
12 minute read
Zonnige toekomst voor productie bedrijf dat zelf poedercoat
Organische deklagen Zonnige t oekomst voor produc t iebedrijf dat zelf poederc oat
Donk Industries ontwerpt en maakt allerlei aluminium producten, geeft ze een nabewerking en doet ook het poedercoaten zelf. Dit vanuit de bedrijfsfilosofie dat ze hun klanten van a tot z willen ontzorgen. Voor al dat werk beschikt het bedrijf over veel verschillende afdelingen met in totaal 140 medewerkers. Ze hebben nooit overwogen het poedercoaten uit te besteden. Alles zelf doen voorkomt communicatieproblemen en leidt makkelijker tot een constante, hoge kwaliteit, is de redenering. Wat betekent dit alles voor het productieproces?
Een belangrijk gevolg van deze benadering is een groot aantal verschillende werkzaamheden en afdelingen. De matrijzen worden immers zelf gemaakt, evenals de tekeningen daarvoor. Het gewenste aluminium kan op verschillende manieren worden geproduceerd. Bijvoorbeeld handmatig coquille gieten voor klein seriewerk in matrijzen van stalen blokken, hogedruk spuitgieten voor grotere series of wat complexere delen, vacuüm gieten van aluminium als een heel hoge kwaliteit gewenst wordt, Zamak-spuitgieten met een zink-aluminium legering waarmee je heel dunwandig kunt spuitgieten, maar ook kunststof spuitgieten en tot slot handmatig slijpen.
De gehele productielijn kent veel verschillende afdelingen, zoals een gereedschapsmakerij, een gieterij, een nabewerkingsafdeling (frezen), een zagerij voor pro elen, twee poedercoatlijnen en een assemblage-afdeling. “Wij maken heel veel verschillende producten voor veel verschillende markten en dat doen we al negentig jaar”, vertelt Gilbert Schmitz, hoofd verkoop. “We werken in ploegendiensten en zijn met name gespecialiseerd in klein en middelgroot seriewerk, zowel qua aantallen alsook qua gewicht van de producten. Dus vanaf twintig gram tot een kilo of tien maximaal.” A L L E S I N E I G E N H A N D In-house worden talloze verschillende producten gemaakt en gepoedercoat, varierend van extrusiepro elen, aluminium gietstukken, diverse producten voor zonweringen en assimilatieverlichtingsbakken voor tuinkassen, tot allerlei behuizingen voor verlichtingsarmaturen en andere apparaten, alsook allerlei consumentenartikelen – eigenlijk ieder onderdeel van aluminium of waar iets van kunststof aan zit. De markten waarvoor het bedrijf produceert, lopen uiteen van elektronica, medische industrie, automobielindustrie tot lucht- en ruimtevaart, o shore en zonweringsindustrie. “Voor de o shore-wereld hebben we in de loop van tientallen jaren heel veel ervaring opgedaan om de juiste combinatie te maken die lang bestand is tegen de inwerking van zout en zonlicht. Die combinatie heeft betrekking op het gietstuk, de juiste aluminium-legering, de voorbehandeling en het poedercoaten. We hebben ook heel veel testen gedaan om die combinatie zo goed te krijgen. Daarbij gaat het onder meer om verlichtingsdelen op schepen, boortorens en op windmolens op zee.”
Handmatige poedercoatlijn voor klein seriewerk.
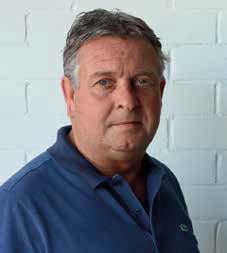
Gilbert Schmitz.
De afdeling poedercoaten is opgesplitst in twee lijnen: een volledig geautomatiseerde lijn voor groot seriewerk en een handmatige lijn voor klein seriewerk en voor werk waarbij snelle kleurwissels gewenst zijn. De chemische voorbehandeling bestaat uit ontvetten, beitsen, spoelen en dan drogen in een droogoven. De baden zijn louter en alleen gemaakt voor de behandeling van aluminium. De ovenbehandeling heeft niet alleen als doel te drogen, maar ook om luchtinsluiting in de producten zoveel mogelijk tegen te gaan. De automatische lijn en de handmatige lijn komen aan de achterkant weer bij elkaar voor de mo eloven. Op de producten wordt geen primer aangebracht, alleen één of meer lagen poedercoating. Voor o shore toepassingen zijn dat vaak drie lagen. Soms staat in de automatische lijn een spuiter in de cabine om op bepaalde plekken een extra laag aan te brengen. De totale laagdikte varieert van enkele micrometers tot ongeveer 200 micrometer.
K W A L I T E I T S C O N T R O L E S “We hebben nooit overwogen het poedercoaten uit te besteden. We willen juist alles in eigen hand houden. Bij uitbesteding krijg je te maken met zaken als transport en communicatie, maar ook met eventuele beschadigingen en afkeur. En dan krijg je discussie; ook eventuele miscommunicatie kunnen we zodoende ondervangen. Verder neemt bij uitbesteden de doorlooptijd toe en die heb je dan niet in de hand. Wij kunnen vanaf de opdrachtbon in twee tot drie weken een product ontwerpen, maken, nabewerken, poedercoaten en assembleren. Al die handelingen hebben we op elkaar afgestemd. Wij zijn altijd volledig verantwoordelijk voor onze producten en hebben hier één aanspreekpunt. Ook als het bijvoorbeeld gaat om het assembleren van aluminium onderdelen waar een kunststof deel in moet passen.”
Die totale verantwoordelijkheid betekent ook: regelmatige kwaliteitscontroles in de hele productie. Een belangrijk aandachtspunt vormen de luchtinsluitingen die tijdens de productie kunnen ontstaan. Die zijn vast te stellen door simpelweg het gewicht van producten te meten. Als iets 1,8 kilo moet wegen en het weegt 1,76 kilo, dan zijn er dus luchtinsluitingen. Bij het vervaardigen van prototypes maakt het bedrijf ook gebruik van mold ow analyseapparatuur, om vroegtijdig te zien waar luchtinsluitingen kunnen ontstaan. Verder worden visuele controles uitgevoerd bij het nabewerken, poedercoaten, assembleren en verpakken. Aandachtspunten zijn kleur, glansgraden en gewenste texturing op het eindproduct. Die controles zijn extra belangrijk vanwege de exibiliteit in de bedrijfsvoering. Donk Industries kan alle genoemde bewerkingen doen, maar ook slechts een deel daarvan als de klant dat wil. Ook zijn er klanten met klein seriewerk, korte doorlooptijden of klanten die niet vast willen zitten aan een bepaalde levertermijn. Die exibiliteit zou kunnen gaan botsen met de vereiste kwaliteit, wat het bedrijf door regelmatige controles en automatisering wil ondervangen.
G R O E N E T O E K O M S T Hoe ziet het bedrijf de toekomst? Gilbert Schmitz: “Wij hebben maatschappelijk verantwoord ondernemen hoog in het vaandel staan en kijken dus goed hoe we afval kunnen verminderen dan wel hergebruiken, en hoe we energiebesparing en -hergebruik kunnen realiseren. Wanneer je als productiebedrijf in Nederland wilt blijven voortbestaan, dan moet je op die gebieden echt stappen maken. Zo willen we zonnepanelen op ons dak gaan plaatsen en warmte uit de ovens gaan terugwinnen. Ook willen we verder gaan met automatiseren, met name in de gieterij. Maar alles moet in samenhang bekeken worden, want als producten bijvoorbeeld sneller uit de gieterij komen, heeft dat invloed op alle stappen daarna. Verder zien we bij grote productiebedrijven in Europa de tendens om de productie van China naar Europa over te hevelen. Dan zullen wij ook vaker in beeld komen, zeker als we passen in het plaatje van groen ondernemen.”
Voorbeelden van aluminium onderdelen

M E E R I N F O R M A T I E www.donkindustries.nl
Lees verder of reageer
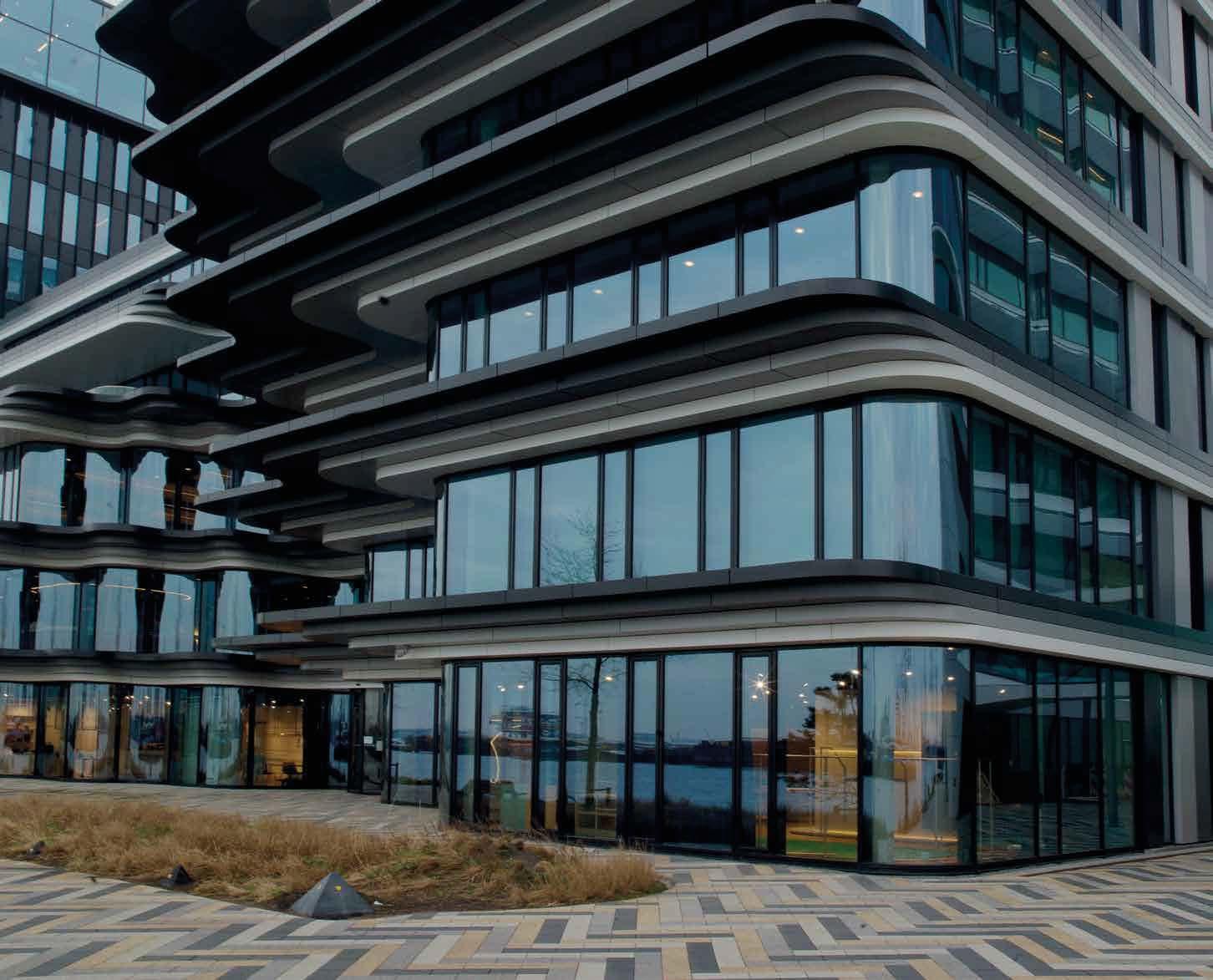
Tro ts op het werk
Het bedrijfsgebouw DK125 in Amsterdam is te zien als een waar kunstwerk. Het gebouw kenmerkt zich door golvende uitkragingen, geleverd door gevelbouwer Aldowa. De gevel is opgebouwd uit veel ronde delen in vier matte kleuren. De poedercoatings voldeden aan de vereisten van de bouwindustrie en zijn Qualicoat klasse 1 en GSB goedgekeurd. Door de radius van de gebogen en gelaste delen was het voor Schoen Poedercoating een uitdagende opdracht. Het bedrijf heeft voor dit project speciale ophanghaken moeten maken om het coatproces optimaal uit te kunnen voeren. Daarnaast was tussen opdrachtgever en poedercoater een afwijkende leverafspraak overeengekomen. De gecoate objecten werden zonder tussenkomst van de opdrachtgever direct bij het bouwproject afgeleverd. Daarvoor is ook een bepaalde verpakkingsmethode ontwikkeld. Door de levering werden de materialen per etage verwerkt. Een intensieve samenwerking in de keten, een goede planning en een strenge uitgangscontrole hebben bijgedragen aan een voorspoedig bouwproces. De klant heeft ook gekozen voor een maximale conservering: een twee lagensysteem van 110 micrometer volgens Qualicoat SEASIDE.
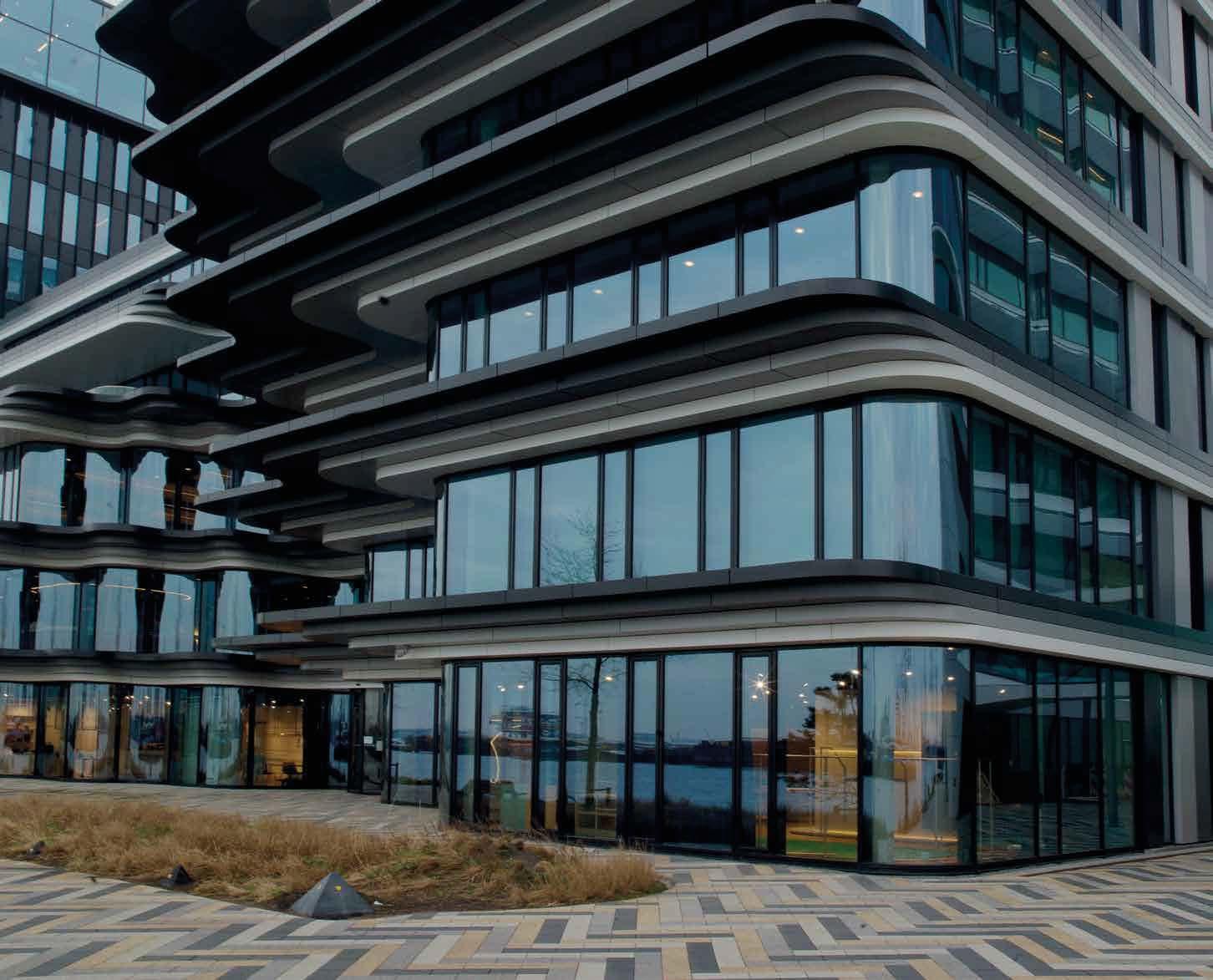
Algemeen Planmat ige aanpak van energiet ransit ie en CO -reduc t ie2
In de komende decennia vindt een energietransitie plaats om de klimaatverandering te beperken. In het coalitieakkoord van december 2021 heeft de Nederlandse overheid op basis van het Europese “Fit for 55” de CO2-reductiedoelstelling verhoogd van 49% naar 55%. Een enorme uitdaging. Dit artikel behandelt twee belangrijke aspecten die bijdragen aan het reduceren van de CO2-uitstoot en toont een stappenplan hoe dit in een oppervlaktebehandelend bedrijf gerealiseerd kan worden.

De aspecten die bijdragen aan het reduceren van de CO2-uitstoot zijn: • Energiebesparing verbreedt zich naar CO2-reductie in scope 1, 2, en 3-maatregelen • Een langetermijnvisie op CO2-reductie en energiebesparing laat zien dat meer mogelijk is dan we nu denken, als we maar anticiperen en sturen op verandering en innovatie.
De energietransitie vindt plaats door CO2-reducerende maatregelen te nemen, de juiste keuzes te maken op natuurlijke momenten en het toepassen van innovaties. In de Europese Klimaatwet zijn doelen vastgelegd voor een klimaatneutrale EU in 2050 en een vermindering van broeikasgasemissie met 55 procent in 2030 ten opzichte van 1990. Deze doelen moeten worden verwezenlijkt enerzijds door energiebesparing en anderzijds door vergroening van de opwekking van elektriciteit en warmte, resulterend in CO2-reductie.
O P W E G N A A R C O - R E D U C T I E2 De koolstofemissies (CO2) worden voor een groot deel veroorzaakt door het gebruik van fossiele brandsto en. Bedrijven zetten momenteel volop in om hun CO2 -emissies te reduceren. Je kunt zeggen dat de focus op energiebesparing verbreedt naar CO2 reductie. Wat houden die CO2 -emissies in? Volgens het toonaangevende GHG Protocol (Green house Gas) worden de broeikasgasemissies van een bedrijf ingedeeld in drie scopes:
Scope 1-emissies
Dit zijn directe emissies van middelen die eigendom zijn van en gecontroleerd worden door het bedrijf. Met andere woorden: emissies komen in de atmosfeer als direct gevolg van activiteiten op bedrijfsniveau (zoals ovens, stoomketels, branders, oplosmiddelen, procesemissies, voertuigmotoren).
Scope 2: indirecte emissies
Scope 2-emissies zijn indirecte emissies die ontstaan door de opwekking van bijvoorbeeld elektriciteit, warmte en koeling in installaties die niet tot de eigen onderneming behoren, doch die door de organisatie worden ingekocht en gebruikt. Voor de meeste bedrijven en organisaties zal elektriciteit de enige bron van scope 2-emissies zijn.
Scope 3: indirecte emissies
Scope 3-emissies zijn alle indirecte emissies die niet opgenomen zijn in scope 2, maar plaatsvinden in de waardeketen van een bedrijf. Deze zijn te onderscheiden in stroomopwaartse emissies (bijvoorbeeld gebouwen, aankoop machines, technologie, voertuigen) en in stroomafwaartse emissies (bijvoorbeeld bij distributie, in de gebruiksfase), gekoppeld aan de bedrijfsactiviteiten.
De meeste bedrijven leggen bij hun CO2
reductieplannen de focus op scope 1 en 2-maatregelen. Vaak zijn dit “vertalingen” van de energiebesparingen naar CO2 reductie. Scope 3 voelt voor velen nog als buiten de invloedsfeer en lastig te beheersen en te kwanti ceren. Echter: er zijn al veel initiatieven op dit vlak. Zo ziet de chemische sector in Nederland het recyclen van koolstofcomponenten als een belangrijke CO2-reductiemaatregel. Voor de oppervlaktebehandelende industrie kun je stellen dat zij positief bijdraagt aan

scope 3 via de verduurzaming van materialen door corrosievorming tegen te gaan. Een bekend instrument is de CO2-Prestatieladder die bedrijven en overheden helpt bij het inzichtelijk maken en het reduceren van CO2 en kosten.
C O - R E D U C T I E O P T I E S2 De kunst is om in een bestaande locatie het productieproces geleidelijk om te bouwen met nieuwe CO2-reducerende technieken die bruikbaar zijn in de branche oppervlaktetechnieken. Vaak zijn dit vergelijkbare processen als in de huidige situatie, maar slimmer op elkaar afgestemd, met minder verliezen, met sensoren die het proces exact naar behoefte regelen (Advanced process control, Smart Industry) en elektri catie.
Als we dan de focus op aardgasreductie (scope 1) leggen, zijn de voorbeelden: • Hybride uitvoering van droogovens en mo elovens, deels elektrische, deels gas uitgevoerd • Goede isolatie van de ovens • Restwarmtegebruik zodat aardgasverwarming voor halverwarming en
gebouwen wordt geëlimineerd • Naverbranders vervangen door gaswassers, of de restwarmte ervan volledig gebruiken • Compartimenteren: alleen die secties verwarmen die functioneel zijn, de rest niet • Klanten goed opleiden om “onder”- en
“over”-speci catie van coatings te voorkomen • Overleg met leveranciers over welke oppervlaktebehandelingstechnieken minder CO2-belastend zijn.
Ook elektriciteitsbesparing blijft nog steeds mogelijk (scope 2, is ook gasbesparend op basis van de huidige wijze van elektriciteitsopwekking). Denk aan optimaal geregelde afzuiging en ventilatie, led-verlichting in hallen, persluchtcompressoren vervangen door oplossingen met stappenmotoren om werkstukken in positie te brengen in plaats van persluchtcilinders te gebruiken, elektrisch intern transport, eigen opwekking met PV (zonnestroom). H E T C O O F
2 E N E R G I E T R A N S I T I E P L A N Bij energiebesparende maatregelen denken we vaak aan de erkende maatregellijsten uit de Informatieplicht energiebesparing. Het kiezen van de juiste maatregelen met impact op de CO2 -emissie in het vier-jaren-stramien van het Activiteitenbesluit milieubeheer of de Europese Energie E ciëntie Richtlijn (EED) is niet eenvoudig. Vroegtijdige vervanging om energieredenen is vaak niet aantrekkelijk. En hier zit nu juist het voordeel van het opstellen van een transitieplan tot CO2-neutraal produceren in 2050. Het transitieplan biedt meer vrijheid om oplossingen te bedenken en in te spelen op de natuurlijke vervangingsmomenten en innovaties van installaties, gebouwen en productieapparatuur. Er is dan sprake van meerkosten ten opzichte van een “standaard” investering. Bij deze vraagstukken wordt niet uitsluitend naar energiekosten en energiebesparingen gekeken, maar wordt naar CO2-reductie in combinatie met andere voordelen voor een bedrijf gezocht. Denk aan hogere productiecapaciteit per apparaat, betere productkwaliteit, logistieke voordelen,
Figuur 1: Routekaart met CO2-reductie projecten in een tijdspad
verdergaande automatisering, reductie van grondsto enverbruik, arbo-veiligheid, waarde voor eigenaren en aandeelhouders, enzovoort.
Traditioneel komt de meeste CO2-reductie voort uit maatregelen voor utilities en de inkoop van hernieuwbare energie. Om CO2-reducties te realiseren van 50 tot 90 procent zijn echter ook maatregelen vanuit de kern van de processen nodig. De verduurzamingsopties van toekomstige CO2-reducerende alternatieven zijn daarmee te vinden op de drie keuzevelden (KWA Triple Choices model): 1. De proces unit operations; CO2 reductie in de productieprocessen (ovenproces, keuze ander type oppervlaktebehandelingsproces, temperatuurniveau, elektrisch in plaats van warmte) 2. De energieconversiesystemen;
CO2-reductie in de utilities (zoals de stoomketel, koeling, perslucht) 3. De energiebronnen; CO2-reductie door de inzet van andere energiebronnen (CO2-arme of CO2-vrije energiebronnen, hernieuwbare energie). R O U T E K A A R T Uiteindelijk leidt het uitwerken van de CO2-reductieopties tot een lijst van projecten die wordt gepland zoals in guur 1 staat als voorbeeld. Zo ontstaat een routekaart op een tijdslijn naar 2030 en verder ( guur 2). Om de innovaties en grote veranderingen te implementeren, is een goede voorbereiding nodig. Vandaar dat de voorbereiding expliciet is meegenomen in deze routekaart. Per maatregel of project wordt CO2-reductie voor scope 1 en 2 berekend. Zo ontstaat een CO2-reductielijn die het uiteindelijke transitiepad naar CO2-neutraliteit inzichtelijk maakt. Het KWA Triple C-model is als tool met handleiding op te vragen bij uw contactpersoon van KWA Bedrijfsadviseurs.
Het transitieplan vraagt een lange termijnaanpak waar iedereen in het bedrijf zich aan conformeert en staat daarmee als een soort paraplu boven de organisatie. Borgen ervan kan in een ISO-systematiek ofwel het Energiemanagementsysteem ISO 50001. Realiseer je dat de energietransitie geen keuze is, maar de manier waarop je deze vormgeeft wel. Faseer, start met wat ertoe doet en breidt dit uit. Gun jezelf haalbare doelen en vier het behalen ervan. Zo wordt het nog leuk ook.
Fons Pennartz Senior-adviseur Energie en Procestechniek KWA Bedrijfsadviseurs
M E E R I N F O R M A T I E www.lokogalvano.nl www.kwa.nl www.co2-prestatieladder.nl/nl (Maatregellijst 2022)
Lees verder of reageer
Figuur 2: Planningstool maatregelen en resultaat in verloop van de CO2-emissiereductie, indicatief