
4 minute read
Dezignatek Dezignatek expanding colours & capabilities
Dezignatek Business Manager
Mike Meekings says the major colour update for Dezignatek marks a significant milestone for the business as it continues to grow and evolve.
Eight of the 16 new colours have been sourced from the Arborline range and their introduction marks the end of the Arborline brand. Hamilton-based Arborline was bought by NZ Panels Group in 2018 and the manufacturing of doors was integrated into the more sophisticated Dezignatek production line at East Tamaki.
The expanded thermoform production facilities now include five CNC machines, two thermoform press beds, a new fully automated sanding line and robotic spray booth. Combined with the introduction of a new door scanner and tracking system, Dezignatek is now the largest and most sophisticated door producer in the country.
“The 16 new colour additions brings the total thermoform range to 48 and allows the range to include more on-trend colours and a lot more matt finishes which are a big favourite of designers right now,” said Mike.
“Our sales team is just itching to get out and show the new colours to clients – it’s a big job to remerchandise all the folders and boards, but if people can’t wait to see them, they can order a keychain direct from the Dezignatek website.”
Edging services also upgraded
In the past 18 months, the edging capability for Dezignatek has also been expanded. In addition to the two laser edge banders, a 45 degree edge bander was bought to satisfy the demand for hidden handles which are increasingly requested. More than 40 colours in the Prime and Bestwood melamine ranges can be finished with a 45 degree bevel edge and 43 colours have the option for laser edging.
Acrylic doors can all be edged with laser and all can be finished with a 45 degree straight edge. The very popular Prime Laminate Soft-Matt Laminates can also laser edged by Dezignatek.
With an improved five-day turnaround time on edged doors, Mike says the team is feeling pretty chuffed about the changes, and the positive feedback being received from clients.
“In combination with our newly upgraded online ordering system for edged acrylic, melamine and laminate doors, we’re very positive about where the business is heading for both our edging and thermoform doors business.”
our Thermoform Range
10 YEAR WARRANTY NEW
We’ve just added 16 great new designs to our thermoform vinyl range, expanding the offer to a total of 48 colours. That’s 16 more creative possibilities for you and your clients. A welcome addition of colour sees some soft greys, blues and greens added to the range, meeting the demand from kitchen designers and their clients for these tones.
Spectra 48 productive manufacturing
Awesome Kitchens was started by Nathen Liu in 2016. Starting with a staff of three, in just four years, Awesome Kitchens has grown to a team of over 20 staff, manufacturing around two kitchens per day. They have a wide scope of supply, including property developers, commercial and residential clients. They aim to provide good quality kitchens at a reasonable price.
When it came time to choosing machinery to start their new business, Nathen knew that to be successful in a competitive industry they would need modern and efficient machinery from the outset. After considering the options, Nathen chose a mix of new and used machines supplied by Jacks. An economical Chinese made CNC, an edgebander and new Felder K500S panel saw formed the backbone of the workshop floor. They also chose the PRO100 Kitchen design-to-machine software package to ensure efficiency from design to manufacturing. Together the software and machinery package had Awesome Kitchens up and running quickly, and it wasn’t long before they had one of the most productive manufacturing processes in their area.
Awesome Kitchens have already begun the process of upgrading to the next level of machinery. Last year Nathen chose to trade-in their existing CNC for an Anderson Spectra 48. At 3000 kilograms and with a reputation for being extremely reliable, Nathen felt their business was on firmer ground with such a well-built workhorse of a CNC. The new CNC has also increased their efficiency– another requirement of upgrading. With a faster vector speed, larger drilling head, and material pusher with vacuum arm, the Anderson Spectra 48 ticks the box of increasing productivity.
“The transition from our old CNC to the Anderson Spectra was very smooth,” says Nathen. “Jacks took care of everything. The installation and training process went as well as could be expected. Our staff love the new CNC. It’s good and functional and we’ve had no problems with the machine since it was installed about a year ago.”
Nathen has plans to continue growing their business, with an edgebander for laser-edged tape their next purchase. Going by their track record over their first four years of business, there’s undoubtedly more growth to come as Awesome Kitchens make in roads into the Auckland kitchen market.
Anderson GS-612
AWISA 2020 was to provide Kiwi visitors with an opportunity to view and discuss the fastest and most productive flat-bed CNC available in the world.
Available through Jacks, the Anderson GS-612 uses groundbreaking lineal iron core motors to drive the X & Y axis movement – the same technology as used to propel high-speed trains. With an acceleration of 0.7G and vector speed of 169m/min, the GS-612 delivers an average 30% more productivity than conventional CNCs. Wear and maintenance free, the iron core motors in would have been seen combination with the 11.2kW liquid cooled spindle enable cutting speeds of 45m/min.
The Anderson GS-612 is built for speed, accuracy and durability. These claims are supported with the quality of the componentry -for example the 32 spindle drilling head with twin 2.2kW motors, large 25mm THK guides and 32mm Z axis ball-screw.
There’s no need to wait for the next AWISA: there’s an Anderson GS on the showroom floor at Jacks in Auckland. Call today for a demonstration.
Safety first with Felder PCS
AWISA 2020 was to provide the official lunch of the Felder PCS® system in Australasia - a safety system that makes serious accidents on sliding table panel saws a thing of the past.
Every woodworker has ten good reasons not to compromise when it comes to safely working on a sliding table panel saw. Felder Group’s new PCS ® system prevents accidents at the speed of light. When the risk of an accident is detected, PCS® triggers the lowering of the saw blade under the saw table at the speed of light. The functionality is based on the electro-magnetic law of repulsion, facilitating an extremely short response time of a few milliseconds.
Upon detection of an unexpected and fast approach within the saw blade area, PCS ® triggers the safety mechanism, lowering the blade. A safety zone envelops the saw blade and protects against access from all directions.
Unlike other safety systems, the PCS® safety system works with damage. After an activation, a simple push of a button and the sliding table panel saw is immediately ready to use again. PCS® works without consumable parts and is therefore completely adjustment and maintenance free.
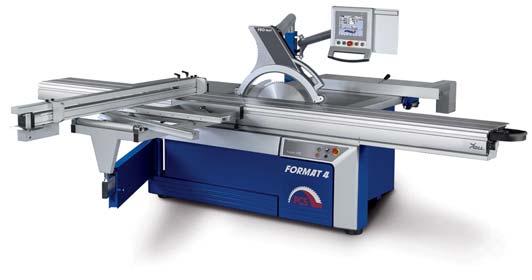
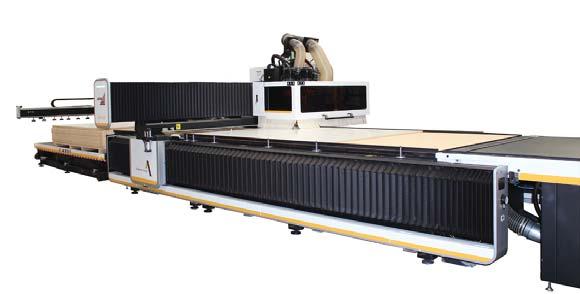
For more details talk to Jacks. 0800 522 577
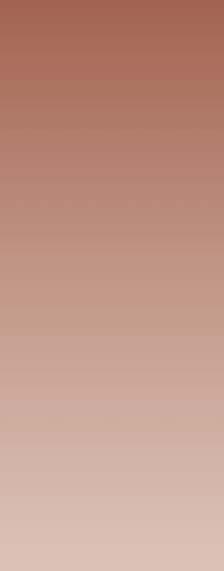

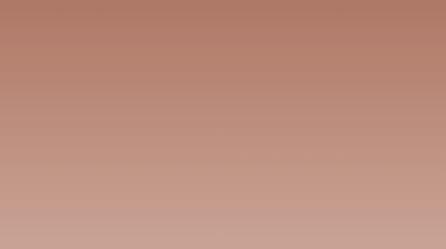
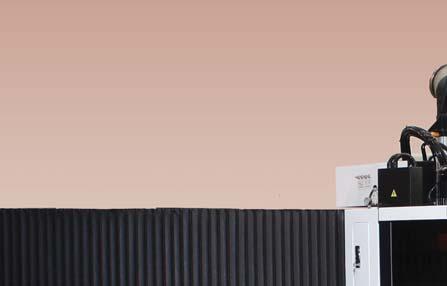

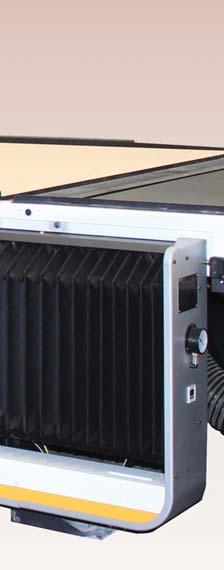
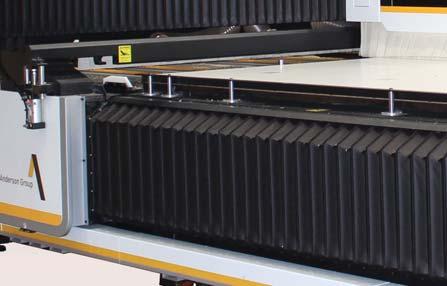


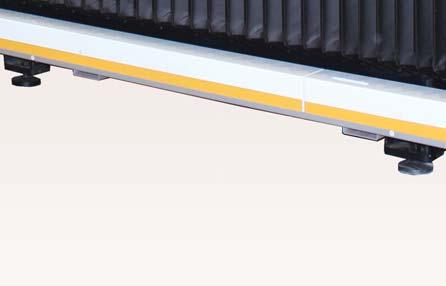