
8 minute read
Industry News
Proximity warning tech keeps Nightingale workers apart
Some of the Interserve workers who are turning the Birmingham NEC into a makeshift field hospital have been kitted out with special backpacks that signal when they get too close to anyone else.
Advertisement
Although the first phase of NHS Nightingale Birmingham opened at the National Exhibition Centre (NEC) on 16th April, providing 800 critical care beds to treat Covid-19 patients, work continues there towards an ultimate capacity of 4,000, if required. way, it is intended to raise spatial awareness and affect behavioural change on site.
SiteZone Safety was approached by Interserve while the build was getting into full swing in early April. Its makes proximity warning devices are used on construction machinery but there was nothing off-the-shelf for this particular application, so prototypes had to be swiftly made, tested and approved.
Proximity warning specialist SiteZone Safety has supplied six of its personnel distancing systems (PDS) to Interserve Construction to help enforce the so-called ‘two-metre rule’ of social distancing on the site.
The PDS consists of a 2kg pack, and a detection ‘tag’ that can be worn on a hard hat, attached to a belt or strapped to the upper arm. The system has 100 hours of rechargeable battery life.
The exclusion zone can be configured to suit the site’s needs. The proximity alarms are triggered if workers get too within the set boundaries, at which point both their wearable tags will vibrate and the PDS alarms.
Two site safety ambassadors wear the PDS units full time and patrol the site to ensure remaining workers are observing the two-metre rule. If not, they are reminded, with accompanying demonstrations using the PDS. The other four units are being rotated between different key tradespeople on site to reinforce social distancing. In this Interserve site manager Stuart Palmer said: “We knew about SiteZone Safety’s proximity warning expertise, and they have been able to meet the challenge for us in record time. There was an urgent need to get NHS Nightingale, Birmingham, completed, so high standards of health and safety practice were key drivers to the success of this project. SiteZone Safety’s PDS solution helped us achieve both.”
There were specific challenges when developing the PDS, including making it lightweight, easy to use, and efficiently powered to function for long periods of time.
The PDS repurposes the original SiteZone proximity warning system, which prevents collisions between personnel and mobile plant and vehicles. This time, other people are the threat, and the exclusion zone is rigid.
Gary Escott, co-founder of SiteZone Safety, said: “We had an unusually short period of time to develop and produce a solution that we could deploy quickly. The biggest single advantage we have is that our PDS is built on proven technology, with over 125 million hours in use. The technology has been repurposed for this new application i.e. an invisible virus is now the risk, not a moving vehicle or machine.”
The PDS will be used for the duration of construction at the NEC – approximately four weeks. NHS Nightingale NEC has been provided with their PDS units for free as part of SiteZone Safety’s and its hire partner ESS-Safeforce’s appreciation of the work that Interserve and the NHS are doing in response to the Covid-19 outbreak.
ESS-Safeforce is now offering personnel distancing systems for hire to others who feel they can benefit from it. PDS can later be re-purposed for vehicles and machinery after the requirement for social distancing is over, it says.
ESS-Safeforce managing director Mick Jones said: “Social distancing is a priority during the Covid-19 crisis and the hire model increases accessibility of the SiteZone PDS to a wide variety of users, who we are pleased to serve in this time of urgent need.”
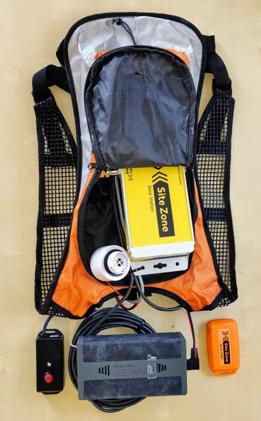
Industry News 05
Flexible working trial aids Fastflow’s return
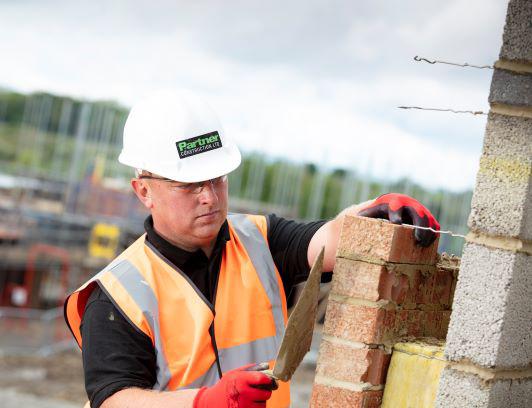
Fastflow had begun trialling flexible working in 2019, with a six-month pilot project conducted by subsidiary United Living (UL) in partnership with the Chartered Institute of Personnel and Development and the government’s Flexible Working Task Force.
The trial included home and remote working – both of which have become essential business practices during the coronavirus crisis, although 80% of Fastflow’s 1,100 employees have now been furloughed.
However the experience of last year’s trial helped UL and other group divisions DW Support Services (DWSS), Fastflow Energy Services (FES) and Fastflow Pipeline Services (FPS) to continue providing maintenance and repair services to infrastructure and buildings during the lockdown. It has also informed preparations to resume some of the suspended operations of group member Partner, which builds new homes for affordable housing providers.
Chairman and chief executive Neil Armstrong said: “We have all faced working and personal difficulties over the past few weeks. “For us it has been ensuring that everyone stays safe and healthy as we work on the UK’s gas and water networks and carry out important repairs to people’s homes. “There is no doubt that the lessons learned during the flexible working experiment gave us an advantage in planning new ways of working which meet the government’s safety and social distancing guidelines. “Closely following advice from government and the Construction Building and infrastructure maintenance specialist Fastflow Group has implemented flexible working policies to prepare to resume suspended activities in line with social distancing guidelines.
Leadership Council, whilst drawing on our own experience of working safely when providing essential services, we have now developed additional safe systems of working. “Over the coming weeks, we intend to re-mobilise new housing sites where it is safe to do so.
“This will be on a graduated, phased and risk-controlled basis, prioritising external work and focusing on areas where social distancing can be maintained.
Bouygues wins upgrade of German power plant

Quality Marking Services (QMS) put all its employees on furlough when the lockdown began, except for managing director Greg Clark and finance manager Peter Nicholson.
However, Greg Clark says that he is now confident of getting the company back to work in accordance with public health requirements.
“I have been fully reviewing all of the guideline documents from central government, Public Health England and the Construction Leadership Council together with our own risk and method
Devon-based highways specialist Quality Marking Services is another industry supplier retuning to work on Monday.
statements to enable a safe and legal return to work for the company,” he said.
“I therefore advise that we are now in a position to start a phased return for the business from Monday 27th April. We shall be undertaking training with those staff returning, providing updates in accordance with our review of the risk and method statements to ensure that whilst we are able to deliver the works for our clients, the safety of our staff remains top priority at all times.”
He added: “The ‘new normal’ is upon us, and we must adapt our processes to ensure legal and safety compliance.”
A subsidiary of Bouygues Construction has won a €100m (£87m) contract to modernise and extend the power plant serving a chemical complex near Leipzig in Germany.
Subsidiary Kraftanlagen’s modernisation of the InfraLeuna plant is designed to secure the energy supply for companies based in the Leuna chemical complex and increase the capacity.
Kraftanlagen will be the general contractor for the entire modernisation project. It will be responsible for the engineering studies, construction and commissioning of the whole plant, including integration of the existing installation.
The modernisation of the existing InfraLeuna power plant will provide a high-performance combined-cycle gas and steam turbine plant, with improved efficiency and flexibility. In addition to the construction of the new combined-cycle plant, the contract includes the connection of the existing gas turbine to a new heat recovery steam generator.
developer-update.co.uk
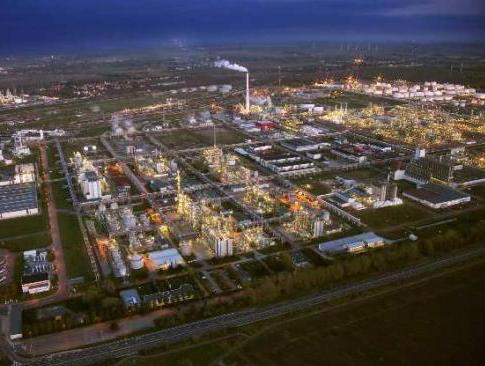
BAM builds fully electric road roller
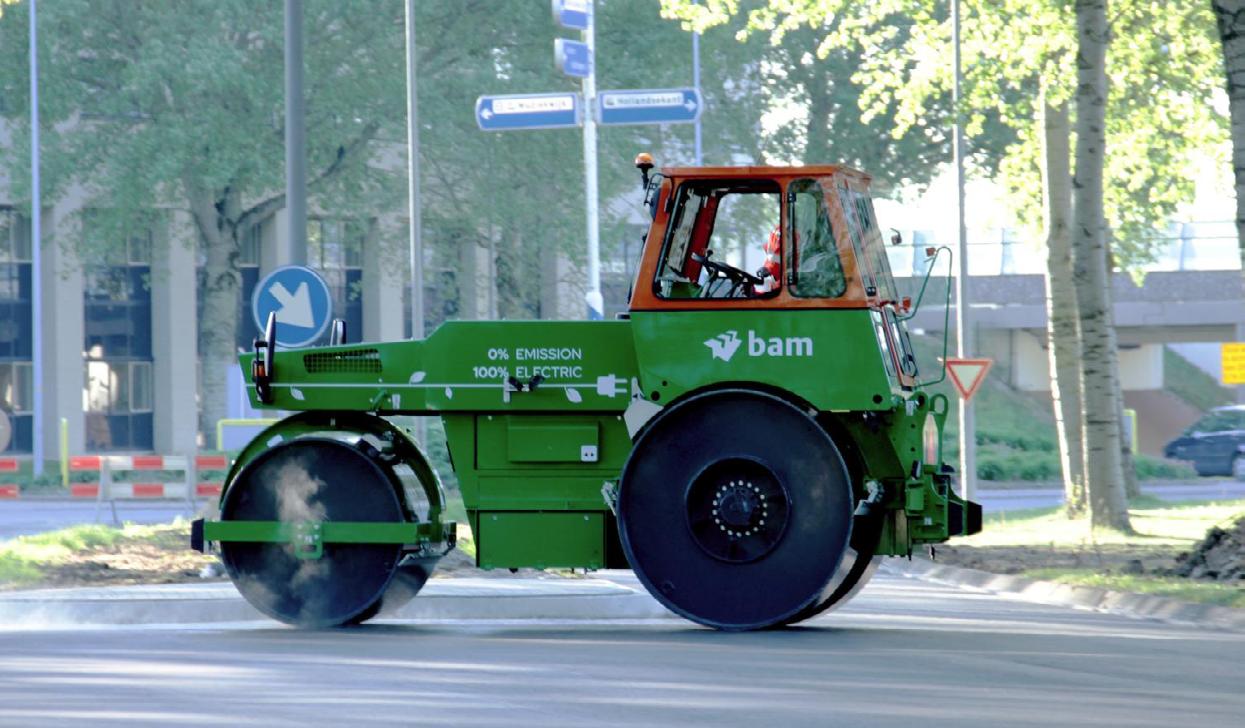
BAM Infra Nederland has built what it claims is the world’s first fully electric 10- to 12-tonne road roller.
It was created by BAM’s plant and equipment department, working on an old machine that was due for an overhaul.
This week the emission-free road roller was put to work on its first project, in the city of Almere.
Koob Bovenhuis, manager of the plant division BAM Infra Materieel,
said: “This has been an incredible achievement and a fine example of the expertise and can-do mindset of our people. From the initial idea during a strategy session, it’s taken us just one and a half years to make the electric road roller a reality.”
The company said that electric alternatives are available for many types of lighter equipment but that the options in the heavier categories are few and far between. Staff put their specialist knowledge to use in the design and fabrication in an effort to realise BAM’s sustainability ambitions and those of its clients.
Thanks to its electric propulsion, the roller emits no carbon dioxide or nitrogen whatsoever. In addition, the electric road roller is much quieter than conventional models.
BAM said that, compared to other heavy equipment, electrification of road rollers is relatively simple as they don’t have to perform repetitive heavy lifts tasks or prolonged excavation tasks. Much like a car, a roller needs energy mostly for driving and steering. Of course, the engine of a road roller needs to propel more weight, but unlike a car a roller doesn’t need an extensive driving range. the roller’s original diesel engine. With the electric road roller, BAM is able to reduce its carbon emissions by approximately 236kg per day. On an annual basis, with 180 days of operation, the roller could reduce CO2 emissions by more than 42,000 kilograms.
A fully charged battery will keep the roller running for eight hours, and recharging takes just three to five hours. As a result, the company said that it can count on the road roller to be ready for action every morning.
BAM said that it considers the electric road roller to be just the first step towards developing a fully emission-free paving train. In addition to electric propulsion, the use of hydrogen could offer possible solutions for the propulsion of heavier equipment.