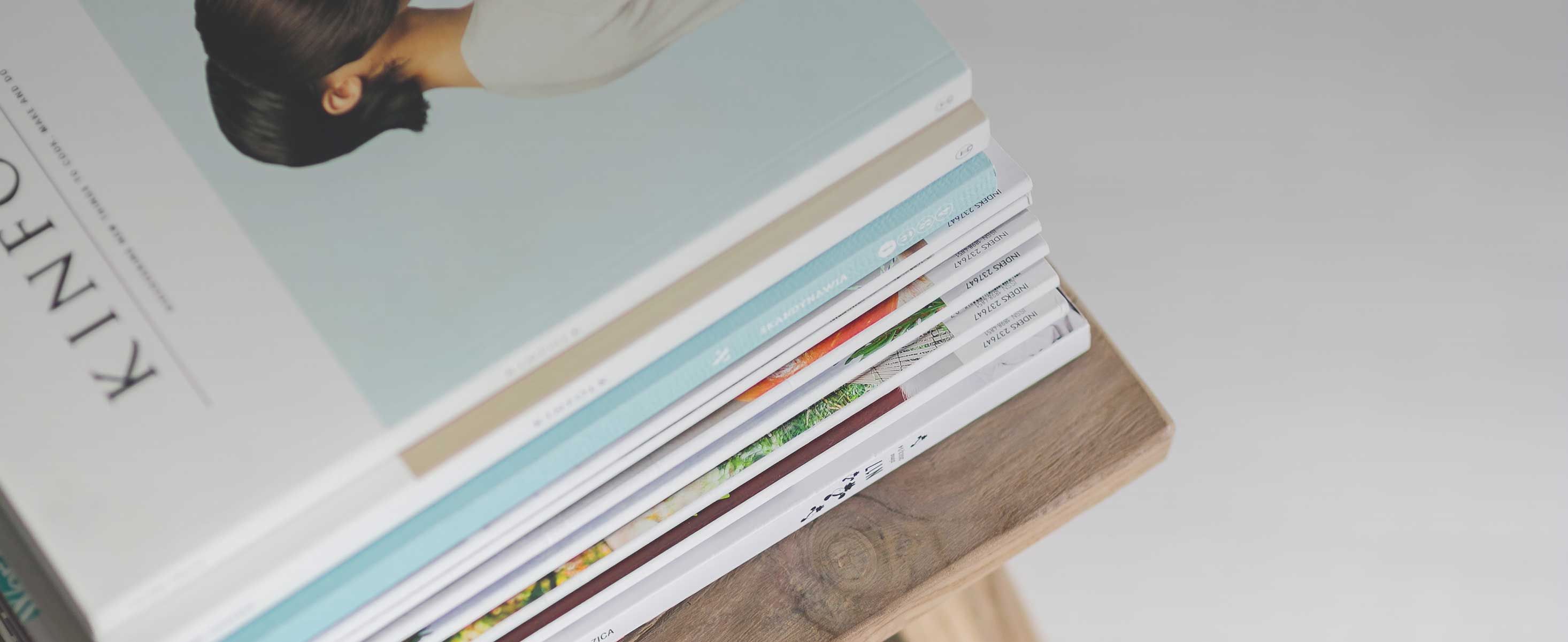
5 minute read
FACULTY’S INSIGHTS
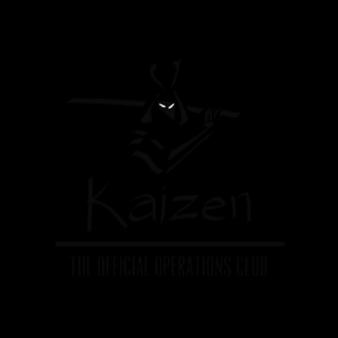
Dr. Rajan Kumar Gangadhari Faculty Associate, Department of Operations Management and IT IBS, Hyderabad.
Advertisement
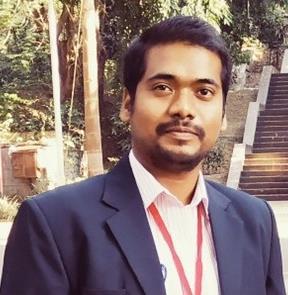
Covid-19, Evergreen incident and the global supply chains: Lessons for handling crisis in supply chains
According to a number of studies and research agency reports, the Covid-19 pandemic has a negative impact on more than 86% of supply chains. The process of controlling the flow of products, services, and information from suppliers to customers is known as supply chain management (SCM). It entails managing and coordinating all sourcing, procurement, conversion, and logistics management processes as well as coordinating internal information flows within a business. SCM aims to guarantee that the appropriate products are created at the appropriate time, cost, and location, and that the appropriate quantity is delivered. SCM also aims to improve the supply chain's overall efficiency in terms of cost, quality, and service. Demand management, sourcing, production planning, inventory management, transportation, warehousing, and logistics management are crucial components of SCM. Following the COVID-19 pandemic, the world was at a time of calm and rising demand. To meet the demands, the businesses were channelling their operations.
The operations and profitability were also impacted by the inventory, holding costs, and restrictions put in place by various nations. The Taiwanese Evergreen Marine Corporationoperated Ever Given ship was hit in the Suez Canal for 7 days in March 2021. Approximately 12% of global trade was lost as a result of the Suez Canal blockage, according to data from Lloyd's list, and daily trade worth more than $9 billion was being delayed. The Suez Canal, which links the Mediterranean Sea to the Red Sea and offers a direct route between Europe and Asia, is a crucial waterway for international trade. It shortens the distance travelled by cargo ships transporting goods between the two continents and avoids the time-consuming and hazardous trips around the southern tip of Africa. As a result, the Suez Canal is important to global supply chains, especially for sectors like manufacturing, shipping, and the oil and gas industry.
Due to these two unanticipated events, the world's supply chains have been significantly impacted over the past three years. Most organisations have established systems for risk management or mitigation. But unexpected and unavoidable events could happen to us. Supply chain management involves identifying potential risks and threats that could obstruct the flow of goods and services, assessing their likelihood and impact, creating and putting into practise strategies to mitigate or prevent those risks, continuously assessing risks and adjusting strategies as necessary, incorporating resilience and agility into the supply chain, using data and analytics to make informed decisions, and improving the overall effectiveness of the supply chain.
We merely aim to summarise some broad conclusions drawn from the published literature regarding the lessons to be learned from crisis supply chain management in this work. Recent catastrophes and unanticipated events in the international markets have taught us the value of having a tested continuity plan, increased visibility and transparency, strong relationships with suppliers, agility and flexibility, effective communication, digitalization, risk management, diversification, resilience and sustainability, and continuous learning and improvement in managing supply chains. Automation and data exchange systems are being used more frequently in manufacturing technology as a result of Industry 4.0. Manufacturers are utilising industry 4.0 technologies like cyber-physical systems (CPS), the internet of things (IoT), cloud computing, and cognitive computing to supplement human decision-making with decentralised technology. By adopting industry 4.0 systems, the benefits can be explored; however, the organisations may face challenges such as high inventory, resistance to change, difficulty with transformations, a lack of leadership, or poor performance.
However, organisations can gradually implement data-driven decision-making step by step, starting with one department within the organisation, implementing it for a few months, and observing the change in performance; if the change is positive, they can proceed with full-scale implementation. This is done keeping in mind the long-term benefits. These technologies may eventually have a big impact on COVID-19 activities.
This crisis demonstrates that regional systems are more likely than global supply chains to be strong and resilient. Localization is also necessary for the environmental supply chain to be sustainable. Local production can be used to quickly respond to local needs while using minimal energy and resources. For instance, during the COVID-19 pandemic, several "hot spots" manifested. More lives may be saved or the spread of positive cases may be slowed by ensuring essential supplies through more adaptable manufacturing and speedy distribution logistics to crisis areas, both of which are problems for social sustainability. Flexible manufacturing system technologies like robotics and additive manufacturing make it possible to localise production capacity. Prior to changing behaviour in response to the COVID-19 crisis, this action entails amicably resolving problems. As systems, particularly the market and governmental regulatory systems, begin to fail, organisations must change how they behave. Similar behavioural adjustments may promote sustainability. These insights can be used to lessen the crisis' effects and improve readiness for future disruptions.
The COVID-19 pandemic has brought to light the potential dangers associated with having global supply systems that only prioritise effectiveness. Implementing localization and redundant sourcing is one method to lower risk. This is crucial for remote communities that heavily rely on global supply chains for food security, like Pacific Island nations. In response to the COVID-19 disruptions, these communities have started to establish regional food markets, sharing programmes, and bartering systems. Food waste and pollution have decreased as a result of this localization. The COVID-19 crisis raised concerns about the sharing economy as well. For instance, during slowdowns and shutdowns, vehicles such as service or delivery vehicles that were not being used for their intended functions were repurposed to deliver necessities. Due to the excess capacity and availability during the crisis, one supply chain executive from a reputable international organisation claimed that they were able to use passenger and military aircraft to deliver goods internationally. Crowdsourcing may eventually become a standard method for logistics and delivery due to this adaptation to crisis needs. Public managers should therefore be aware of the effect they have on supply chains and develop laws that can help businesses come up with recovery strategies. By including international suppliers in the development of sustainability policies and initiatives for supply chains, governments should offer opportunities for learning. By doing this, social sustainability capabilities can be developed as a regular aspect of organisational operations as well as a means of responding to unforeseen crises
Supply chains have learned the value of having a resilient and adaptable system in place as a result of the COVID-19 pandemic. It emphasises the importance of having backup plans and a diverse pool of suppliers. Technology adoption for remote operations and better visibility has become essential. Collaboration and effective crisis communication are also essential. Additionally, the pandemic has highlighted the value of local production in lowering the possibility of global disruptions. Supply chain crisis management emphasises the value of readiness and risk assessment, prompt decision-making and adaptation to changing conditions, effective communication with stakeholders, backup plans and contingency measures, collaboration and coordination across the supply chain, as well as continuous monitoring and process improvement.
About the Author
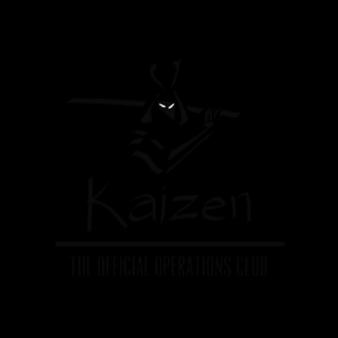
Dr. Rajan Kumar Gangadhari is an experienced safety engineer with a demonstrated history of working in the construction, theme park, and manufacturing industry. He is skilled in HSE Management Systems, Risk Management, Data Analytics, HAZOP, Audits, Assessments, and Emergency management.