PROJECTIVE SYSTEMS
DIRECTED RESEARCH
Advisor: Professor Iman Fayyad
INSTALLATION DESCRITIZING GEOMETRIES ILLUSORY IMAGE FLATTENING
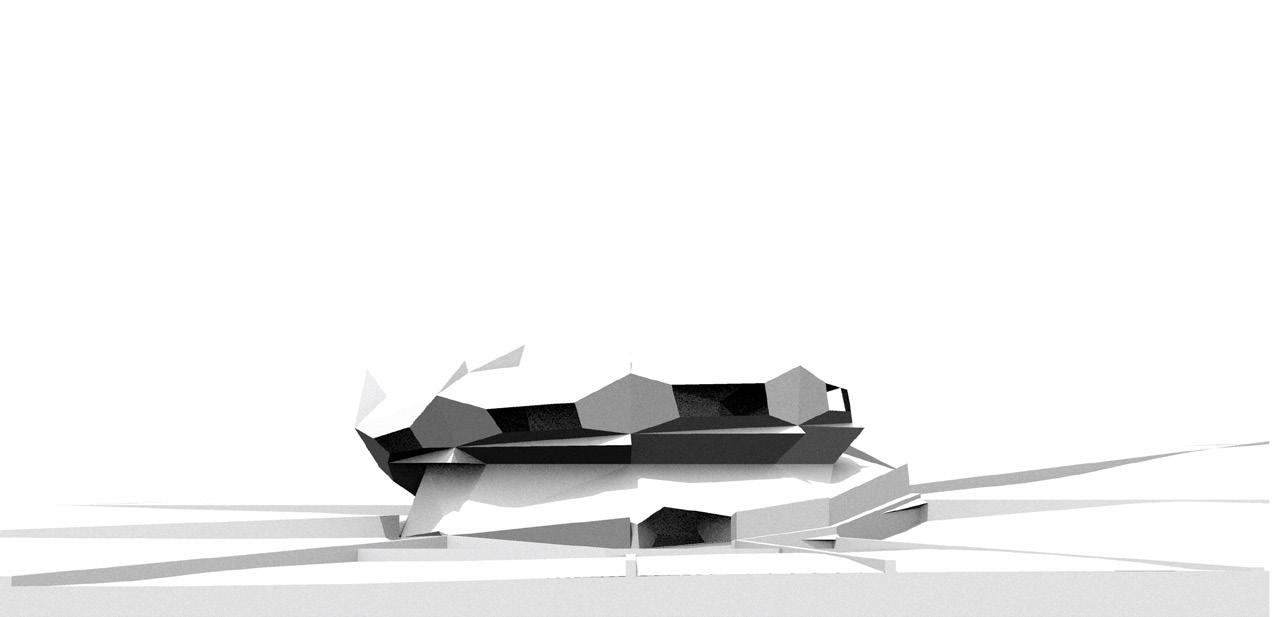
DIRECTED RESEARCH
Advisor: Professor Iman Fayyad
ANALYTICAL HAND DRAWING OF SHELF - Exploring flatness and flattening
DESK SHELF INTERIOR
The prompt for this one week drawing exercise was to demonstrate a form of flattening through drawing. In reparation of this we researched trait and trompe drawings produced by and for stone masons. These drawings layered common parallel drawing such as plan, section, and elevation atop of each other to create a comprehensive documentation to produce a complicated 3D object through flat drawings.
From this I focused on a shelf I had produced for a wood working class, which started as flat planar material, and was drawn and designed on that same material. This process of the drawing was a sort of re-flattening and analysis of the shelf. This process allowed me to actually find a design mistake, and understand the construction of this object more.
This second exercise was focused on working with singularly ruled geometries such as cones and cylinders that are created through revolving a line. In this there was the design of a three dimensional form from which the image would be based. The goal of this exercise was to leverage the qualities of geometry to make an illusion in which multiple three dimensional forms could exist as a result of a singular drawing. This was done through varying rendered underlays, line weight, which ultimately resulted in a drawn form in which multiple different surfaces could be true at once.
After this the geometry from which this drawing was based, was unrolled into a continuous strip and turned into a trait drawing. The unrolled surface was then experimented with, rolled up and folded to create the new geometries vastly unlike the original object.
This process was focused on negotiating the issues of translating complex curved geometries into planar material through the processes of various discretization methods. Within this, the methods of discretization were meant to take priority over the original geometry and begin to create thresholds and apertures. In this particular case the geometry we chose was the Klein surface that effectively is a three dimensional figure 8 folded over itself.
Because of the characteristics of the geometry, we decided to chose the program of a courtyard house. Within this, there would be a singular circulation path that would intersect at the entrance where one could chose to go up the ramps to the private or down towards the more public area. In the actual process of discretization an outward pointing secant plane and the truncated cone. The truncated cone was used as sparingly as possible and only used where the Gaussian curvature switches from positive to negative. At these points the secant plane method is not possible due to the normal curves being completely perpendicular, which pulls the one end of the secant plane off for hundreds of feet. As such, the truncated cone was used in these areas to create apertures and bring in light and visual connection to the space.
This project was completed in collaboration with Maxwell Fernandez.
This installation was the culmination of our previous three exercises and explorations into geometries and representation of them.
This phase of the Directed Research class was focused on creating something at pavilion through the processes of applying curved crease folding and origami to standardized panels four by eight feet. Within this, there is a focus on the individual panel and more specifically maximizing the 4’x8’ standard sheet size.
Under the guidance of Professor Iman Fayyad, this project along with the other two in our class, was awarded the Britton A. Memorial Award for best group project
This project was completed in collaboration with Sarah Fellingham, Dairus Polillio, Adrian Suciu, and Oscar Cheng.
The research for the pavilion first started with finding a design of a panel that had to meet two main criteria: in which it had to be formally interesting and it had to be able to able to make multiple forms through the attachment points of individual panels . Within this the goal was to design something that could twist, turn, or continue in a straight line depending on how the singular panel was configured.
After the folded panel to the right was designed, study models were constructed to see its potential to be infinitely replicated and the different ways in which these panels could connect in unique ways. When connecting 5 “roof” panels together the lower half of the “wall” panels could be attached together at the base and make a sort of pinched connection. This connection proved to be an integral piece of the way in which the panel was used and allowed us to get an element of rotation
Another element that was explored was how to potentially create seating from the same material using a single or half sheet of 4x8 HDPE. This proved to be a challenge as we had decided to integrate the seats into the design and attach them to the actual wall panels. This meant we had to design seats to have an angle that matched the wall panel once folded. These seats also served as the footers to stabilize the structure and stop it from splaying out.
Seating experiments of how to create structure using a single or half panel. Some of these methods employed curved crease folding to create structural rigidity
This model was constructed at 1” = 1’ in order to study the constructibility of our proposed design and seating options. In the spirit of studying how it would actually be assembled, no glue was used and instead aluminum wire was used to simulate a bolted connection.
It was also created to identify potential structural issues prior to construction such as sagging roof panels, areas that required more fasteners, and issues of how it would meet the ground
Physical model constructed in collaboration with Sarah Fellingham
There were a lot of lessons learned from the actual full scale production of this. Many were concerned with oversights in end conditions of the structure and unforeseen site and material issues.
1. The materials we received were a different ductility then the ones we had tested with so they were much more brittle and tended to crack at the cut creases. We used heat guns to mitigate its affect, but this combined with Syracuse’s cold weather continued t create issues with pieces breaking. This resulted in structural issues and the destruction of some panels.
2. Because we designed the panel system to be seemingly infant it was very difficult to deal with the ends of it. This was because structurally it wanted another set of panels to support it. In a future iteration of this we would go back and add in caps for those two end pieces shown in the right most photograph.
3. We also had to move the structure after it was assembled which resulted in more cracks and structural issues.
4. The weight of the actual HDPE material helped keep the structure more stable then the one to one model but also was an issue at the two ends where it tended to sag. We would have to design a sort of end cap panel to help carry the load at the ends.
5. After doing one side of the pavilion we learned that we could preheat and prefold the panels in order to make assembly easier.
6. We wanted to attach the panels without fasteners and design a tabbed connection in order to limit the amount of fasteners.
7. As seen in the first image, the final materials turned out to not be as rigid as our test materials which lead to structural issues in the seats which would need perpendicular supports in order to avoid this.