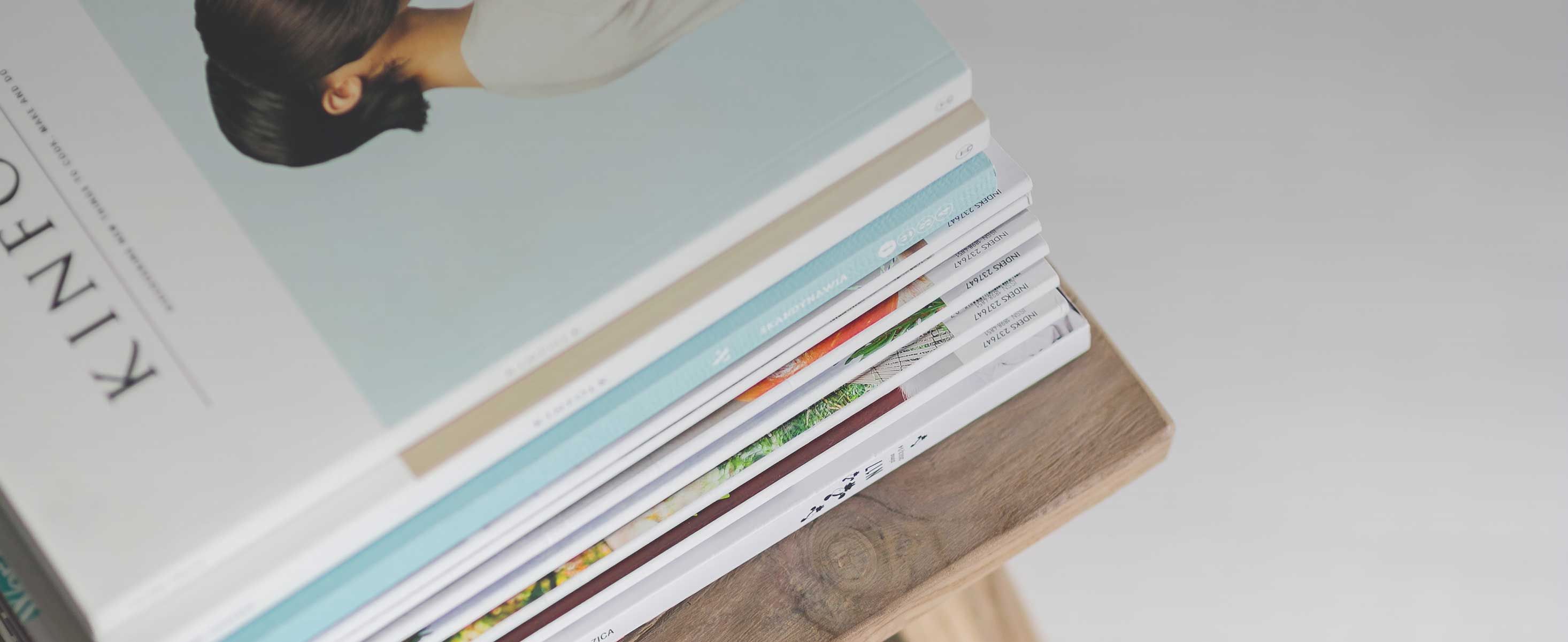
2 minute read
Peter Hay Kitchens Peter Kitchens in par tner ship with HOMAG in partnership with HOMAG
The recent installation by Auckland based Peter Hay Kitchens of three sophisticated edgebanding production line machines from the EDGETEQ S-500 range made by German manufacturer HOMAG AG represent not only a substantial commitment to the development of new processes and the use of technology but also to HOMAG AG as the mentor behind the technology. Bob Nordgren from JOINERS Magazine spoke with both owner Peter Hay and Sales and Marketing Manager Karl O’Hanlon about this latest install that moves the business ever closer to the creation of a world class Batch One processing line for cabinet production, a process they started back in 2015.
The three edgebanders including one with the latest HOMAG airTec technology have enabled the business to deal with the challenge of meeting increased demand by producing efficiently more volume in kitchen and bathroom cabinet production and the variation in jobs to be performed. These machines are capable of working with all types of edging materials be they solid or veneer. The integration of their existing returns provide for greater productivity as part of the Batch One system.
“We needed a partner who in our view could take us through to the full potential of automated production machinery. Choosing HOMAG Group was a decision based on the future and where we see our future business going. We came to the conclusion that HOMAG as the leading manufacturer of robotics and automated machinery made for that partner” explains Peter. “They fit as the machinery supplier who have developed the best technology and most importantly, continue to develop their technology down to the smallest detail. This detailed approach in all aspects of their machinery is vital to our business.”
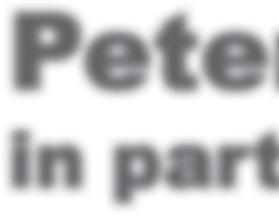
One of the more interesting outcomes has been the use of all the production data to help grow the business. Karl says “This has become a powerful tool for us to grow and develop the business in terms of sheer production as well as the future direction.” The factory operation has been digitally linked to HOMAG AG in Germany. This enables any issues with their operation and maintenance to be addressed quickly and effectively.
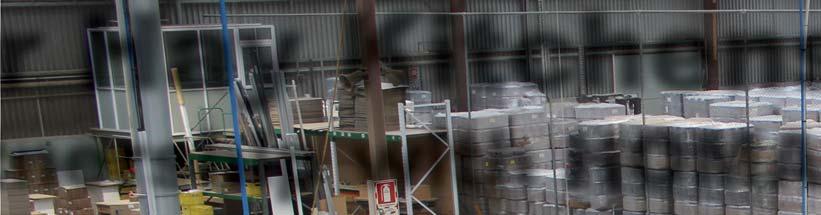
“These machines are the very latest in edgebanding technology.” comments Karl. “The inclusion of the FF32 multi trimming unit and the use of a multi profile scraper offers us a greatly improved quality of finish. These machines offer us real flexibility such as being able to use either PUR or EVA glues as well as airTec. The use of hot melt glue is quick and easy to set up and clean. They provide for greater configuration options through the processes of premilling, gluing and post processing.
In particular they offer us three key features: perfect trimming through vibration free tooling, minimal set up time with multi profile technology and optimum processing due to servo controlled positioning throughout the machine. The airTec option means zero joint technology that produces even better quality finishes.”
The business has benefited in several ways from this technology. There has been low staff turnover. “Through this kind of investment in the business it has made life easier for everyone. In many cases staff can now take on more functional roles than before. For our clientele be they merchants, ‘brownbox’ or commercial anywhere in New Zealand we are able to meet demand for whatever they need ontime.”
The use of technology, automation and software at their 10,000m2 factory will continue to see Peter Hay Kitchens as the foremost business of its kind here in New Zealand. “I believe our partnership with HOMAG Group with their developed and developing technology and their Imos/HOMAG iX software will see this business go forward as a world class operation.” says Peter.
With the business to have it’s 50th anniversary in 2023 there will be even more to celebrate.
For more information contact Karl O’Hanlon at Peter Hay Kitchens on 09 573 0225 or karl@ peterhaykitchens.co.nz or visit www.peterhay.co.nz all managed by Maestro active watch supervision software that allows for the production process to be managed and controlled by monitoring the status of the individual machines in real time