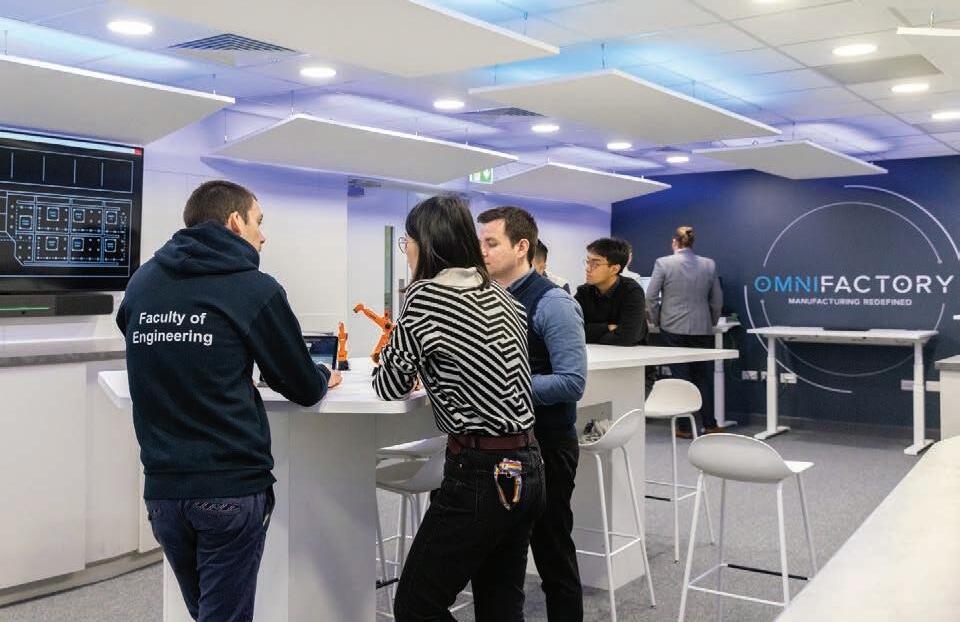
3 minute read
LOCAL UNIVERSITIES WILL HAVE A GLOBAL IMPACT
East Midlands universities are at the heart of the smart tech revolution as they work with businesses to tackle key challenges that could have a global impact.
Last month, the University of Nottingham opened the Omnifactory, a national demonstrator and testbed for smart manufacturing systems that will be used by industrial partners to use digital technologies for improving traditional manufacturing practices.
Situated at the Jubilee Campus built on the site of the former Raleigh bicycle plant, it features a bespoke factory floor that provides a unique reconfigurable environment.
The floor autonomously adapts itself to the next product’s environment and specifications, leveraging technologies including robotics, AI, data analytics and industrial IoT.
Svetan Ratchev, director of the university’s Institute for Advanced Manufacturing, says the £3.8m facility, which is funded by Innovate UK, will help to solve a number of industry challenges by “developing the next generation of smart, highly agile and efficient factories”.
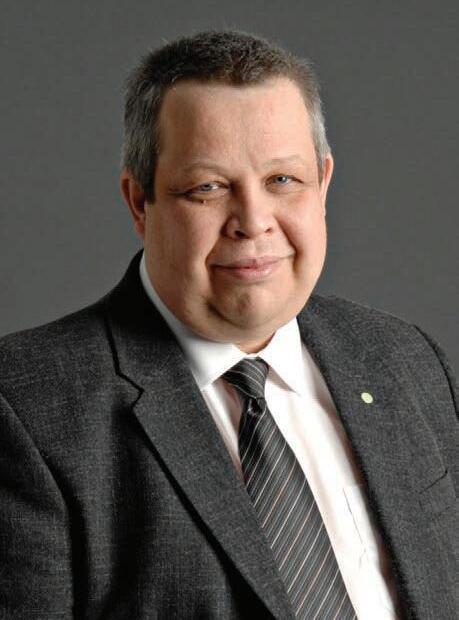
“Across different sectors like automotive, aerospace and consumer goods, manufacturing is becoming more configurable and customised to meet changing customer requirements and choice,” he says
Svetan adds: “The environment is in place to establish new collaborative research programmes with industry, as well as develop local supply chains and skills, which ultimately creates jobs and prosperity in the region.” reused, as well as reduce energy demand via monitoring. Recently, a team of academics led by Dr Elliot Woolley submitted an application for funding to use AI for further optimising food waste as part of the UK’s net zero commitments.
CUTTING FOOD WASTE and speeding up financial document analysis are two examples of how Loughborough University researchers are deploying smart tech for real-life impact.
Other projects are exploring how data analytics can give insights into individual consumption and health.
“At the same time, we’re moving from large volume to much more variable and unpredictable demand – for example, defence products can go from nothing to very high volumes in a short space of time because of geopolitical changes. It means businesses need to be able to rapidly ramp up production so they can be quick to market, as well as be able to mix different types of manufacturing in the same environment.
“During the pandemic, we also experienced the disruption of global supply chains, which highlighted a need for greater resilience, and since then we’ve had to deal with labour costs and a lack of skills.
“With all these challenges, we must think about how to rewrite the rules around manufacturing. This is what we are doing with the Omnifactory, which is highly agile in order to be efficient and cost-effective when we want to make complex products at high volumes or meet fluctuating demand.”
Digitisation can unlock a new business model known as manufacturing-as-a-service, in which a company can focus on product innovation while outsourcing the manufacturing process to a modern factory that is equipped with the latest technologies.
Its productivity and environmental benefits have already caught the attention of multinational manufacturers including Airbus and GKN, which will carry out projects at the Omnifactory, while Siemens has provided the technology.
The Engineering and Physical Sciences Research Council (EPSRC) Centre for Innovative Food Manufacturing, run in collaboration with major industry partners and the University of Nottingham, carries out research to identify new sources of material and reduce the demand on existing resources by simultaneously improving food products, manufacturing methods and supply networks.
It aims to redefine manufacturing activities from “post-farm gate to supermarket shelf” by exploring how smart technology can, for example, optimise how materials are used and
Professor Sergey Saveliev, who is the academic lead for Loughborough University’s AI and cognitive technologies global challenge work, says: “We can collect information about an individual’s health and what food they usually buy to understand how people’s eating habits are influenced, and how they could change.
“We could use a smartphone app, for example, to create a personal dashboard and offer suggestions on what they should buy for healthier eating.
“The data can also be used to understand the global picture by forming different clusters of society, which helps with supply chains and where to deliver changes at business and policy level.
“This can have huge potential for businesses, even in solving very simple problems. If you’re a local milkman who might be guessing on wastage, the data can help them make better decisions that increase profit margins.”
Loughborough’s AI and cognitive global challenge team, working with the computer science department, has also developed an AIbased solution for automatically analysing and extracting large amounts of information from computer documents.
Working with business process automation specialist Xceptor, it has created a deep learning model for natural language processing that can analyse the content and structure of invoices, tax forms and other digital documents in order to sort the information into categories.
The improved system will streamline processes such as setting up bank accounts, approving mortgages, responding to customer queries and processing insurance claims.