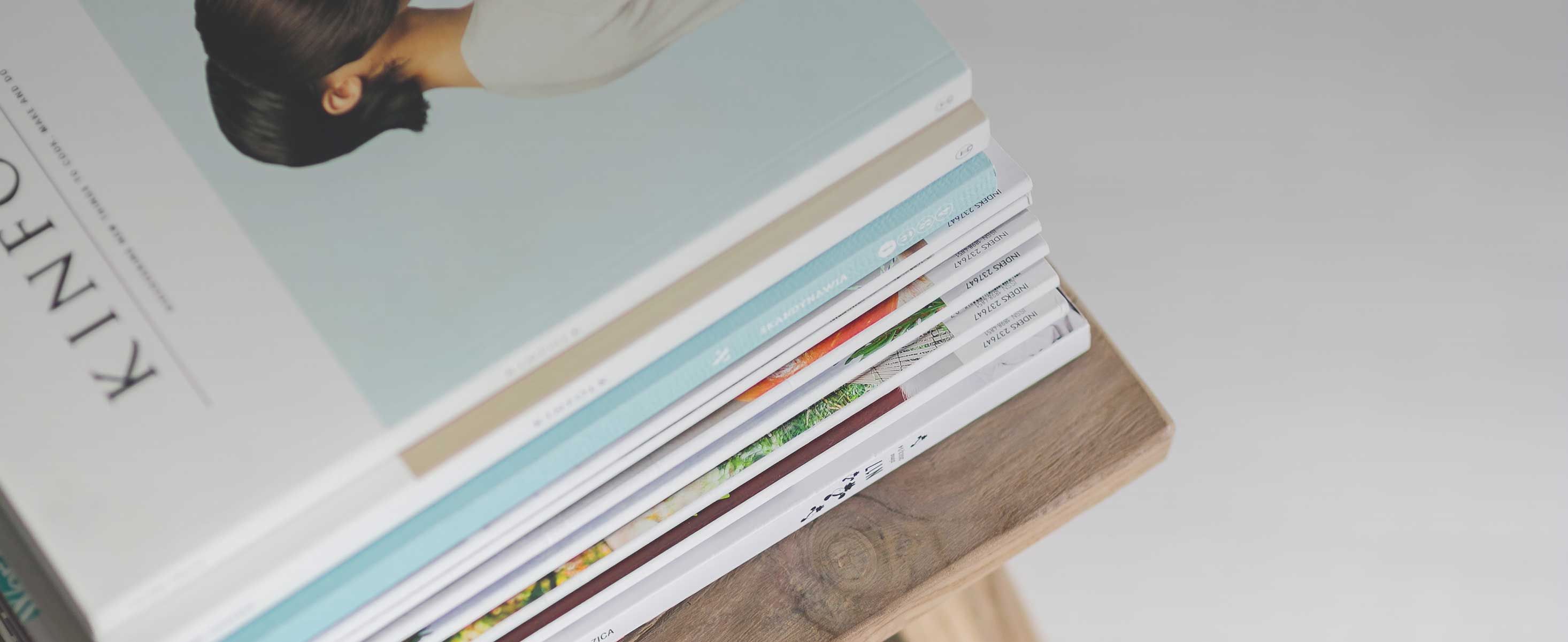
1 minute read
Being SMART in a tight labour market
With no end in sight to increasing labour costs and constraints, manufacturers need to find ways of increasing output and reducing costs. Those that do will be in much stronger position to ride out any potential market softening and be best placed to take advantage of the next significant upswing.
Nest-based manufacturing really took off in New Zealand about 10 years ago, improving productivity by up to 300% over the traditional method of cutting and drilling cabinet components. Software has also seen huge improvements during this time, with kitchen and cabinet designs now converted into CNC manufacturing files in just minutes. Bespoke, batch size 1 manufacturing can be just as efficient as mass production. So what is the next evolution on the pathway towards increased efficiency and productivity?
Most industry experts agree the next big area for evolution in cabinet making is material handling. It’s an obvious area where improvements can be made to drive down costs.
One of the simplest and most obvious areas to realise this is with automatic loading and unloading of the CNC. It doesn’t require a degree in robotics and hundreds of thousands of dollars to put into practice. Automatic material loading and unloading tables are relatively inexpensive and require no programming. These days many CNC manufacturers design their CNCs so that adding loading and unloading tables is virtually plug and play: the machines are prepared with the hardware and electrical connections from the factory. Automated handling can be installed at the same time as the CNC or some years later, as and when required.
Automatic labelling of parts improves productivity even further. The sheet is labelled while waiting on the scissor lift table prior to loading on the CNC. Parts are processed unloaded onto the conveyor table labelled and ready for edgebanding. Labels will typically show which edges need banding with part and job number identification, and the part dimensions. All very useful information to accelerate downstream production.
The addition of automated units for material handling will improve productivity by approximately 40% - 50%. It will also eliminate those times when two people are required to manually load panels on the CNC, while reducing the chance of materials and parts being scratched or damaged. If you’re investing in a new CNC, it really does make sense to add these units from the beginning or to at least invest in a CNC that has the capability to have them added later.
For further details, contact Jacks: 0800 522 577 or sales@jacks.co.nz