
3 minute read
Complete programme with unique SPGPrints Screens
Printers today face a multitude of challenges as they try to remain competitive and – at the same time – meet brand owners’ requirements for quality and flexibility of service. SPGPrints’ screens give you an exceptionally reliable, longlasting and highly accurate means of printing on a wide range of web widths.
RotaMesh® screen material
The ultimate workhorse in screens for rotary screen integration
SPGPrints’ RotaMesh® is a top-quality screen customised for the SPGPrints Rotary Screen Integration (RSI®) printing unit. A RotaMesh® screen is a non-woven, electroformed mesh made out of 100% nickel. The unique hexagonal ‘honeycomb’ structure ensures sharp printing quality, maximum stability and consistency.
RotaPlate® screen material
The perfectly fitting mesh for all rotary screen printing presses
RotaPlate® is an excellent alternative for users of woven screen material. It’s strong, stable and offers a long working life. Thanks to a patented production process, SPGPrints’ RotaPlate® features a pre-sensitised coating and a hexagonal ‘honeycomb’ structure that is made out of 100% nickel. The result is excellent print performance at each stage of production. Get more printed metres out of your mesh.
Jet technologies offers local technical support by simplifying digital pre-press workflow for rotary screen making, starting with cutting and punching facilities, on all sizes of rotary screen material as well as welding and film free state of the art laser exposing technology. All these services are based at our head office in Sydney and backed up by SPG Prints global service.
We also offer a wide range of rotary screen-printing consumables as well as the latest developing and drying system to standardise quality and accelerate throughput in your pre-press workflow.
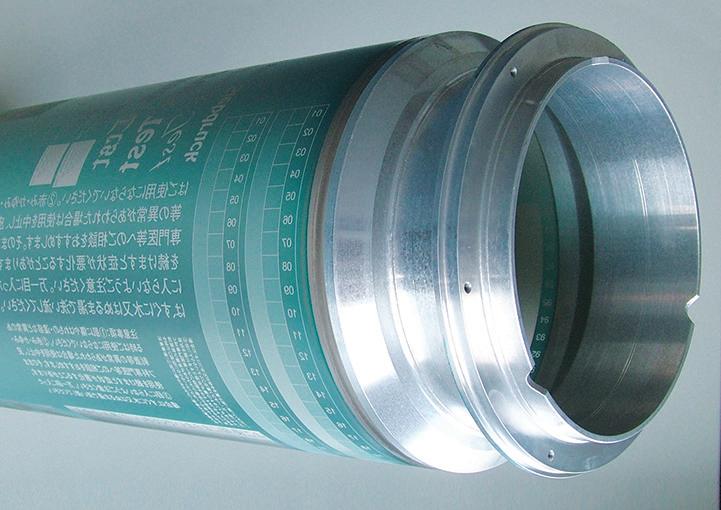
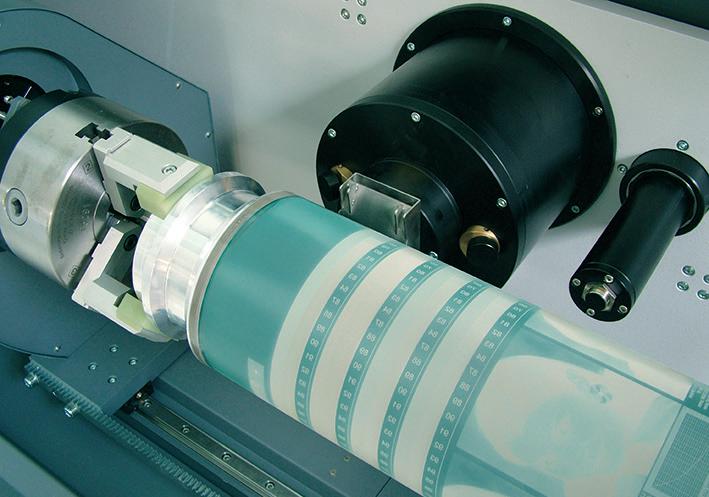
We all know that cleaning press parts is a hassle and really hard work. There are a lot of parts that must be consistently clean if you want continually high output from your printing machine. There is no easy way to go about it, or is there?
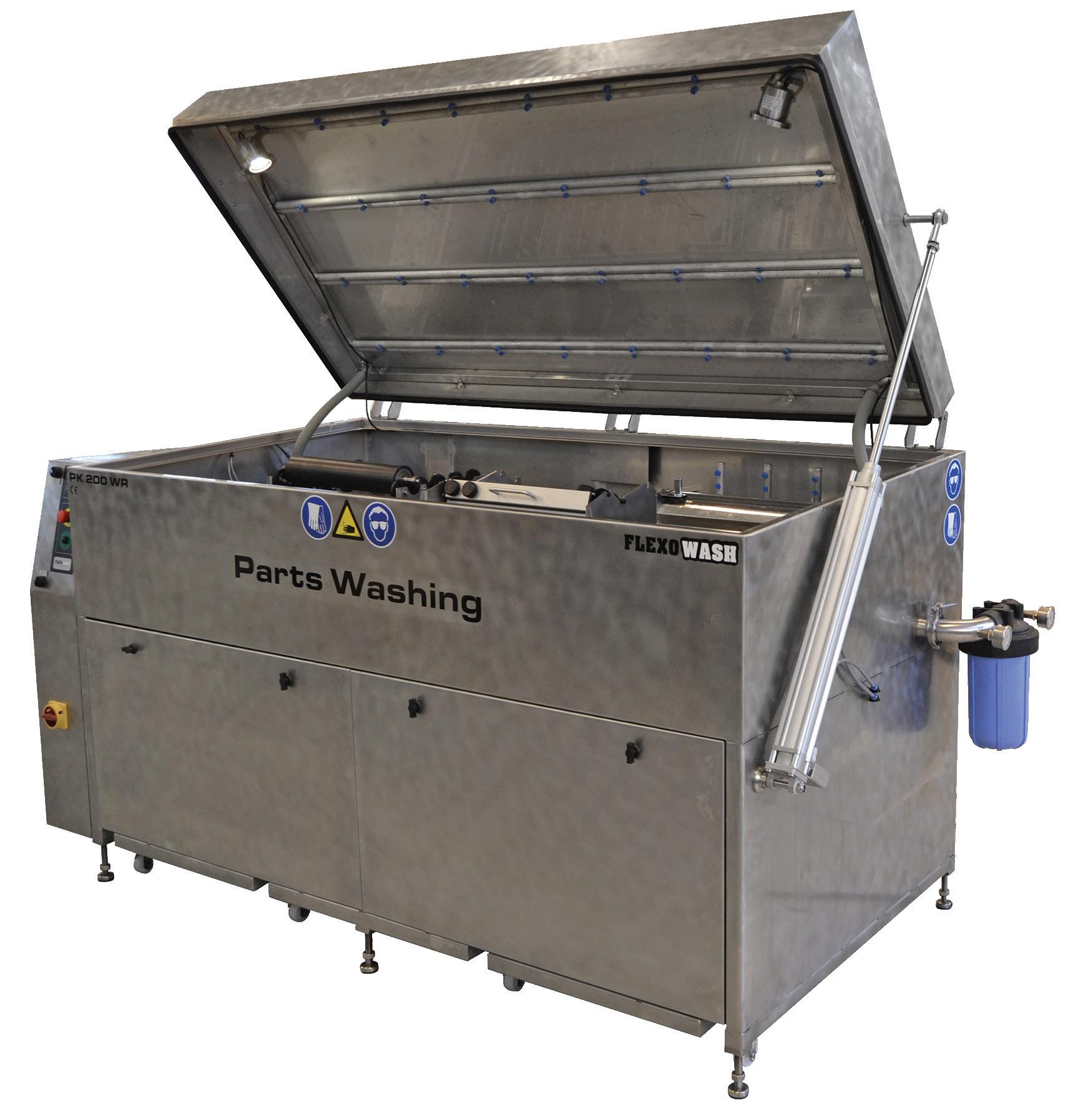
Automated cleaning of press parts is the smart way to make sure you have consistent high output from your printing machine and the highest possible printing quality. It does not matter whether you clean with solvents, non-flammable liquids or alkaline liquids you get the same high results every time.
With staff shortages during the pandemic there is a focus on automation to increase efficiency, save time and reduce manual labour.
Here are the benefits from automated cleaning
1. Improve overall production quality
When you implement automated cleaning into your production you significantly increase the overall cleanliness of your workplace. However, the most important thing is that you reduce the number of do-over printing jobs you have in your production, your print quality improves, and you will potentially be able to scale up your production to do even more printing jobs.
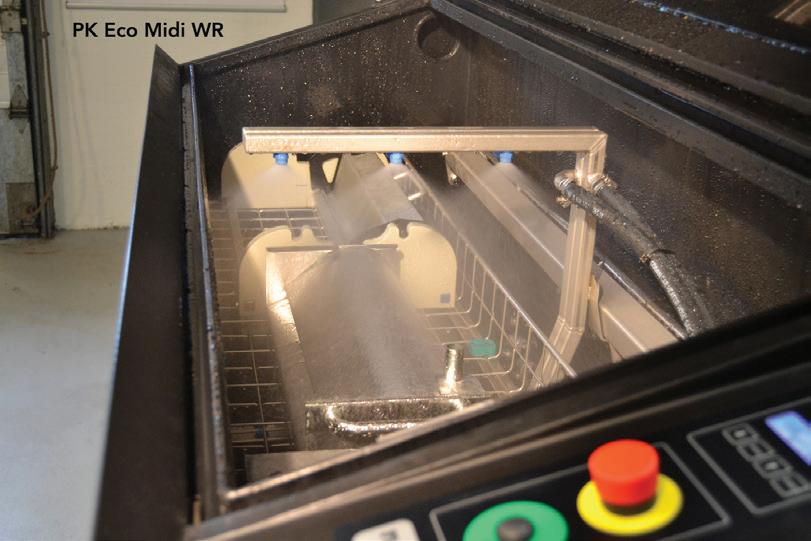
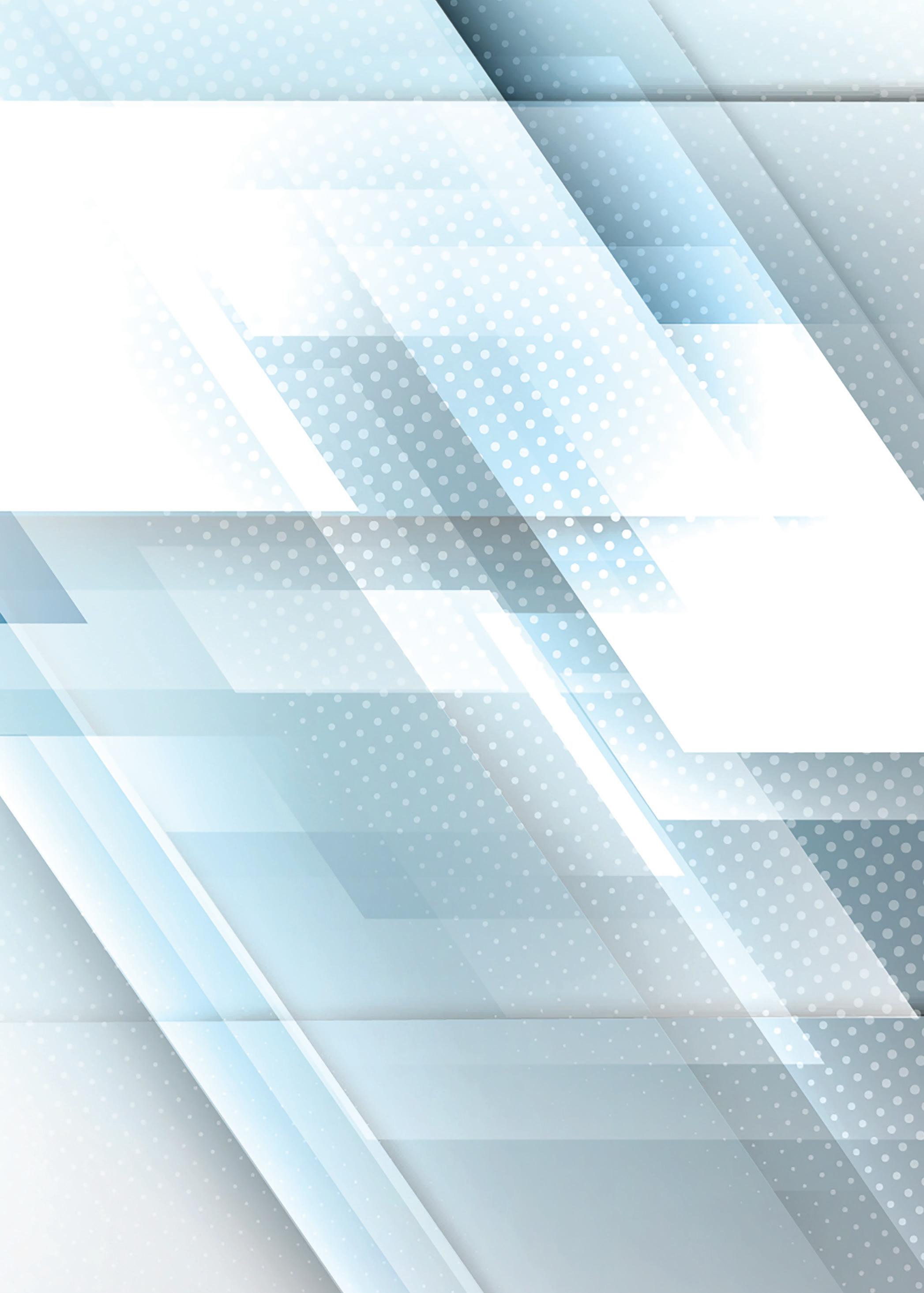
The printing machinery you have invested in has certain numbers that you bought into, amongst other printing speed time to set up and quality etc. none of those can on day-to-day basis be reached if you run the operation based on manual cleaning.
2. Reduced downtime
Downtime is bad for business. One thing is that the productions halts, because of a flaw or failure - the worst thing is that you must spend valuable time finding, where the fault is and then most of the time start all over again on your project.
With an automated cleaning machine for your press parts, you make sure that your printing machine is always clean and is always ready to do your next printing job – and do it well.
3. Prolong the lifetime of printing machine
Your printing machine is the heart of your production. It is the main thing that makes you money, but do you know what else makes you money? Proper cleaning.
Proper cleaning of you printing machine prolongs its lifetime and you get more in return on your investment and fewer do-over jobs, because you have a clean machine that does not affect your printing job.
4. Improve your HSE (Health and safety environment)
Manual cleaning of your press parts is a slow and tedious process that takes a lot of manpower. But what is even worse is the effect manual cleaning has on the cleaner’s health. Research show that a person that does manual cleaning is more likely to get sick and leave their position. Even if you want to do it right, setting up a manual cleaning operation without any health hazards is challenging.
Implementing automated cleaning significantly increases the overall health and safety of your employees and they are more likely to remain in their job for longer, which means you can concentrate on more important matters, than rehiring for the same position repeatedly.
5. Free up production space
Manual cleaning takes up a lot of space. You need space for all the equipment, solvents, and workers. Then you also need a place to dry all your press part and lastly you need a place to store the used material safely. With an automated cleaning machine, you immediately reduce the amount of space you need.
When you switch to automated cleaning you can create a new unique workflow for your production, where you bring the cleaning closer to the printing machine and in return reduce the time it takes to clean your machine even more.