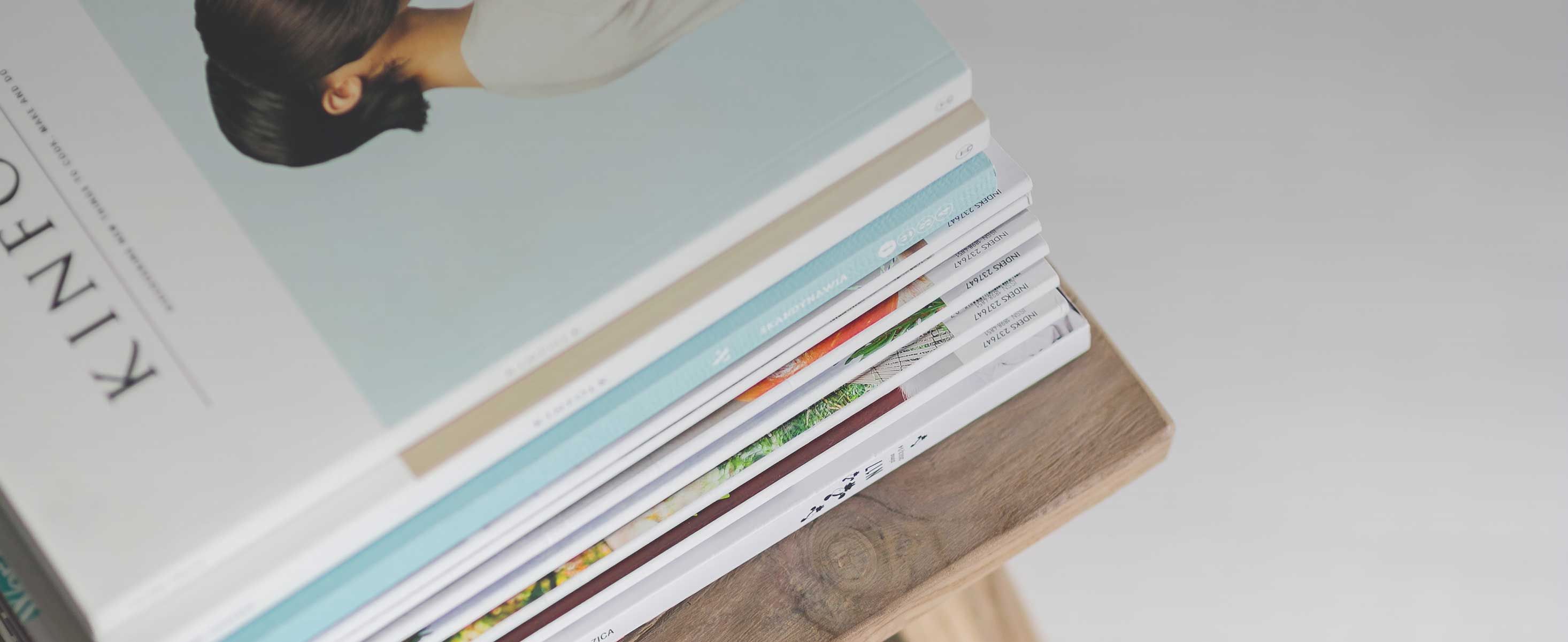
2 minute read
Simulation of AC power controller
Course Outcomes
At the end of this course, students will demonstrate the ability to 1. Study the electrical, magnetic and thermal loading of electrical machines. 2. Learn various factors which influence the design of dc machine. 3. Comprehend various factors which influence the design of transformer. 4. Learn various factors which influence the design of induction machine. 5. Realize various factors which influence the design of synchronous machine. 6. Use software tools to design electrical machines.
Module 1: Introduction (7 Hours)
Major considerations in electrical machine design, electrical engineering materials, space factor, choice of specific electrical and magnetic loadings, thermal considerations, heat flow, temperature rise, rating of machines.
Module 2: DC Machines (8 Hours)
Sizing of a DC machine, main dimensions, Choice of number of poles, Estimation of number of conductors/turns, Coils, Slots, Conductor dimension, Slot dimension, Length of air gap, Design of field system, Interpoles, Commutator and Brushes
Module 3: Transformers (8 Hours)
Sizing of a transformer, main dimensions, kVA output for single-and three-phase transformers, window space factor, overall dimensions, operating characteristics, regulation, no load current, temperature rise in transformers, design of cooling tank, methods for cooling of transformers.
Module 4: Induction Motors (8 Hours)
Sizing of an induction motor, main dimensions, length of air gap, rules for selecting rotor slots of squirrel cage machines, design of rotor bars & slots, design of end rings, design of wound rotor, magnetic leakage calculations, leakage reactance of polyphase machines, magnetizing current, short circuit current, circle diagram, operating characteristics.
Module 5: Synchronous Machines (7 Hours)
Sizing of a synchronous machine, main dimensions, design of salient pole machines, short circuit ratio, shape of pole face, armature design, armature parameters, estimation of air gap length, design of rotor, design of damper winding, determination of full load field mmf, design of field winding, design of turbo alternators, rotor design. Module 6: Computer aided Design (CAD) (7 Hours) Limitations (assumptions) of traditional designs, need for CAD analysis, synthesis and hybrid methods, design optimization methods, variables, constraints and objective function, problem formulation. Introduction to FEM based machine design. Introduction to complex structures of modern machinesPMSMs, BLDCs, SRM and claw-pole machines.
Text Book
1. A. K. Sawhney, “A Course in Electrical Machine Design” , Dhanpat Rai and Sons, 6th Edition 2010.
Reference Books
1. S. K. Sen, “Principles of Electrical Machine Design with computer programmes” , Oxford and IBH Publishing, 2nd Edition, 2006. 2. K. L. Narang, “A Text Book of Electrical Engineering Drawings” , SatyaPrakashan, New Delhi, Reprint Edition, 1993/94. 3. A. Shanmugasundaram, G. Gangadharan and R. Palani, “Electrical Machine Design Data Book”, New Age International, New Delhi, Reprint 2007. 4. K. M. V. Murthy, “Computer Aided Design of Electrical Machines” , B.S. Publications, 2008. 5. Electrical machines and equipment design exercise examples using Ansoft’s Maxwell 2D machine design package- ansoft-maxwell.narod.ru/en/CompleteMaxwell2D_V15.pdf
19EE2008 Digital Signal Processing
Course Objectives
1. To impart basic knowledge about digital signal processing 2. To understand Digital (IIR and FIR) filter design procedures.
L T P C
3 0 0 3