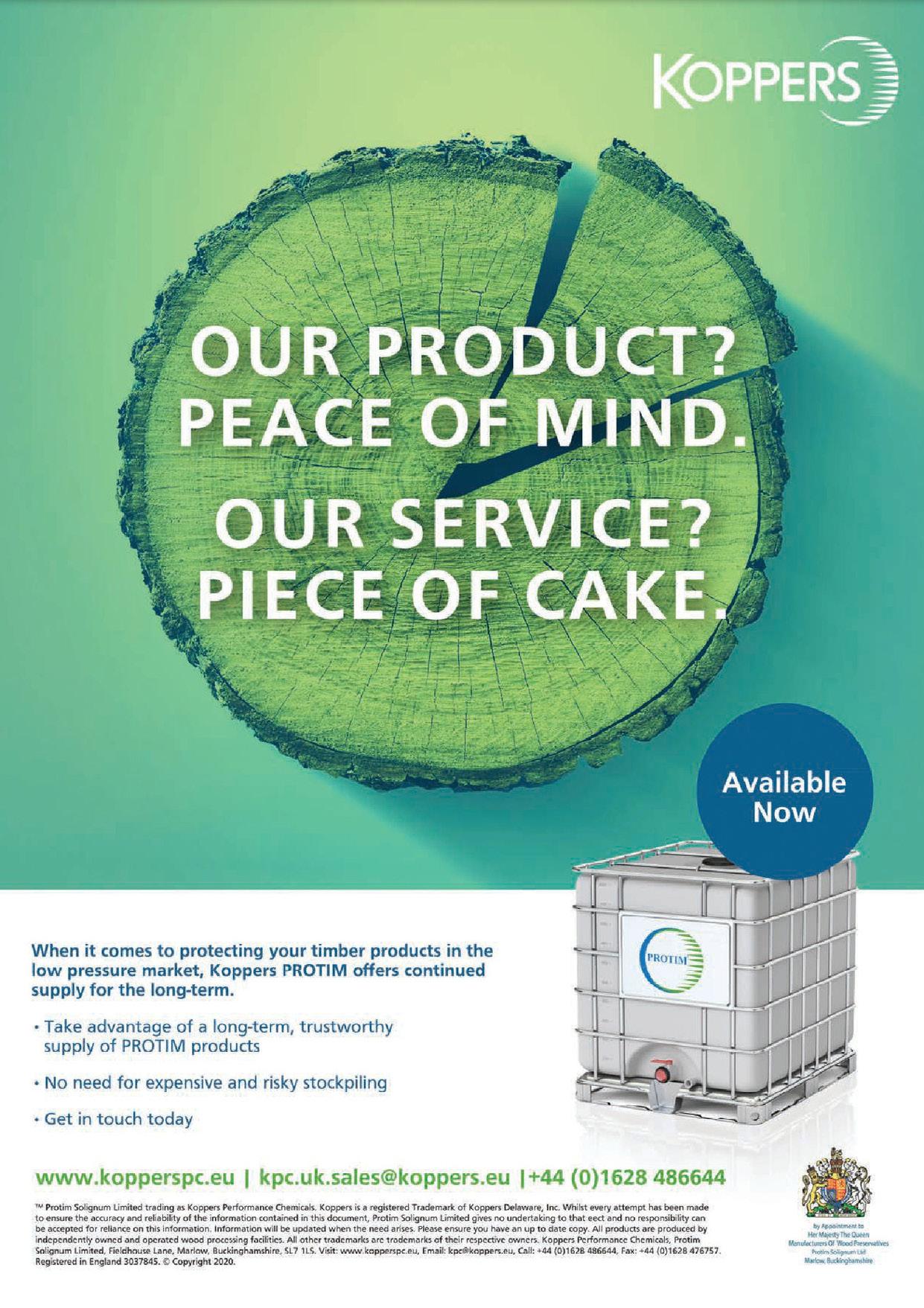
5 minute read
Doors & Windows
When we talk about paint breathability, we mean how much air and water vapour can easily flow through its surface. Older properties were built using materials that were designed to promote this airflow. Using paint with a high level of breathability, coupled with breathable building materials, means that moisture doesn’t become ‘trapped’ beneath the surface of the paint. Lime for example, is a traditional building material which has been used in the construction of properties for hundreds of years, and shouldn’t be sealed with a plastic based paint. It’s durable yet highly flexible. Being moisture permeable, it allows the walls to breathe. So the paint used on top should be breathable too.
Using a non-breathable paint can cause problems with the fabric of the building if left. Trapped moisture can lead to damp walls, causing the paint to bubble, peel and eventually blow completely. It can also contribute to a harmful living environment.
Advertisement
Earthborn Claypaint is highly breathable, but that’s easy to say and proof is needed. Paint breathability can be measured in a couple of different ways:
The first is the Steam Diffusion (or SD) value. It is widely accepted that for a paint to be classed as breathable it should have an SD value of 1 or lower; the lower the value the more breathable the paint.
Earthborn Claypaint has an SD value of just 0.02m. The other method used is the moisture vapour transmission rate (MVTR) which measures the amount of water vapour (in grams) able to pass through the paint surface over a 24 hour period. The higher the figure, the more water vapour that can pass through, and therefore the more breathable the paint. Earthborn Claypaint has an MTV of 1115g/m2/24h, compared with a typical emulsion paint which usually measures between 400-500g/m2/24h. In addition, Earthborn Claypaint has no oils, no acrylics and a negligible VOC content – less than 62 parts per million! Legislative recommendations mean manufacturers should not claim paints to
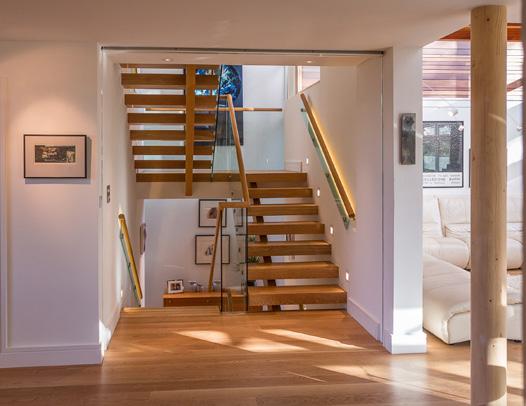

Why use a breathable paint?
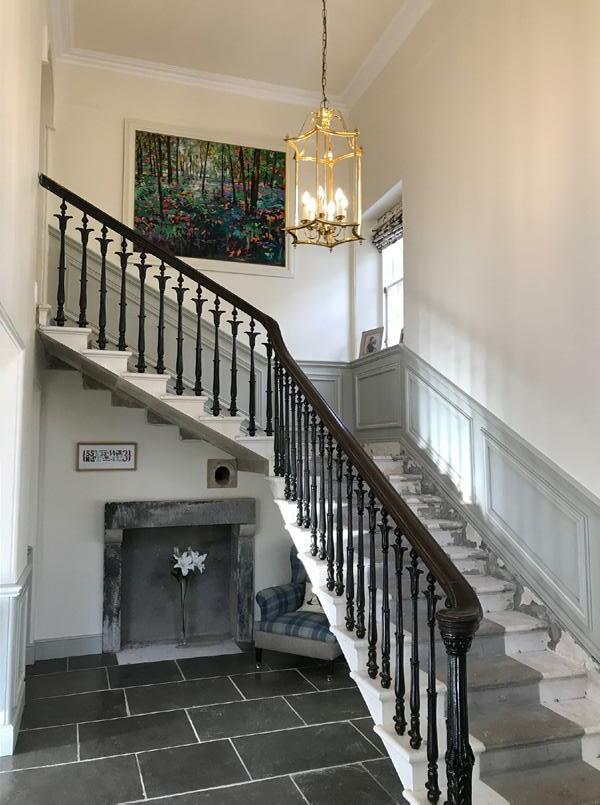
be 100% VOC free so we honestly describe our products as virtually VOC free. Ease of use, high covering power and lack of harmful emissions make Claypaint an ideal option to optimise breathability for any building.
Earthborn’s new colour card showing all 72 colours in the classic range is now available and100% recyclable, including the adhesive and the paint chips that use real Claypaint.
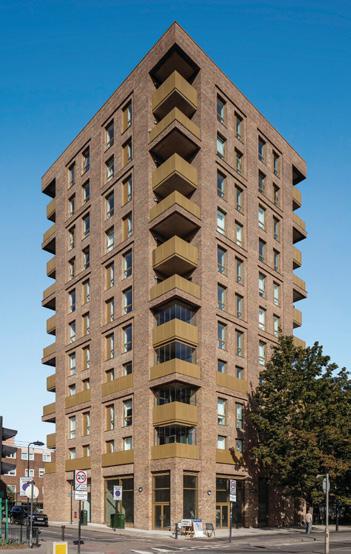
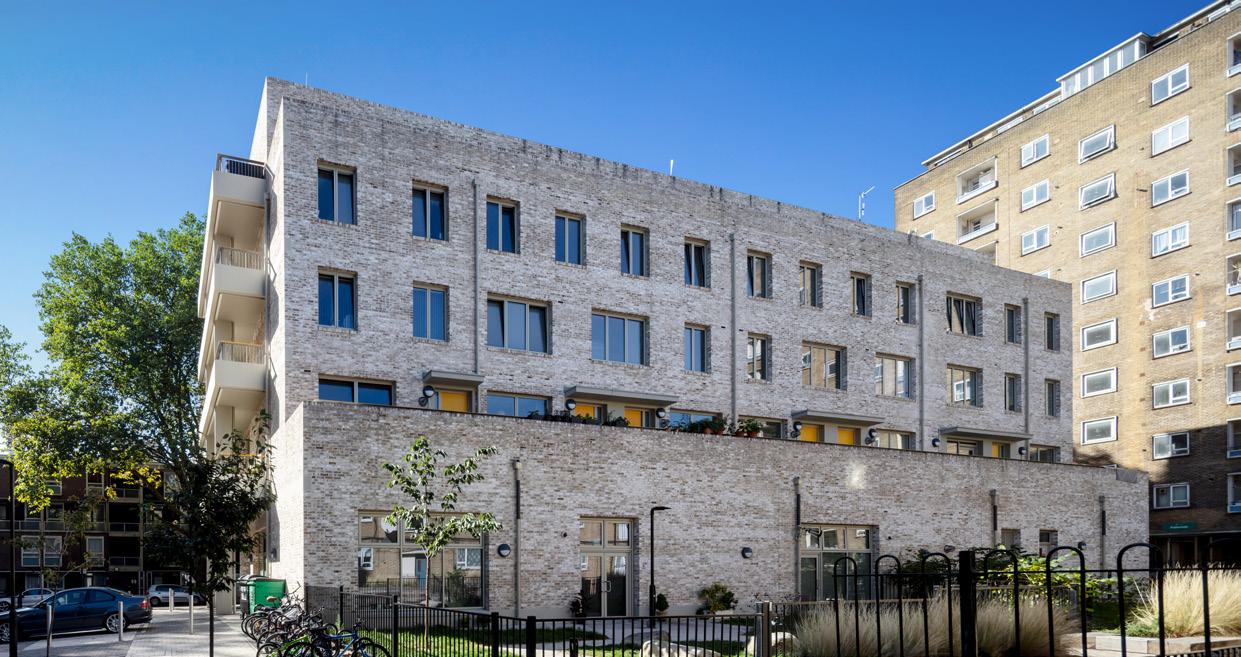
CASE STUDY
Project:
Regent’s Park Regeneration
Project address:
Camden, London, NW3 2YS
Products used:
Welded Masonry Support, Brick Slip Lintels, B.O.S.S. (Brick On Soffit System), Cast-in-Channel
Architect:
Ingleton Wood
Brickwork Subcontractor:
Chime Brickwork
IG Masonry Support’s brick slip soffit solutions help deliver architect’s vision for huge innercity housing project
Overview
Regent’s Park Regeneration is a £72m development which has seen the creation of 122 affordable new homes and community facilities in Camden, north-west London. The scheme, on behalf of Camden Council, followed the demolition of housing and businesses in the area to make way for the High Speed 2 rail link between London and the West Midlands.
As a result, Lovell Homes London, in conjunction with architects Ingleton Wood, was selected to deliver the new homes across eight sites within the existing estate. The oneto-five-bedroom apartments are situated in an inner-city location with buildings ranging from three-to-eleven storeys in height. For all of the project’s apartment blocks, IG Masonry Support worked alongside the contractor and architect to develop a range of prefabricated brick slip components to help achieve the intricate brick elements and brick soffits featured throughout the development.
The Challenge
Each building within the Regent’s Park Regeneration presented a slightly different challenge, with the brick elements playing a vital role in fulfilling the architect’s vision for each of the blocks. Various brickwork features in an array of bespoke designs were required for the exterior of the blocks. Traditionally, achieving these features requires skilled labour cutting bricks onsite, a time-consuming process
which IG Masonry Support’s offsite manufacture of bespoke, pre-fabricated brick slip components helped to significantly speed-up. The Solution

The intricate brick detail achieved at the Regent’s Park Regeneration project highlights the design versatility of IG’s offsite brick slip solutions. The company worked with the architect from an early stage to design effective offsite solutions which enabled the project’s complex brick details to be achieved across the eight buildings; Cape of Good Hope, Newlands, Rydal Water, Robert Street, St Bede’s, Varndell, The Victory Pub and Dick Collins House. IG Masonry Support was challenged to supply brick slip soffit solutions, accommodating the range of different sized openings and soffit requirements throughout the development. A combination of Brick Slip Lintels and B.O.S.S. units capable of achieving both stretcher and soldier course bond patterns, were designed by IG’s technical team. These offsite units achieved the beautiful brick soffits over apartment block windows and openings on the various elevations of the buildings throughout the development. The Newlands and Rydal Water buildings presented complex brickwork elements that required IG’s technical team to design bespoke B.O.S.S. units to achieve the detailing specified within the architect’s designs. Beautiful brick soffits varying in depth from 102mm to 440mm feature over the balconies on every corner of these apartment blocks, as well as recess panels with 102mm brick soffits in a stretcher bond pattern on each elevation. A flying beam features on the upper level balconies of the Varndell building. This architectural detail, which has a 665mm soffit, was also achieved using bespokedesigned B.O.S.S. units. IG Masonry Support’s precise, prefabricated solutions manufactured using a consignment of bricks from site, blended seamlessly within the buildings’ eyecatching exterior. From design stage to delivery, IG Masonry Support worked alongside the contractor and the architect to deliver complex brickwork elements that formed an integral part of the design of the buildings. The result is a stunning, modern inner-city housing development which has not only been shortlisted for a host of industry honours including the RTPI Awards for Planning Excellence, New London Architecture Awards, and RICS Social Impact Awards; it’s provided new homes and peace of mind for hundreds of residents whose domestic lives were transformed by the government’s ambitious rail project.
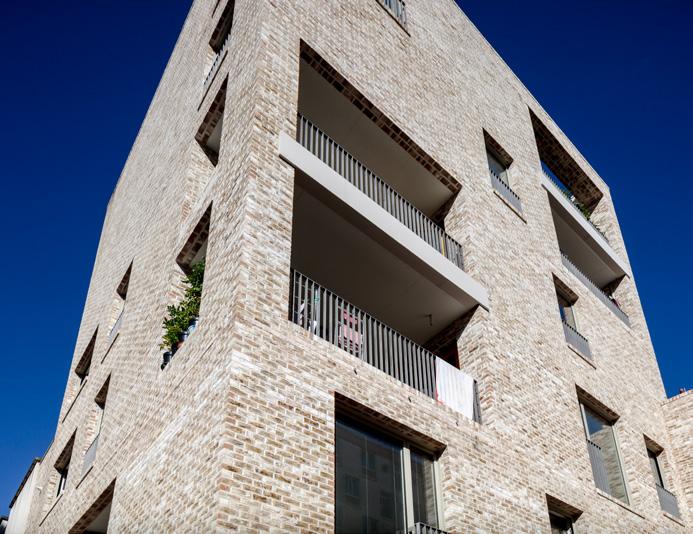
igmasonrysupport.com