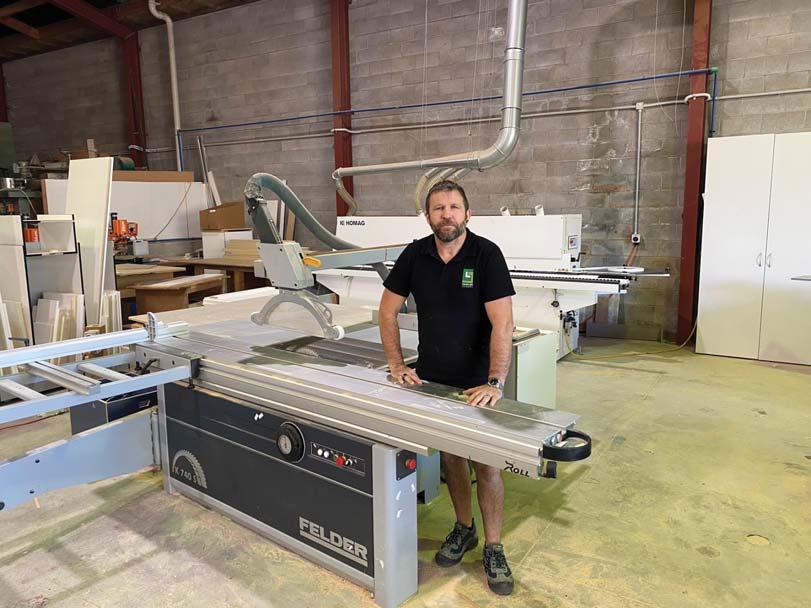
3 minute read
Doing homework saves time
Paul Crawford is one of those guys that makes you wonder how someone can possibly get so much done in a day. When Paul talks about the work that’s gone into his showroom, offices and workshop along with the first few years building up a business that was on its knees, you know there have been some long, hard weeks and months.
After finishing his Joinery apprenticeship at Pat Gavins Kitchens in Whangarei, Paul worked down the road at Sherwood Kitchens for the best part of 16 years. In that time there wasn’t much in the business that didn’t have his fingerprint on it. Three years ago Paul decided it was time to skipper his own destiny. With such a solid foundation in the industry, there was no holding him back. He and wife Anna purchased Mason Joinery, which was ripe for an overhaul. Paul and Anna were the perfect team for the challenge. And so Crawford Joinery was born.
Paul worked on his own for the first six months with Anna helping-out a couple of days a week. Fast forward to now, Anna is full time, they have three full time staff in the workshop and a couple of contractors they call on when required.
Purely by word-of-mouth
Crawford Joinery has gone from strength to strength. Paul attributes the success to a personal touch and being a local business. Paul is onsite for most installations. “You can do everything right in the workshop but still mess things up during the install. It’s all about client satisfaction”. While Crawford Joinery has a focus on kitchens and internal cabinetry, with Paul and his team’s skill set, they also diversify into solid timber jobs, some pre-hung doors and insurance work.
Paul realised early on that the edgebander needed a significant upgrade. “I looked around and spoke to people in the industry before deciding to go with a Homag from Jacks. Follow-up and service was very important for me when making my decision. Apart from a couple of minor issues, the Homag has proven a reliable edgebander producing the consistent finish we need.”
Paul invested in a Micronair extraction system at the same time. “There’s no point in having a high quality edgebander without good extraction,” Paul says.
The Micronair was bigger and more powerful than Paul needed at the time. He had plans. Twelve months later Paul took delivery of a Profit H08 nesting CNC and K740S Panel saw - both manufactured by the Felder Group out of Austria, supplied and supported locally by Jacks. “I did my homework again. Particularly on the CNC. I had experience operating a CNC that was only driven on one side of the gantry. It had its issues so I wanted a CNC driven on both sides. I also really like the automatic tool length measuring system. Compared with the previous CNC, measuring tools is a piece of cake.” Paul continues: “there’s no way we could possibly put out the volume of work we do without the CNC”. www.jacks.co.nz
Even though he’s very busy, Paul takes the time to research, ask around, and therefore he’s getting the benefit in production from having done his homework. Perhaps that’s his secret to getting so much done in so little time?
Diamaster WhisperCut & WhisperCut PLUS
The light and low noise jointing cutterhead with the PLUS of efficiency
Noisy and heavy tools result in stress for man and machines. The light and low noise Diamaster WhisperCut jointing cutterhead is specially designed to reduce noise and increase efficiency.
Sustainability
Light, low noise and reusable
Considerable noise reduction of up to 5 dB(A) through optimised tool body shape and weight halving
Reduced load of spindle and machine through light tool body Reusable tool body saves resources
Quality
Perfect results
Clean workpiece finish through trouble-free chip ejection and excellent chip collection with DFC-technology
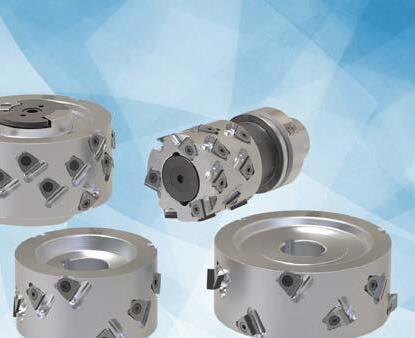
Perfect quality even with demanding panel materials
Leitz for the Best in Edgebander Tooling & Servicing
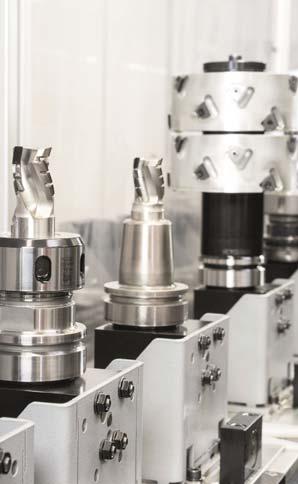
Leitz Tooling have been producing tools for the woodworking industry for over 145 years. A family business in it's fifth generation, reliability and longevity are the keys to Leitz' success. Leitz New Zealand specialises in the servicing of edgebanding machinery, using the latest diamond sharpening machines and technology in their Penrose Service Centre in Auckland.
“Even the best quality tool can only provide optimum performance if it is regularly maintained by experts” comments Wolf Hoheisen, Leitz New Zealand Manager. “In our Auckland Service Centre we use the same machinery and programmes as Leitz in Germany. This gives our tools consistent top quality, including the ability to sharpen tooling from all manufacturers.”
Leitz offers minimum machine downtime with quick servicing turnaround and reliable tool pickup and delivery across Auckland for edgebanding tools. Leitz Tooling has 140 service centres worldwide and great importance is placed on quality, with certification to DIN ISO 9000 standards providing a uniform standard across all servicing.
Efficiency
Cost reduction and increased productivity
Reduced costs per running metre through sharpenable cutting edges and reusable body Shorter set up times through constant diameter Optimum knife usage by exchanging unused cutting edges within the tool
Leitz Service ENDORSEMENT FOR YOUR SUCCESS
Latest diamond sharpening machines and technologies in our Penrose Service Centre Reliable tool pick up and delivery across Auckland Sharpening of tooling from all manufacturers