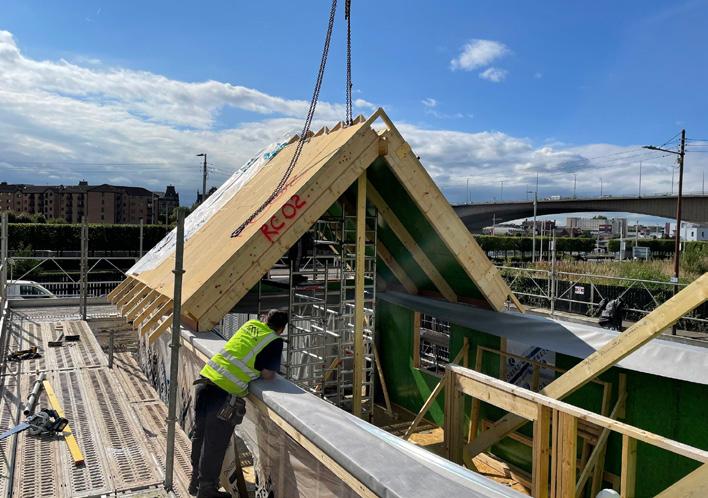
13 minute read
Roofing & Cladding
Roofing & Cladding Construction of COP26 House in progress for UN Climate Change Conference
COP26 House will showcase what is achievable with today’s materials and technologies
Advertisement
Work is in progress on the construction of the COP26 House, a zero carbon, timber frame building built by Beyond Zero Homes. Sustainable wood-based panel manufacturer, MEDITE SMARTPLY is playing a vital role in the build. The project will showcase low carbon, circular solutions in building and living during the 2021 UN Climate Change Conference in Glasgow this October 31st- November 12th, demonstrating how the climate emergency can be met with products and building strategies that are already in existence. Chris King, Managing Director at MEDITE SMARTPLY, commented on the project: “Actions speak louder than words. This building encapsulates MEDITE SMARTPLY’s commitment to building a more sustainable future. “We in the construction industry have not only the opportunity but the responsibility to put theories into action and show the world how we can build and live sustainably, using wood and ecologically responsible solutions.” The members of Beyond Zero Homes are united by a common goal that goes beyond zero carbon: to demonstrate how beautiful, affordable, healthy homes can be developed with minimal impact on the environment throughout their lifecycle, to help us meet our climate commitments. The Construction
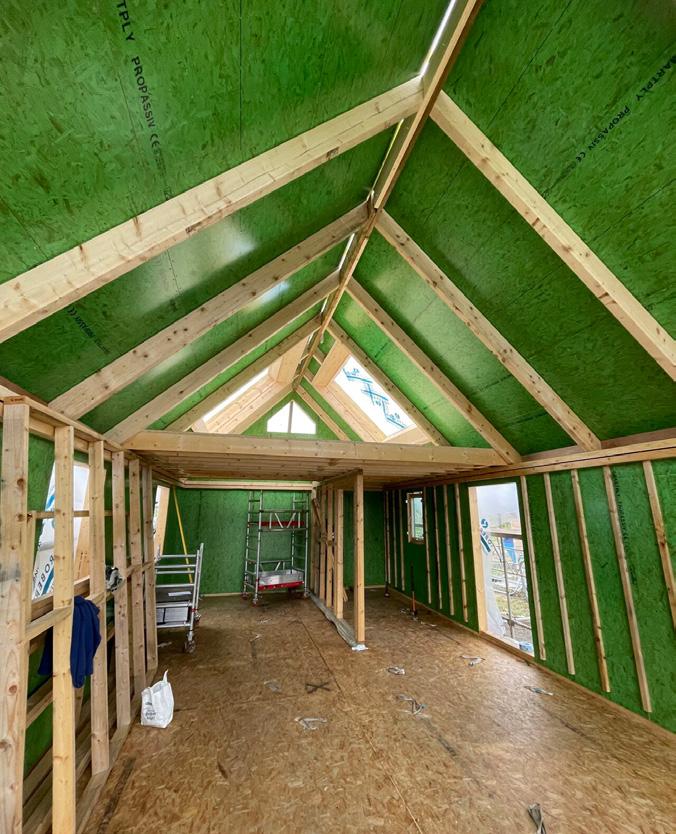
The one-bedroom house has been specifically designed to use homegrown C16 Spruce to avoid the need for imported timber, lending itself perfectly to the specification of SMARTPLY OSB, sustainably produced in Ireland and already stored across the UK. The build features the integration of SMARTPLY PROPASSIV, a structural OSB panel with integrated vapour control and air barrier properties for use as structural sheathing in timber frame structures. Additionally, the build is incorporating SMARTPLY ULTIMA for the internal flooring and underside boarding, while SMARTPLY STRONGDECK is being used for the internal mezzanine level flooring. The construction is based on a 1.2m grid, allowing it to be easily panelised and prefabricated, or even self-built on site by two people, driving potential emissions from construction down even further. The design has been adapted from one of Roderick James Architect’s signature designs, the barn house. Max Bishop, Specification Manager at MEDITE SMARTPLY said: “It’s fantastic to see progression on site of the COP26 zero carbon build. This is a statement to the rest of the world that sustainable zero carbon building is possible, and it can happen right now.” While the house has been designed with small scale, rural self-build developments in mind, the potential for it to become the future of sustainable residential building is real, as it can be adapted to larger scale developments and offsite prefabrication. As part of the Coillte Group, MEDITE SMARTPLY prides itself on its sustainable supply chain and manufacturing processes, meaning the company’s products are as environmentally conscious in their make up as they are in their application. MEDITE SMARTPLY has pioneered the sustainable timber industry in Europe, with all specialised woodpanels—MEDITE Medium Density Fibreboard (MDF) and SMARTPLY Oriented Strand Board (OSB).
Find out more and follow its progress: beyondzerohomes.co.uk Discover more about MEDITE SMARTPLY: https://mdfosb.com/en
Roofing & Cladding COST EFFICIENCIES AND AESTHETIC APPEAL GO HAND-INHAND FOR GRADE II LISTED ROOFING PROJECT
The timeless beauty of the handmade Marley Canterbury clay plain tile is on display at Christ’s Hospital School following the completion of a major extension project. However, as the school was on its present site since the 1890s, and as a Grade II listed building, it was paramount that any developments also integrated into the existing complex of listed buildings.
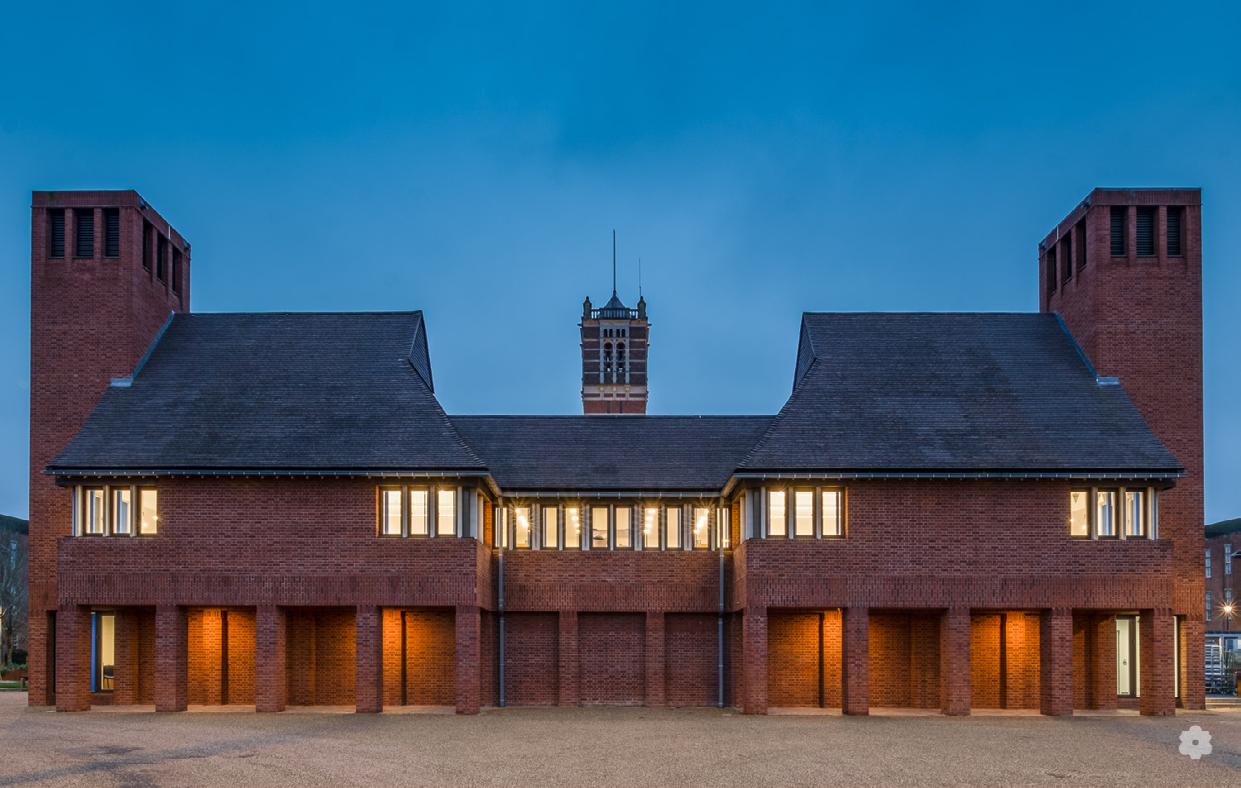
Over the years the main route of access to the school had changed, which saw NRAP Architects called on to develop a single, largely symmetrical building fronting the approach road, positioned to create two new external spaces. These newly formed spaces would be used to offer a state-of-the-art teaching and catering facility, while the second space would create a new entrance court that would be used to welcome staff, students, and visitors.
This saw NRAP Architects propose a series of linear gableended pitched roofs, with tile to brick upstand junctions at each end, to house the kitchen, with the plant within the roof space above. While chimneys at the end of each gable, run perpendicular to the dining hall and front the public spaces and classrooms. In addition, under roof-lit vaulted ceilings, face the approach road.
The key criteria for the design team at NRAP Architects, as well as conservation officers from English Heritage and local planners, was that all materials scheduled to be used were authentic to the prevailing building style of the school and could seamlessly match the surrounding vernacular. From a roofing perspective, the answer lay in the specification of traditional handmade clay plain tiles. With the existing listed building featuring slate roof tiles, the project’s architects were keen to work with a roof tile which could offer the right amount of texture that arises from having slight variations in shape and colour across the roof surface. Marley’s Canterbury tile not only blended with the rest of the building’s aged appearance, but its distinctive colour character will help to enhance the striking appearance of the school for decades to come.
The decision to specify Marley’s Canterbury handmade clay plain roof tile in a Loxleigh fine sanded finish helped to satisfy the aesthetic demands of all key stakeholders and simultaneously delivered a significant cost efficiency. More than 100,000 Canterbury tiles were handmade by Marley to satisfy the extension project’s requirements and delivered to site to meet the project construction deadlines, which was phased to ensure all facilities were maintained during construction. In addition, with A+ BREEAM environmental credentials and meeting certification for BES 6001, Marley’s Canterbury tile also played a part in meeting the sustainable objectives of the project too.
Richard Owers, Director at
NRAP Architects, adds: “When working on a project of this type, it is essential that all specified materials and finishes seamlessly match the existing
The unrivalled aesthetic appeal, functionality, and cost effectiveness of Marley’s Canterbury handmade clay plain tile, has made a significant contribution to the success of a building project after being specified as the ideal roofing solution for a Grade II listed school in Horsham, Sussex.
buildings and setting. We went through a careful process with the choice of brick and mortar and followed these principles when it came to the selection of the final roof tile that would complete the new extension’s appearance.

“With Marley’s help, we were able to make the case for the specification of the Canterbury handmade clay plain roof tile. The Loxleigh colourway creates an ideal blend with the surrounding school buildings, providing an attractive colour character that helps to complement the overall look we aimed to create. As well as the unique and traditional properties the Canterbury tile offers, by specifying it we achieved a 30% cost saving when compared to other similar roof tiles.”
Stuart Nicholson from Marley,
comments: “The design project team had originally specified an alternative handmade clay plain tile. But following discussions with Marley it was clear that our highly functional Canterbury handmade tile would deliver a crafted, quality product that would aesthetically match the current building. And it also presented a guide cost saving of approximately 30% compared to the original roof tile specified. This powerful combination provided a compelling argument to ensure that the Canterbury solution was chosen and installed on the new extension areas at the Christ’s Hospital School.”

For more information on Marley’s Canterbury range visit:
www.marley.co.uk/roof-tiles/ clay-roof-tiles/canterburyhandmade-plain-tile
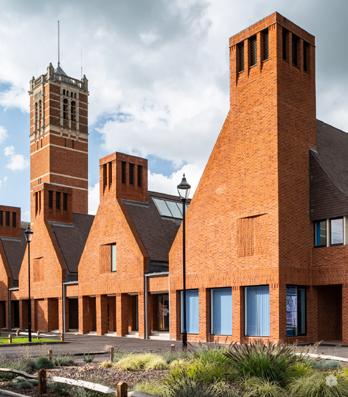
ROOFING ALL YEAR ROUND: WHY RUBBER EPDM IS A WINTER SOLUTION
What makes EPDM winter-proof?
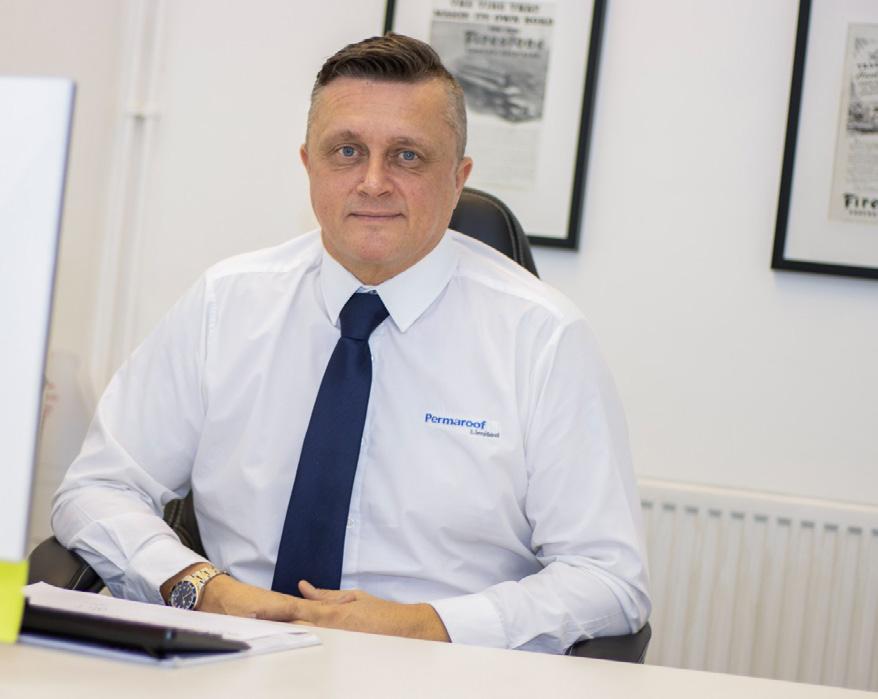
EPDM is developed using a synthetic rubber ethylenepropylene-diene terpolymer, which is formed into a 100% cured, single-ply roofing membrane. This material is long-lasting and durable, making it ideally suited to winter weather, and the low maintenance nature of the solution ensures customers gain reliable peace of mind from their investment. Suitable for any type of flat roof, EPDM offers a comprehensive waterproofing solution for both domestic and commercial buildings, and is particularly convenient for use on garages and sheds to guarantee valuables are protected from water damage. A year-round roofing option, EPDM rubber roofs also resist UV and ozone, due to the material containing a high proportion of carbon black and no plasticisers or antioxidants, giving it a life expectancy of more than 50 years. Simplified installation Completing roofing projects and repairs in the winter can be a job that people dread, due to the added challenges presented by the inclement weather. Therefore, a quick and easy installation is essential to beat the elements, complete the job and prevent further damage. EPDM is supplied in large, seamless sheets, up to 15.24m in width and 61m long, negating the requirement to cut and piece many sheets together. Not only does this make using it time efficient, as one sheet can cover an entire roof, but also improves longevity as it reduces the number of seams required.
developer-update.co.uk
As we head into the winter months, external building and maintenance work enquiries often slow down due to the cold, wet weather. However, when a roof needs repairing, it’s usually a job that can’t be left unaddressed due to the potentially catastrophic effects it can have on a structure. Adrian Buttress, managing director of PermaRoof, part of PermaGroup, discusses why EPDM rubber is the ideal material to equip roofs for the winter.
An EPDM rubber roofing installation requires no specialist tools and no heat or flame, which means less time on site and an easier application when out in the elements. However, we strongly recommend that installers attend our Firestone EPDM training centre to guarantee the best possible finish on a project. Efficient repairs Full training on EPDM instillation reduces the potential of issues developing further down the line with the roofing system as, when a tradesperson hasn’t completed the training, there is a higher chance the membrane has been laid incorrectly. However, no matter how durable the material is, there will always be a possibility of repairs being needed.
Unavoidable splits and cracks can, fortunately, be easily repaired by the reliable repair method used on EPDM roofs, liquid PU – or “liquid rubber” as it’s commonly referred to. The liquid rubber creates a watertight and weatherproof seal to protect roofs all year round, particularly from the elements in winter. Applying the liquid PU is simple and it quickly cures on a variety of surfaces – ideal characteristics for when you are working within a short and unpredictable gap in cold, wet, or dark conditions.
Only one coat of PU liquid is required to effectively seal a repair and it comes in a premixed solution that can be applied straight from the tin using a brush – no complex process required. For this reason, we advise every roofer to keep a tin of liquid rubber to hand for those emergency calls and quick, reliable fixes, when faced with the harsh climate of a British winter.
Winter ready roofing As a tradesperson, winter can bring a feeling of dread as the weather leads to more issues with roofs and an increased challenge with repairs, however, EPDM rubber’s natural attributes ensure it’s the quickest, most effective, all-weather solution.
With smaller projects, such as adding outdoor buildings, on the rise due to the impact of people spending more time at home, as well as larger extensions being considered due to house moves becoming less likely, flat roofing is certainly a market that offers plenty of opportunities for installers – especially during the winter months.
For more information on Permaroof UK, please visit www.permaroof.co.uk or call 01773 608839.
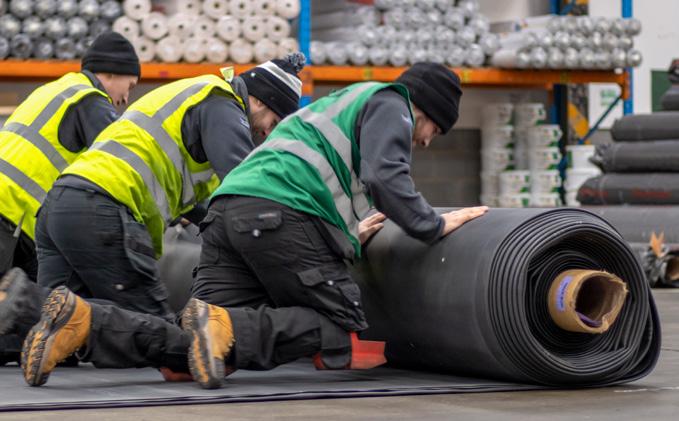
STRATEGIC PARTNERSHIPS:
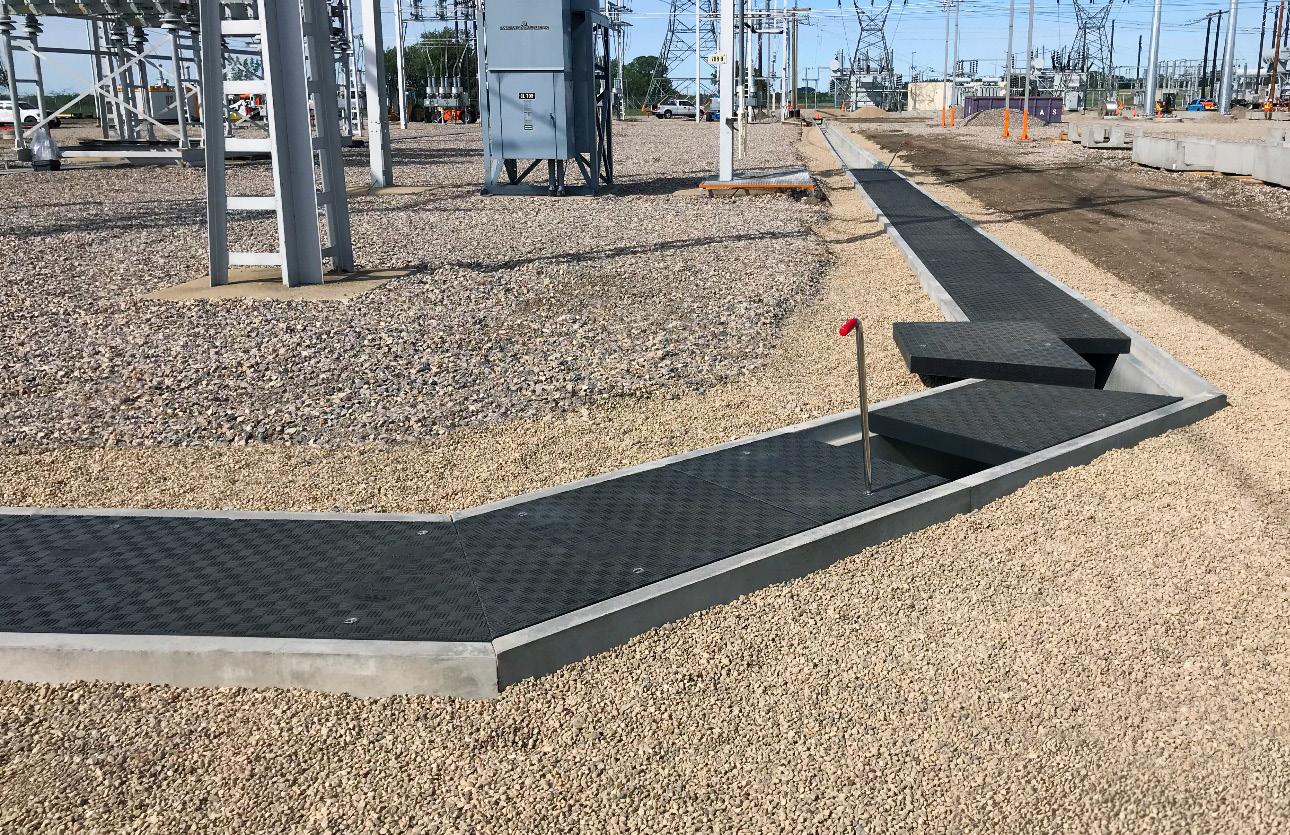
PRECAST & PREFORMED TROUGHS & FIBRELITE’S ‘MADE TO MEASURE’ GRP COVERS
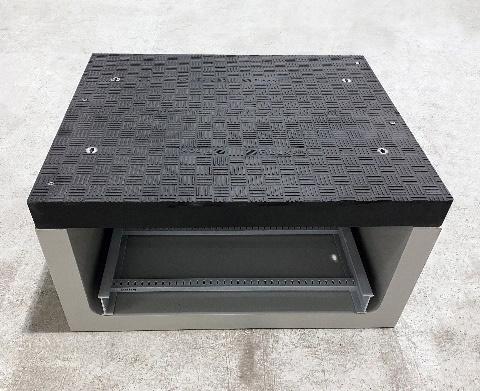
MAIN IMAGE: Custom Fibrelite covers installed in precast concrete manufacturer Trenwa’s troughs at major US sub-station
ABOVE: Custom Fibrelite covers designed and engineered to fit manufacturer Fibex’s preformed GRP troughs Composite access cover manufacturer Fibrelite has formed strategic partnerships with a number of major manufacturers of precast and preformed troughs (also known as trenches, channels and ducts) in Europe and the USA (including Fibex and Trenwa) to create new collaborative product offerings integrating Fibrelite covers and precast and preformed troughs, combining the strength and longevity of precast and preformed troughs with the easy, safe manual removal and durability of Fibrelite’s lightweight composite covers.
Health and safety issues surrounding manual handling are of paramount importance to site managers.
Without the necessary provision of dedicated lifting apparatus and training for operatives, traditional concrete and steel trough access covers can be a concern due to their sheer weight. Concrete slab covers can weigh as much as five times the weight of an equivalent size Fibrelite GRP composite trough cover.
Fibrelite covers have an industry leading strengthto-weight ratio and are designed to be safely and easily removed by two people, using the Fibrelite
FL7 ergonomically designed lifting handles.
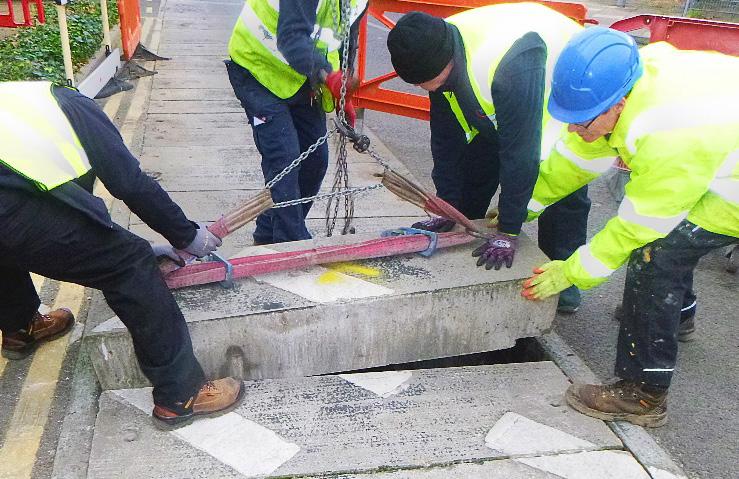
ABOVE: Concrete slab covers can weigh as much as five times the weight of an equivalent size Fibrelite GRP composite trough cover
Driven by focusses on health and safety, weight, durability (no corrosion) and reduced installation time, GRP composite access covers have moved from being a niche product used on petrol station forecourts to being specified at the outset of new build and retrofit projects for some of the world’s most prestigious brands in technology, data centres, ports, airports, hightech manufacturing facilities, utilities, infrastructure and many more. “In recent years, the demand for highly customisable, high-tech access covering solutions has grown exponentially, and we’re proud of the part we’ve played in their adoption over the 40 years since we invented the world’s first. Since then, we’ve continually innovated, focussing on creating solutions to industry and customer challenges.” Commented Jo Stott, Fibrelite’s Marketing Director “Partnering with precast and preformed trough/trench manufacturers was a logical next step, and I’m proud to say that, since we created our first partnership offering with Trenwa in 2014 we now have over 50 kilometres of our covers installed in precast and preformed troughs across the globe” David Holmes, Fibrelite’s Technical Director added “We work closely with architects, contractors, and end users from tender stage right the way through to delivery and even installation where required. This collaborative process ensures that the supplied product fulfils both product quality demands and strict project completion deadlines. Fibrelite covers can be custom designed and manufactured with dimensions matched precisely to specified trough opening/rebate dimensions (Fibrelite’s adjustable tooling allows covers to be manufactured within millimetres of a clients requirement)” Recent Installation: New Build Data Centre, Northern Europe
Some clients favour a complete GRP solution for both troughs and covers. Where appropriate, this can further reduce installation costs and time due to their reduced weight for transit and installation. Earlier this year, Fibrelite engineered and manufactured 550 metres of custom trough covers for a new build data centre in Northern Europe. These GRP preformed troughs were supplied with custom fit Fibrelite bolt-down covers, for added security. ABOVE: Fibrelite trough covers are designed to be safely and easily removed by two people

Recent Installation: Cruise Ship Terminal, UK
Fibrelite custom engineered and manufactured 500 metres of F900 (90tonne) load rated GRP trough covers to fit precast concrete troughs at a UK cruise ship terminal. The stepped covers were supplied in a number of customised sizes to fit the trough configuration. The F900 load rated covers were stepped to reduce the unit weight in compliance with the customer’s specified manual handling limit.
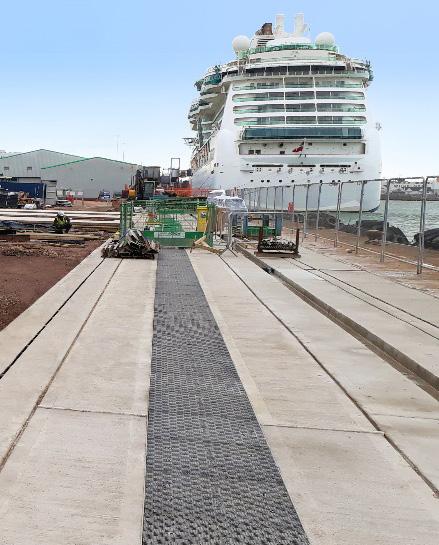
ABOVE: F900 (90-tonne) load rated GRP Fibrelite trench covers in precast concrete troughs/trenches at a UK cruise ship terminal