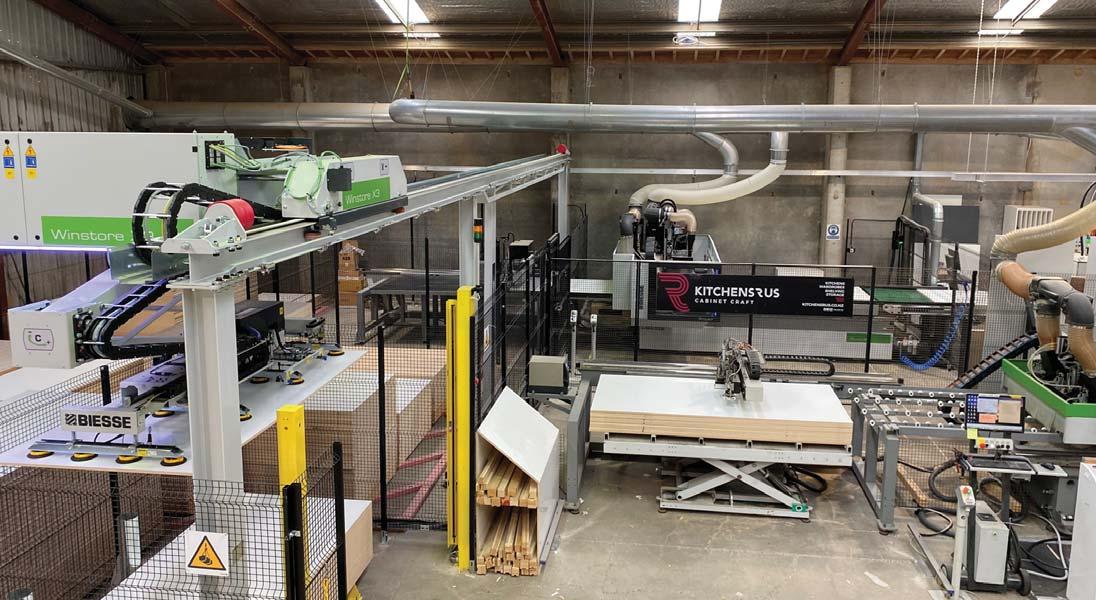
3 minute read
Winstore X3 optimising the storing and retrieval of board
An increasing workload for Tauranga based Kitchens R Us who manufacturer kitchens, wardrobes, storage cabinetry and commercial shop fit-outs, meant the company needed to introduce a second manufacturing line into their busy business. A lack of space to do this saw them look seriously at how they were running board through their factory. The end result was the first Biesse Winstore X3 in New Zealand, a board storage and retrieval system which resolved the factories space issues while taking the heavy lifting out of board handling.
“We had been very busy for some time,” says Kitchens R Us owner Russell Reardon. “Our current CNC was maxed out but we didn’t really have the factory space to easily add a second one, so we needed to work out how we could condense the use of the factory space we had, to accommodate a second CNC.
“I had been looking at what robotics can do in joinery applications and had seen a Biesse Winstore in operation in the US on a trip there three years ago. I had been impressed at the way the storage system condensed board storage while taking out the people. We were already running a Biesse CNC and looking to purchase a Biesse Rover S for our second line so the Winstore X3 looked a good fit to feed them both.
“The results have been impressive it basically works all day and all night storing and sorting board into job-lots. When we bring in new board it is left in the loading bay and the Winstore starts loading it into storage. It can prioritise its work so that if a machine needs loading it will leave storing board and service the machine before going back to its previous task.
“It knows exactly where it has stored each board and when provided with a jobs details it goes and gets the required sheets. We carry around 15,000 sheets of board in a variety of colours. We have about 13 stacks and each stack can have different colours. Winstore know where it has stacked each board, so if a required board is in stack 6 and 10 boards down it will go and get it by reshuffling the stack.
“The secret is the Winstore X3 and the CNC’s talk to each other. We have always used Cabinet Vision which is very compatible with the onboard Biesse software and we have invested in Stack Easy which is an additional package developed in Australia specifically for the Winstore, which helps configure the best option at any one time. Together they work brilliantly to retrieve board for each job ready for both CNC’s in order of our job runs.
“This is the first Winstore X3 to be installed in New Zealand so we were a little nervous about the install and commission but it basically went seamlessly. Everybody stuck to prices and quoted time lines, Biesse provided details of our requirements and drew up plans and guidelines to allow us to talk to specialists in areas such as dust extraction, electrical wiring and air compression where we needed to increase our capacity ready for the new set up.
“Biesse progressed the install very well. First we shifted the existing line during our downtime between Christmas and New Year so that starting the year we were able to operate the existing line from a different area of the factory. We sectioned off the area for the new line and Biesse installed our new Rover S and the Winstore X3 over the next month or so without any disruption to our ongoing operation
“Biesse did a great job, I am very happy that we decided to go with them on this project. It was very important that they had people in NZ to install the project especially during covid as we didn’t want to be relying on technicians from overseas. Dylan Staples from Biesse assured me it could all be done locally, I had dealt with him in the past and trusted in his ability to do a good job.
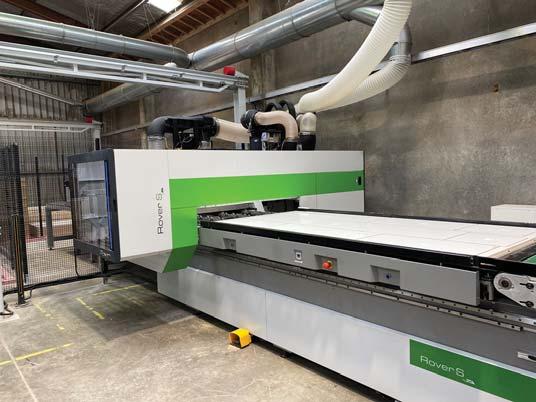
“A couple of months on from the install the factory is flowing smoothly and we are experiencing lots of productivity gains. We were previously using a forklift to feed our CNC, one job at a time. Now the Winstore X3 feeds both lines automatically, we don’t require the same area for storage and we don’t need to involve a forklift driver as in the past.
“All of this with no mistakes in board selection and a system which is quieter, faster and safer and a lot more capable than that which we were using.
We’ll be giving away a free 12 months subscription courtesy of 3D Kitchen™ with every issue of JOINERS Magazine!