
1 minute read
Logistics
from Bulletin - EN 2023
by KOMA MODULAR
It took almost a year for the individual parts and materials for the construction of the airport to arrive from the Czech Republic and Italy. Let's take a look at the logistics of the project, which not only included coordination within KOMA in Vizovice, but also the teamwork with subcontractors. In order not to get lost on the 7,000-kilometre journey, the modules had to be wrapped in foil and numbered after production. The numbers are not only markers for transport, but also for the crane operators who loaded and unloaded the modules at the various stops between
Vizovice and Saint-Louis. The expedition underwent special customs clearance. Every module and shipping container with material had to have its own bill of lading. The most complicated was the clearance of the socalled ADR goods. (These are hazardous substances such as paints, sprays, gases, etc., editor's note) These are subject to an IMO declaration, which defines which substances and combinations of substances can be shipped together. These goods are then given a special label and safety class. Goods on the route from Vizovice to Hamburg were transported in trucks. Here, the containers were transferred to the RoRo ship, Grande Angola, on special chassis (technically, muffy trailers) to the hull of the ship.
Advertisement
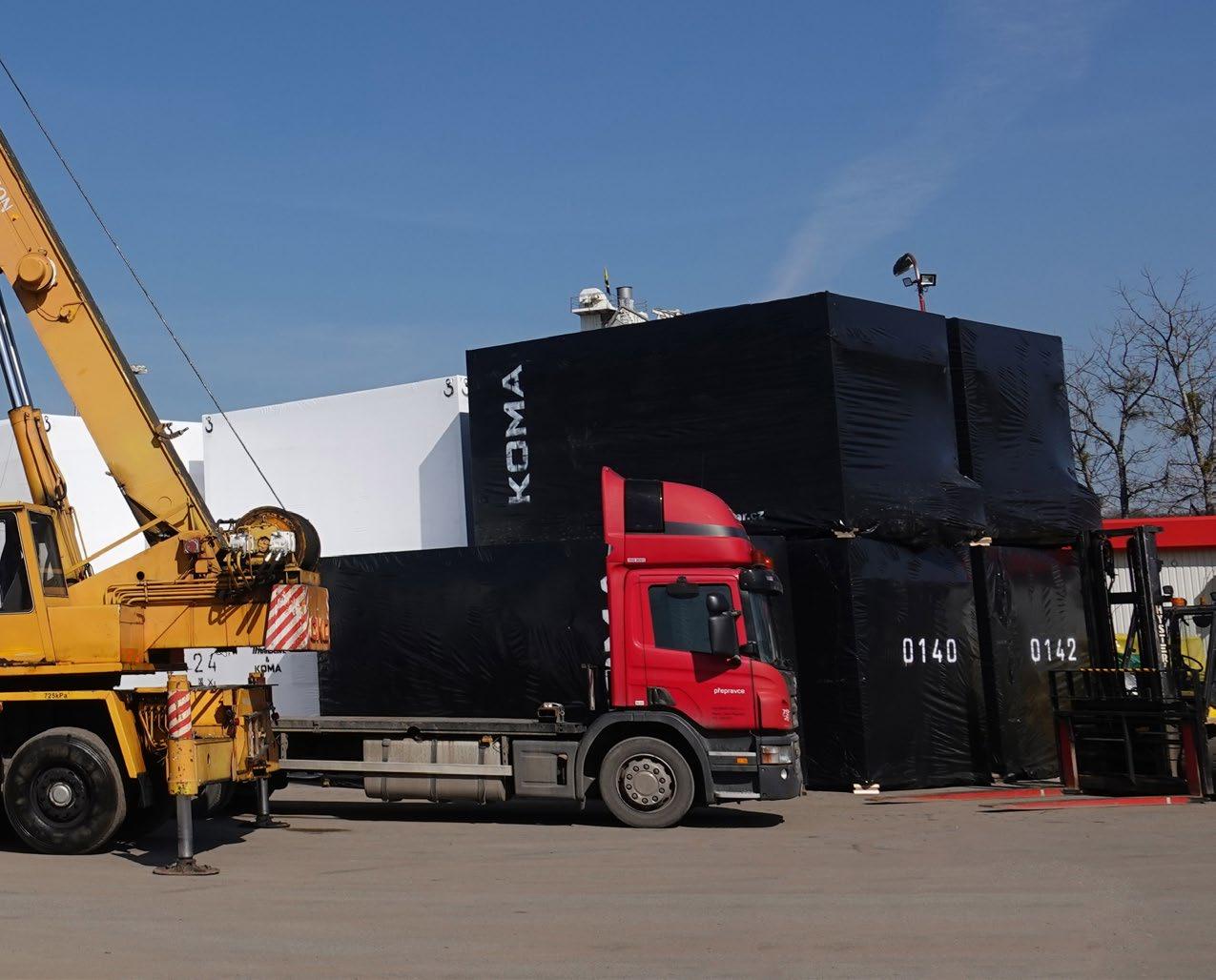
The ship docked at Dakar's largest port. From this point, the cargo continued on trucks to the storage facility. We wanted to use all the space for logistics. The material and equipment were packed both in shipping containers and in the airport modules themselves. The assembly material and other equipment were transported in KPT boxes. Thanks to their ideal dimensions, they filled the spaces of the modules perfectly and there was a minimum of wasted space during transport. As there was a lot of material – a mobile ware- house was created on site from the shipping containers brought in with an arched structure and a canvas cover installed between them. One of our warehouse employees from the Czech Republic was on site and was in charge of all material movement. All the material, after being picked up in Vizovice, was prepared electronically for the Saint-Louis registration warehouse. From there, the warehouse worker took out the material in the standard fashion using the tablets we use in our Vizovice operation. This provided us with an overview of the material in stock both in Vizovice and on site. We were, thus, able to react with flexibility in the event that we were running low on materials.