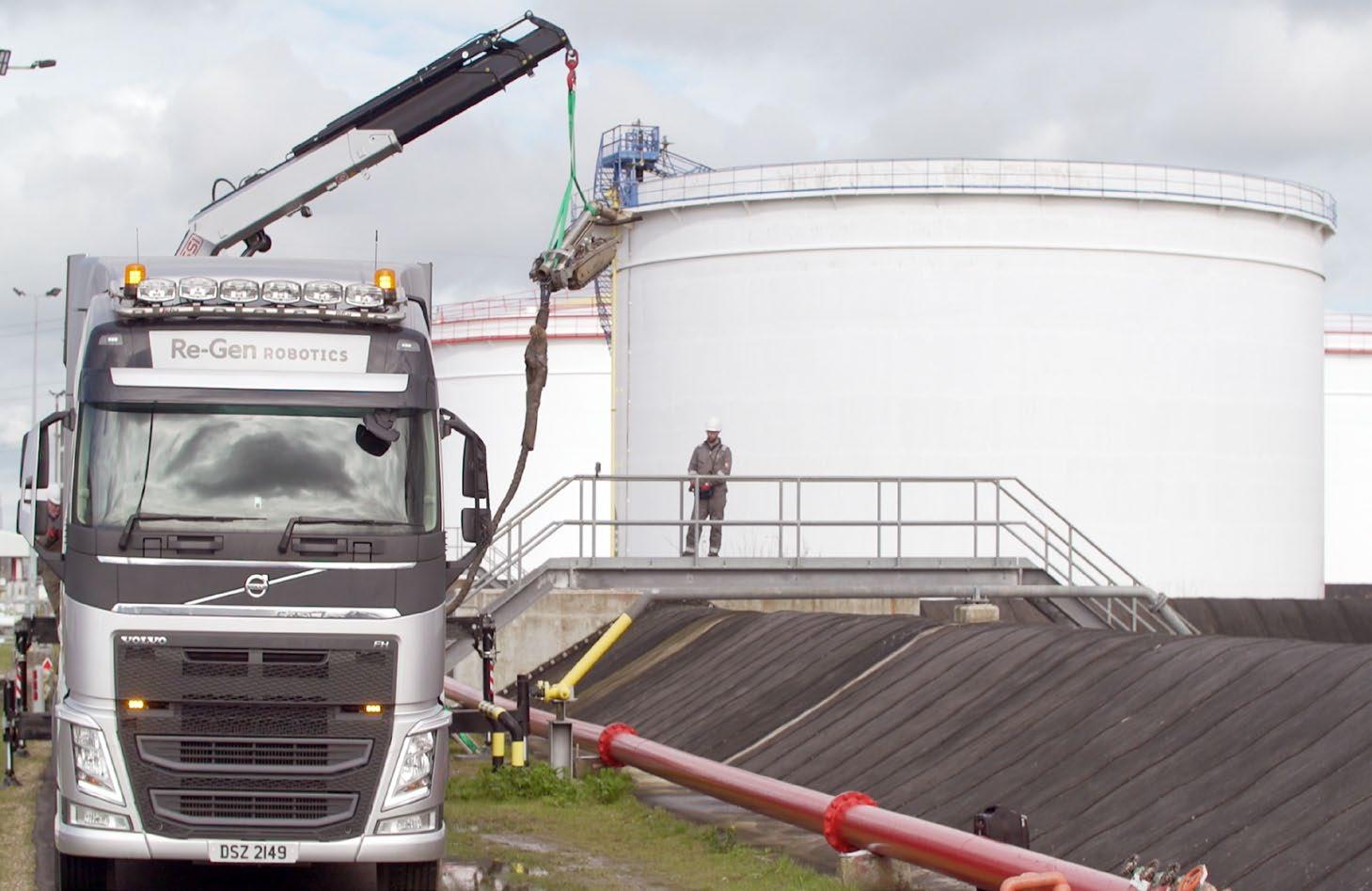
4 minute read
Re-Gen Robotics: secures the safety and integrity of your tanks
RE-GEN ROBOTICS secures the safety and integrity of your tanks
Managing Director Fintan Duffy discusses how his company supports some of the world’s most respected oil majors through his company’s tank maintenance solutions.
Last December Re-Gen Robotics picked up three Energy Industries Council Awards for our services to the oil terminal industry including: The Innovation Award for delivering enhanced products, services and strategies to meet specific client needs and for building differentiation in the sector; the Sustainability Award for taking responsibility as part of our business strategy, to conserve natural resources and protect global ecosystems and the Company of the Year Award, based upon best practice scores from the EIC’s 57 industry judges.
Presenting the Company of the Year Award, EIC President Campbell Keir praised Re-Gen Robotics for applying 100% no man entry robotics technology to “reduce the personal risk of a routine activity that many people are not aware of but is an essential industry task.”
While not always the most topical subject, asset integrity is indeed the most important part of an oil terminal’s operations. Ensuring tanks and related equipment are operated, maintained, and inspected according to the highest industry safety standards should sit at the heart of every company’s priority list.
Ignoring safety critical maintenance and asset performance optimisation can lead to enormous loss – damage to infrastructure, loss of production time, public investigations, environmental damage, and fines can have a very negative impact on a company’s brand value and reputation.
Safety and innovation are embedded in the culture of Re-Gen Robotics and underpin everything we do. The tank cleaning solutions we provide ensure the integrity of oil tanks, enhance performance, and support all regulatory compliance.

Productivity is enhanced and tanks are brought into operation again more quickly. Our closed loop cleaning system can reduce cleaning time by up to 80%, significantly decreasing downtime and loss of production whilst oil tanks are not operational.
On average cleans are 40 to 80% faster than a manned crew. A white oil tank which would ordinarily take an eight-person team, eight days to clean can now be cleaned in 2.5 days, reducing 280 man hours of CSE to zero hours.
Our patented, self-contained system includes vacuum, jetting, cranage, and robotics, with nothing extra to hire or buy, simplifying the entire tank cleaning process.
To date Re-Gen Robotics has made over £7 million investment across several key areas including our people, service offering, state-of-the-art headquarters, and robotic equipment and trucks. Our highly skilled team is proactively exploring emerging technologies and through our Research & Development Department and our sales team who stay in close communication with our clients, we are developing the tank cleaning solutions of the future.
In the last three years, Re-Gen Robotics has eliminated 11,000 plus hours of confined space entry cleaning. Over 40 tanks consisting of white oil, black oil and distillate tanks in gas plants have been cleaned and the first worldwide, 100% no man entry tank cleans for oil majors such as Shell, Phillips 66, Valero, and Vermilion, have been completed. As the sole authorised provider of this innovative technology and service in the UK, what we have created is a market leading offering. Supported by a fully equipped team with the expertise and confidence to clean any shape or size of oil tank including Fixed Roof, Floating Roof, Heavy Oil and Coned Floor Tanks.
Compared to anything else on the market, our tank cleaning solutions are risk free and far more efficient and economical. Our equipment is dexterous and versatile and can navigate and work in its environment using multiple sensors, while our operator remains in a stateof-the-art control room, protected from hazardous conditions.
Tank Terminal operators are focused on attaining productivity while also maintaining operational efficiency. By taking advantage of our latest and most advanced technology, they are reducing the duration of the tank clean and its intensity, and realising the significant benefits of efficiency, safety, quality, and cost saving.
