
7 minute read
Ross Campbell
The notion of selecting Kiwis who have done well in Australia is not a new one. There have been such stories written by many, about many, successful New Zealanders across the ditch in all sorts of industries and activities. About a year ago at the last Master Joiners Conference I broached the subject with one of my two selections, Ross Campbell, if he would do me the honour. He did and the following is a commentary from him based on questions I put to him. Covid 19 knocked my idea of going to Sydney to do it in person. For the record, Ross was born in Kawerau. His replies are incisive, as you would expect from the Australian Managing Director of ten years standing, of one of the biggest woodworking machinery manufacturers in the world, Homag AG. Despite this there is a distinctive Kiwi feel to his comments which I have left untouched. Many readers will either know or know of Ross. I’m very pleased he agreed to participate in this, our 100th issue. Bob Nordgren.
I first met you back in 1996 when you were a Divisional Manager and director for W & R Jack Ltd based in Auckland. What got you into the woodworking machinery scene?
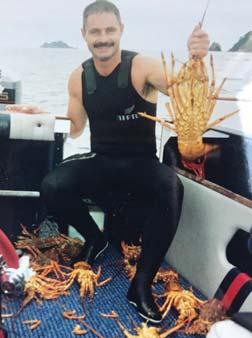
Good luck? Cannot have been good management! Or maybe being born in Kawerau to the aroma of the pulp and timber mills had something to do with it. A little bit of wood something was in my veins. Reality was purely chance along with some people who put their faith in me and gave me a go. It was late 1974, I was seventeen, lacking direction and casting around looking for a job. I responded to an advertisement from Jacks for a job as a woodworking machinery salesman (I knew what a skillsaw, a hammer drill and a sawbench was OK!) and so I was offered a job in the warehouse. Well that’s one way to learn the business. Fortunately I was surrounded by good folks and with plenty of encouragement, some great guidance and mentoring I was soon offered the chance to ‘go on the road’. On a part-time basis of course. That was a life-changer and a lifeline really. Turned out I had some ability other than packing parcels and paperwork and with huge support have never looked back. They were great days, still a way off 20 years old, company car charging around the countryside selling buzzers and thicknessers and spindle moulders and all kinds of machines many in the industry today would not have even heard of. In those days, many of the customers were happy to take you under their wing, share their knowhow. Thank goodness for that.
The 1990’s was a period of great change in the woodworking machinery industry, especially with the emergence of CNC technology. What bought that about and what challenges did it present for the woodworking industry?
Think I am right in saying the engineering machine tool industry had some sort of numeric control on some of their machines since the early 50’s. Analog and digital control followed some time later. Woodworking machinery was the poor cousin although we worked with tool speeds which even at that time would make the hairs on the back of an engineer’s neck prickle more than a little. But it was very artisan, the quality of the product was mostly determined by the skill of the individual wielding the tool or operating the machine. And there was some clever buggers around that is for sure. The first woodworking process with a computer was of course the CNC router. Voodoo and witchcraft and a healthy bank balance were needed to contemplate one of those beasts. Quite quickly the nc router morphed into the point to point borer which become todays modern day ‘cnc’. Parallel the panelisation of wood fibre expanded, and machine components that could be controlled from computer via a PLC grew in quantum leaps and the rebirthing of today’s woodworking technology was underway. At that time and still today there is no other technology that can determine the destiny of a woodworking business in such a significant way. Today there is no destiny without digtial.
Your professional career took a turn when you moved to Australia in the early 2000’s to end up working for the German company HOMAG AG, one of the largest and most influential woodworking machinery manufacturers in the world. That business started with you in the role of Sales Director and you have been their Managing Director in Australia for some ten years now. What led you to join them?
First a little more background to put it into context. From 1974 to 2002 I had a wonderful career with Jacks. Robin Jack opened doors for me and there was no looking back. During the 80’s and 90’s I was given the opportunity to focus on timber processing and sawmilling and that was a very successful time for our industry, for Jacks and for myself. Eventually Jacks invited me to join their Board and to become a small shareholder. A long way from the packing bench when I started in 1974! I loved it.
As Jacks grew in the NZ market they became the HOMAG distributor in NZ. Within a very short time HOMAG invited Jacks to start a company representing HOMAG in Victoria, and later Western Australia. It wasn’t long before HOMAG like many multi-nationals was globalising, partnering and taking ownership of its front line distribution around the world. Australia eventually was in focus and so a joint venture was born. The Jacks business in Australia morphed into HOMAG Australia which took over the distribution of HOMAG nationally in Australia.
Like to know more about HOMAG software? Scan the QR code to connect ...
Why did I join the move to Australia? Well it was the opportunity for a completely new adventure. For Jacks I was already spending considerable time in Aussie, the market was new for me, it was vibrant, it was ‘here-andnow’ and I was ready for a change.
The world woodworking machinery market has been coloured by the influence of China and its ability to produce cheap machinery. In your experience over the last twenty years has the ‘West’ reacted to this successfully?
Your putting me on the spot. HOMAG also has a large manufacturing plant in China (as we do in Germany, Poland, India, USA, Brazil) and we have delivered numerous machines from our Shanghai plant into Australia. And they are not cheap. My experience is you can buy everything you want in China, and you can choose at which level on the price spectrum you will buy. And you get what you pay for. There are other countries also building ‘cheap’ woodworking machinery, China is not alone.
Yes, the Chinese machine building industry has grown significantly, not just in scale but also complexity and maturity. Chinese manufacturers are like others around the world, they want reliability, they want the latest technology, they want support. They can also choose to buy at the lower end of the price spectrum and forego some of these things, or they can choose to buy at the higher end of the price spectrum and their expectations are no different to an Australasian manufacturer. As they say, you get what you pay for. I think John Rushkin had it right way back in 1768: It is unwise to pay too much, but worse to pay to little. Pay too much and you lose a little money, that is all. Pay too little and sometimes you lose everything because the thing you bought is incapable of doing the job. The common law of business prohibits paying a little and getting a lot. It cannot be done. If you deal with the lowest bidder it is well to add something for the risk. And if you do that, you will have enough for something better!
Technology and the workplace: a match made in heaven?
Today there is no place, workplace or otherwise without technology. Every day we are increasingly connected and if you don’t embrace it you will be lost. From the connected television and refrigerator at home to the connected processing machines in the workplace. Our expectations are now, today, we want the answer ‘now’. That’s the diet that the Internet has been feeding us and we are intolerant of anything less. Long gone are the days when I first started at Jacks and you requested help or information from a European machine builder by writing a letter, sending it by airmail, and getting an answer 4, more likely 6-months later. Think about that! So an emphatic yes to that, a match made in heaven because the alternative is not survivable.
Where to from here?
More of the same yet more and more. Our lives, our machines, our ability to seek and source information, cooperation, support’ is now well on the digital path and I see no going back. Technology will foster mutual co-operations, sharing, pooling of resources, the ability to ‘crowd resource’ skills and competencies the likes of which we have not seen before.
If you can take one thing away from Covid 19 it is that we have learned to communicate effectively without the absolute need to be face-to-face. Yes its different, but it can work and can be more efficient. That’s the why, its more efficient, as to the where-to? I do not have a single answer to that but as Benjamin Franklin said if you do tomorrow what you did today you will get tomorrow what you did today. With that in mind all I can say is don’t look back!
What’s it mean to you being a Kiwi who has been a major part of and then led a large German company in Australia – in a tough competitive industry - for the best part of two decades?
Who would have thought? Not I. As mentioned earlier there is no way would I be where I am without having had the support of two great mentors. Firstly Robin Jack and latterly a guy from our German head office, Thomas Frey. Both exerted great influence and encouraged me to reach higher. What’s it mean? Well it’s an honour really and only made possible by the mentorship and the ongoing support and guidance of all the other people working at HOMAG Australia and let’s not forget the people in the industry. I reckon the woodworking industry has more than its fair share of good folks working to do the right thing by themselves and those around them. Maybe it’s something to do with working with wood.
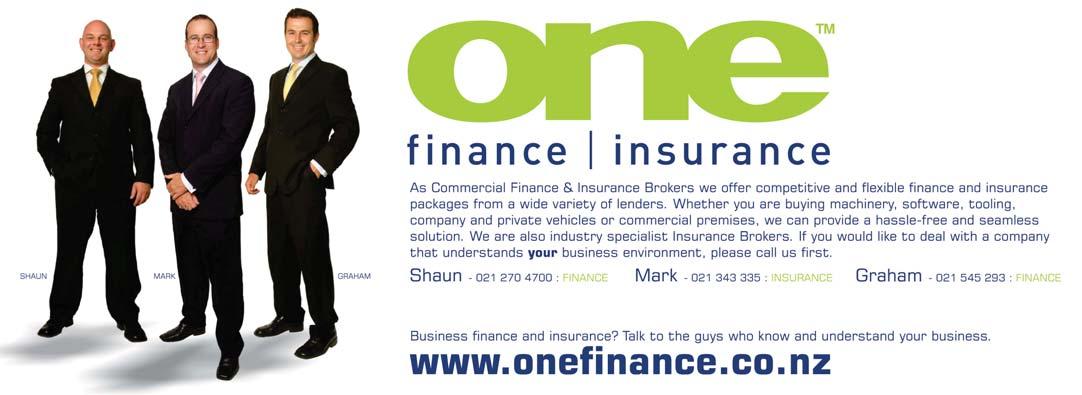
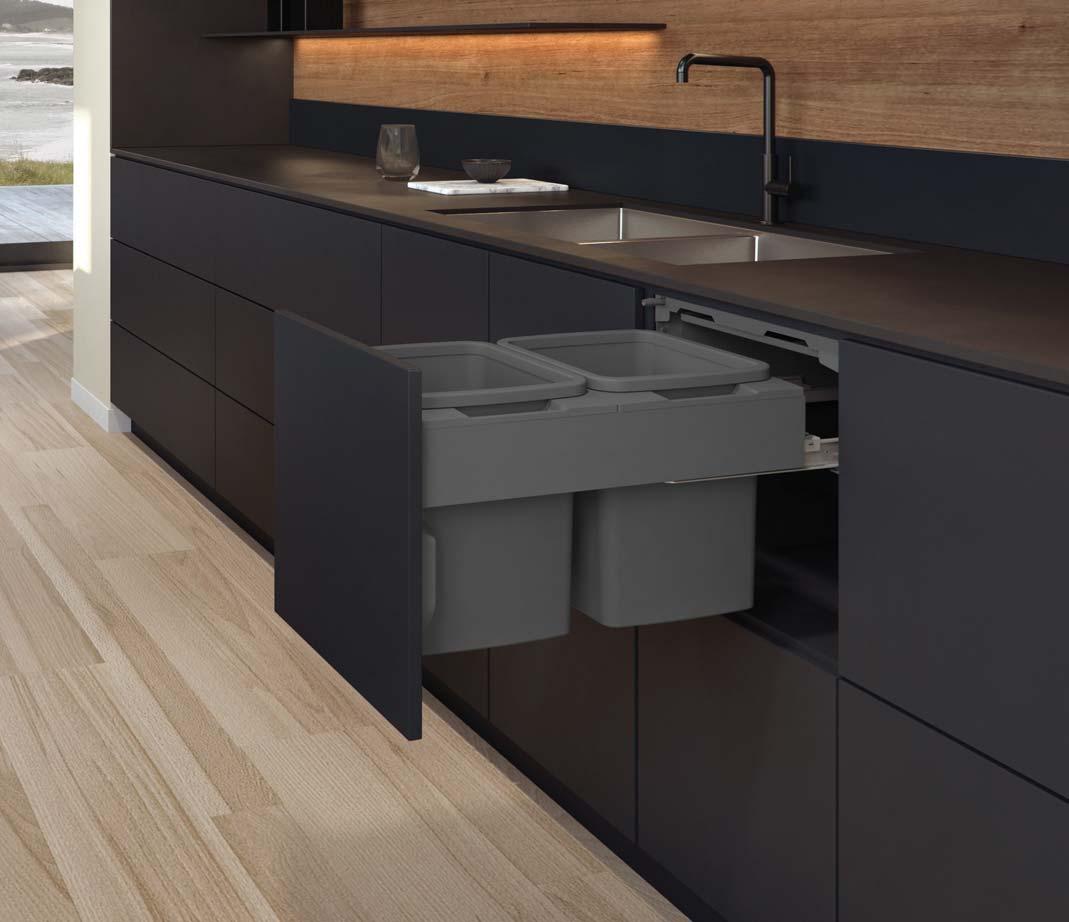

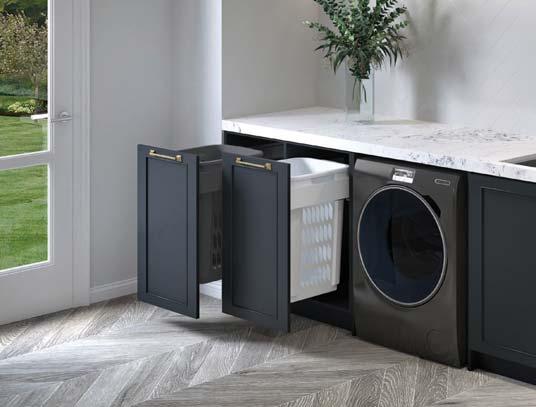