
7 minute read
Syntegon: Single-serve packaging for sustainability
Single-serve sustainability
COVID-19 affected the ways companies pack their products, organize operations and run their facilities. It also caused an increase in demand for industrial pre-packaged bakery products, and sustainable ones. A major step towards more sustainable packaging is enhancing its recyclability.

Mono-material films further cater to the sustainable packaging requirements of many industries, e.g. bakery
+Moving to individually wrapped items and increasing the packaging speed is not without challenges. Packaging smaller, individual portions creates a bottleneck within the feeding process: for example, single-serving items would have to be picked and placed into the flow wrapper without harming their integrity, which is especially needed when handling fragile bakery goods. Packaging products individually also faces limitations that stem from the shape of the product itself, whereas bulk packaging often does not require a specific shape. Product distribution systems are required here, or robotic solutions to feed, align and group the products.
This move also marks an abrupt departure from previous considerations regarding (environmental-friendly) packaging, which would encourage minimal or no wrapping whenever possible. Packaging sustainability becomes, under these circumstances, an even more important goal. A major step towards more sustainable packaging is enhancing its recyclability; one way to achieve this is by wrapping bars, cookies and crackers using polyolefin-based mono-material films, such as polypropylene (PP). It offers the same product protection as conventional plastic but can be fully recycled via established recycling streams.
Moreover, portion packs can support product quality: singleunit packaging within a multi-pack keeps products fresh for longer, since consumers can portion the products more easily. Added functionalities, such as easy opening and closing features for resealable packs, further increase the product’s shelf life.
A sustainability mindset
Given the notable focus on sustainable packaging, equipment manufacturers such as Syntegon Technology have been adapting existing packaging machinery, including horizontal flow wrappers, to package confectionery products in paper flow wraps, and cater to the need for alternatives to classic film-based packages. “Paper flow wraps are currently in the spotlight as a viable path towards a truly circular economy, which envisages to close energy and material cycles through efficient resource use, recycling and waste reduction,” Andreas Schildknecht, global product manager robotics and bakery at Syntegon Technology, highlights. Paper
Shaped paper pods are a sustainable option for single-serving packing of e.g. sandwich spreads, confectionery, or cookies
packaging on the one hand helps achieve these goals, since it is made from renewable raw materials as well as being recyclable and biodegradable. As far as plastic packaging for baked goods is concerned, on the other hand, thinner films with modified dimensions and narrower sealing seams will further reduce the amount of material used in packaging, the specialist explains. “From a sustainability point of view, it is also crucial to reduce the amount of packaging material. Some individually wrapped products are packed too loosely and come in oversized packs with a lot of enclosed air, creating other sustainability issues along the whole supply chain,” Schildknecht points out.
To answer packaging sustainability needs, Syntegon developed its ‘paper-ON-form’ retrofit set for a wide range of its traditional horizontal flow wrapping machines. The solution comprises a patented flow-wrap forming unit and sealing jaws for paper cold- and heat-sealing applications. It allows barrier papers to be processed without wrinkles, scores or cracks, while the customized cold and heat-sealing tools gently create the sealing seams. While the paper is shaped and processed, its barrier properties are maintained. “The ‘paper-ON-form’ retrofit kit can be used for different types of paper as well as conventional materials, enabling a step-bystep transition not only to paper packaging, but to a successful interplay of product protection, sustainability and efficiency,” the specialist explains.
To choose the best available option sustainability- and safetywise, the characteristics of the packaging material should be thoroughly assessed, as bakery products have different barrier and sealing requirements. While film solutions will continue to play an important role in maintaining shelf life and minimizing food waste, there is a chance some products could be packaged in alternative packaging materials, including paper. “The extent to which paper packaging is suitable for baked goods certainly depends on the requirements of the products at hand. At first glance, mono-materials seem more suitable as a sustainable packaging solution for bakery products,” Syntegon’s specialist underlines. Mono-materials like PP are on the rise thanks to their outstanding recyclability. Unlike commonly used composite packaging materials, monomaterial films only comprise layers of the same type of plastic. They are recyclable and therefore help to reduce plastic waste.
In terms of product safety, a tight pack protects the product first and foremost. Horizontal flow wrapping equipment offers extended sealing times, such as long-dwell or box motion sealing technology. For example, Syntegon Technology’s Amplified Heat-Sealing technology (AHS) for mono-material packaging combines the sealing capabilities of box-motion wrappers with the speed of a conventional rotary wrapper. “Thanks to the extended sealing times and the precise
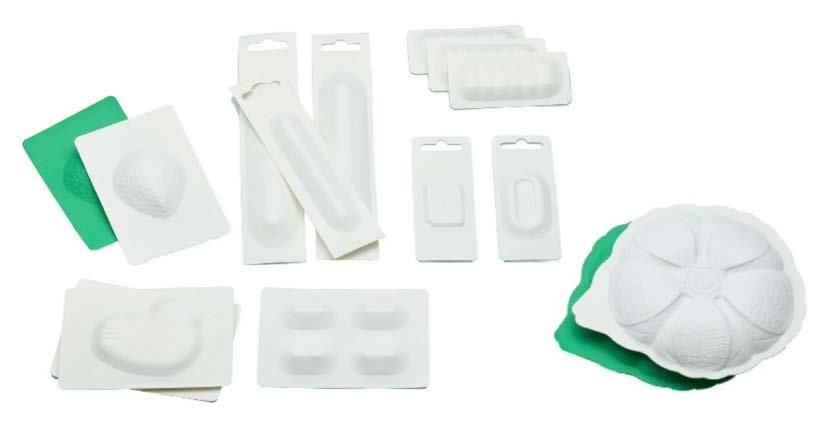
© Syntegon
KOENIG Motiv4 NTS 91x53.qxd 12.02.2007 11:10 Uhr Seite 1ADVERTISEMENT
Quality-brand and freshness with long tradition
The Nut specialists
Almond- Hazelnut- and Peanut-Products, roasted, sliced, diced and slivered. Hazelnutfilling and Multi-Crunch.
Please ask for products meeting your specifications.
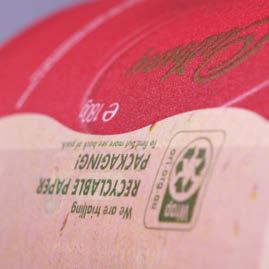
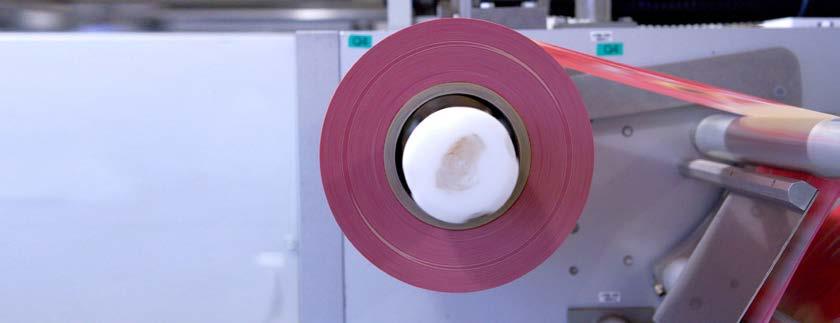
Paper fow wraps are used for confectionery products such as chocolate bars, as seen at Mondelēz
application of heat to the film, the flow wrapper can process a large variety of films at very high speeds, including fully recyclable mono-materials,” Schildknecht explains.
Paper or plastic?
The choice in packaging materials not only impacts the product’s qualities over time, but also the operations throughout the packaging operations. Processing alternative materials at constant speeds is a matter of properly adjusted packaging machines. In the case of plastic film, for instance, modifications on the film dimension can have a big impact. The specialist illustrates that “Reducing roll width and take-off length by two and five millimeters per pack, for example, can result in material savings of over 130,000sqm at an output rate of 200 packs per minute, in 23-hour operation.” Over a period of 50 weeks, this is equivalent to an area the size of 19 soccer fields.
When it comes to paper, the biggest challenge is the desired production output. “On horizontal flow wrappers, for example, cold seal plastic films can run at a speed of up to 1,500 pieces per minute. In order to achieve comparable speeds with paper, technological developments were needed, especially in the area of paper forming and heat-sealing media,” he says. Syntegon Technology has successfully conducted machine tests showing that flow wraps can be produced using cold- and heat-sealable paper without compromising on speed. However, heat sealing poses a significant challenge for paper packaging, because paper is a good insulator, meaning that it is not suitable for high output packaging, since sealing times have to be as short as possible. As a result, cold sealing is the common choice for high output quantities of paper flow wraps. A very thin plastic barrier layer provides the necessary product protection, while the packaging still qualifies for recycling.
Fully-recyclable Cadbury chocolate wraps
Paper packaging scores highly because it can be reprocessed in existing paper recycling streams. Consumers also perceive paper packaging as particularly sustainable and make their decision at point of sale based on touch and feel. Paper packaging receives increased attention with flow wraps, leading food manufacturers to consider the change from conventional packaging materials to paper-based packaging. However, this format poses a particular challenge, as paper is not as easily processed as films and can be difficult to use on existing flow wrapping machines. Mondelēz International is committed to making all of its packaging recyclable by 2025. Aiming to package its Cadbury chocolate tablets in fully recyclable paper flow wraps, the confectionery giant approached Syntegon. Within a year, Syntegon had developed a forming unit and sealing jaws for cold sealing applications, at its test laboratory in Beringen, Switzerland. This upgrade kit has successfully been tested on Cadbury’s flow wrapping machines for chocolate tablets.
Paper packaging has a number of limitations which makes it challenging to protect the product to the same degree as proven conventional films, while generating the same output on the machine. Paper is a good insulator, and a fairly stiff material, which makes it easy to crease or tear during the pack forming-process and result in damage. The shape of the chocolate tablet itself posed an additional challenge, Syntegon revealed. While normally bar formats are easier to handle, chocolate tablets like Cadbury’s Energy tablet are much broader and very flat, which makes them more challenging to process. The packaging specialist developed the ‘paperON-form’ forming unit, a retrofit that could be installed on existing machinery, based on Cadbury’s selected paper film and the desired pack size, using 3D-printed components. The kit was installed on Cadbury’s H-series flow wrapping machine.
Comprehensive tests have shown outputs without speed limitations with paper flow wrapping essentially matching the performance of flow wrapping using films. The forming unit and sealing jaws can be used with different types of paper, regardless of thickness and supplier, making paper packaging a real, sustainable option. +++