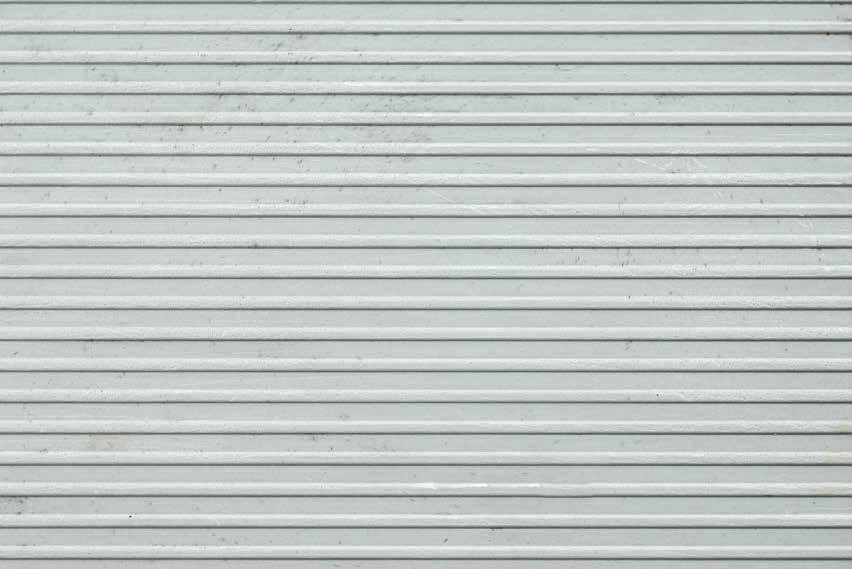
2 minute read
Grain drying technology aims to increase profitability and efficiency

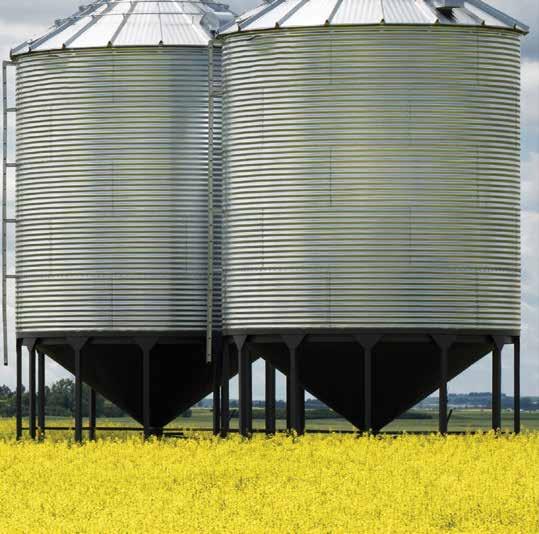
Grain drying technology aims to increase PROFITABILITY EFFICIENCY
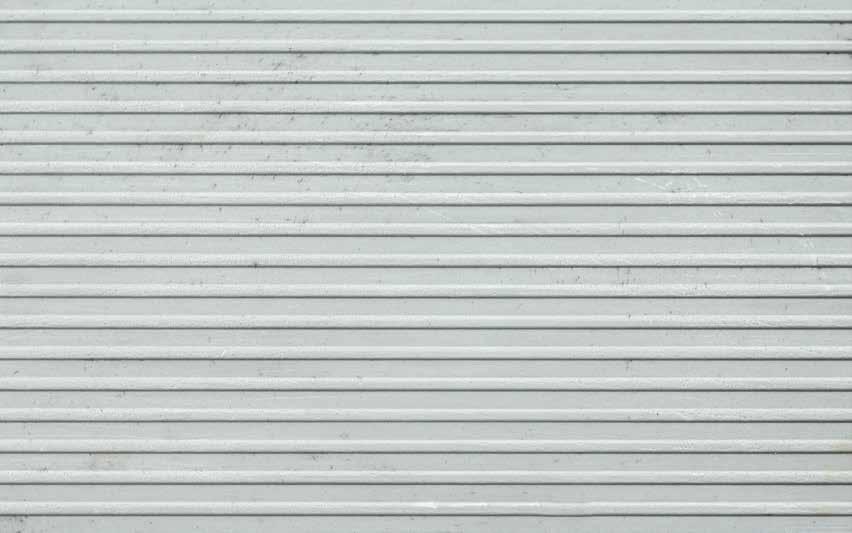
Unexpected weather across Western Canada illustrates how producers are at the mercy of Mother Nature when getting their crop in the bin. This applied research project is close to concluding whether it’s possible to increase profitability on today’s technology-based grain farming operations.
Together, Alberta Innovates, Top Grade Ag, Lakeland’s crop research team and the Student-Managed Farm – Powered by New Holland (SMF) crop unit are developing in-bin sensormediated drying procedures to increase profitability and efficiency. “As part of the research project the SMF students dried 8,000 bushels of wheat this fall to field test calibration factors for the Top-Grade Ag in bin drying system. This is the third year that SMF has used in-bin drying to condition their grain, but this year the Top-Grade Ag technology took the guess work out of the drying time. Being able to effectively target a moisture content not only saved the students the frustration of guessing when the grain was dry, but also maximized their profitability by not overdying the grain,” says Kyle Kipps, instructor The Calibration of In-bin Drying Project involves real-time, farmlevel monitoring of a sensor-based in-bin drying system using the SMF. The system could help producers determine when grain will dry rather than estimating when it will be. Sensors in the drying bin capture humidity, temperature and pressure data to model water removal, according to Graham Stuparyk, a secondyear crop technology student and a member of the SMF crop unit’s analysis team.
Stuparyk’s responsibility was to organize the grain’s movement from one bin to another, then take moisture samples for the study so that they could calibrate how much moisture was leaving the grain. “By doing this, we could calibrate the system to measure moisture levels properly. I also entered the data into the website.”
The data entered in the website goes to software that calculates water removal based on the moisture levels you started with and the bin's drying conditions. Possible results to industry could provide producers with a low-cost option to managing crop quality while utilizing existing grain storage infrastructure. This new technology will turn any aeration bin into a “built for purpose” grain drying system at a fraction of a stand-alone grain dryer cost. The benefit of harvesting early is warmer ambient temperatures which result in much lower grain drying costs and energy usage. Ryan Lutz, Lakeland’s agriculture technician, who helped install the systems in the college’s grain bin, says, “It was my first time working with this kind of tech, and I didn't know what to expect. I’m impressed. Before this year, we were just using construction heaters and just blowing hot air in the bin. The students put in tons of extra labour, flipping the bins, turning the grain over so they didn't get hot spots and so they knew where the moisture was at.”
This project, which began in April 2020, wrapped up in March 2021.
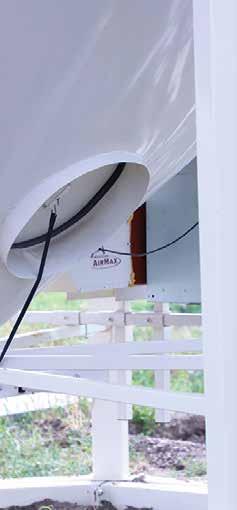
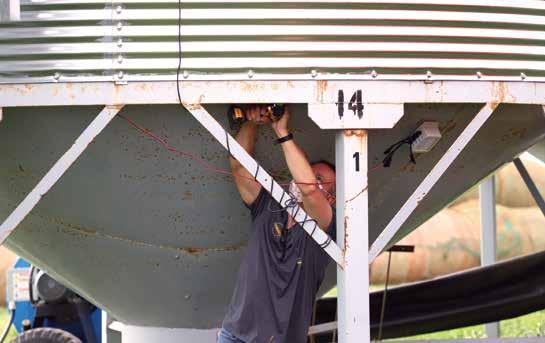