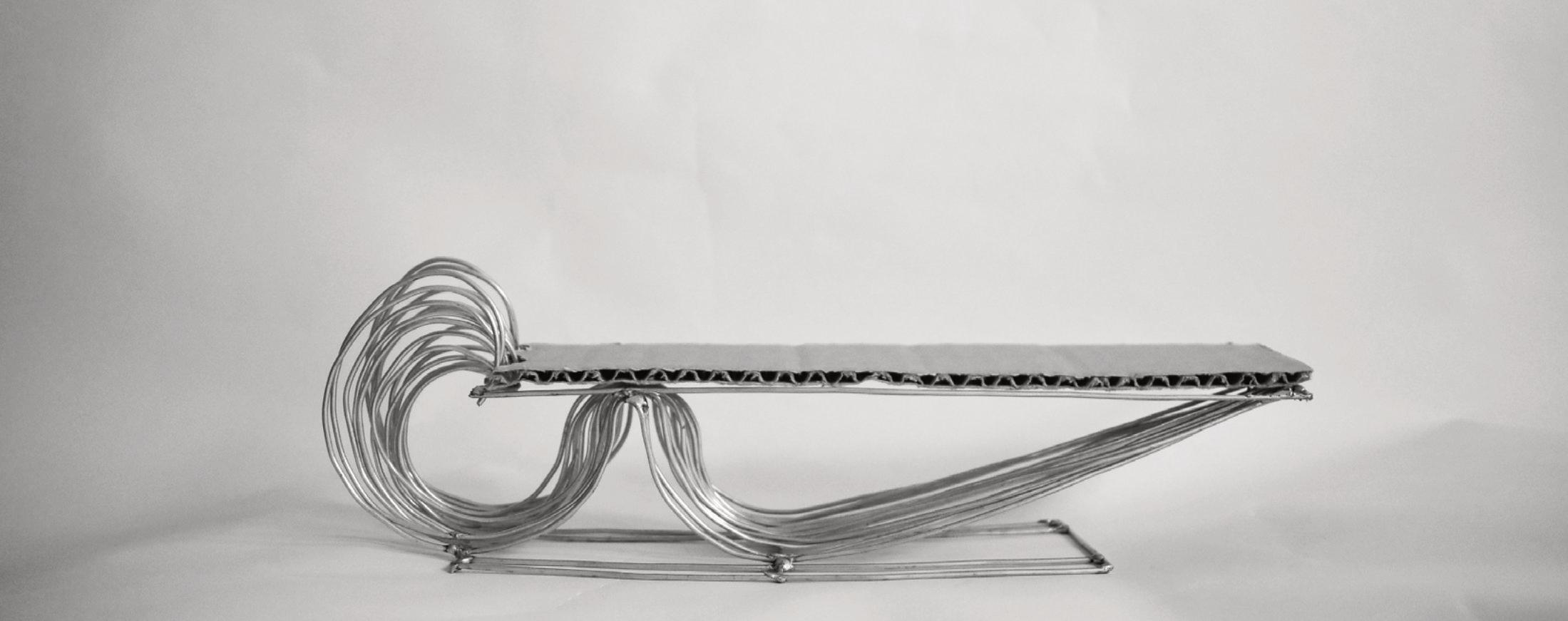






DB SCHENKER CHANDELIER
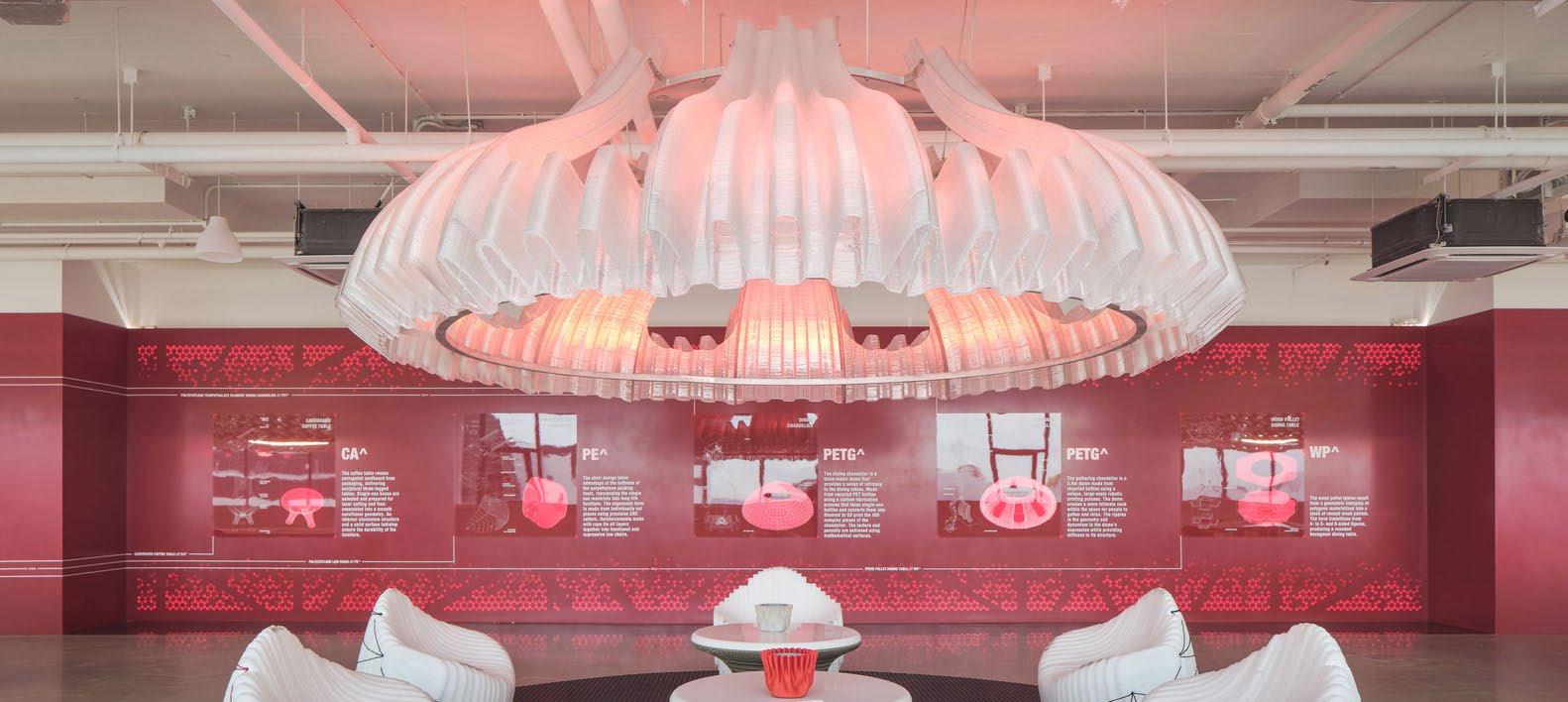
An upcycled plastic bottles chandelier made for logistics company DB Schenker
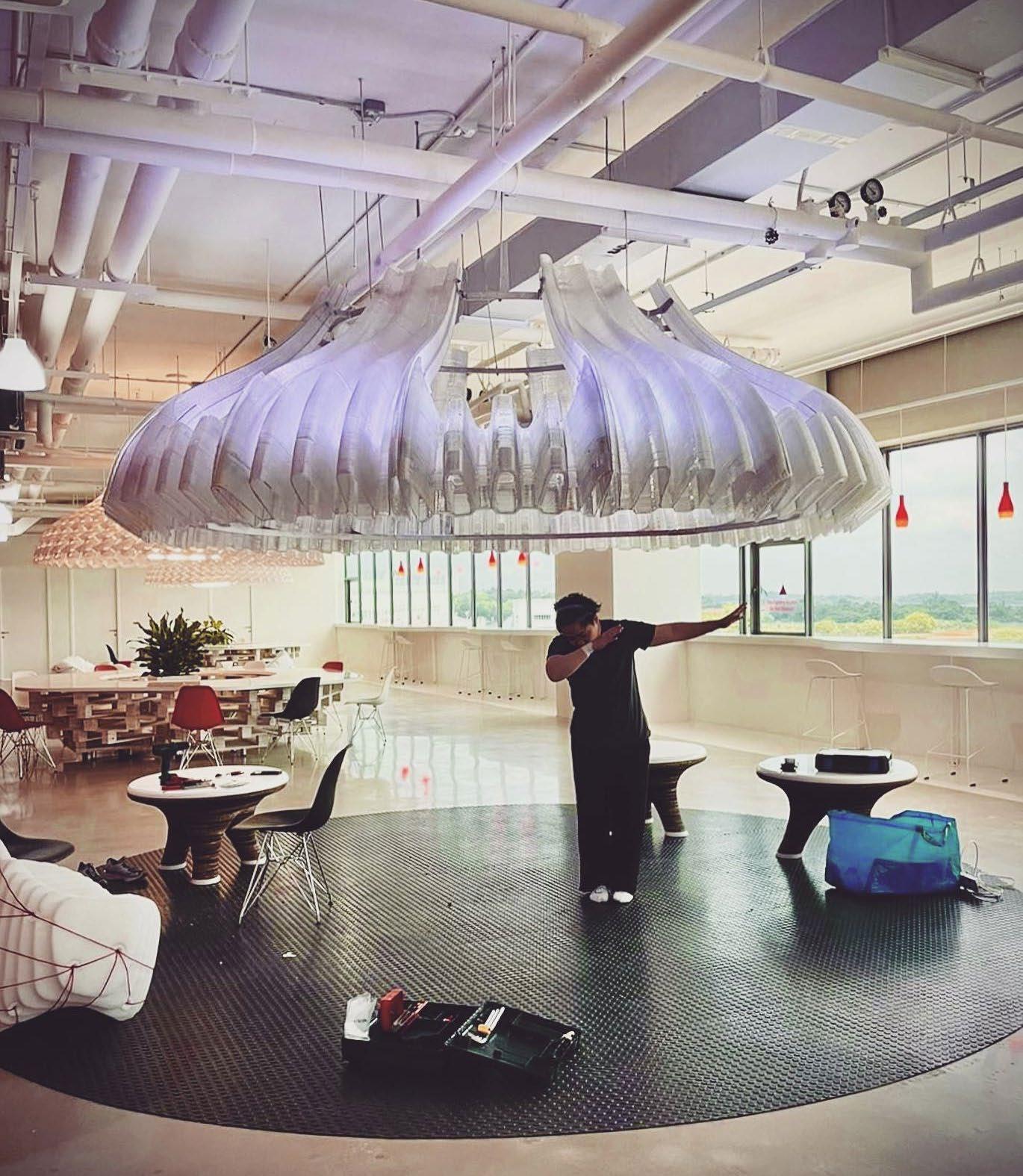
Year: 2018 - 2021
Location: AIRLAB SUTD
Role in Project: Computational Designer, Fabricator
Involvement: Toolpath generation, 3D printing calibration, robot operations
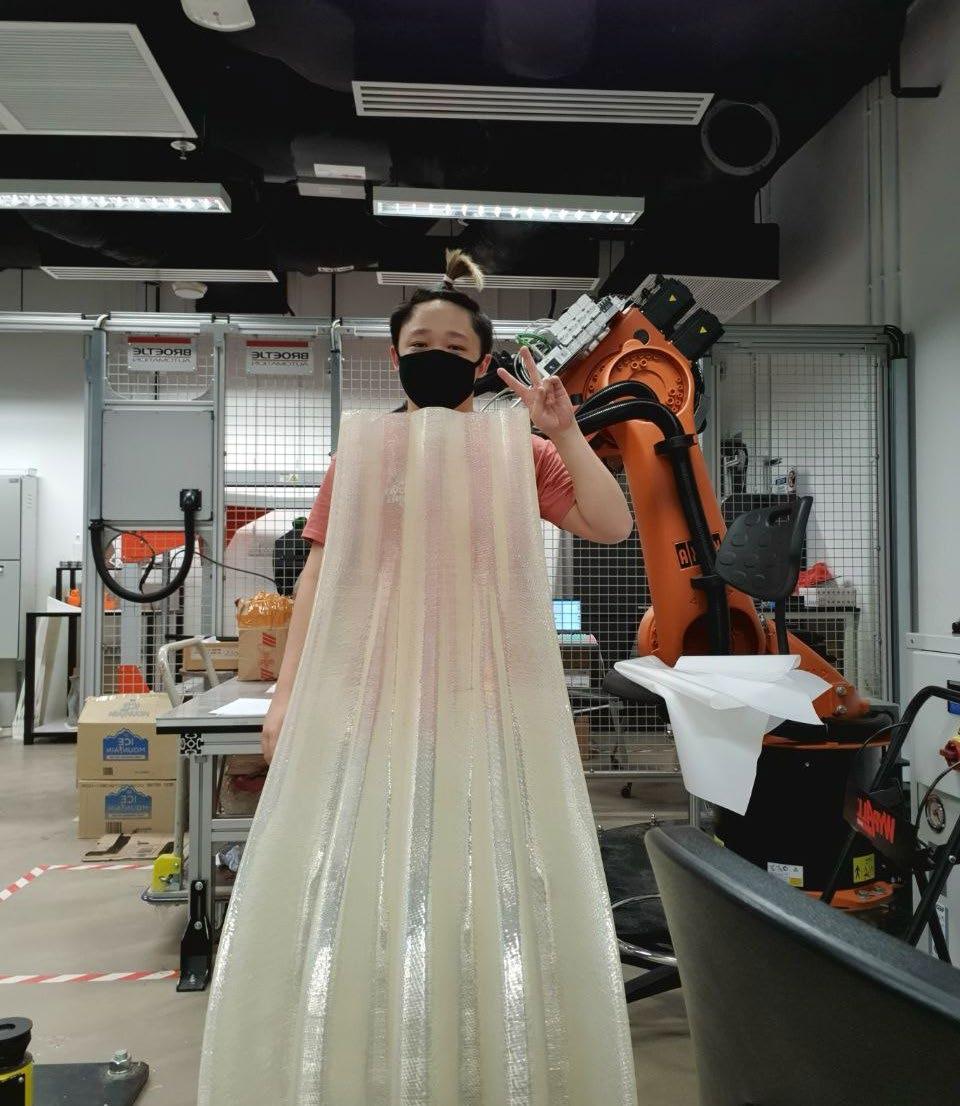
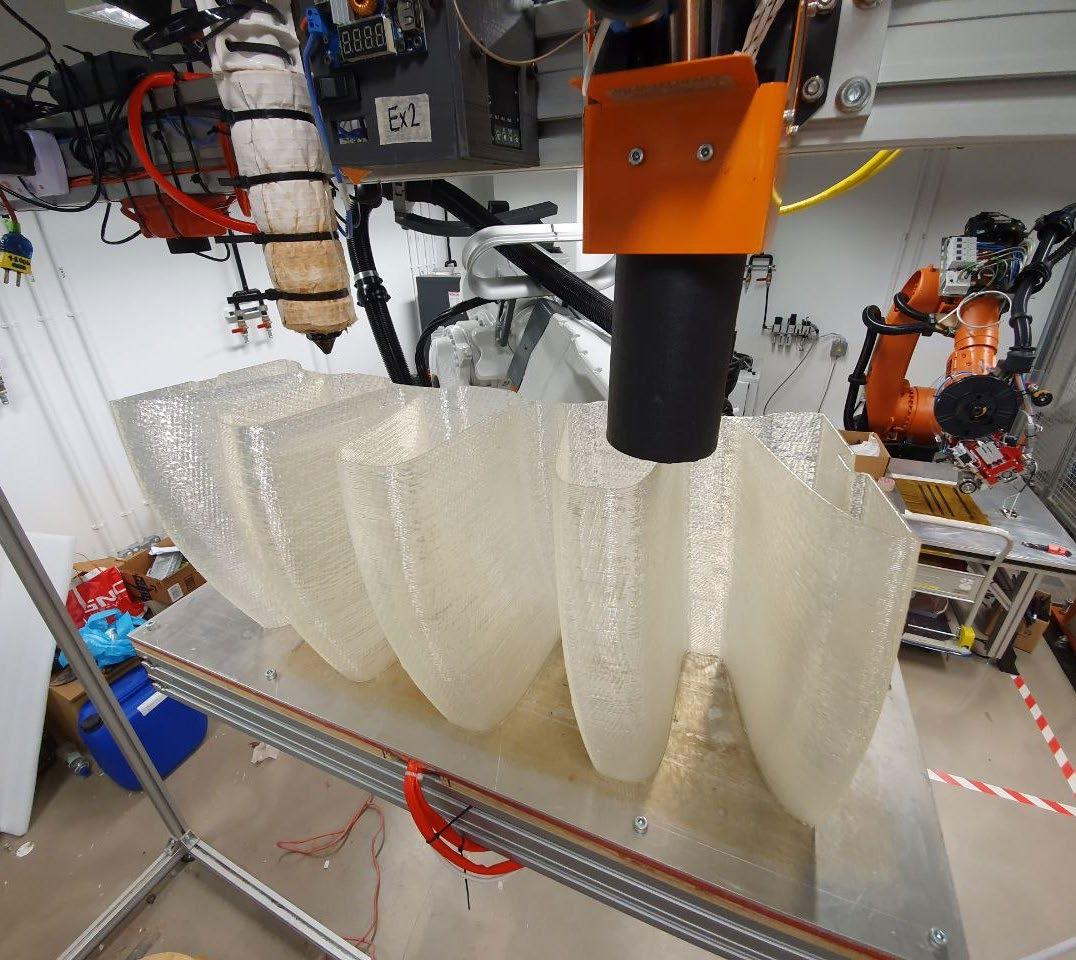
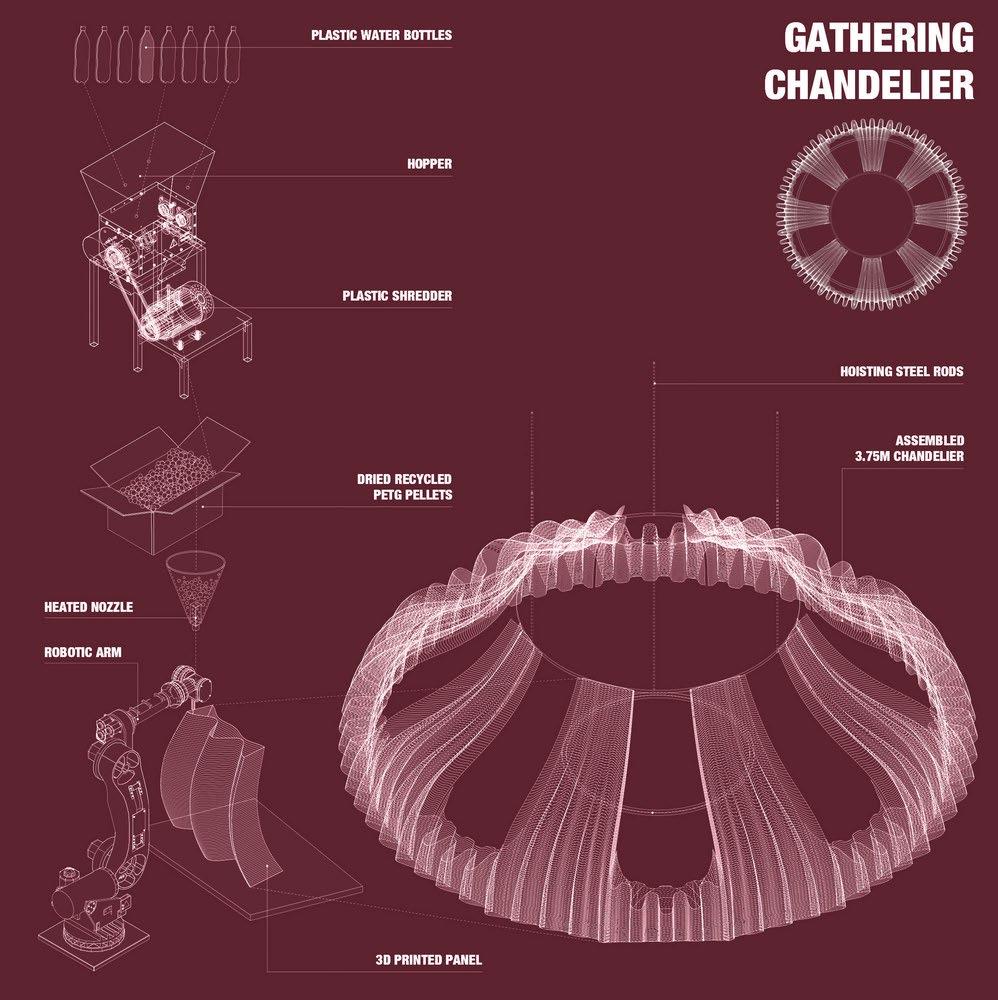
The Upcycling Hub project was launched in 2018 with the aim of promoting the concept of circularity in the logistics and supply chain industry among users and visitors. The hub was created to demonstrate the potential of waste and encourage a reevaluation of waste throughout all stages of the supply chain, from design to production, consumption, and beyond, through innovative 3D printing techniques. This creates a space to reassess our understanding of waste throughout all supply chain stages from design, production, and consumption through new 3D printing processes.
My involvement in this project focused mainly on resolving the design for printing, toolpath generation, printing calibration, and overall robot operations. The calibration took 3 months, and I tested different print settings, including layer height, print speed, print temperature, bed adhesion etc. Having the chance to experiment with a printer with so many more degrees of freedom compared to normal desktop printers was a very unique experience. At the end of the 3 months, had managed to program and therefore automate the printing for all 16 pieces of the chandlier.
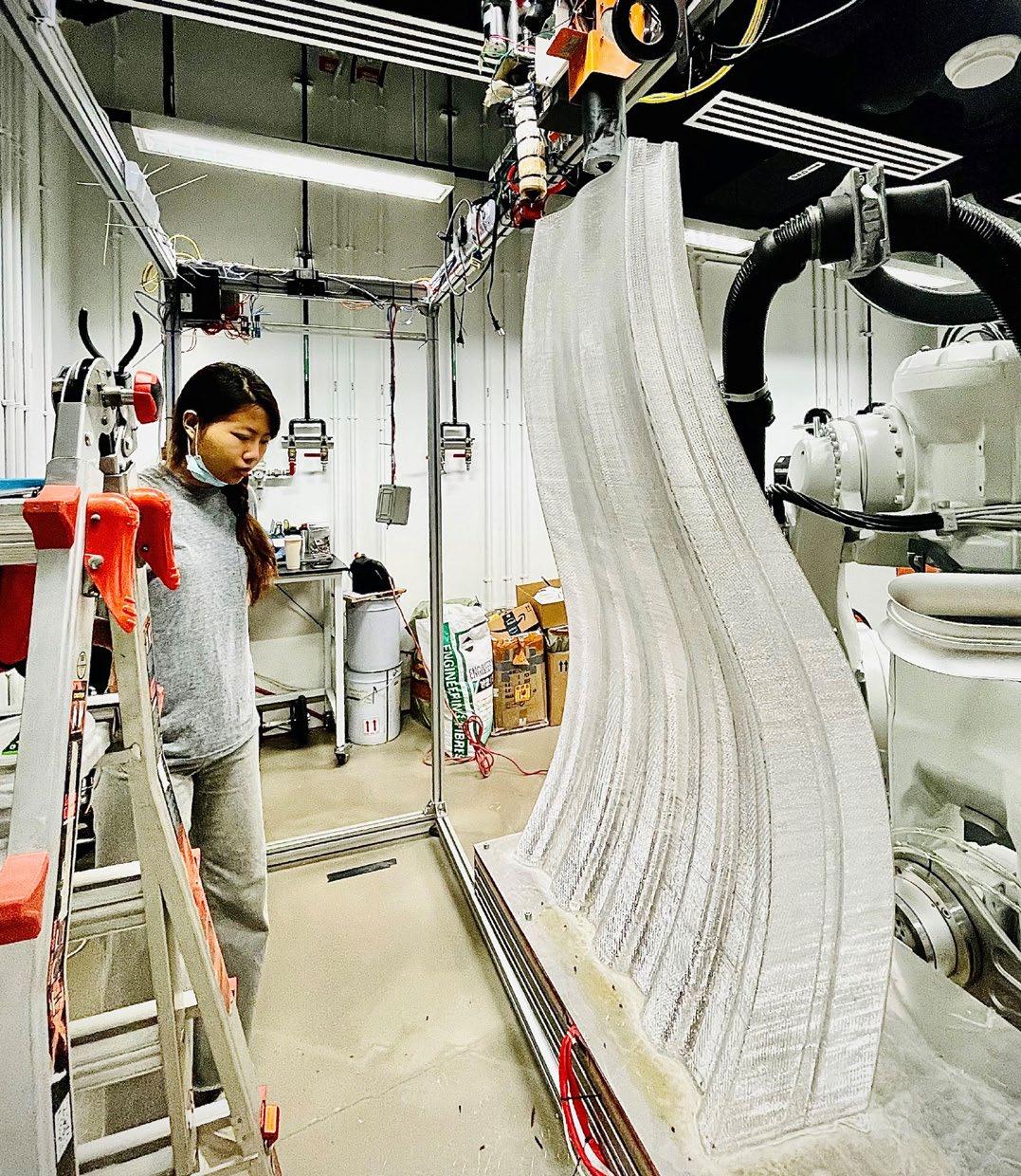
BIOMIMETIC CHITOSANALGINATE THREADING
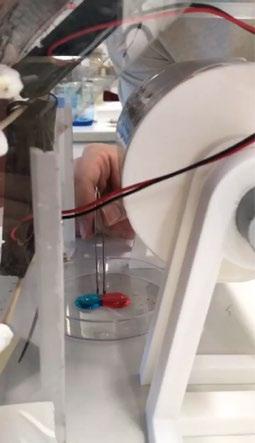
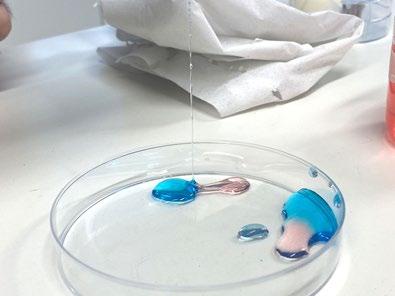
An exploration into biomimetic material properties and its production methods
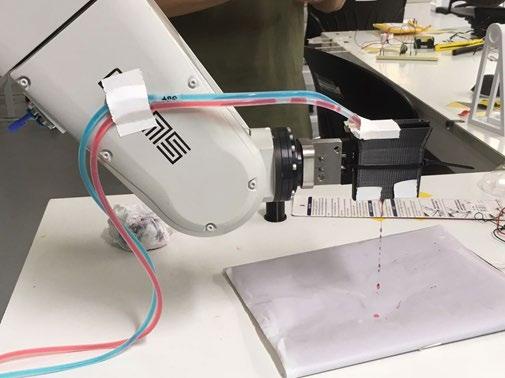
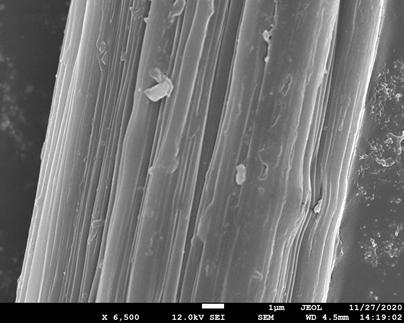
Year: 2020
Location: SUTD
Role in Project: Team Member
Involvement: Research, Fabrication
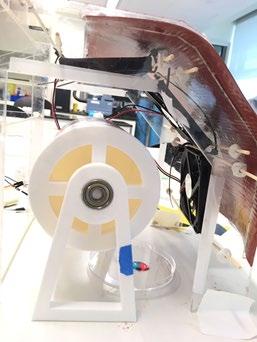
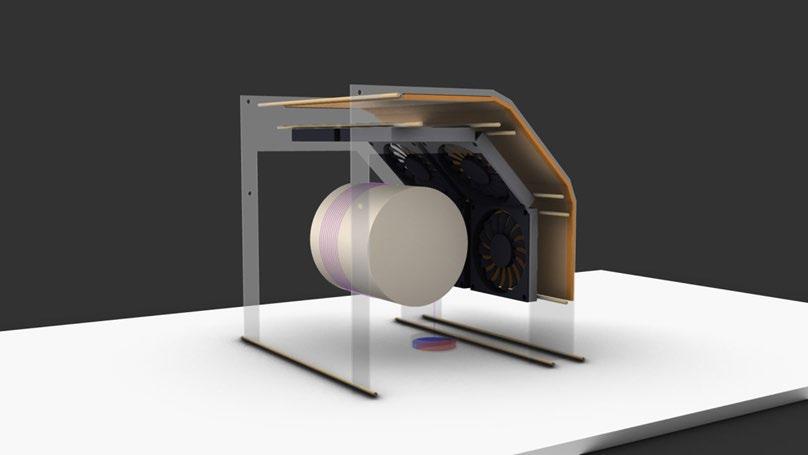
In this work, Sodium Alginate and Chitosan are precipitated to form threads that are biodegradable and have chemical and mechanical properties that are different from normal threads. Prior research in the field has shown that chitosan cations(+) and alginate anions(-) can spontaneously form polyelectrolyte complexes (PECs) when they are mixed in an aqueous solution. This was done in hopes of finding a creative and improved solution for existing products, such as gauze as chitin and alginate has antimicrobial properties.
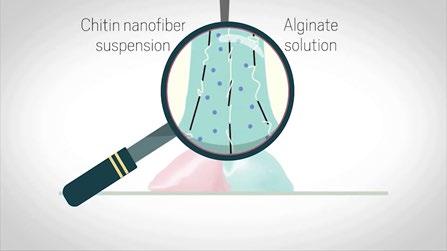
Findings of thread properties include strength (tensile, fatigue, yield), toughness and anti-microbial. The threads are formed by extracting and pulling a point on the surface where chitosan solution and sodium alginate solution meet to create a fibrous line. This would later then be scaled up in volume using a mass production method. After production, the Chitosan-Sodium Alginate threads could yield infinite possibilities. The original idea was to use the threads for printable objects by laying them out using a heated moving bed, which would allow for printing of anti-microbial gauze. However as that had failed, the result we achieved was a way to spool the thread, which at the time was still at the forefront of this technology.
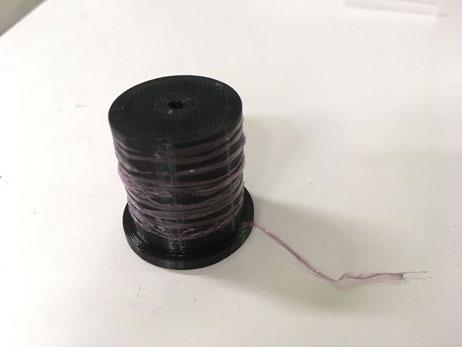
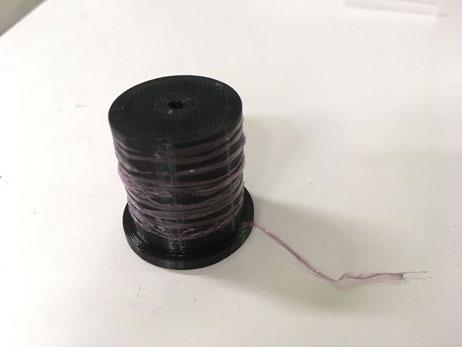
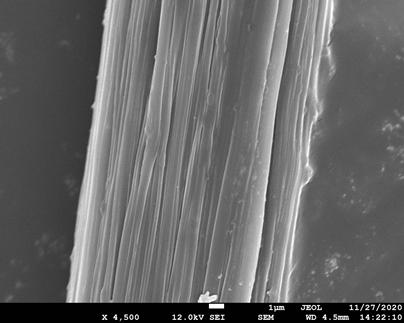
LAMPARDA CHANDELIER
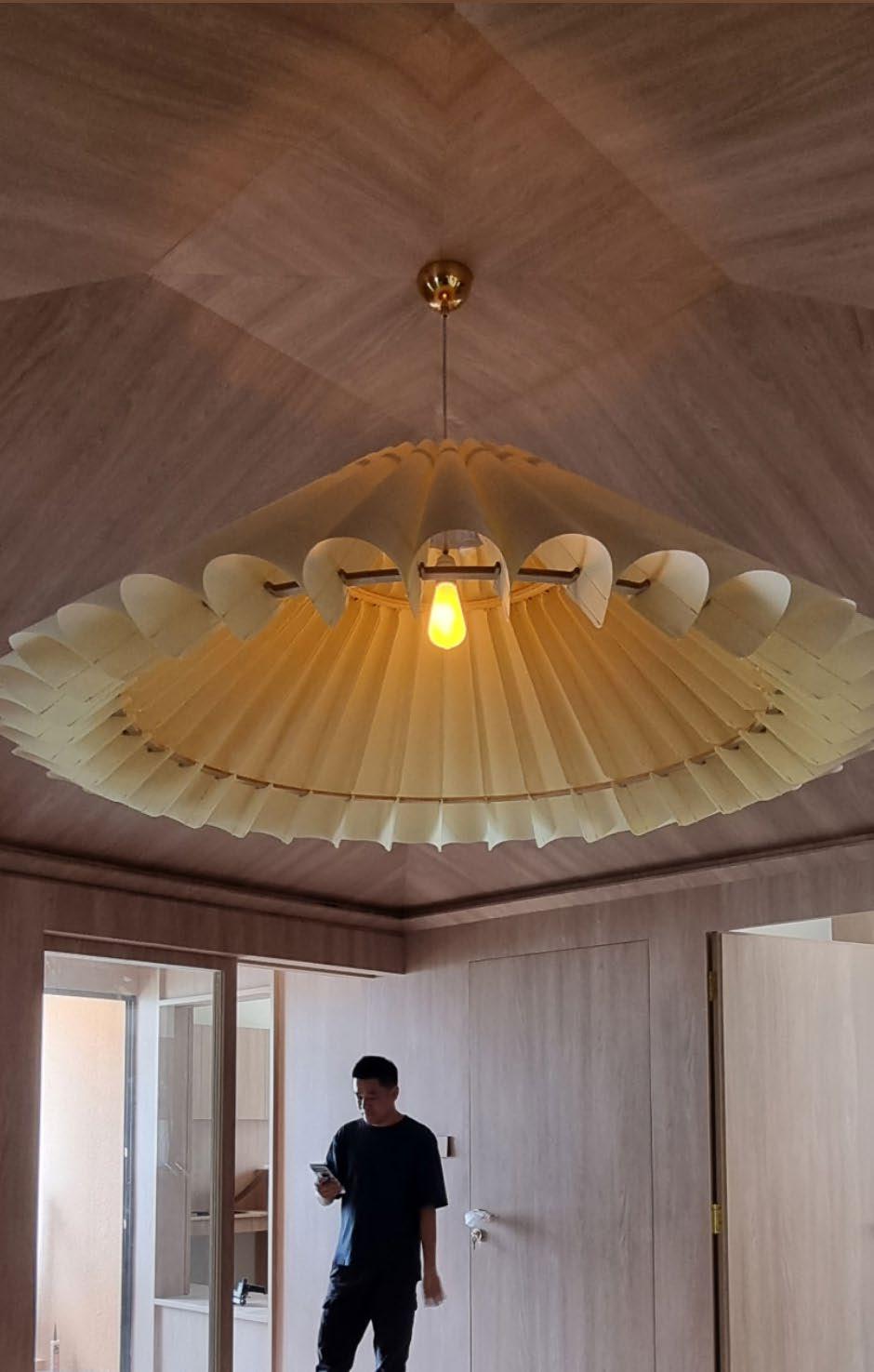

A furniture centerpiece for a family room
Year: 2022
Location: Superstructure Singapore
Role in Project: Computational Designer, Fabricator
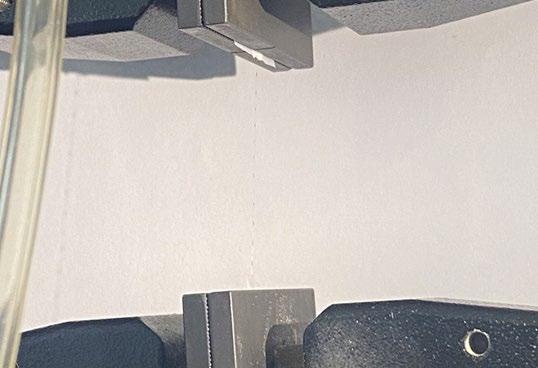
Involvement: Conceptualised, Designed, Resolved Fabrication Details, Installation
Lamparda started as a client request to create a centerpiece for the family room. I was tasked to design this lamp based on the room, which had most of its furniture and walls cladded with wood veneer. Below the lamp would also be a cozy sitting area for the family to gather. Therefore, my design aimed to create a comforting canopy using natural materials to give a sense of shelter as they sat under the lamp. The umbrella like shape would also fit with the slanted ceiling and therefore illuminate the space evenly.
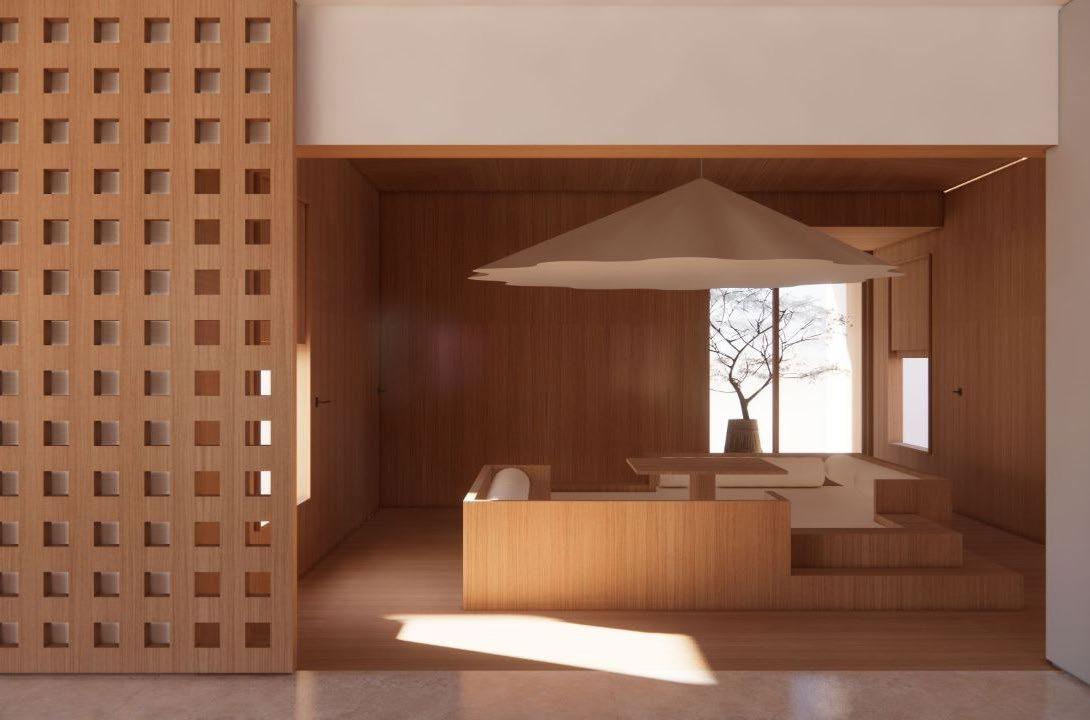
I also had to solve for the construction details as we were requested to not use any glue or adhesive. I spent about 1 month testing different connection methods such as using paper tabs to join the petals to each other, using eyelets, and then finally settled on sewing the petals together for a more discreet look that tied into the natural feel. The paper used was a thick 230gsm fibrous paper with a yellowish tint, which when illuminated gave a soft warm natural glow. The paper was then held up by a piece of glass and 2 wooden birch rings, which was held in place by tabs cut out on the paper itself. used a laser cutter, a zund cutter and a 3 axis CNC machine to achieve the final result.
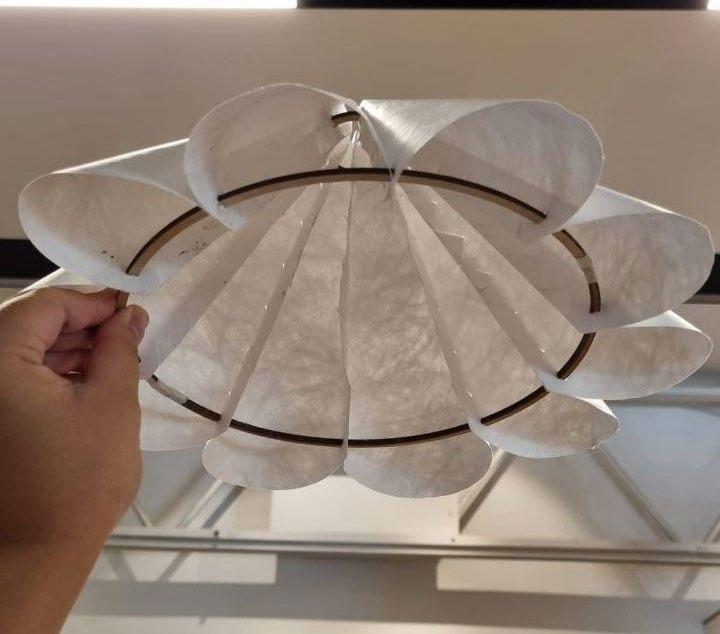
Testing different distilled water to chitosan powder ratios to determine which percentage gives the desired viscosity.
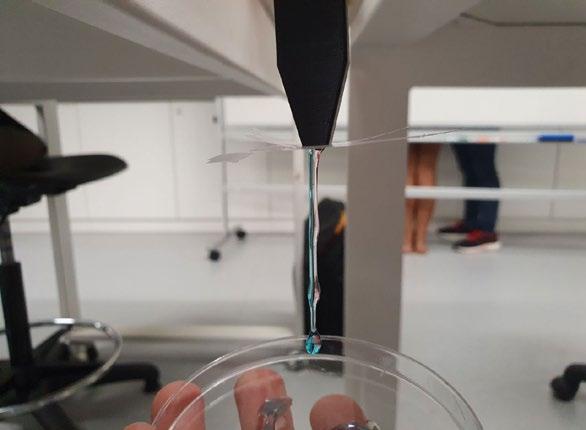
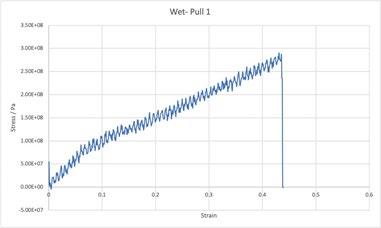
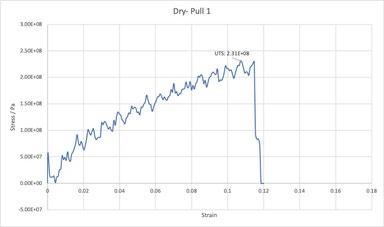
As
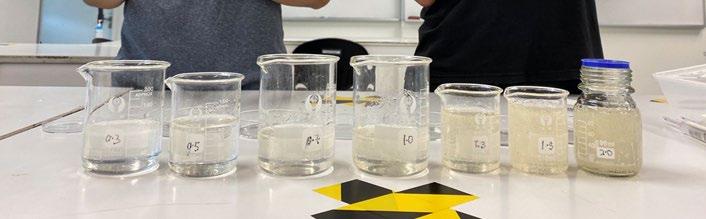
BREATHING ARCHITECTURE
An exploration into auxetic patterns and their behaviours
Year: 2021
Location: SUTD
Role in Project: Team Member
Involvement: Computation, Fabrication, Research
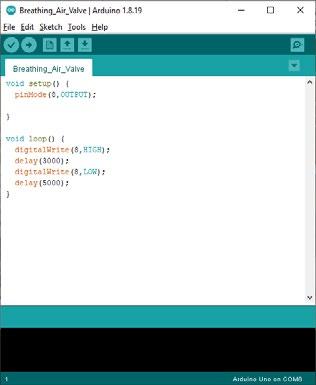
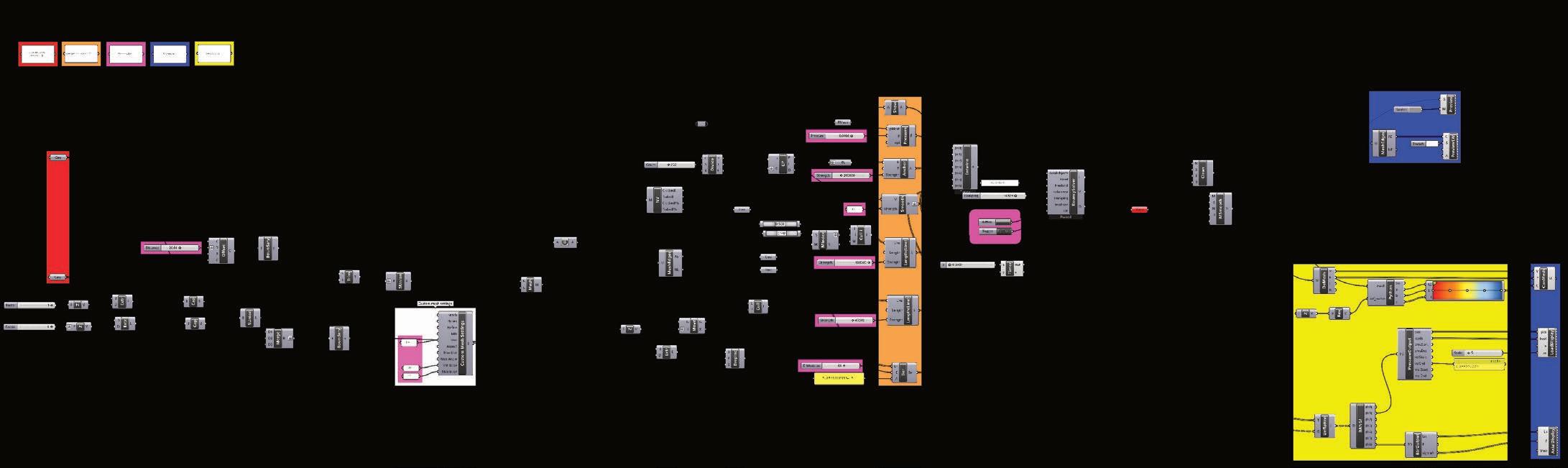
Our inspiration stems from the Nike’s 2016 additions to its Free footwear family. The pattern on the mid-soles of the shoe offers the runner multi-directional flexibility; expanding and contracting based on the force exerted by the runner’s foot. We thus wanted to explore other patterns that offer similar qualities and investigate the tolerance of expansion in response to a pneumatic inflation. We hypothesize possible uses in architecture in the form of dynamic facade or a shell structure.
We thus wanted to explore other patterns that offer similar qualities and investigate the tolerance of expansion in response to a pneumatic inflation. We hypothesize possible uses in architecture in the form of dynamic facade or a shell structure that can respond to environmental conditions.
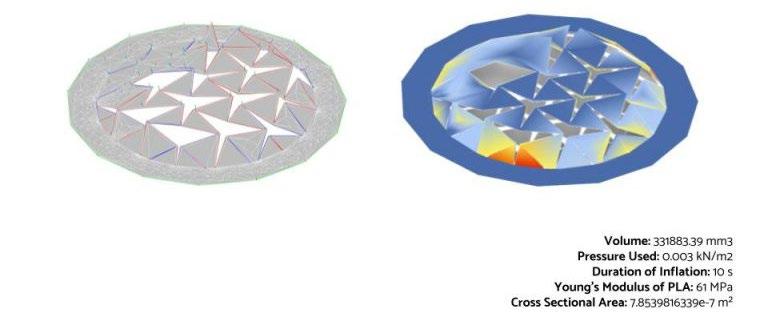
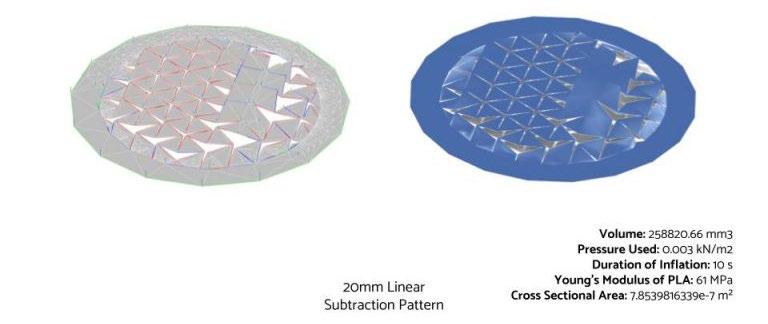
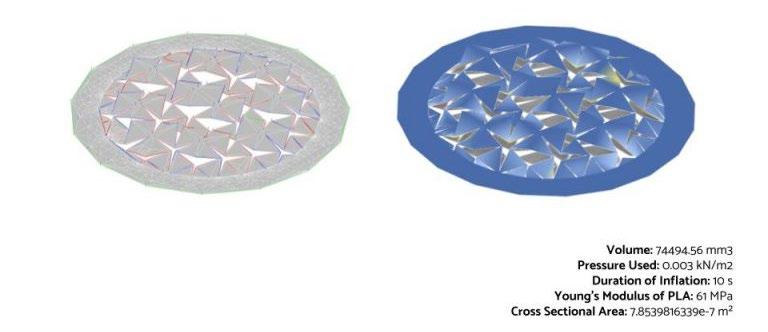

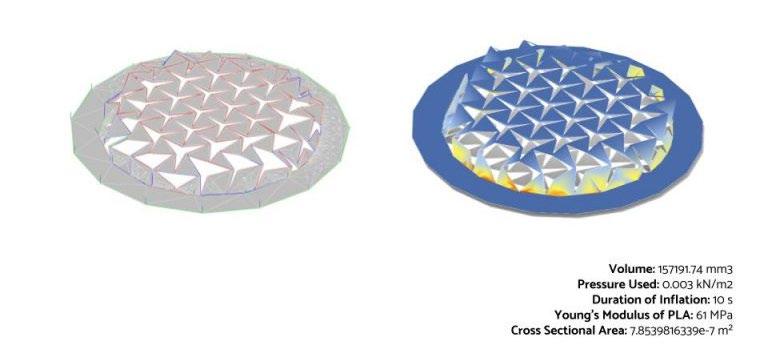

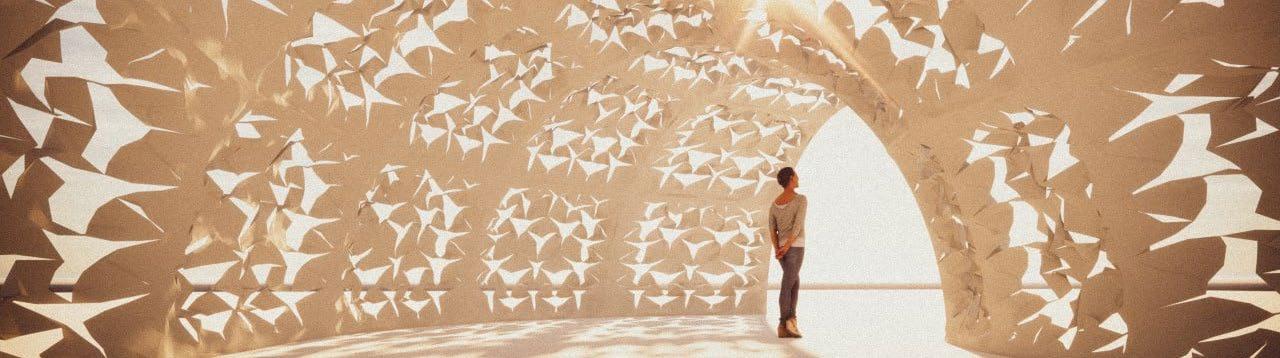
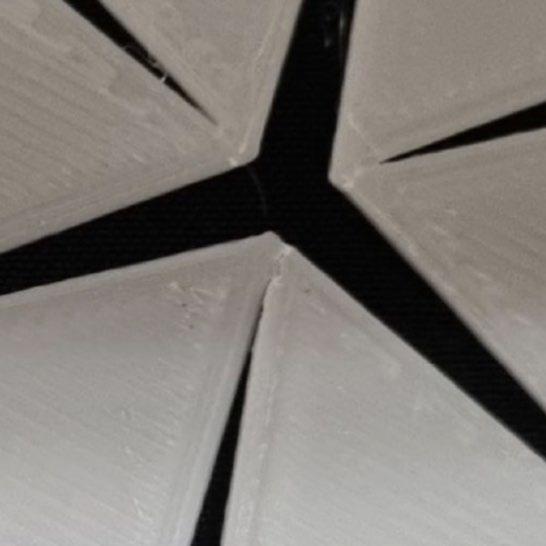
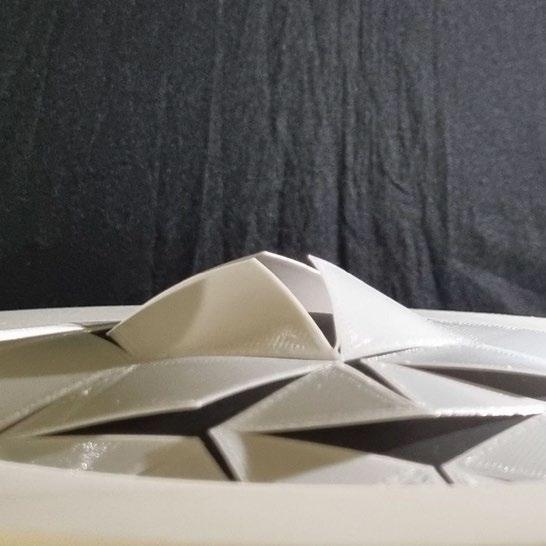
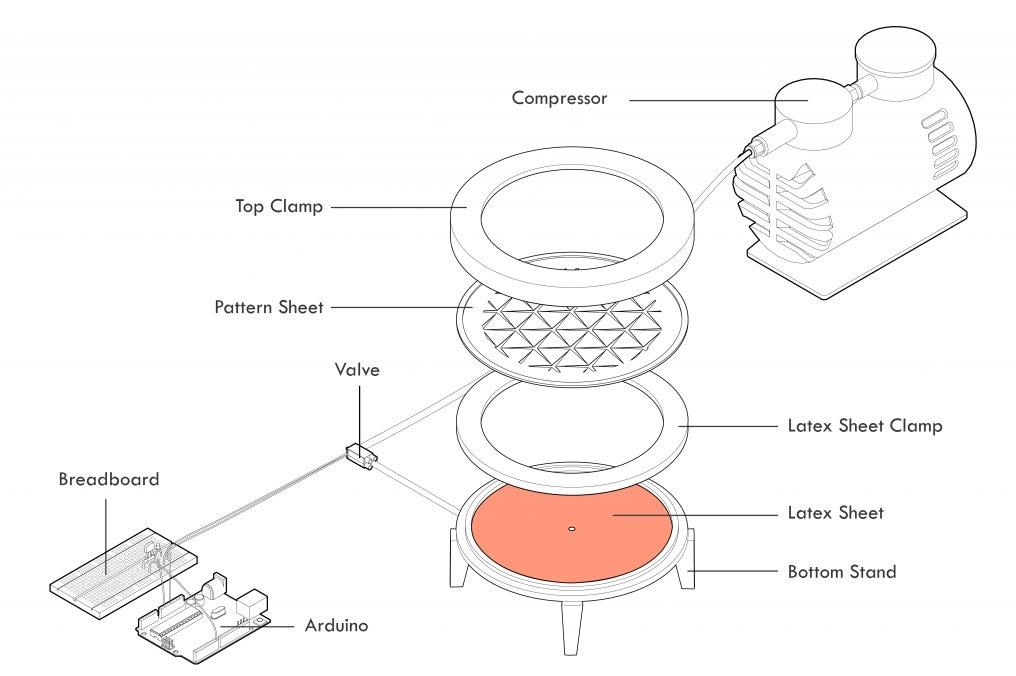
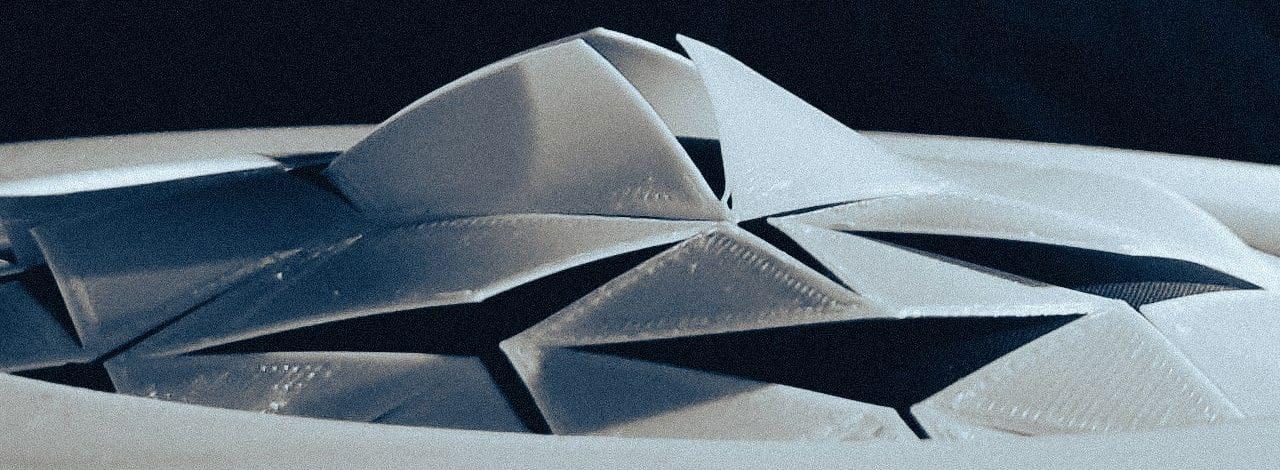
The digital setup aims to madel the experiment such that results obtained digitally are as accurate to the results obtained from the physical setup. Digitally, we were also able to vary the amount of pressure and the starting form of the sheet.
Instead of creating a simulation for the auxetic structure with digital tools we decided to start from experimenting physically. We used a simple set up using an arduino to inflate the latex sheet for a set duration, allowing us to control the volume.
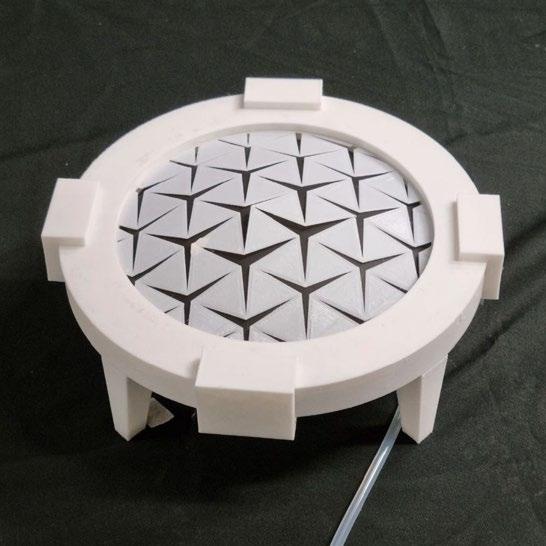
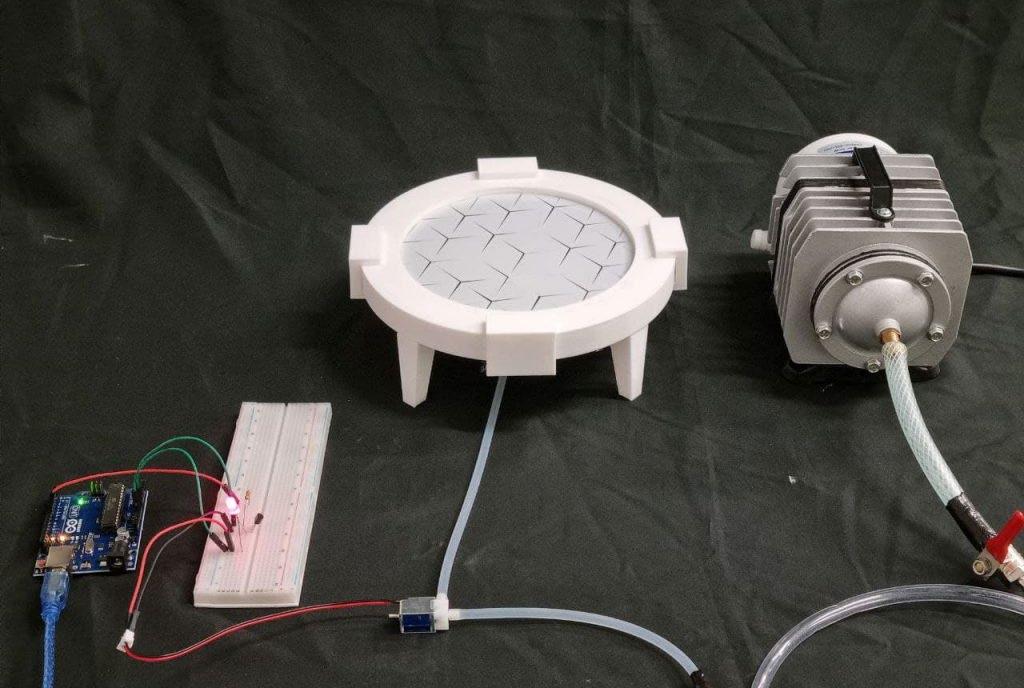
After testing multiple different designs, we found that by subtracting the cutouts in a concentric pattern, it gave more interesting expansion forms. The final facade explored the ring subtraction in further detail, by varying the radius of the ring, as well as selecting segments of the ring. Using the two rules, we created simple renders to showcase their application in the real world.
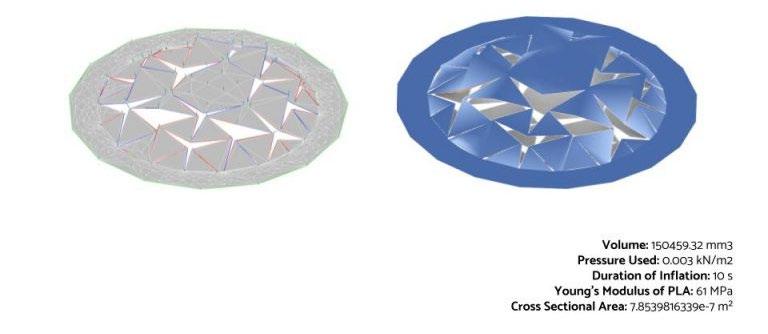
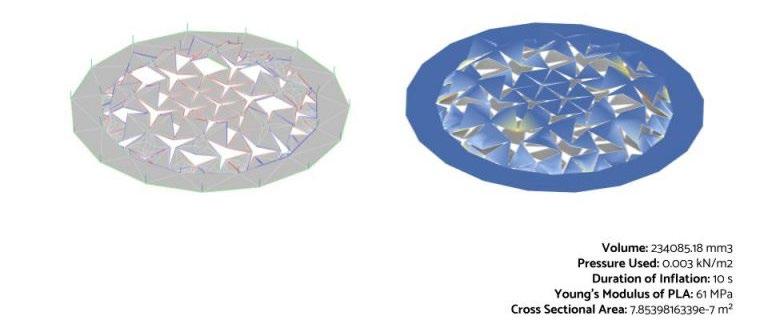
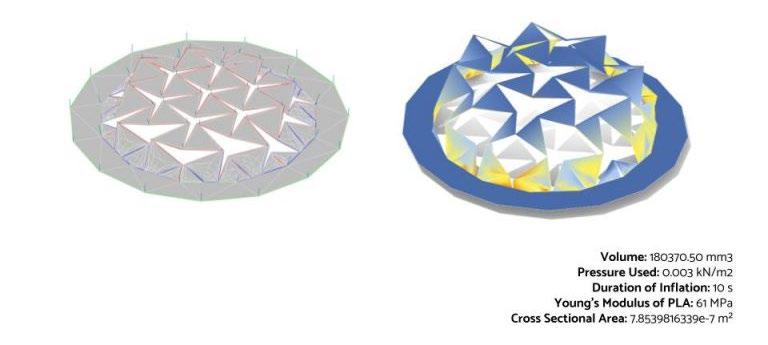
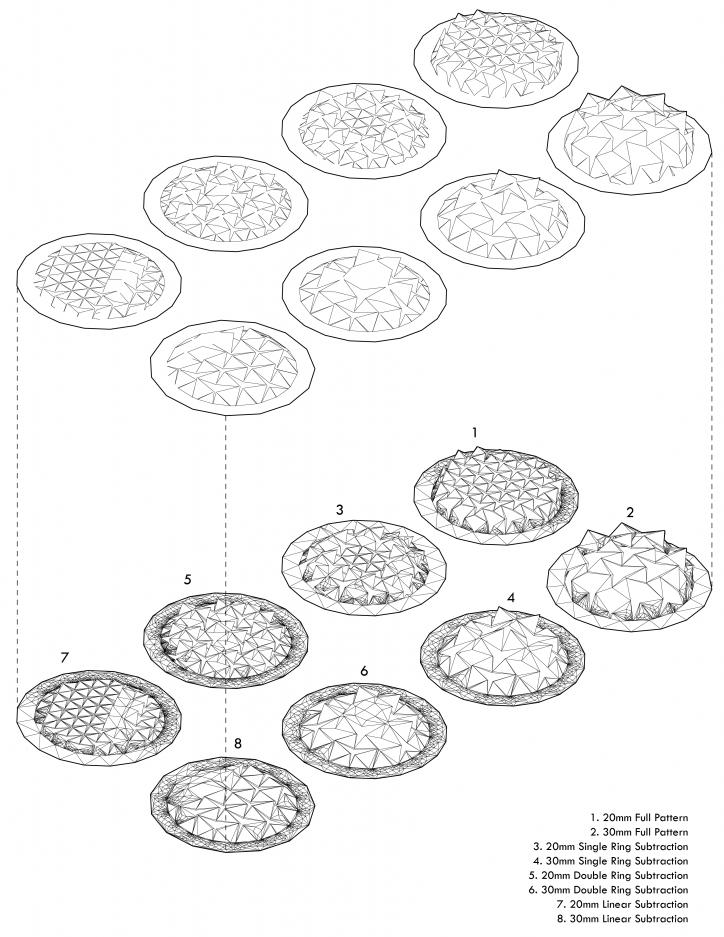
We then measured the maximum displacement of the patterns aand checked for wear and tear within each pattern to determine maximum inflation volume.
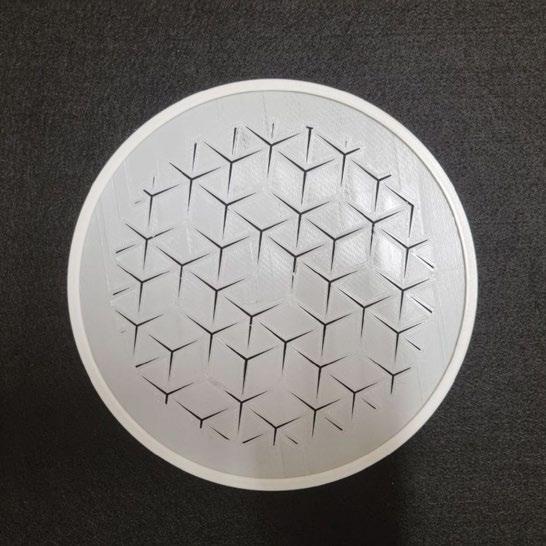