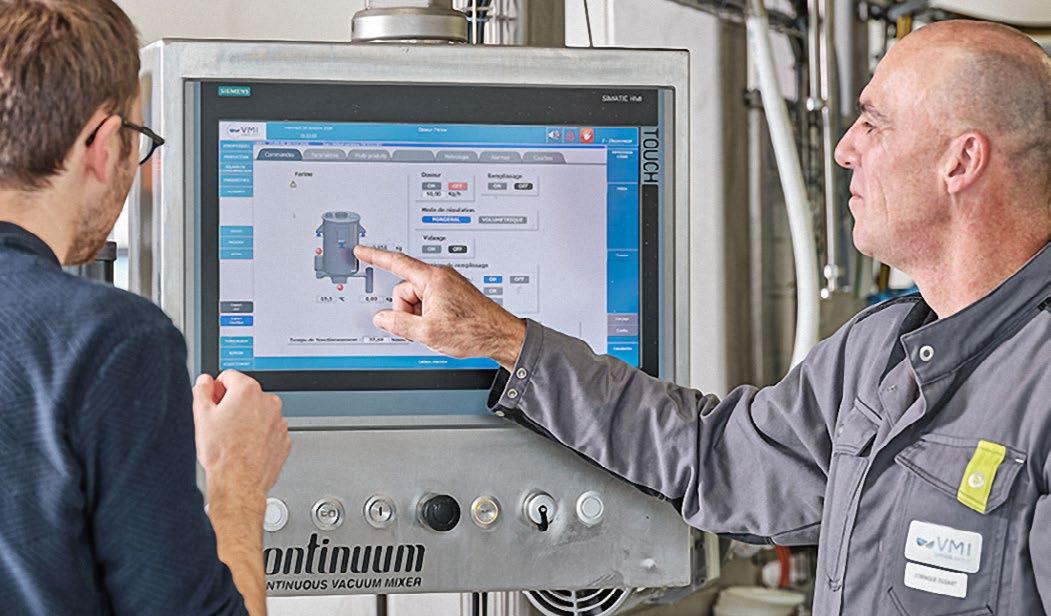
5 minute read
Energy savings under the hood
Managing energy consumption is a growing concern for bakers, in Europe and beyond, now and for the long term. How can equipment help industrial bakery, pastry, and snack manufacturers reduce their energy consumption?
+Controlling energy expenses is becoming more critical to manage than ever, as manufacturers are facing several hard knocks, such as the increase in the price of raw materials, supply difficulties, and now the rise in the cost of energy. It is also bound to drive competitiveness for companies looking to improve their environmental performance and their transition to more sustainable development.
VMI targets sustainability when designing equipment. The French mixing specialist strives to support its customers in this transformation process, taking into account sustainability and environmental impact measurements when developing equipment and services. As part of its design strategy, VMI has three specific goals in this regard:
+ Optimizing energy consumption, especially during the machine design phase
+ Improving the way equipment monitors water and electricity consumption
+ Identifying areas for improvement and implementing corrective actions together with its customers
Equipment design
Working on custom solutions for mixing equipment, VMI’s engineers consider specific plant issues for the design of the machine, starting with the project study. In addition to safety, standardization, or modularity, they also consider energy efficiency when developing or upgrading equipment. “A well-thought-out design can result in significant energy savings. VMI complies with European regulations as our heavy-duty equipment is fitted with IE3 motors. While the latter may have higher purchase prices, they have reduced operating costs due to lower electricity consumption. For a motor that operates intensively throughout the year, this opens up the prospect of a quicker return on investment,” VMI’s specialists explain. Installing a more efficient motor can be a sustainable investment for continuously running equipment with high maintenance costs, since it can increase both the reliability and the lifespan of the equipment.
Several VMI machines are equipped with a variable speed drive, which ensures the equipment starts smoothly with an acceleration ramp for a gradual increase in speed. “It is especially useful in reducing the stress on mechanical parts and can consequently limit their wear and tear while avoiding consumption peaks during start-up,” VMI details.
Some types of equipment incorporate technologies for more sustainable production. For example, the Kneadster vertical batch mixer has a drive on the tool and on the bowl that enables the mixer to store and re-inject energy into the tool drive circuit and vice versa, reducing its consumption.

Moreover, another main design feature that can have a significant impact on energy consumption is the shape of the tool and the tool/bowl ratio. “Our R&D team works to ensure efficient pairings, which may allow quick and efficient dough mixing, with minimal machine heating and stress, which, in turn, makes it more durable and more reliable,” VMI highlights.
Connected Process intelligence to monitor industrial performance
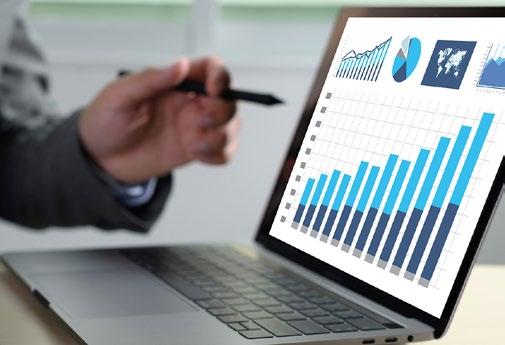
Choosing the right equipment directly influences energy consumption. As far as the process is concerned, the first step in reducing consumption is being able to measure it. VMI is convinced that information is the key to making improvements in this area. Accessing and analyzing data is a challenge for many bakery and food manufacturers.
How can it help reduce energy consumption?
Different applications have been designed to provide a high level of analysis. Operators can not only view the overall consumption levels of their facility but also that of each connected machine. In addition, energy consumption can also be related to the amount of dough to compare different production flows. Recipes can be sorted to help identify the most energy-intensive and the most eco-efficient options. Manufacturers can then choose to change their recipe management according to this new criterion. Resulting areas of improvement could range from adjusting speeds, improving dough hydration, or checking ingredient dosing, among others.
To help manufacturers access and analyze this data, VMI has developed Octopus Solutions®, an IoT platform designed to monitor industrial performance. This tool gives centralized access to all machines and connected processes and allows bakeries to visualize their operations and optimize them.
“The smart Octopus Solutions ® can collect, store, analyze and use data to monitor key equipment indicators for more intelligent, integrated and efficient production.,” adds VMI. Applications cover:
+ Production monitoring
+ Consumptions – electricity, water for washing, overall water consumption
+ Preventative maintenance, as well as stops and defaults that can impact production and efficiency
IoT also helps to follow water consumption, especially during cleaning, to identify differences between production operations. In addition, the consumption of water that is used for cleaning should not be overlooked, VMI notes. “On an automated mixing system, and for a standard bakery recipe with 60% hydration, a bowl can be cleaned, on average, every five minutes. This requires several liters of water. With accurate measuring, inconsistencies or overconsumptions will be identified. They can be related to production (e.g., using more water to clean after a certain production cycle or specific recipes), or to maintenance, such as leaks (a leaking seal, for example) due to wear and tear and poor maintenance. By comparing the consumptions between similar production runs, unjustified deviations can be corrected,” VMI explains. One of its customers managed to reduce its water consumption used for cleaning on one of their lines, by 50%. They were able to identify that one washing ramp was clogged and they were wasting time and energy cleaning their bowls, in this instance. This type of optimization may also represent substantial financial savings, the mixing specialist points out.
Since a global dashboard gives access to all the installed lineup of machines, data can easily be correlated to each other, and KPIs to some observed events during the production process. Implementing such a web platform, connected to equipment and processes, can be a powerful analysis and decision-making tool.
Services to improve the mixing process, machine use and maintenance
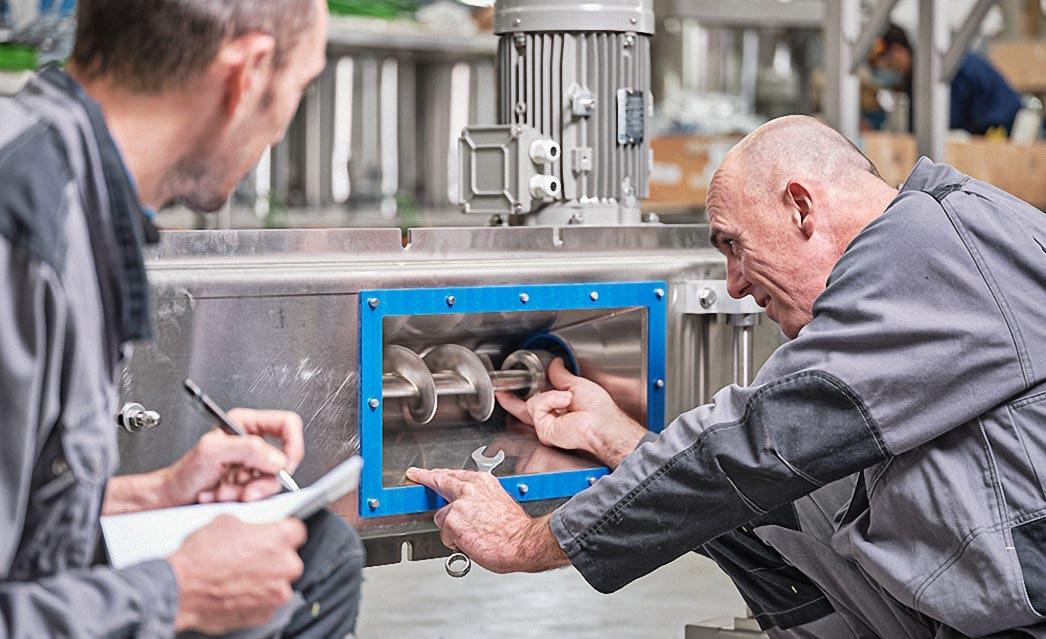
Once overconsumptions, inconsistencies, or abnormal use have been identified, corrective actions become more obvious. VMI aims to support bakeries in the optimization of their processes and equipment in the following ways:
+ If improvements must be made to the process such as recipe management or cleaning cycles, technical coaching is a good solution. VMI technicians will coach operators and supervisors on best practices to limit any production interruptions to help get optimal operation of production processes.
+ If human errors occur, proper training can avoid stoppages or unwanted changes in settings. With visual and easy-to-interpret data, it also becomes easier to highlight inconsistencies or regular issues on the line, to raise team awareness. Follow-up and training are essential to limit downtime or slowdowns. VMI is working on developing flexible training methods aimed at all levels and professions to meet the needs of bakery manufacturers.
+ Overconsumption linked to the machine such as leaks can signal that more regular and thorough maintenance may be recommended. Consistent maintenance visits are recommended for prevention before troubleshooting arises. Retrofitting operations can also help optimize the machine’s process or prevent equipment obsolescence.
Conclusion
VMI believes that IoT systems like Octopus Solutions ® will play a major role in the future, in meeting changing manufacturing challenges. By developing and growing this technology, VMI also gets to know its customers and better understand their challenges: “In the long run, we hope that our customers will be able to build their own benchmark in terms of production performance or energy efficiency, compared to reference values.”
Compiling KPI data thanks to IoT tools will support decisionmaking. It can work throughout the facility to compare performance between production sites, to ensure consistency. Finally, it can also help guide the choices in terms of production, renewal of the machine base, or the choice in ingredients suppliers. VMI will work on further developing this tool, in partnership with key market players. +++