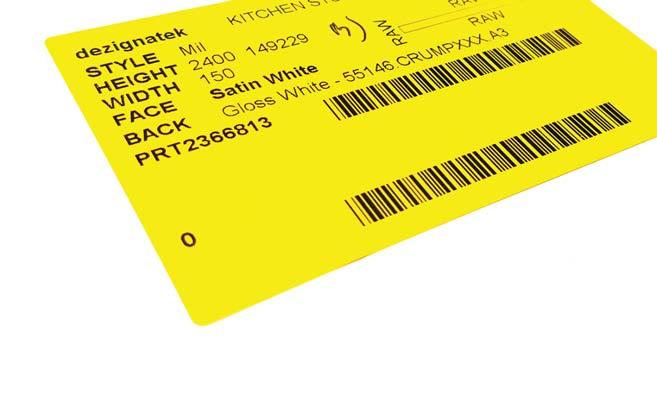
1 minute read
Robotics & Automation
the key to high quality and high volume producton at Dezignatek
Over the last five years, Dezignatek has gone through transformative change as it took on a large volume of thermoform door production from the Arborline business it acquired, in tandem with a huge upswing in demand for both custom thermoformed doors and its laser-edged melamine, HPL and acrylic doors.
Orders made online are transferred directly to optimization and then to one of five CNC machines for door profiles to be cut. With each order having anywhere from one to 30 pieces that go through a range of production processes, a bespoke tracking system is essential to ensure all orders are made and despatched correctly.
Dezignatek Business Manager
Mike Meekings says the impressive job tracking system was designed in-house and has real benefits for customers and staff alike.
“When an order is placed and optimised for production, every single item needing to be made is visible with a graphic display showing how it tracks through the plant from the CNC machine, through the sanding line, robotic spray booth and thermoform press, or to the custom edging production area. All panels are then tracked through packing and despatch – the pick-up by the courier company then triggering a despatch advice to customers.” from programming the CNCs to optimally cut every project, to ensuring doors are sanded, glued, pressed, trimmed, packed and despatched without delay.
He says the 13 scanning stations help avoid the issue of lost panels and there is visibility over exactly where in the production system all panels are.
“Dezignatek account managers also have visibility over the system and are able to help clients understand where their job is, and likely timing for delivery,” he says.
A large, German-sourced RobaTech fully automated sanding line was commissioned two years ago, resulting in a more consistent finish for thermoform panels and a much faster through-put for the sanding area.

Mike says the efficiencies gained by automating so much of the production provide benefits for all clients, but also for production, sales and customer service staff
Robotic sanding
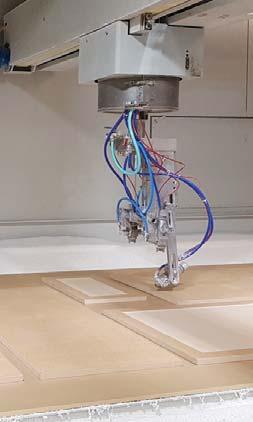
And Gluing Ensure Optimum Quality
In the early days of Dezignatek, all panels were hand sanded and then also had their pre-press adhesive applied manually in a spray booth. Those times are long gone with hand sanding only limited to very complex or deep profiles.
The fully automated robotic spray booth also ensures thermoform doors have a consistently high standard of finishing. Delamination issues are avoided by repeated testing of panels in a specialist oven throughout the production day to check appropriate glue strength.
While automation may seem to have taken over, there are more than 40 staff on the production floor involved in everything
“It’s a win-win and the investment has been totally worthwhile.”
If
DRY Dust Filtration
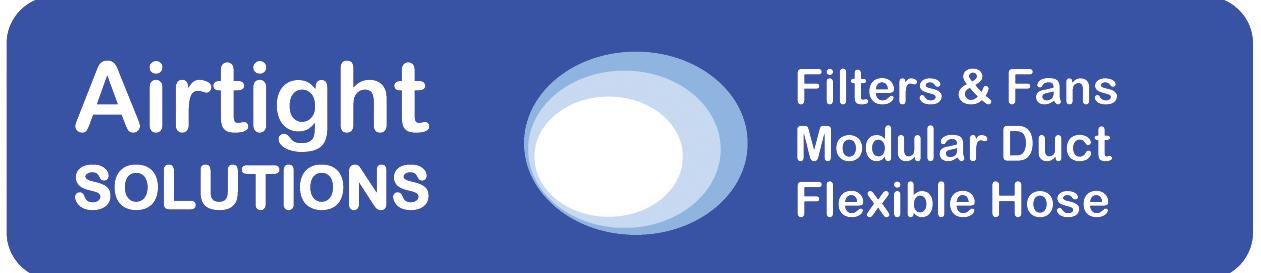
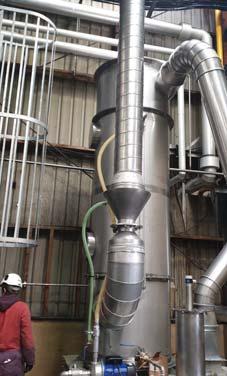
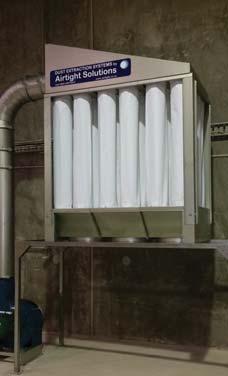
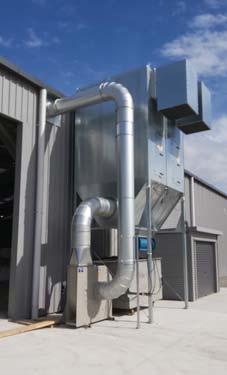
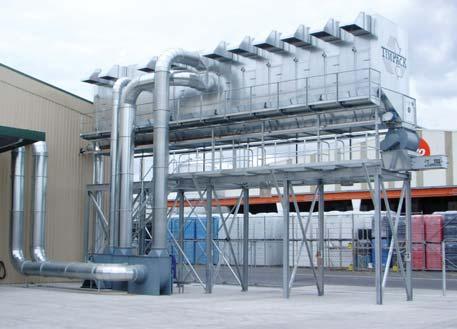
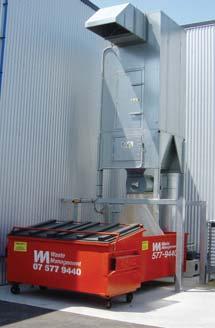
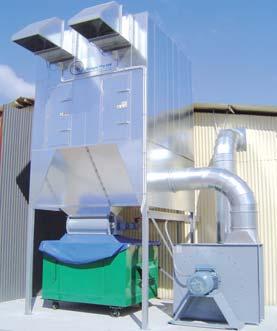
WET Dust Filtration
If