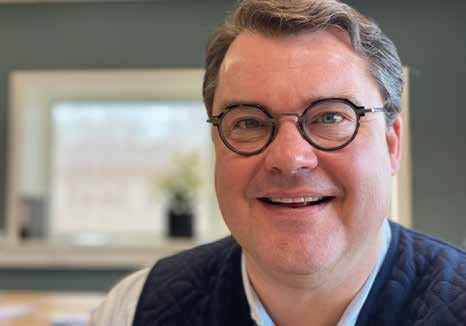
15 minute read
Duurzaamheid wordt drijver van de chemie
Het kan echt niet anders. Zonder duurzaam ondernemen zal je als bedrijf op termijn de boot missen. Daar van is Jeroen Wester veld, directeur van Kluthe Benelux BV (Kluthe), overtuigd. “Als je vanuit je productieomgeving CO2-neutraal of zelfs CO2-positief bent, zal je interessanter zijn.”
Kluthe is in transitie. Letterlijk. De kantoren en het tankenpark van de producent van chemische producten en procedés voor opper vlaktebehandeling aan de Produktieweg in Alphen aan den Rijn worden momenteel vernieuwd en zullen in 2025 volledig worden opgeleverd. Het pand zal dan dankzij duurzame oplossingen (lees: warmtepompen, centrale luchtbehandeling, gerecycled materiaalgebruik) vrijwel CO2-neutraal zijn. Je mag gerust zeggen dat de transitie van het pand van Kluthe een allegorie is van hoe de wereld van de opper vlaktetechniek verander t. Of moet veranderen, corrigeer t Jeroen Wester veld. De directeur van Kluthe wil zeker niet belerend zijn, maar hij waarschuwt wel.
Breder
Kluthe is een productiebedrijf dat chemische sto en ontwik kelt, produceert en levert aan de metaalbewerkende, lakverwerkende en gra sche industrie. Aan de metaalsector biedt Kluthe zowel mineraalolie en mineraalolievrije en synthetische koelsmeermiddelen aan, als waterige reinigingsmiddelen. En het scala is nog breder; het gaat van lakverdunners en spoelverdunners (inclusief destillatietechniek) tot aan voorbehandelingsmiddelen, ijzer-, zinkfosfateren, dunnelaagtechnologie en afvalwaterbehandeling. Speciaal is dat het op lage temperaturen werkt. Traditioneel werkt men in de lakverwerkende industrie met reinigen/ontvetten op 60 °C. Kluthe biedt producten aan waarbij het proces op 20 tot 30 °C functioneer t, met dezelfde resultaten.
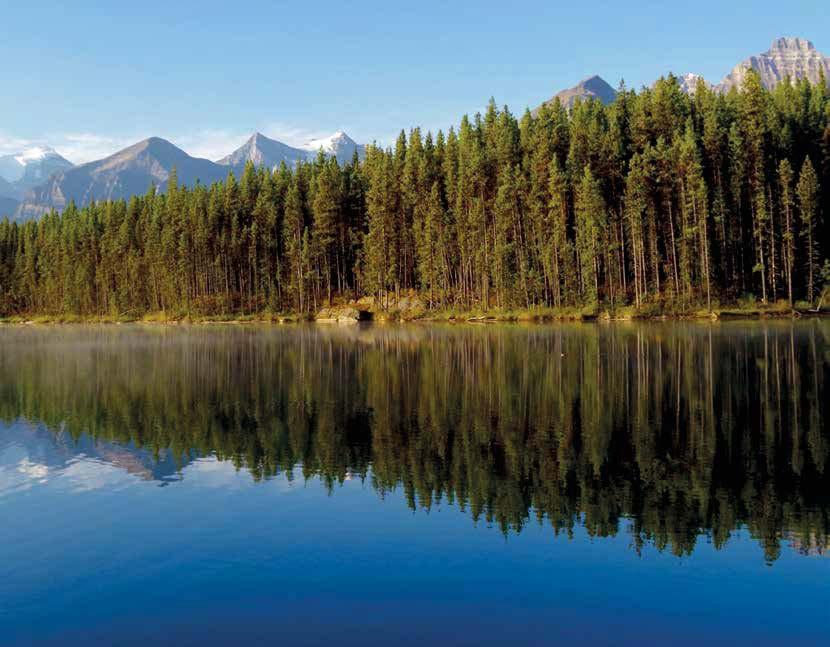
“Wij zijn ons er zeer bewust van dat we veel gebruikmaken van natuurlijke bronnen. Hoe minder we daar van gebruiken, hoe beter het is. Dus k ijken we altijd naar alternatieve, vaak biobased, oplossingen”, zegt Wester veld. “Dat is de kern van ons bestaan, al meer dan honderd jaar.”
Was die keuze voor duurzaamheid aanvankelijk ideologisch gedreven, vandaag de dag is circulair en duurzaam ondernemen van levensbelang, vertelt Wester veld. “We krijgen op kor te termijn in Europa voor mk b -bedrijven een CO2-tax. Deze CO2he ng is er al voor grotere industrieën. CO2 gaat er voor zorgen dat bedrijven niet meer alleen naar de prijs gaan k ijken, maar ook naar de individuele carbonfootprint van een product. Hoe minder CO2 je inkoopt, hoe lager de aanslag is Met andere woorden: als je vanuit je
BOS productieomgeving CO2-neutraal of zelfs CO2-positief bent, zal je interessanter zijn om geselecteerd te worden als leverancier In ieder geval verhoog je de fossiele voetafdruk van je klant niet; wellicht verklein je die zelfs.”
Kluthe Internationaal heef t het Klimaatak koord van Parijs omarmd. Dat betekent dat het bedrijf meewerkt om de opwarming van de aarde te beteugelen. De eerste stap die werd gezet, was de aankoop van 56 vierkante k ilometer bos in Canada. Het bos stond op de nominatie om te worden gek apt voor houtbouw. Kluthe heef t een apar t bedrijf opgericht, Kluthe Sustainability Limited, dat nu aan actieve bosbouw doet. Op dit moment heeft het chemiebedrijf acht boswachters in dienst. Die kappen alleen de bomen die verzadigd zijn of in de weg staan om bestaande bomen verder te laten groeien. Een van de extra doelen is om de bossen meer biodivers te maken. Het resultaat is niet alleen bosbehoud; de hele Kluthe Groep is zelfs CO2-positief geworden, volgens de standaarden van VCS (Veri ed Carbon Standard).
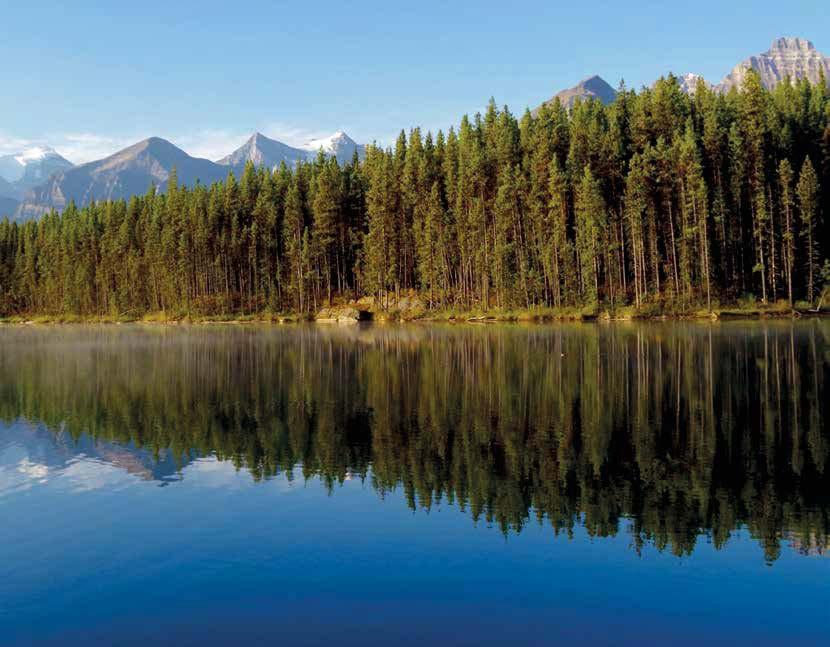
Footprint
Hoe ver gaat het? De automotive industrie in Duitsland - toch de kern van de combinatie metaal en lakken - wil al CO2-neutraal zijn. “Je moet daar wel in meegaan, anders kom je niet eens in aanmerk ing om te leveren. En in München, Stuttgart en Ingolstadt bepaalt men de norm.”
Wester veld ziet dat niet alleen Kluthe, maar ook andere bedrijven meer en meer open staan voor duurzaamheid. Tien jaar geleden was de por temonnee nog leidend, nu is er een kentering. Positief, vindt hij. Want de generaties na ons gaan hier van de vruchten plukken.
“Mis de boot niet, als je je plek in de keten wilt behouden. Sta open voor innovatieve technisch- chemische ont wikkelingen”
“We zullen onze administratieve systemen straks moeten aanpassen, omdat ook op de facturen de ‘product- carbonfootprint’ wordt afgedrukt”, voorspelt Wester veld. “Emissie per product gaat doorslaggevend zijn. Als je als lakverwerker of welk bedrijf dan ook hiermee nog niet bezig bent, ga je het heel zwaar krijgen. Duurzaamheid gaat een wens en een eis worden in de hele keten. Als je daar niet aan kunt voldoen, is je product niet meer relevant.”
SPAAK
Is dit toch een waarschuwing? “Ik ben niet de persoon die anderen de maat neemt. Maar bedrijven moeten actief verduurzamen; stilstand is geen optie Dat geldt voor iedereen, van het kleine mk b tot en met grote ondernemingen.
Mis de boot niet, als je je plek in de keten wilt behouden. Sta open voor innovatieve technisch-chemische ontwik kelingen. Het k an namelijk beter, veiliger en met minder milieubelasting.”
Waar k an het nog spaak lopen? “Er wordt met twee maten binnen de EU gemeten”, geeft Wester veld aan. “Het k an niet zo zijn dat we in Nederland andere vergunningsvoorwaarden hebben als in sommige andere EU-lidstaten. Er moet een level playing eld zijn. Anders komen er kostprijsverschillen en dat is oneerlijke concurrentie. Dit geldt ook nationaal voor de vergunningverlenende instanties en handhaving. Een gelijk speelveld is eerlijk voor iedereen.”
Akzo Nobel-duurzaamheidschef Bruinsma:
Wijnand Bruinsma van Akzo Nobel zet hoog in. Niet alleen zijn bedrijf Akzo Nobel moet duurzaam zijn, ook de keten waarmee het bedrijf werkt moet zich bewust worden van de uitdagingen. Niet alleen vanwege het milieu, maar ook vanwege economische kansen. Ook buiten de verf- en coating-sector. “Kernuitdaging is eigenlijk het koolstofvrij maken van de waardeketen.”
Akzo Nobel heeft onlangs ambitieuze duurzaamheidsdoelen aangekondigd voor zijn coating-business. Het bedrijf streeft ernaar om zijn CO2-uitstoot tegen 2030 met 42 procent te verminderen ten opzichte van de basislijn van 2020, en tegen 2050 CO2-neutraal te zijn. Om deze doelstellingen te bereiken, wil Akzo Nobel verschillende maatregelen implementeren, zoals het verhogen van het gebruik van hernieuwbare energie, het verbeteren van de energie- e ciëntie van zijn activiteiten en het ontwik kelen van meer duurzame producten.
Het bedrijf streeft er ook naar om zijn water verbruik tegen 2025 met 20 procent te reduceren en ervoor te zorgen dat in datzelfde jaar 100 procent van zijn op hout gebaseerde grondsto en afkomstig is uit duurzame bronnen. Wijnand Bruinsma is directeur duurzaamheid bij Akzo Nobel. Tijdens de European Coatings Show in Neurenberg gaf hij zijn visie over hoe verven en coatings een rol spelen in de duurzaamheidsdiscussie, vooral als het gaat om CO2-reductie
Wat is de rol van verven en coatings in een duurzamere toekomst?
“Onlangs liep ik langs van die grote windturbines en keek ik omhoog. Ik voelde me echt overschaduwd door het formaat er van en vroeg me af wat de impact van coating nu kon zijn op een enorme structuur als deze. Maar toen deed ik een stap terug en zag ik het barre klimaat waarin zo’n windturbine func tioneer t. En dan doen coatings er wel toe.”
“We kennen allemaal de foto’s van overstromingen, droogte en bosbranden. Ik ben geen k limaatactivist. Ik geloof in feiten en de wetenschap, en de IPCC-rappor ten zijn duidelijk. De k ans dat we kunnen zorgen voor een duurzame toekomst wordt snel k leiner. In de veer tig jaar dat ik op de planeet ben, is het aandeel koolstof in de atmosfeer met zo’n 25 procent gestegen. De gemiddelde temperatuur steeg met 0,7 of 0,8 graden. Dat klinkt misschien als weinig, maar het heeft een enorme impac t. Het aantal natuurrampen is verdubbeld. Dit zal niet stoppen, tenzij we nu handelen. Maar ik voel me overweldigd door de uitdaging waarvoor we staan.”
Wat kan de ver f- en coatingbranche daar aan bijdragen?
“Wat is de impact van ver f en coating op het totaal aan CO2? Ik heb een paar aannames gedaan en eigenlijk lijkt het maar een heel k lein aandeel. Er zijn 140 productiefaciliteiten in de wereld en die vormen maar een k lein deel van de totale footprint. Dat is niet veel, tenzij we van perspectief veranderen en kijken naar de totale waardeketen van verf en coatings. Ik heb het over de productie van grondstoffen, ver ven, aanbrengen van coatings, uitharden en de verwijdering er van. Vergelijk je dat met de voetafdruk van huishoudens, dan kom je op een aantal van 70 miljoen. De carbon footprint is even groot als die van alle huishoudens van Noor wegen,
Zweden, Finland, Duitsland, Nederland, België, Oostenrijk en Zwitserland bij elk aar Dat is de impact die onze sector heeft.”
Is Akzo Nobel klimaatac tivist aan het worden?
“Nee. We worden geen NGO, we zijn nog steeds een bedrijf en we doen zaken om geld te verdienen. Maar voor ons is duurzaamheid een belangrijke drijfveer
Van de bijna 11 miljard euro omzet is 4,3 miljard afkomstig van duurzame oplossingen. We willen dat laten groeien, maar al 40 procent van de omzet komt van Sustainable Solutions en we zien ook onze eindmarkten in die richting evolueren. We zien dat veel van onze klanten zich bij ons aansluiten bij het stellen van doelstellingen voor het koolstofarm maken om hun eigen ecologische voetafdruk te verk leinen. Ik denk dat de energiecrisis heel duidelijk heeft gemaakt dat onze klanten ook k ijken voor alternatieven met een lager energiegebruik.”
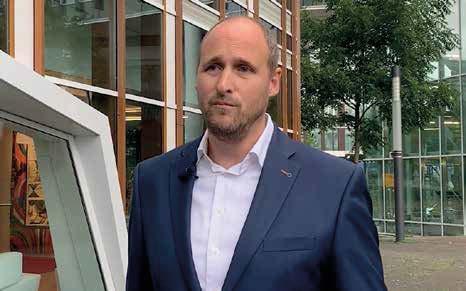
Hoe vullen jullie ‘groen’ concreet in?
“Bij Akzo Nobel concentreren we ons op drie belangrijke punten. Ten eerste gaat het om k limaatverandering. Dat is een enorme uitdaging is waarmee we worden geconfronteerd, maar het biedt ook k ansen omdat klanten om dit soort oplossingen vragen. Circulariteit is een ander belangrijk element. De kern van circula-
“We moeten de impact beperken door de overgang van oplosmiddelen naar watergedragen te maken. We moeten deel zijn van de oplossing, niet van het probleem” riteit is er voor zorgen dat de producten de tand des tijds doorstaan. Dat is wat wij doen. Maar het is ook een uitdaging om de substraten die we gebruiken te kunnen hergebruiken. En dan is gezondheid en welzijn een derde belangrijk gebied. We moeten de impact beperken door de overgang van oplosmiddelen naar watergedragen te maken. We moeten deel zijn van de oplossing, niet van het probleem.”
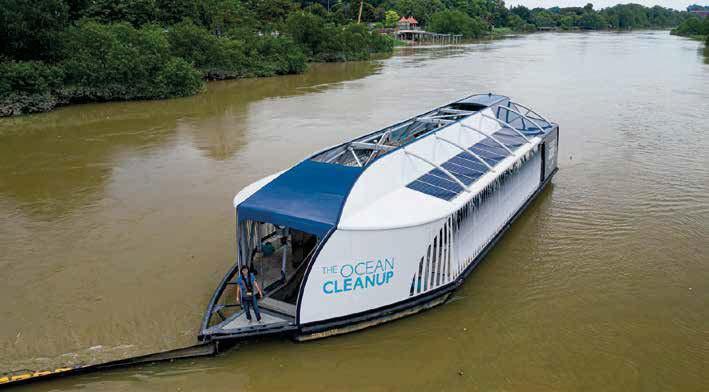
Jullie ambitie is groot: de CO2-uitstoot tegen 2030 met 42 procent verminderen. “We hebben vier ambities voor 2030. De eerste, en heel belangrijke, ambitie is 50 CO2-reductie in onze eigen activiteiten. We zitten daarbij al op 28 procent. We zijn goed op weg om ons doel voor 2030 te bereiken, maar de grote uitdaging ligt in de keten. De tweede ambitie is honderd procent circulair materiaalgebruik door hergebruik en recycling. In onze eigen activiteiten hebben we het afval aanzienlijk kunnen verminderen, en ongeveer 60 procent van het afval dat we nog hebben, kunnen we zelf hergebruiken of recyclen. Ten derde willen we onze inkomsten uit duurzame oplossingen laten groeien tot 50 procent. En last but not least: onze sociale inspanning We willen honderdduizenden mensen opleiden in samenlevingen om ons heen. Mensen met een minder bevoorrechte achtergrond opleiden tot de schilders en wetenschappers van de toekomst. Maar de kernuitdaging is eigenlijk het koolstofvrij maken van de waardeketen.”
Hoe gaan jullie de keten zo ver krijgen om ook koolstofvrij te worden?
“Meer dan 46 procent van onze totale CO2-voetafdruk zit bij onze leveranciers en de leveranciers van onze leveranciers 2 procent betreft onze eigen activiteiten. Nog eens 30 procent van de footprint zit bij de toepassing bij onze klanten, en solvabiliteit en end-of-life -aspecten omvatten allebei ongeveer 11 procent van de CO2afdruk. Hoe kunnen we de processen bij onze klant e ciënter maken? Hoe kunnen we ze minder energie -intensief maken?
Bijna 78 procent is echt gerelateerd aan de energie die wordt gebruikt om producten te maken. We hebben op 26 van onze locaties zonnepanelen geplaatst en er zijn lege daken en lege velden die we kunnen gebruiken om duurzame energie te produceren. In Europa gebruiken we 100 procent hernieuwbare elektriciteit en in Noord-Amerika hebben we aangekondigd dat we ook daar overstappen op 100 procent hernieuwbare elektriciteit. Maar er moet meer gebeuren. Hoe kunnen we overstappen? Denk aan warmtepompen, denk aan waterstof en waarschijnlijk zijn er meer goede ideeën. Elektri catie en het verk leinen van de ecologische voetafdruk zullen essentieel zijn.”
Is dat afdoende?
“We hebben enige tijd geleden onze poederarme bak producten gelanceerd, waardoor de uithardingstemperatuur wordt verlaagd. Door de huidige temperatuur te verlagen, verminderen we het energiegebruik van onze leveranciers en voor onze klanten. Dat bespaart niet alleen geld, maar verk leint ook de ecologische voetafdruk van onze klanten. Het overschakelen naar een andere uithardingstechnologie vereist ook investeringen van onze klanten, omdat ze hun lijnen en hun apparatuur moeten aanpassen. Het is dus onze taak om ze te helpen de juiste beslissingen te nemen en te ondersteunen bij het nemen van die beslissingen.”
“We hebben al een aantal jaren ons Waterway-programma. Dat was eerst gericht op sier- en houtproducten maar richt zich nu ook op metaal. Grappig toch, om iets tegen roest te beschermen met een product op waterbasis. We moeten blijven k ijken naar meer watergedragen producten en zoeken naar verschillende manieren om de hoeveelheid oplosmiddelen te verminderen. Er zullen enkele industrieën zijn waarin het erg moeilijk is of waarbij het nadelen zal hebben op andere gebieden die nog steeds oplosmiddel nodig hebben. Laten we k ijken naar manieren om dat op te vangen.”
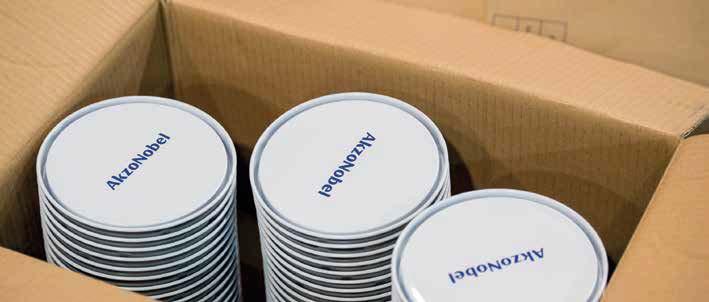
En circulariteit?
“Ik heb veel verfresten in mijn garage die ik zo nu en dan opruim. Die breng ik naar de milieudienst en dan worden ze waarschijnlijk verbrand. Wat als we die verf konden hergebruiken? Wat als we overgebleven verf konden gebruiken om weer een nieuw product te maken? Dat is eigenlijk waar het bij SikkensAlpha Recycle om draait. We gebruiken 35 procent van de gerecyclede verf om er een nieuw product van hoge kwaliteit van te maken. Maar k ijk ook verder dan onze eigen industrie In andere industrieën k an sprake zijn van afvalstromen die we eigenlijk heel goed in de onze zouden kunnen gebruiken. Bijvoorbeeld calciumcarbonaat dat we uit papierslib kunnen halen, een bijproduct van de de papierindustrie.”
Wat moet de coater doen?
“Laten we niet blijven gissen naar de CO 2voetafdruk van producten. Ik wil mensen aanmoedigen om samen te werken voor duurzaamheid en gegevens over de CO2voetafdruk van producten te delen. Zo kunnen we er echt voor zorgen dat we op feiten gebaseerde beslissingen nemen en in de goede richting sturen. Neem deel, en laten we samenwerken als je nieuwe oplossingen hebt; laten we samen innoveren. Grote ambities vereisen veel actie. Daarom nodig ik iedereen uit om met ons samen te werken.”
Kom voor het voet licht met de Informat.ION nieuwsbrief!
Kom via de digitale nieuwsbrief van de Vereniging ION in contact met meer dan 2.500 beslissers die allen werkzaam zijn in de oppervlaktebehandelende industrie.
Interesse?
Bel met Jetvertising b.v +31(0)70 399 00 00 of stuur een e-mail naar sales@jetvertising.nl
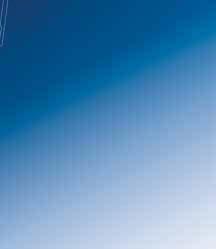
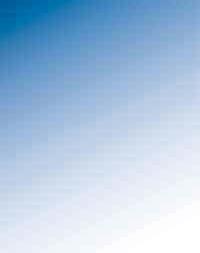
ERVAAR NU ZELF UW BESTE STRAALOPLOSSING: GRATIS EN VRIJBLIJVEND!
STRA ALKASTEN
Uitgebreid programma voor zowel droog, nat- als sodastralen
STRA ALKETE LS
Voor allerlei soor ten straalwerk, inhoud variërend van 18 tot 500 liter
VACUUMSTRA ALMACHINES
Veilige, schone straaloplossing voor spotreparaties en/of in-situ blasting
Ga bij de aanschaf van professionele straalapparatuur niet over één nacht ijs. Probeer eerst de vele mogelijkheden uit in de prak tijk en kom zo tot de beste oplossing van uw straalprobleem
Hiervoor bent u van harte welkom in ons unieke Experience Center in Ridderkerk Waar u niet alleen kennis maak t met de talloze straalmogelijkheden, maar ook met Gritco’s 33 jarige kennis en ervaring als ontwerper en fabrikant van hoogwaardige straalapparatuur
Galvamé inve steert in duurzaamheid:
Ron Gebuijs kijkt even naar de naam op de glazen deur van zijn vergaderruimte:
‘Joop’. Dat is zijn vader. Een paar kantoren verder zit de zoon van Ron. Het Rotterdamse Galvamé is specialist in opper vlaktebehandelingen van metalen producten en heeft duurzaamheid hoog in het vaandel staan. Zowel als het gaat om de familiebanden en het personeel, als wanneer het gaat om het productieproces.
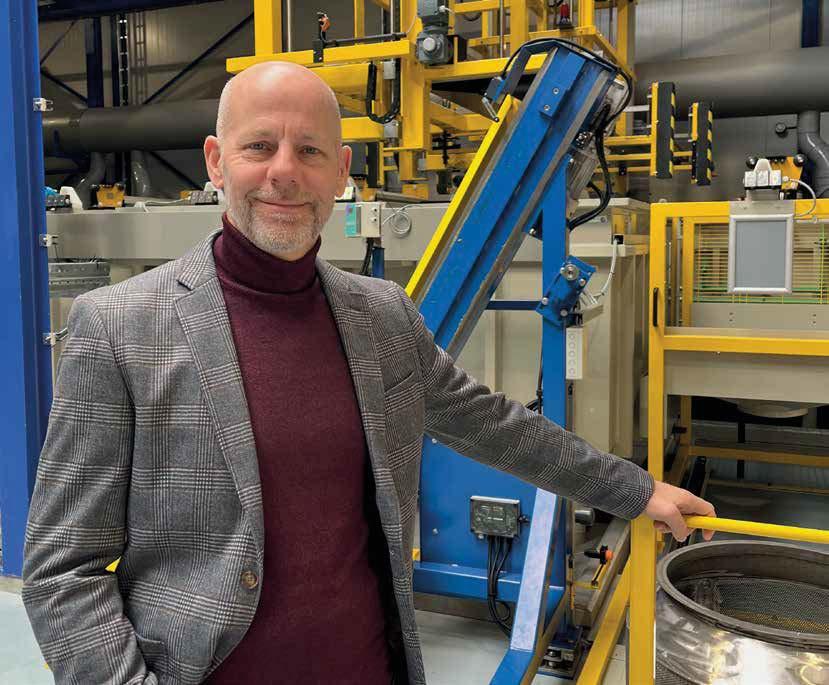
Chroom
Chroom en auto’s, het blijft een prachtig huwelijk. Dat weten ze ook bij de Volvo Klassiekers Vereniging. Op 18 maar t bracht de Regio West van de autoliefhebbersclub een bedrijfsbezoek bij Galvamé Metaalveredeling BV Vooral het verchromen van auto- onderdelen is favoriet. Maar het is geen sinecure, weet Gebuijs. “Zo’n excursie voor de Volvo Klassiekers Vereniging is ook voor ons leuk om te doen. Zij willen weten hoe wij de onderdelen van hun klassieke auto’s opnieuw verchromen, en wij kunnen ons werk showen. En begrip kweken voor het feit dat restauratiewerk niet altijd perfect k an worden. Je hebt namelijk niet altijd invloed op dat wat je tegenkomt bij een restauratie. De geometrie en de aanleverstaat van de onderdelen is van grote invloed op het eindresultaat.”
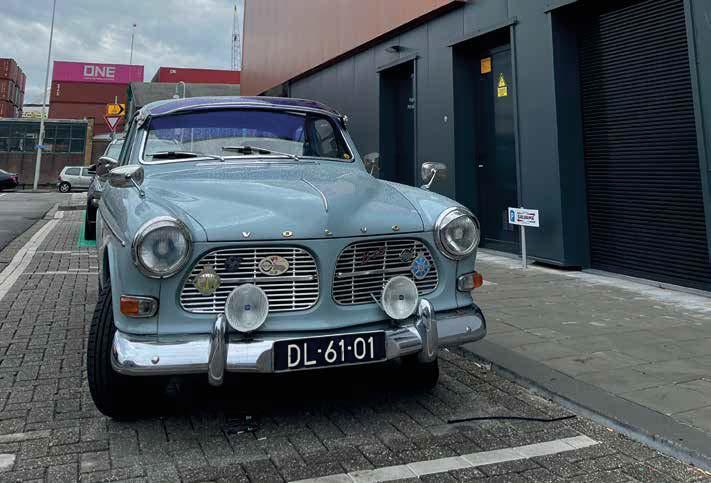
Op eerste Paasdag 2019 wordt Gebuijs gebeld. Het gebouw staat in brand. Zijn gebouw. Een van de panden waar Galvamé is gevestigd, heeft vlam gevat. Er is veel brand- en rookschade bij het Rotterdamse bedrijf. “Het was een onwerkelijke situatie toen ik vanaf het paasontbijt op de zaak kwam”, zegt Gebuijs. “Vragen uit de wijk, milieudienst Rijnmond wil alles weten, politie op de stoep. Het was heel hectisch, en toch word je dan even stil. Ik herinner me dat ik dacht: ‘Zo snel mogelijk schoonmaken en weer door ’.”
Op tweede paasdag moest hij de realiteit onderkennen: er was meer nodig dan een opk napbeur t. Dus kwam er een plan, met daarin twee elementen. Ten eerste ging het erom om zo snel mogelijk de productie waar mogelijk weer op te pakken. Deel twee was het vernieuwen van alles wat bij de brand verloren was gegaan. “Het was enorm improviseren om met onze mensen de productie weer relatief snel op orde te krijgen. Maar iedereen stond er volle bak achter. Gelukk ig zijn onze nieuwe afvalwater zuiveringsinstallatie en volautomatische productielijn onbeschadigd gebleven.”
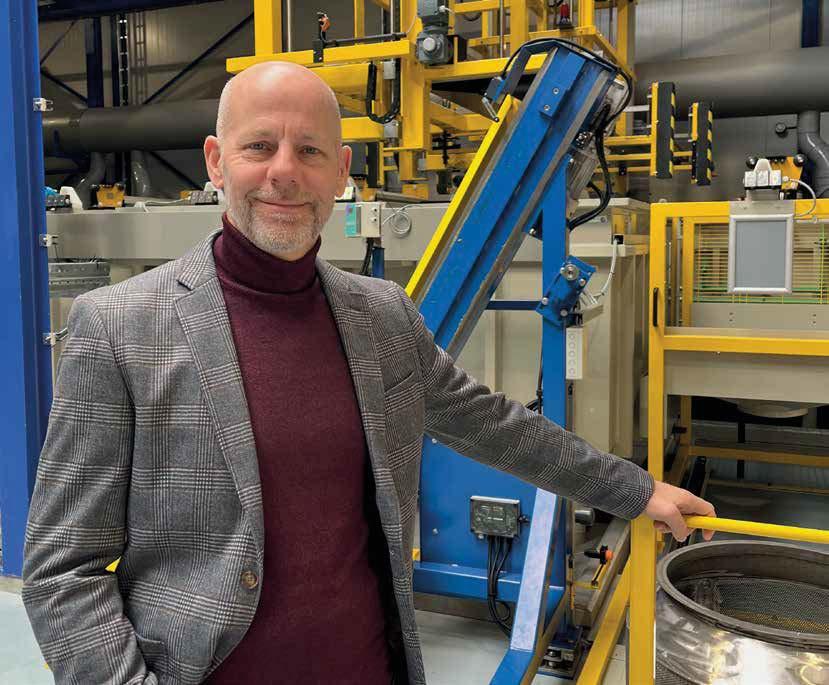
En dat vernieuwen? “Misschien zijn we er wel sterker uit gekomen”, zegt Gebuijs trots. Er is recent nog een nieuwe productielijn gebouwd, waarbij voor de badver warming gebruik wordt gemaakt van warmtepompen. “In overleg met de toeleveranciers hebben we gekozen voor energiezuinige processen op lagere temperaturen. Dat maakt het mogelijk om de baden met een warmtepomp te verwarmen, in plaats van met het traditionele cv-systeem. Dat is een keus die je wel zelf moet willen, want de warmtepompen kosten in dit geval circa 75.000 euro. We hadden er ook een cv-ketel van ongeveer 6.000 euro voor kunnen laten plaatsen.”
Gebuijs k iest niet alleen voor duurzaamheid omdat klanten het waarderen of omdat het op termijn wellicht rendabeler zou zijn. “Het is een persoonlijke overtuiging. We hadden bijvoorbeeld de nieuwe installatie van Duits fabricaat goedkoper in een ander land kunnen kopen, maar ik laat dan de mensenrechtensituatie en het regime dat in dat land aan de macht is sterk meewegen in mijn beslissing. Dat hoor t voor mij ook bij maatschappelijk verantwoord ondernemen. Iedereen ziet dat het anders moet. Je k an zelfs je vraagtekens zetten bij het idee dat elk bedrijf altijd moet groeien. Het houdt een keer op, denk ik. Dus wil ik de groei die we doormaken in ieder geval op een verantwoorde manier doen.”
ONDERGEWAARDEERD?
Galvamé bestaat sinds 1944, is specialist in opper vlaktebehandelingen van metalen producten, en gevestigd in het Waalhavengebied in Rotterdam. In 1983 nam Joop Gebuijs het bedrijf over van toenmalig eigenaar Klaas Ketting. Ron heef t het in 1994 van zijn vader Joop overgenomen. Nu werken twee van de zoons van Ron ook in het bedrijf. Sinds 2021 is de oudste van de twee bedrijfsleider
Binnen de familie is de liefde voor galvaniseren duidelijk. “Wat we vooral willen doen, is de techniek achter het proces uitleggen”, zegt Gebuijs. “Galvaniseren is lastige materie en nog steeds een belangrijke techniek in de industrie. Ondanks dat het basisprincipe al een tijd bekend is, zie je dat er veel bij komt kijken om op het hoogste niveau mee te draaien. Globaal schat ik dat er makkelijk 150 variabelen zijn die een rol spelen in een gemiddeld galvanisch proces. Met alle verschillende samenstellingen, stroominstellingen, temperaturen en mogelijke verontreinigingen is het een uitdaging om het proces telkens k loppend te krijgen.”
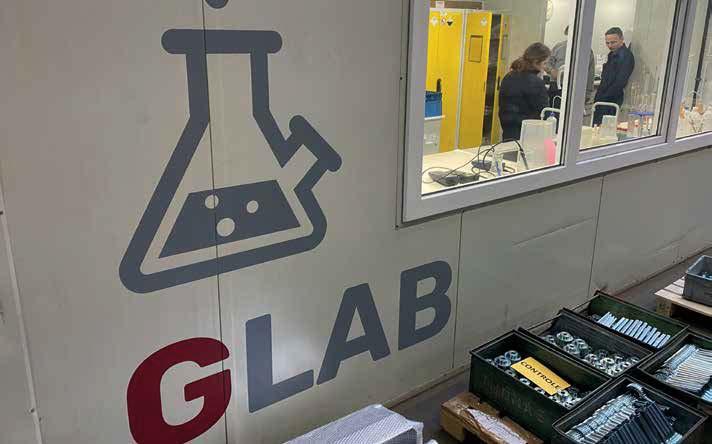
Is galvaniseren een ondergewaardeerde techniek? “Als je onze bewerking bek ijkt ten opzichte van de waarde van het product, omvat het vaak maar een klein deel van de maakkosten van het hele product. Ondanks een langzame afname van het aantal galvanische bedrijven, blijft de concurrentie scherp. Tegenwoordig merken we dat k lanten eenvoudig met een paar mailtjes bij verschillende galvaniseerders prijzen kunnen opvragen en dan simpelweg de goedkoopste kunnen kiezen. Dat maakt het lastiger Toch merken we dat onze kwaliteit en ser vice dan onze belangrijkste wapens zijn. Daardoor kunnen we aan de top blijven meedraaien. Een ander voordeel voor Galvamé is dat er veel verschillende bewerkingen in-huis gebeuren. Klanten vragen om zo’n one -stop-shop.”
Nerveus
Bij het bedrijf van Gebuijs kunnen ze elektrolytisch verzinken, vernik kelen, verchromen, verkoperen, ver tinnen, ver zilveren, chemisch vernik kelen, elektrolytisch polijsten, beitsen/passiveren, en restaureren. Met de nieuwe productielijn is daar ook trommel-zink-nikkel bijgekomen, gecombineerd met dickschicht of zwar t passiveren. “Nu hebben we gemiddeld zo’n 60 tot 70 orders per dag. Om die e ciënt en snel te kunnen verwerken, is een hoge mate van automatisering nodig Waar we naar toe willen, is dat we een soor t Bol.com worden. Een order komt binnen en gaat in maximaal vijf werkdagen weer terug naar de k lant. Wij proberen onze klanten nadruk kelijk te ontzorgen bij de uitbesteding bij ons. De klant moet er zo min mogelijk omk ijken naar hebben, en altijd kunnen rekenen op de door ons bevestigde afspraken.”
In 2006 is de eerste volautomatische lijn gebouwd. Maar het bedrijf heeft zich niet gericht op het echte massa-verzink werk. Belangrijker was veel exibiliteit in de besturing van die lijn, zodat het alle mogelijk aanlevercondities en verschillende kwaliteitseisen aankan. “Ondanks een hoge mate van variatie in de producten, was automatisering toch een must. Een aantal van onze klanten komt bijvoorbeeld uit de wereld van de automotive. Als die horen dat een lijn nog handmatig bediend wordt, worden ze ner veus. Dus voor ons was het geen optie om niet te automatiseren.”