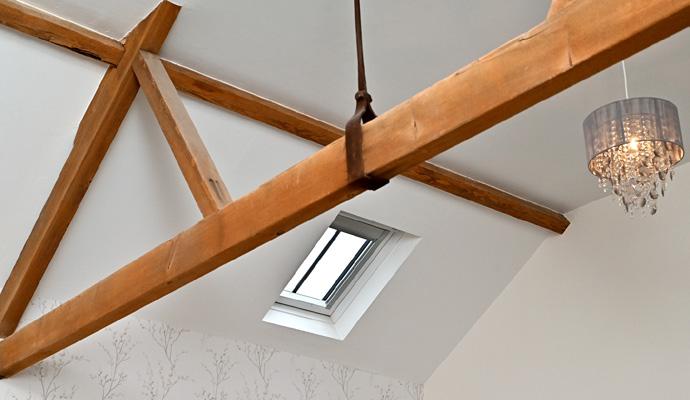
“There is no attic in the barn, meaning the second floor is literally in the roof. Skylights or roof windows were the obvious choice to help bring natural light into the upstairs rooms. Four of our hard-to-reach Keylite windows are electric, which definitely saves us from having to reach with a pole every time we want some fresh air, or when it rains.
“The three bedrooms all boast two Keylite roof windows, and each en-suite has an added one. The light that the windows bring in is wonderful and really helps to enhance the beauty of the property. We were only saying the other day just how much we love it here.”
For more information about Keylite Roof Windows, please visit
www.keyliteroofwindows.com,
call 01283 200 158 or email