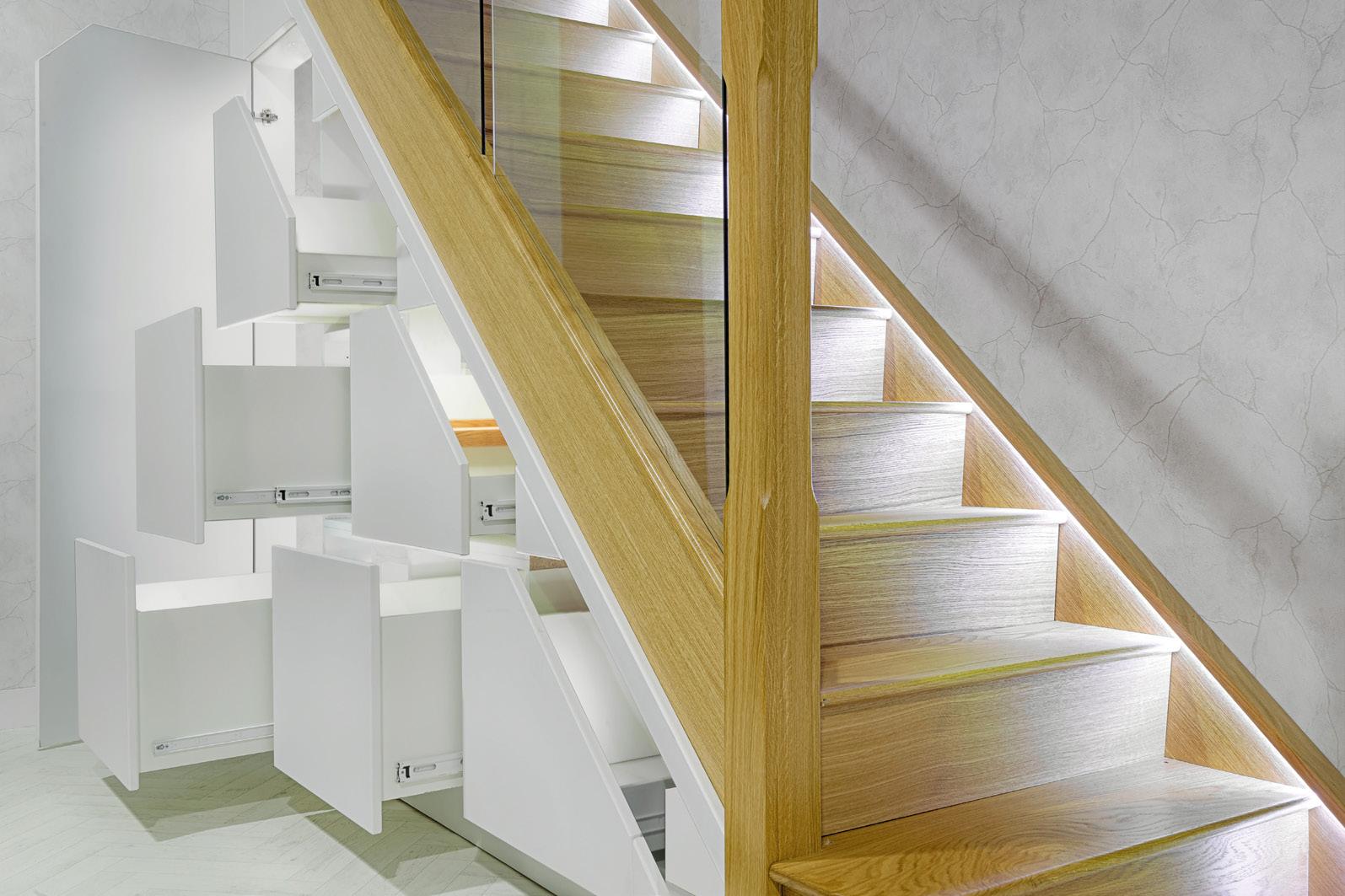
4 minute read
Creating Bespoke and Revolutionary Storage Solutions for Your Home
By Emily Walker & Joel Newman
Photography by: DH Photography
Advertisement
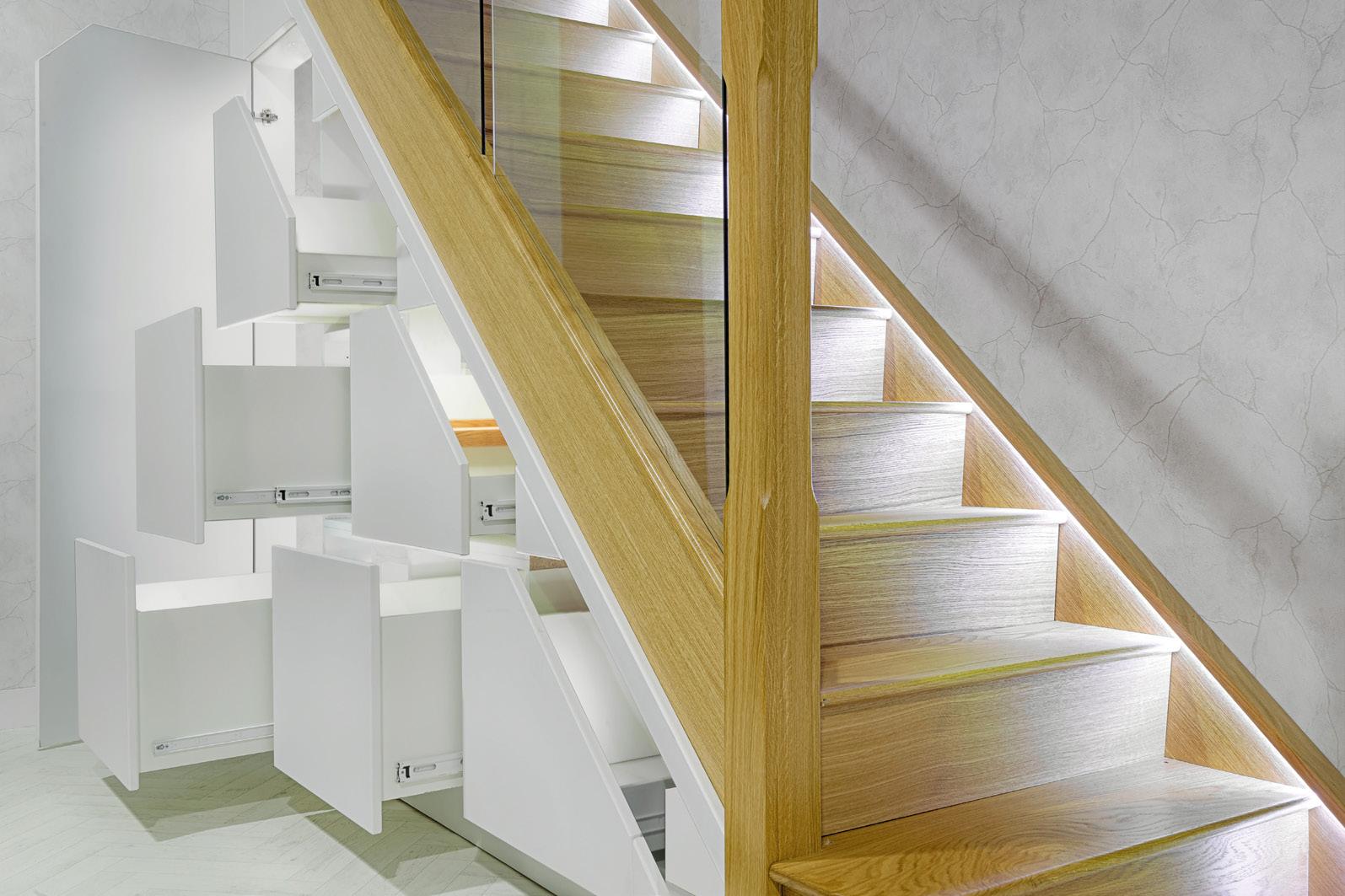
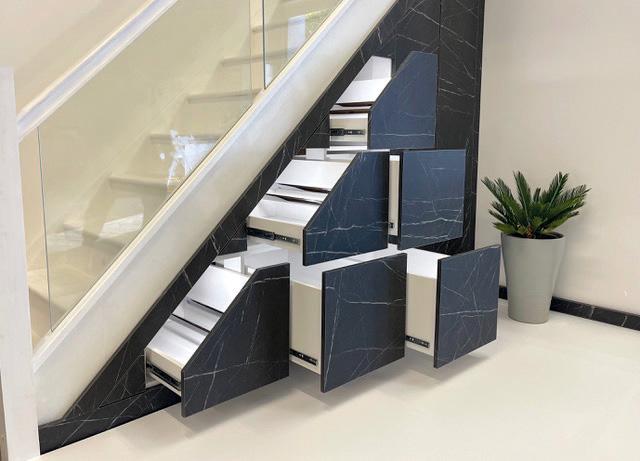
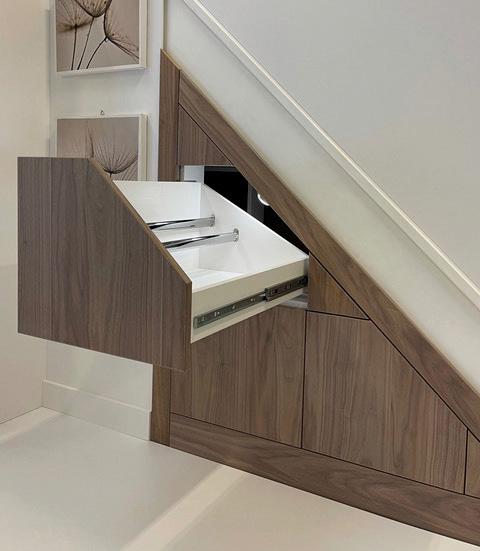
The space under the stairs is statistically the most underutilised place in most houses. In some houses it is simply boxed off, in others it is a dumping ground for children’s toys, shoes and jackets, it usually lacks structure and nearly everything ends up on the floor.
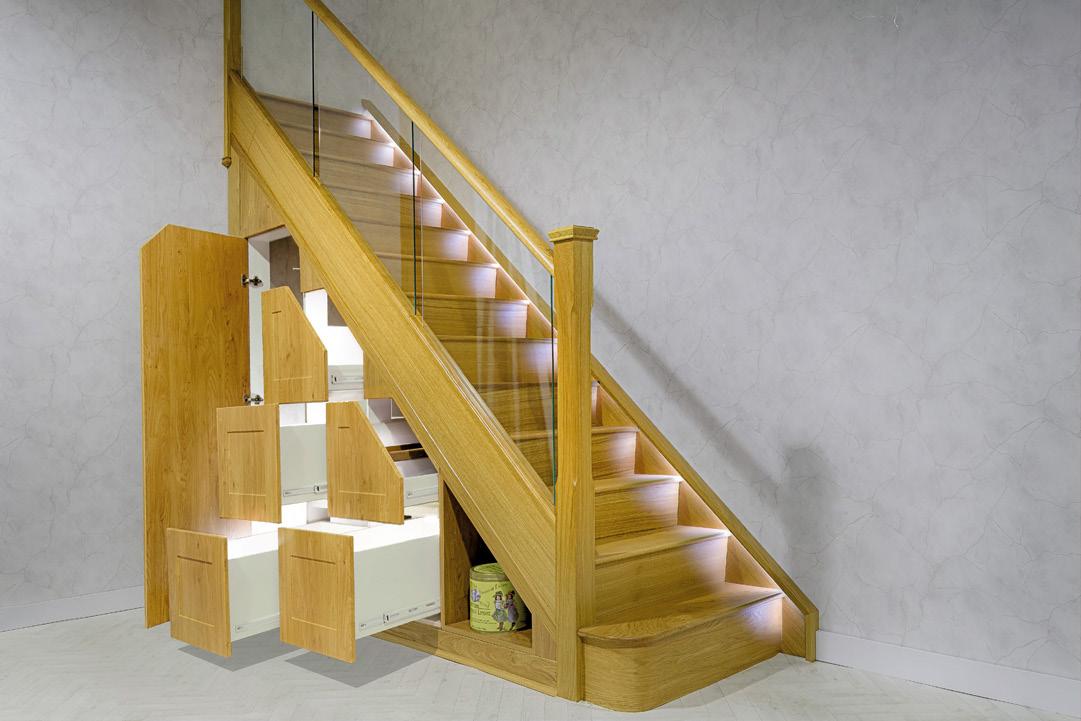
Until two years ago when Understairs started business this was perfectly understandable but now they have revolutionary storage designs to bring order to the under the stairs chaos.
The Father and Son team behind Understairs have over 40 years in Master joinery, Engineering and the Staircase renovation industry, with their initial roots in Designing and Installing bespoke Italian and German Kitchens.
As their work diversified throughout the home it became apparent that the resources and companies providing any form of Understairs Storage was very limited; such limitations meant that the options available were either very expensive or of poor quality imported from Europe. Identifying such a substantial gap in the market, design and development of a solution to this issue began and this Family team Formed ‘Understairs’ a company that would provide bespoke, quality understairs storage options. Formerly based in Manchester the team put down roots at their production unit in Preston investing heavily in state-ofthe-art machinery specifically adapted to produce the angled furniture. They began to introduce their high-quality furniture to the local area of Lancashire and Greater Manchester and have now extended their service area to cover Cheshire Merseyside North Wales and West Yorkshire but insist that they are willing to work outside of the region with consideration to the distances involved.
Understairs were not just looking to fill the gap in the market, they also wanted to increase the quality of the product and the level of service that accompanied the work. Their ‘Process of Care’ is a way of working to ensure the highest possible service levels, all orders are checked by a visit from a professional surveyor to ensure the measurements and the angle of the design is correct for each home, the surveyors visit is also to help and advise on the best configuration of furniture for your individual requirements. Once the specifications are agreed the furniture goes into production, it is then assembled at their manufacturing unit and checked for size and rigidity before

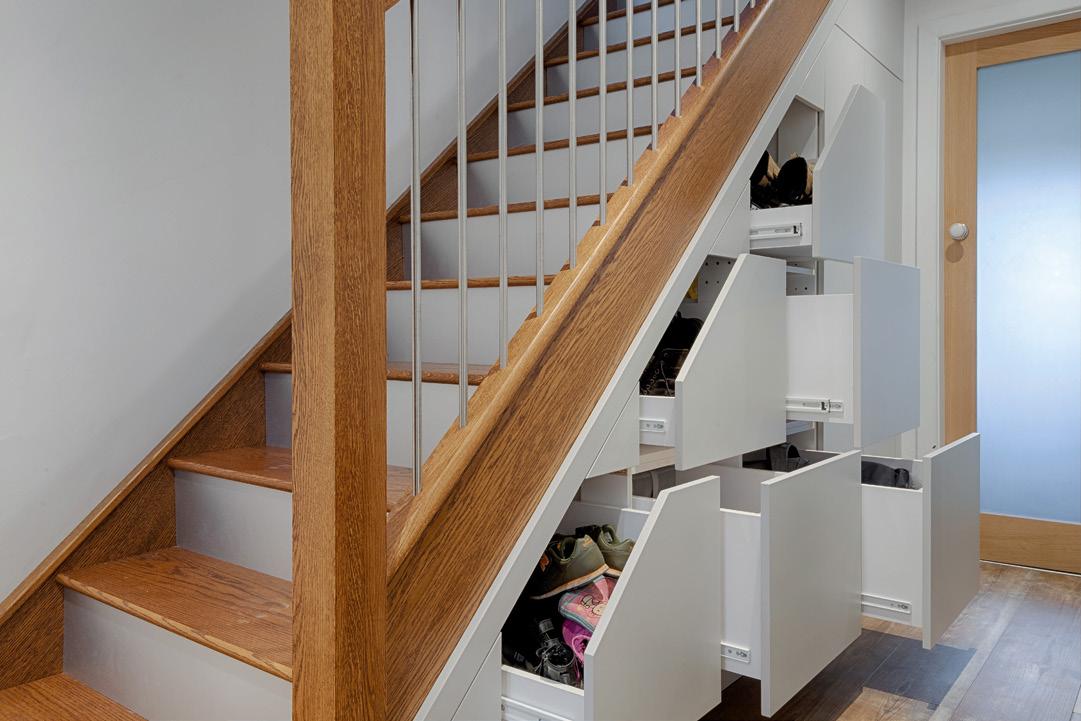
being delivered to the client’s home, this is a marked improvement from the ‘Flatpack’ approach available on the market.
Understairs have increased their standard guarantee from two years to five years from the date of installation and now offer an increased drawer capacity of 45 Kgs up from the previous 35 Kgs.
The final part of the Process of Care is the installation. This is never rushed and the ultimate care is taken, most installations are completed in one or two days depending on the work involved.
Understairs will remove stud partition walls and safely dispose of them together with any packaging and offcuts once the work is complete. Should there be a more substantial brickwork wall underneath the stairs then it is asked that this is removed prior to installation by a qualified builder of the client’s choice
This Process of Care method is setting a new benchmark and is a vast increase in levels of customer service to anything that had previously been offered in this area of work.
It was also an ambition of the company to add some variety to the market, the limited choice that was currently available through other companies offered few styles and colour variations. Understairs did not just want to equal this but set an entirely new standard as they currently offer nine different designs, showcasing combinations of 3, 5 and 6 drawers and angled doors included in a single frame. In addition to these stylistic options there are also available in a variety of colours including: alpine white, light grey, alabaster and cashmere allowing customers more choice to compliment the style of their home. These designs all have a sleek and modern feel and would provide both style and practicality to any interior. There are also useful accessories available to tailor this space to your needs including shoe rails, muddy shoe drawer liners and motion sensor lights.
In addition to stylistic changes from what was already available Understairs felt that improving the materials used for the designs was essential. Understairs decided that for the main frame of the designs they would use white 18mm thick melamine faced furniture board with all leading edges protected by a durable PVC edging as used by highend kitchen manufacturers instead of the 15mm thick MDF with no edging, that was currently available on the market that left edges open to moisture ingress and mould/bacteria, ultimately this new design would be more durable and the product would last longer. The next focus of the design was the fronts of the cabinet, Understairs protect the frontages with a durable 2mm thick PVC edging. This is easy to keep clean and will not need painting or treating in the future.
Understairs are constantly progressing and have attained a solid reputation with incredible reviews on both their website and trustpilot page ‘Understairs by Giobella’.
FOR PRICES VISIT UNDERSTAIRS. CO.UK/ PRICE-GUIDE TO BOOK YOUR BESPOKE STORAGE INSTALLATION OR FOR MORE INFORMATION.
Visit: understairs.co.uk Email: info@understairs.co.uk Call: 0161 624 5000