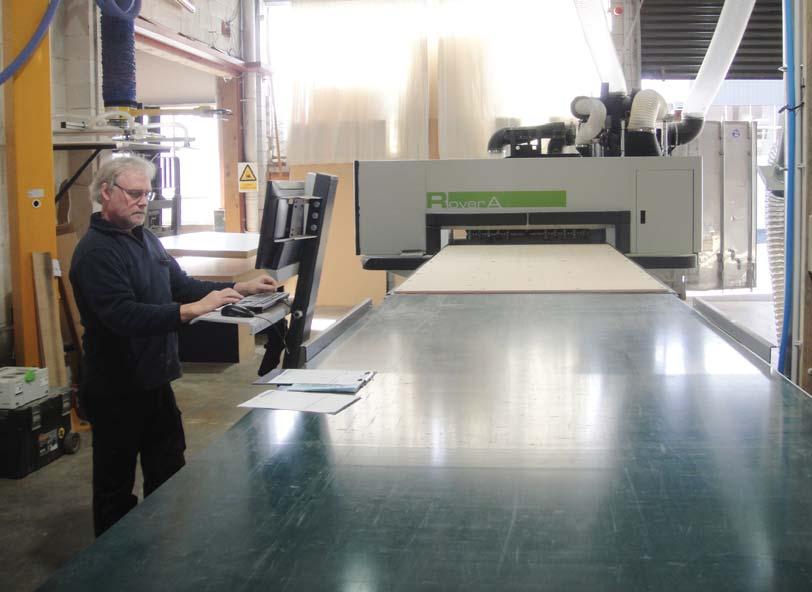
4 minute read
Rover A technology ongoing growth and competitiveness for DBJ
For DBJ Furniture on Auckland’s North Shore, the purchase of a new 5-axis Rover A Smart ft 15 36 from Biesse was prompted by the ongoing need to remain current with software applications and support as much as requiring a new router, but the resultant design and manufacturing benefits also ensure the company’s growth and competitiveness can remain strong through out the next decade.
The company’s previous router also a Biesse was 14 years old and still going well but it was felt an upgrade was needed, as much as anything to ensure the interface between design and manufacture was current and serviceable. As co-owner Paul Walkinton remarked, “where in our lives do we rely on 14 year old software - it was time to upgrade.”
The company’s first purchase decision was to move to a 5-axis. “We are a bespoke joinery and fit-out company and mostly use the machine for nesting but we could see that a 5th axis could have real benefits for us and they are not as expensive compared to 3-axis machines as they used to be,” says Paul.
“Our next decision was what do we add to the base unit. Our factory layout doesn’t suit an in-feed loader set up and as we don’t run it flat out anyway we decided to use the space we had for an unloading table. The cost benefits of this was a no brainer. We are likely to be cutting a sheet into 20-25 parts which need to be stickered and unloaded. Using a sweep to push the cut sheet to an unloading table allows the next sheet to be cutting within 20-30 seconds while we are processing the first - this alone makes it 3 times faster than the old machine.
“At this point it came down to a couple of machines and our previous experience with Biesse helped swing us their way with all our staff, from CAD drawers and designers to machine operators, being familiar with our previous Biesse router.
“The decision has been a good one the nesting side has been a smooth transition and the 5-axis capability has helped opened up new capabilities with solid timber work. We build boat parts from solid teak, previously this required processing through a band saw, then spindle moulder, then hand sanding, very heavy hands on with a lot of manufacturing hours. Now the same product requires a single pass and is millimeter perfect. We also now do our own door hardware, handles and routered hinge cutouts, again all in one pass, and a spindle head which can rotate through 365 degrees provides a great finish.
“Innovation around the vacuum set up has really helped. The ability to zone our table into 4-5 different areas is a great feature giving stronger vacuum where required when handling smaller parts and the fact that we can covert to pod & rail or a mixture of the two adds further flexibility.
“The fact that throughput on this machine is so much faster also allows us to experiment with new products and opens us up to exploring new methods, we are currently looking at manufacturing stair balustrades as an additional component we can produce in house. We are also able to knock out samples for clients or architects that would have taken hours by hand in maybe 45 minutes, again all millimeter perfect.
Paul was also mindful of post sale service and technical support. “I have found you need to invest time and effort in new machinery and software to ensure you gain the most from your investment. The onboard software B-Solid was new to us and took a bit of getting our head around and we did require quite a bit of help to get up and running. You need to push hard to get the most out of new technology and you need someone to help you get there and achieve the efficiencies possible. Biesse have been good in this regard, being proactive in showing us what can be done and responsive to any requests we have made.
“Coming up to a year in place we are very happy, our workflow is faster and our capabilities are wider. We like technology, we like to grow, this machine suits us on both points.”
Leitz HeliCut system
the All-Rounder for flexible processing of Wood and Plastics
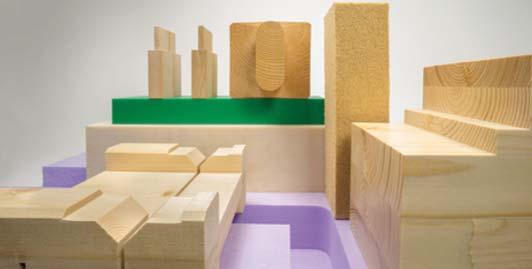
For years the HeliCut cutter head has proven itself in timber construction on CNC-controlled joinery machines. lt is the highperformance tool for special machining operations as for example rafter bird's mouth, tenon joints as well as for grooving and rebating. When cutting with and against feed, cutting in end grain and crosscutting, the cutting results are nearly tear free.
Furthermore, the finish is completely smooth and there are no cutting marks.
HeliCut as a shank router cutter is a multi-purpose tool for sizing, grooving and boring in solid wood, glued laminated timber and plastics. High feed rates and optimal chip ejection are possible with this tool even in large boring depths with spiral shaped arrangement of the edges as well with the plunging edge with chip breakers.
With the HeliCut copy-shaping cutterhead, the customer gets a new, multi- purpose and especially efficient tool. This tool is a real allrounder for reliable and efficient jointing, rebating and sizing operations in different working materials.
The success of the HeliCut-System mostly results from the turnblades used and its arrangement. lmproved cutting edges and cutting geometry as well as optimized different cutting applications.
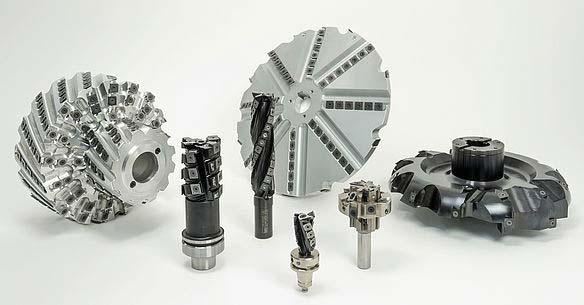
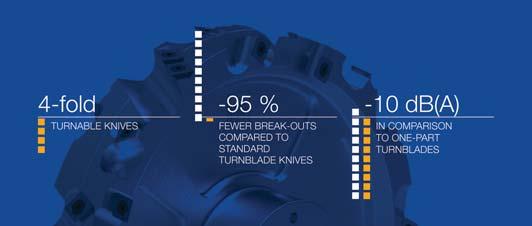

Radial knife clamping without inconvenient wedges, allow easy and precise changing of knives and additionally saving time.
Actually the HeliCut-System has three optimized cutting edge qualities:
• Tungsten carbide: Quality and precision already as a standard version

• Tungsten carbide with micro finish: Allows longer performance times and improved finish quality
• Tungsten carbide-TDC: This coating is used in very abrasive materials such as laminated timber, plywood or multiplex.
Another important component of the HeliCut-System is the tool body. Consisting of highperformance light metal, these bodies can be coated with a wearresistant protection layer. The rather low weight causes high balancing quality relieving on the one hand the machine bearings considerably and on the other hand increases performance times and improves cutting results.
0800 578 665 www.leitz.co.nz
The tungsten carbide knives can be changed four times, resulting in higher tool life and less cost. www.leitz.org