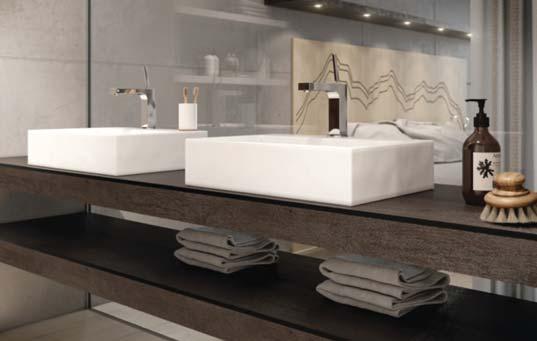
2 minute read
Carbitool the woodworking masters
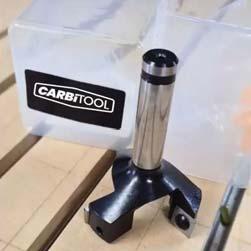
Carbitool has a long standing reputation for excellence in the manufacture of carbide tools for the woodworking, cabinetry, joinery, furniture, timber and panel industries. We caught up with our long-term customer, the renowned custom furniture maker Christian Cole, at his Coburg joinery.
How did you start in the joinery business?
My first-ever joinery was one square metre in my mum’s garage. I qualified as a Cabinet and Furniture Maker in 1994 then spent a couple of years in the construction industry fitting out large commercial projects. Christian Cole Furniture was established in 2000. We rented premises in Eltham then Heidelberg, then purpose-built this factory in Coburg in 2003. There are five of us in the business now. I’ve got two other tradesmen and two apprentices. Plus my wife Fiona takes care of marketing the business.
What does Christian Cole Furniture produce?
Despite our name, around half of our work is architectural joinery – beams, parts of houses, timber kitchens and bathrooms. We also do a lot of interesting staircases. Everything we do is custom-made to order. It’s typically high-end one-offs pieces, but at the moment we’re making 1,000 chairs for a school. We only use salvaged, recycled or FSC timber. The table we’re sitting at now has a single plank for its top, cut from an old redgum that was rolling around a hop farm causing havoc – it now has a new useful life. Some of our clients supply their own special wood for a project. We keep stacks of unusual recycled timber in our factory – sometimes aging it for several years. It’s a bit like a winemaker storing barrels of wine!
In which other ways do you specialise?
Something that sets us apart is our ability to create furniture from multiple veneers. We have the machinery to vacuum press several layers of wood together to create solid boards. We don’t use CNC machines. If any of our projects require large numbers of repetitive processes, we outsource that to someone else. Similarly, people outsource stuff to us that needs a custom, hand turned approach. Basically, we just love pushing the envelopes of joinery –we’d get bored if we did the same things all the time! We don’t mass produce anything; every day it’s a different project.
What kind of machinery and tools do you use?
We’ve invested in heavy duty old machines that are well built. They’re like an old car which you can fix yourself. It would cost around half a million to buy a CNC machine, and we just wouldn’t use it! We’ve used Carbitool router bits for over 20 years – for making dovetail joins, bullnose and straight cutters, and a range of door profile bits.
Why do you prefer Carbitool?
Their router bits are better cutters and last longer. They stay sharp longer without resharpening –then we can get them resharpened five or six times before they need to be replaced. The cost of sharpening tools is one of our biggest expenses, but it’s worth spending $5 or so per bit when a new one can cost up to $50. Carbitool router bits can be a bit more expensive than other brands, but they represent excellent value; they’re definitely the best products.
To learn more about the Carbitool range of timber tools, visit us at www.carbitool.com.au
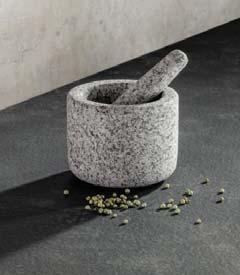

Invest in a simplified manufacturing process
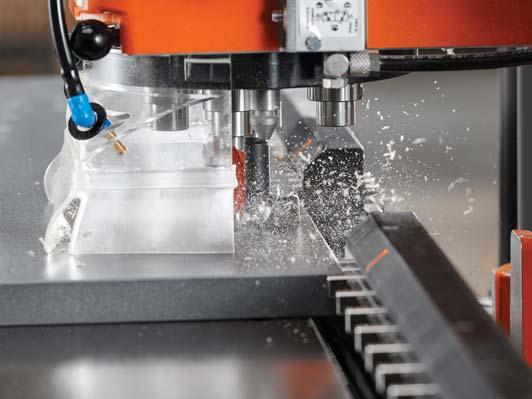