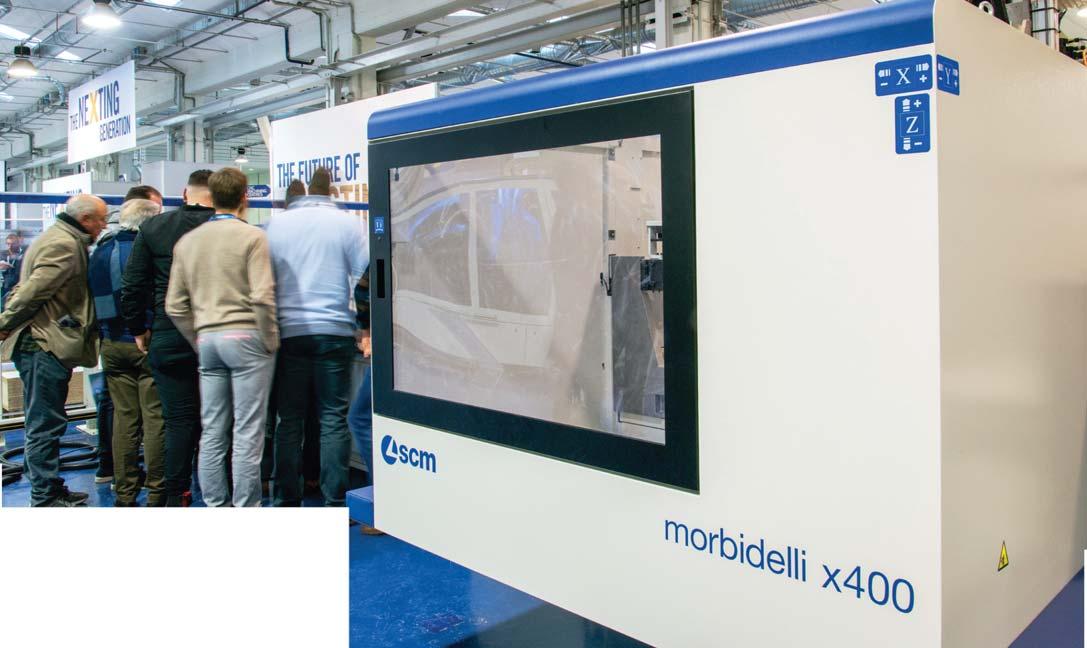
2 minute read
the NeXting Generation is here
For a world that is increasingly moving towards flexible and batch 1 production, the nesting process is undoubtedly a point of reference for furniture manufacturers. The possibility of producing a larger number of pieces and dealing with shapes or very unusual forms, means manufacturers can achieve flexibility and carry out more operations on a single, numerical control machine.
All technology has its strong points as well as its weaker ones. As far as traditional nesting machines are concerned, three key critical aspects can be identified: handling of the spoil board panel, productivity (when compared with sizing machines) and the vacuum seal on small sized pieces.
The SCM team has devised, developed and tested innovative solutions as a remedy to their clients' problems and to give them a chance to increase their own productivity and flexibility at the same time. The result of the work carried out over the years is reflected in the new Morbidelli x200/x400 machining centres that were exclusively presented at SCM's Open House 2019.
“The most acclaimed innovations on the m100 and m200 machining centres have been transferred to these new solutions for Morbidelli x200 and x400 nesting" points out Bruno Di Napoli, BU Manager for SCM Machining Centres.
"The new range is a genuine concentration of innovation and the ideal solution for most companies and artisan workers producing furniture".
The spoil board panel is essential for making the most of the nesting process as it would be impossible to go and work directly on the machine's surface without damaging it. This involves a series of problems and complexities that need to be handled by the operators. Starting with the flattening, moving on to the change of spoil boards that have come to the end of their service life and right up to their removal when there is a need to work with supports that must be fixed to the machine surface.
The new Morbidelli x200/x400 machines offer new innovations that will mean the spoil board panel no longer needs to be removed to carry out all the operations that were required in the past: making horizontal borings directly on the spoil board or positioning special suction cups above them now be possible.
Other important changes introduced focus around the ability of the machine to secure even the smallest pieces during processing. Like so many other machines for nesting, the new Morbidelli x200 and x400 can be fitted with a work surface split into areas, with the possibility of closing off the vacuum areas not in use; that said, these are the only ones fitted with the new X-Vacuum system, for a genuinely dynamic activation of the vacuum. An innovative and automatic function carries the vacuum to exactly where it is needed.
Lastly, a new labelling system and cutting speed up to 50 m/min mean SCM clients can achieve a completely new production for a nesting machine. And that’s not all: just like the cars that so many of us drive each day, the new morbidelli series can be used in smooth, neutral or dynamic mode (the equivalent of comfort, neutral and sport) to customise program use “at the wheel”.
Years of design and investments have brought about the new Morbidelli range. Outstanding performance, maximum configuration and a competitive price mean SCM have a made to measure machine for every client.
The NeXting Generation has officially begun.