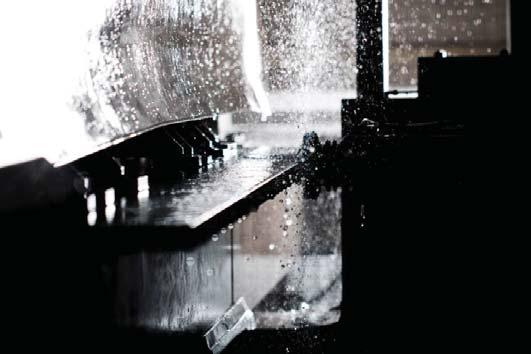
8 minute read
NKBA welcomes NZESAG Accreditation Scheme
The National Kitchen and Bathroom Association of New Zealand (NKBA) is advocating for accreditation, over the next six to twelve months, of all NKBA Associate members who are stone/quartz fabricators under the NZESAG RCS Accreditation Programme.
The move by NKBA is a signal that the kitchen and bathroom design industry is committed to reducing the health and safety risks relating to respirable crystalline silica (RCS) exposure and resultant silicosis or accelerated silicosis diseases, and that fabricators who do not take substantial steps to prioritise the health of their employees and contractors will not be endorsed by the NKBA.
The action by NKBA has been welcomed by the Managing Director of Artisan Stone, Steve Kirk. “Kitchen and bathroom designers work with, and specify, a variety of products and materials. By advocating for the accreditation of NKBA fabricators, NKBA is simplifying the decision for designers. Introducing accreditation, gives designers the confidence to specify stone products that are cut in safe working conditions,” says Kirk.
Silicosis, and the more recently identified accelerated silicosis, are lung diseases that can be caused by breathing in fine crystalline silica dust, a mineral found in sand, rock and mineral ores such as quartz. A condition usually caused through inhalation over a long period of time, silicosis mostly affects those that work in occupations such as mining, glass manufacturing and stone masonry. Engineered stone, which has over twice the RCS content as natural stone, has been shown to hasten the onset and severity of silicosis and the new disease, accelerated silicosis, is directly linked to engineered stone fabrication.
Kirk says statistics from Worksafe indicate approximately 450 New Zealanders currently work cutting engineered stone nationally, but only 85 current or former workers in the industry have initiated the necessary CT Scan and Xray health review through their GPs and ACC. “These figures are concerning. As well as ensuring current workplaces are safe, it’s important for individuals to get this check-up as soon as possible so they understand if they carry any historic damage and can make informed decisions about their future,” says Kirk.
The New Zealand Engineered Stone Advisory Group (NZESAG) RCS Accreditation Programme was launched last month. Established by New Zealand’s leading importers/ suppliers of engineered stone/ quartz surfaces, the NZESAG’s objective is to respond to the occupational health risks to workers of accelerated silicosis when fabricating, manufacturing or installing engineered stone products.
The NZESAG has partnered with Impac Services to establish and implement the RCS Accreditation Programme. Tom Reeves, Director of Impac says there are three levels to the accreditation, and though full accreditation is the absolute goal, at this stage it is just as important to enlist fabricators to the programme. “Participation is key. We want to get as many fabricators as we can signed up to the programme. We know that many fabricators have already invested a lot of time and effort into improving the health and safety of their workplace and have taken the necessary steps to reduce the risks associated with RCS exposure such as accelerated silicosis. We believe the accreditation programme will help to raise awareness of accelerated silicosis to fabricators and improve the way they manage these risks. We are also trying to influence the end-consumer to work with fabricators who are accredited,” says Reeves.
There are three levels to the accreditation. Level 1 is Accredited Participants who have engaged with the programme but do not meet significant elements of the Good Practice Guide. Level 2 are at an Interim Accreditation level, where the fabricator has engaged in the accreditation programme and has met significant elements of the Good Practice Guide. Level 3 is an Accredited Fabricator; this means that they meet all core requirements as set out in the Good Practice Guide and the accreditation audit.
To participate in the programme, fabricators need to register simple information via the registration link at https://impac.co.nz/rcsaccreditation/home/. Once this is done a member of the Accreditation Team will be in touch, within a couple of days, and a time will be made to undertake the accreditation audit. Once the audit is completed, it is aimed a result will be provided within two weeks. In addition, fabricator owners, managers and workers will have access to an online RCS training, and a suite of simple health and safety tools and templates.
NKBA’s Executive Officer, Suzie Rees, says that the accreditation programme not only gives fabricators a framework to abide by, it also provides NKBA designers, manufacturers and the consumer with a clear understanding of which fabricators are taking the necessary steps to keep their workers safe.
“NKBA are in full support of the NZESAG RCS Accreditation programme and will be advocating for all our designers and manufacturers to only specify the use of stone/quartz that is manufactured by fabricators who belong to the programme. Going forward we will only accept membership to NKBA of accredited fabricators, we are drawing a line in the sand about what we perceive as good and bad practice. We understand there is a lot of work to be done in this space and that time is required to educate the industry and get the accreditation up and running smoothly. However, NKBA has full confidence in the NZESAG group and Impac to do what is required to ensure a safer and brighter future for the stone fabricator industry,” says Rees.
Steve Kirk says it’s important to understand that no one in New Zealand is recommending the banning of engineered stone fabrication, which has been floated in Australia.
“The context in which this was raised in Australia indicates this is a negotiation tactic to encourage a reluctant industry and Government to effectively regulate and licence engineered stone manufacture, which I support. However, I agree with Dr Alexandra Muthu, who is an expert on the health effects of silicosis and is working with the industry to research and provide a pathway forward. She says that a ban is not necessarily the answer, because engineered stone can be safely cut with the right equipment, and silica is far from the only dust causing disease. In my mind, I think we need to ensure Worksafe and ACC are reaching fabricators where uncontrolled dry cutting is still occurring. That will be the biggest challenge,” says Kirk.
For more information on how to participate in the accreditation visit: What is the RCS Accreditation Programme? at impac.co.nz
The NZESAG RCS Accreditation Programme for fabricators and installers of engineered stone is now up and running.
NZESAG’s Respirable NZESAG’s Crystalline Silica Silica (RCS) Accreditation Accreditation Programme
The New Zealand Engineered Stone Advisory Group (NZESAG) was established in July 2019 by New Zealand’s leading importers/ suppliers of engineered stone/ quartz surfaces. The Group’s objective has been to respond to the occupational health risk to workers of accelerated silicosis when fabricating, manufacturing, or installing engineered stone products.

Over the last 18 months, the NZESAG has partnered with Impac Services Ltd (IMPAC) to establish and implement an RCS Accreditation Programme to reduce the risk of silicosis across the engineered stone fabrication sector in New Zealand.The RCS Accreditation Programme has been supported by NZESAG members, Fabricators, ACC, and WorkSafe.
The RCS Accreditation Programme is centred around a Good Practice Guide and the auditing of Fabricators against its core requirements. This includes exposure monitoring of workers. The intent of the first audit is to provide Fabricators with a base level understanding of how they are doing with a follow up audit carried out in 12 months to confirm that required improvements have been made. One of three levels of accreditation are awarded after the first audit (see box).
In addition to the Good Practice Guide and accreditation audit, programme participants also get access to online “Managing RCS Exposure Risk” training for their workers and supervisors, as well as simple health and safety templates and tools to help implement elements of the programme.
The RCS Accreditation Programme went live from midApril 2021 with the first audits and accreditations now completed. It is anticipated that all Engineered Stone Fabricators will undertake an initial accreditation audit within 12 months.
A comprehensive communications plan is being developed with a focus on both promoting the programme to Fabricators directly but also to the end consumer to encourage them to source engineered stone product from accredited Fabricators only. This is being supported by ACC and is anticipated to include print, social and visual media.
Levels of Accreditation
Level 1Accredited ParticipantHas engaged in the Accreditation Programme and has met significant elements of the Good Practice Guide in practice and/or intent. Has committed to implementing recommended improvements which will be checked at next audit.
Level 2Interim Accrteditation Has engaged in the Accreditation Programme and has met significant elements of the Good Practice Guide in practice and/or intent. Has committed to implementing recommended improvements which will be checked at next audit.
Level 3Accredited Fabricator Meets all core requirements of this Good Practice Guide as set out in the Accreditation Audit.
Before a Fabricator can be admitted to the programme, they must confirm it has met the following two critical elements of the Good Practice Guide:
1. The primary cutter is water supressed.
2. Fit testing of Respirable Protective Equipment (RPE) (that requires a seal to be maintained between the RPE and the face) for all workers has been carried out by a competent person in the last 12 months.
If you would like more information about the RCS Accreditation Programme visit https://impac.co.nz/ rcs-accreditation/home/; if you have not registered for the programme you can also do that via the link.
Andy Halewood with first year apprentice Mingting Zhu.
Your industry needs you
In my relatively new role as Joinery apprentice coordinator there are some observations I feel are worth discussing. At the Master Joiners conference a question was asked. Where do employers see their next staff coming from? Just a few things I have observed that are maybe worth further discussion.
Starting with educating the public with what a joiner actually does. We are well familiar with the house of the year, Master Builders celebrate annually. When I see a new build start to take shape, it’s a shell the builder has constructed. There are a number of sub trades that complete the whole picture. Without the roofer, the framing is only structural and won’t keep the rain out. The kitchen, doors, windows and stairs are clearly (to us) the work of the joiner. The painter makes everything look amazing.
In my view, the public perception is the builder makes everything. School kids have no idea what joiners do. Their career guidance counselors are not familiar with the joinery industry. Their parents still think joiners and furniture makers are “carpenters”.
Are you willing to get in touch with your local high school?
I have arranged with Stephen Fairbase at Well Hung Joinery to bring 6 Wellington high school kids to their workshop on Nairanga Gorge. Well Hung have 2 UCOL apprentices and may have a few others from other providers. They carry out a wide range of joinery applications and are conscious of future growth especially in training new staff. This is a first for me and time will only tell how successful or what potential it has. Many schools actually do have woodwork classes and these students are our potential future joiners, carpenters and furniture makers.
Education specific !!
Kitchen cabinetry is a lot of white board, CNC cutting and edge banding. A lot of screwing boxes together, attaching hardware and adjusting doors. All sorts of fittings, catches, bench joiners. Fast moving innovation happens in the joinery trade! Then there is all the problem solving that comes with installing the kitchens. Keeping the client happy etc.
Institutions (where I have been for 20 years) don’t always keep up with industry. Schools are even worse. The old wood work shop is what we all dream of hiding away in our retirement or as a second hobby. Surely if we want to educate our future joiners about our industry, we need to begin feeding them some of what we actually do. I am not suggesting schools race out and buy CNC machines, but they could get familiar with nest programs. They could team up with “YOU” and run their programme on your CNC. They could take back to school their components and assemble a kitchen for who knows who. It could be you. It could be a community project.
Andy Halewood Senior Lecturer & Joinery Apprentice Coordinator, UCOL a.halewood@ucol.ac.nz
