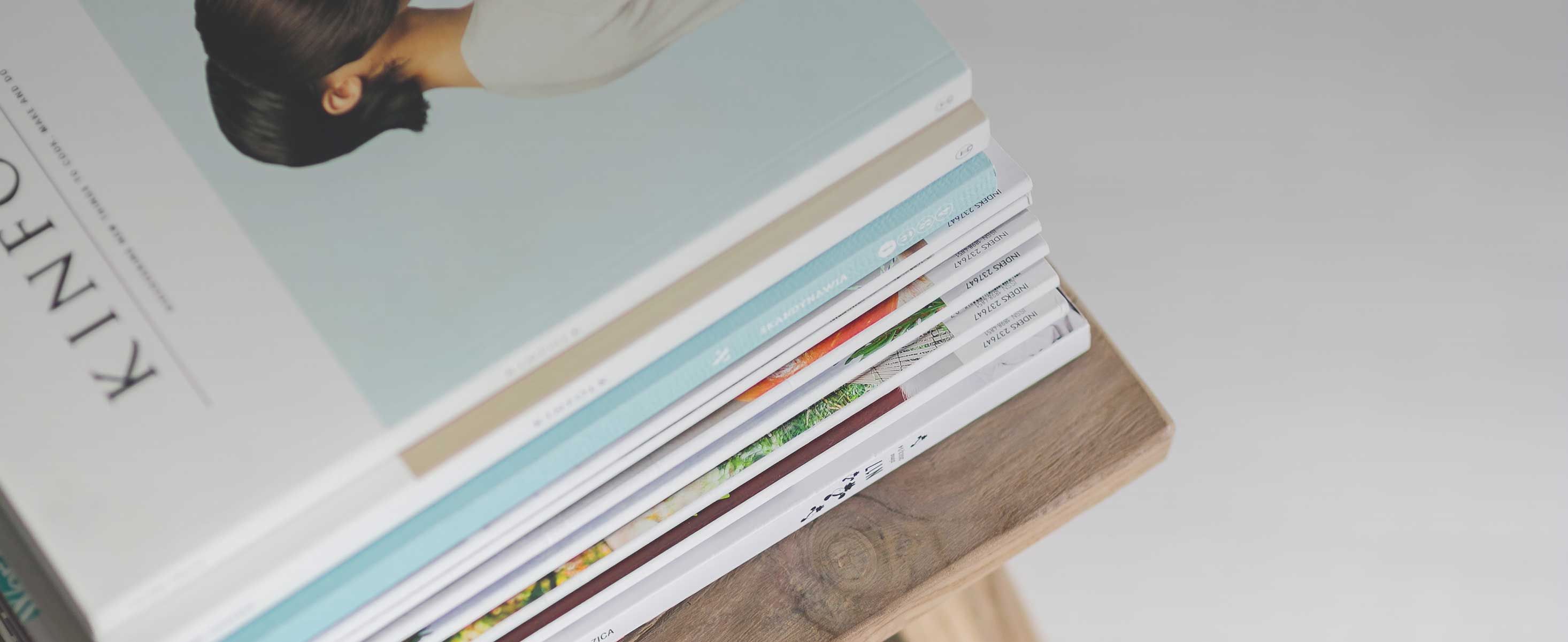
2 minute read
Rover HD Hagley Kitchens take technology to the next level
The Rover B ft High Dynamic is Biesses’ newest model in the Rover range of CNC’s and it is setting a new pace in processing panel for cabinetry and kitchens. Hagley Kitchens are the first in New Zealand to purchase the new HD model and we spoke to Managing Director Nathan Moore about their expectations for the new machine currently being installed in their Christchurch factory. We will return in a future issue to see how those expectations were met.
Hagley Kitchens are currently running two Biesse Rover Bft with a Winstore panel storage system. They are both performing well and the company will continue to use them, but as the workload continues to increase and with the factory already running from 5am - 5pm it was time to add more capacity.
“The two Rovers have worked so well for us we were always going to buy the next version of what we already had. They are real workhorses and with the same software and the same operating systems the new Rover Bft HD has many similarities but offers significant performances gains” says Nathan.
“We are expecting it to run at upwards of three times the speed of our existing machines, largely due to faster acceleration times, faster cutting speeds and improved drilling options.
“The new BHC42 boring head, not only accelerates faster from hole to hole which is itself a big gain, but its larger span allows it to drill in a single plunge where other more traditional boring head would need two or more plunges, a big time saver when drilling holes for cabinet feet or cabinet setup. The onboard tool changer also allows tool changing on the fly while the machine is performing drilling operations.
“To maximize acceleration and deceleration, Biesse went down the track to re-think the safety of the machine, replacing the standard protection canopy around the gantry with a cabin enclosing the machine. In this way not only has Biesse achieved a higher level of safety, but also a greater visibility for the operator and allowing the gantry, that now has shed the weight of the safety, to move the operating units, main spindle and boring head at higher speeds and more significantly higher acceleration and deceleration.
The Rover HD will deliver higher cutting speed and faster working cycles. New tooling technologies, combined with rigid structure and greater acceleration and deceleration will allow it to reach higher speeds within
The new hi-flow vacuum table has been significantly redesigned and our testing has shown that with the same pump you can achieve 75% better vacuum, meaning you are able to cut most components only once, doing away with the need to ‘onion skin’.
Warrick Small Biesse Sales Manager Christchurch
a real cabinets nest. Also tools will benefit from getting to the designated cutting speeds faster, resulting in an improved tool life.
“Biesse are always innovating, always advancing their technology and we have benefited from their improvements with each new purchase over the years. Traditionally the industry used to hang on to machines for as long as possible, repair and replace parts, but not anymore, with advances coming so quickly these days we need to invest to keep up.
“We expect this machine to keep us technologically current over the next 5-6 years until a new set of innovations and improvements present us with further productivity gains that can’t be ignored. I’m not sure where they will be, but reducing labour is the key. For us it is likely to involve a move into robotics at the loading and unloading stage. Our CNC operator who is about to unload his new Rover HD at three times the speed of the previous one is going to find himself busy, we will have to look at that.
“As a company we tend to be leaders in moving towards innovation, it is exciting but also a little daunting embracing new technology but if you don’t attempt to push the boundaries they will always remain, leaving little room for improving capacity and efficiency.
“Judging from our past experience with Biesse the outcome will be good - we will let you know how it goes in the next issue.