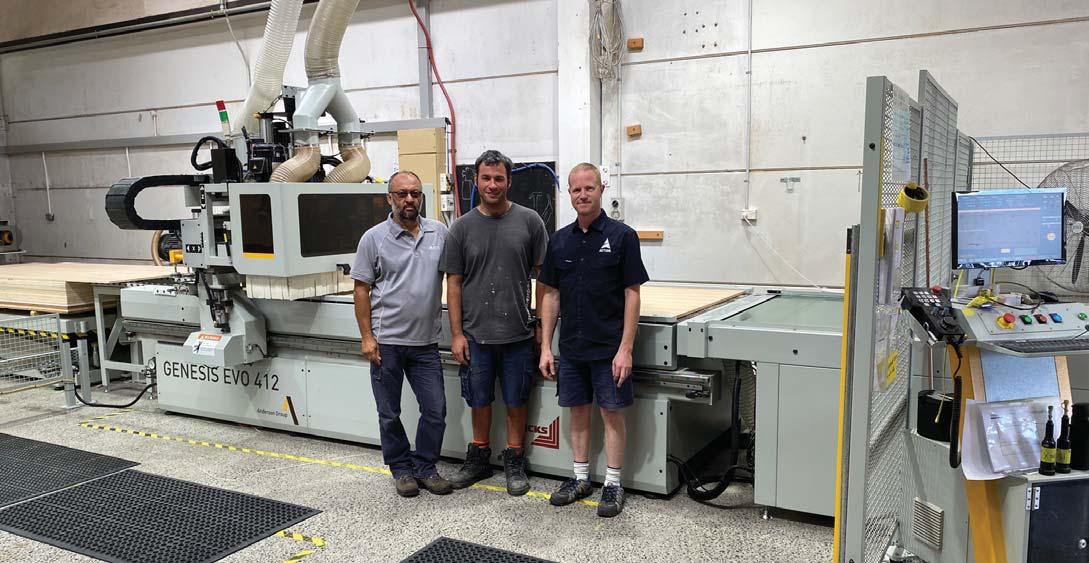
3 minute read
Anderson Evo halves machining time
“We can land a European campervan in NZ, fully kitted out cheaper than we can buy the materials we need to build one of ours here in Auckland.” With this statement Managing Director of Action Manufacturing Grant Brady lays out the stark reality of the commercial environment they’re operating in. At their Albany facility on Auckland’s North Shore, ACTION are fitting out up to 750 Recreational Vehicles (RVs) a year.
Grant’s not complaining when he points to the apparent affordability of European RVs. Instead he’s pointing out a crucial advantage ACTION have. Although apparently cheaper, a European RV is only designed for 15 – 20 of domestic use a year, for a decade or so. Compare that with ACTION’s vehicles, which are built to withstand 240+ days use a year for six years on the roads around both NZ and Australia (ACTION are exporting 40% of production into AU.) “And then they’re sold and used for another 15 years or more as someone’s private RV. It’s like the difference between buying a door handle for your house, and a door handle for a hotel,” explains Grant. “As with a hotel door handle, our RVs are designed and built with durability in mind.”
It’s this durability, alongside the consistent quality of their RVs, that keeps this proudly Kiwi company busy producing for many of NZ’s well-known RV rental companies, including Kea, Britz and Maui. Durability is what dictates ACTION use of 15mm European ply rather than the traditional 12mm. In the same vein, 2mm edgetape is standard throughout their fit-outs, and the production method is cam-and-dowel and glue. Heavierduty materials and hardware are essential to deal with the banging and scraping RVs receive during their rental years.
Durability was also a consideration when ACTION came to replace one of their aging CNCs. Having grown their production from jigs and power-tools through CNC nesting over the years, in 2019 they chose to take the next step in efficiency and invest in a complete CNC nesting cell. “We’ve proven the value of efficient manufacturing over the years” says Grant, “and so decided to step up our investment in machinery, in the expectation of even better results.”
That investment included a new Anderson Evo CNC cell, and a Homag 1650 Edition series edgebander. Just a few months in, the improved efficiency in the machine-shop is already clear. Machine Shop Team Leader Phillip Meads lays it out simply: “Our CNC processing time for a sheet has more than halved” he says. “We can process a sheet in around 8 minutes now.” Given ACTION go through between 18,000 and 20,000 sheets of ply a year, halving the processing time is very significant.
Anderson’s EVO cnc comes with a twelvestation tool carousel for fast tool changes, while pop-up stops and vacuum zones give flexibility for processing. In addition to being fast – up to 80m a minute – there’s a scissor lifting table, a pusher and an off-loading conveyor table, all with dust extraction. After processing it’s over to the Homag for edgebanding - where a Compakto return table adds to the overall efficiency of production.
Mark Julie – Production Manager – confirms that the machines from Jacks are performing as promised. “We’ve had to change a few processes as a result of moving to a newer technology” he explains, “but in general the changes have been related to software.” ACTION have invested in AlphaCam in their busy design office, and transfer machine files to the Anderson Evo CNC via USB. CNC Operator Logan Steven Brown explains the process. “We get the design file for each vehicle from the office all fully nested. We simply open the file, run the nests on the EVO, and then put the labelled parts to our trolleys for transferring over to the Homag.”
Another critical factor in ACTION’s investment decision was the back-up and support available from Jacks. Anderson and Homag machines are renowned for their reliability, but when things do go wrong then Action need fast and effective support – or their Albany site’s assembly teams (with 85 staff) can quickly run out of materials. Jacks’ large and experienced service team can provide the timely support they need. Another back-up:ACTION have kept a couple of their older machines – a CNC and edgebander – to cope with any unexpected overflow. Although so far they’ve been largely redundant.
With their continued growth – the company is spread over three sites employing 220 staff – ACTION are a success story for NZ manufacturing. From the early days of powertools and jigs to today’s modern machine shop employing 8 staff, ACTION’s willingness to invest in new technology is reaping rewards. As Australasia’s leading quality vehicle specializer they represent the excellence and efficiency that lives behind the ‘proudly made in New Zealand’ brand.