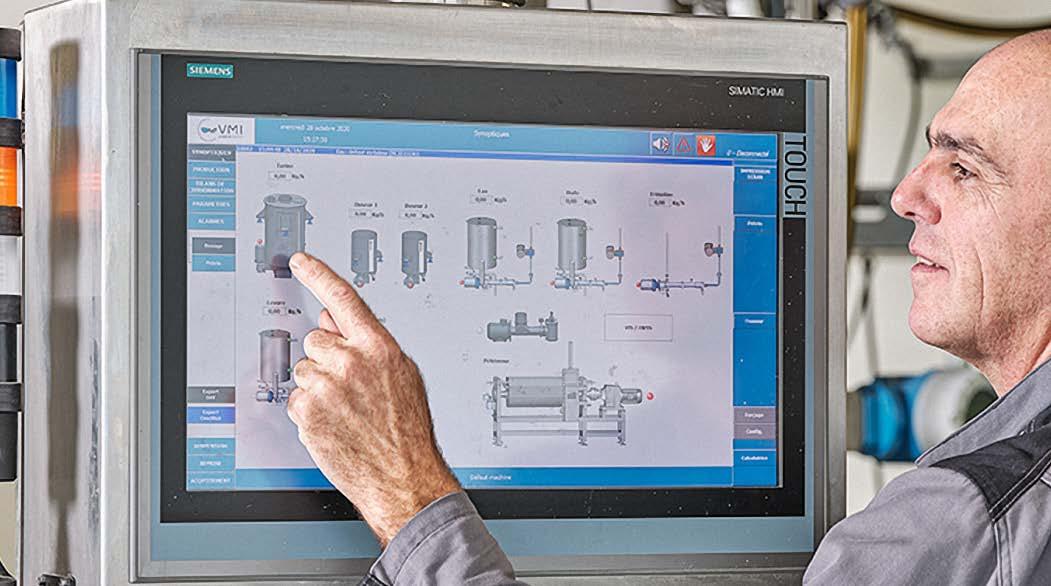
13 minute read
Continuous mixing: The steps to dough consistency
by landmagd
The steps to dough consistency
Automated continuous mixing delivers real-time process assessment and consistency round the clock.
+Continuous mixers allow for all parameters to be constantly monitored and saved digitally, including ingredient stream rates, dough temperature, mixing energy input, throughput, mixer shaft speed, coolant temperatures, starts and stops, ingredient refill status, ingredient totalizers, dough totalizers, and many others. Exact Mixing’s continuous mixing systems, for example, are fully automated, meaning that the operators need only respond to alarms in case readings show parameters deviate from preset values, which doesn't happen very often. The collected data is saved and used to generate graphs to compare actual values against set points. Information quantifying the dough production is also available, with details about its current progress, the amount completed per shift, or sorted by any other criteria that are useful to production.
“The analysis of the data can then be configured in any way that the end-user sees fit. In the control system, all parameters are constantly monitored, and statistical analyses of parameters are available. The available information is only limited by the imagination of the person seeking the data,” Jim Warren, Vice President, Exact Mixing, explains.
Jim Warren, Vice President, Exact Mixing Systems ready for the unexpected
The ingredients’ temperature commonly varies during the mixing process. Differences can be cyclical if the flour is stored in a silo outside or can occur between days and seasons. When dough is produced with continuous systems, other parameters are not likely to vary in the absence of external influences. With continuous mixing, products and processes are fully repeatable from shift to shift and day to day because the metering and mixing processes are fully automated. If there are variations identified, they are generally corrected automatically, before the operator has time to react.
But, “If one parameter continues to create alarms, the system needs to be inspected to determine the cause of the upset. For example, temperature variations can be automatically compensated for with our dough temperature measuring instrument when used in conjunction with our water blending valve,” Warren explains. The water temperature is automatically adjusted to match a set point for the dough temperature. However, in case of a failure with the hot water

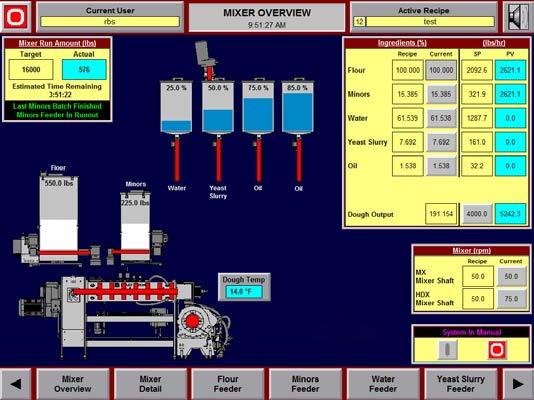
© RBS
supply in the plant, the mixing water temperature cannot be reached. “In this situation, the operator would have to be involved because the source of the hot water is outside of the mixing control system scope,” he recommends.
Fully automated ingredient metering into the mixer is part of the Exact Mixing scope, as accurate metering is critical to the success of continuous mixing. For this reason, developments for this technology have advanced at the same pace with R&D of upgrades to mixing technology.
“Accuracy is ensured using the latest metering technology including loss-in-weight dry metering technology and mass flow liquid metering technology,” Exact Mixing’s VP explains. The measurements recorded are continuously compared with the setpoint data to adjust the process if necessary, or issue warnings if automated corrections are not possible, to protect consistent dough quality. Ingredient delivery technology is a continuous improvement priority for Exact Mixing. The company has recently developed systems that accurately meter ingredients such as solid shortenings, nut-butters, diced cheese, and dried fruit.
The mixing specialist is also constantly bringing improvements to its continuous mixing technology. “For example, we now offer five distinct continuous mixing models for different applications and customer requirements. The HDX Mixer is just one example of technology expansion.” It was developed 10 years ago to allow for the mixing of highly developed doughs such as bread and buns. “More recent technology breakthroughs include the high-speed developer and Hydrobond Technology instant hydration units,” Warren details. All advancements can be fitted onto existing systems. “The core of our continuous mixing has been stable and built around automation. The systems and technologies that are newly developed are meant to augment this base, not replace it,” Warren elaborates. New features are commonly brought online to existing equipment; program upgrades can be made locally, in most cases, and remotely on newer systems with connectivity features.
In addition to these advancements, automation features can step up as requested, with many options available to choose from, such as the automated control of the ingredient and water temperature, automated dough re-work, automated control of the dough hopper level downstream – to name a few. Fully-automated control packages Exact Mixing provides include (but are not limited to): + Recipe setup, storage, and control + Recipes can run for a fixed amount of time, or production can be set for a fixed amount of resulting product + Fully graphical presentation for controls, for easy management + All parameters are recorded as well as all alarms, input changes, and operator interventions. Other types of data can also be added for monitoring and analysis. + System parameter changes are indicated by color changes on the operator interface + A general operations screen for an overview of the process, as well as detailed screens for subsystems
Overall, continuous mixing is designed for maximum process efficiency. Such steps are established to do just that, to ensure all parameters are measured and recorded, and that the resulting data is immediately useful. “The goal is to have the operators focus less on ‘making dough’ and focus more on making the best dough. For this to happen, we must give the operator the best, real-time information possible,” Warren underlines.
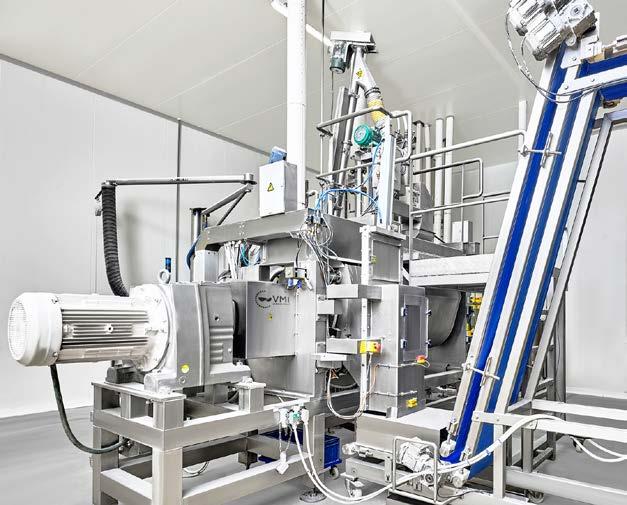
© VMI
In the mix: VERYMIX
VMI’s VERYMIX continuous mixer also monitors and controls several parameters, including the energy throughout the process. “From premixing to the end of the mixing process, the viscosity and the formation of the gluten network are monitored thanks to the energy tracking,“ explains Mélanie Gay, Marketing & Digital Development at VMI. Everything can be managed from the HMI, from recipe formulation, dosing, programming, to monitoring and traceability. “Whether it is the ingredients consumed or the amount of dough produced, you can check on the curves to view the flow control of the dosing devices. In this way, you can check that the flows and the calibration of the powder dosing scales are maintained,” she illustrates. Recipe data, consumption balance, alerts and any other requested parameters can be exported to Excel files or made available to the Manufacturing Execution System, for a better understanding and optimization of production cycles. The information can be accessed in real-time and past performance data is also available. It can be visualized by duration or by team/shift.
Given the breadth of data, numerous adjustments can be made, including the preventive adjustment of the process, for example, according to the use and data VMI collects and analyzes on request. The VERYMIX flow rate can adjust itself automatically, based on experience feedback from previous cycles. Parameters can also be measured and adjusted manually, including mixing time and intensity, dough temperature before, during, and after mixing, energy transmitted to the dough, and the opening of the glycol valves, VMI’s specialist explains. “The ability to optimize the use of VERYMIX is a point that is of great interest to our customers, whether it is the process itself, the costs associated with its use (e.g., energy consumption), or maintenance.” Pre-hydration can also be controlled; VMI’s horizontal pre-mixer (HPM) integrates ingredients in the bowl in two zones, one for powders and one for liquids in the form of spray droplets, and a third zone specific to mixing. “Flour, sugar and other baking ingredients are combined with water and immediately form a homogeneous dough and the beginning of a gluten network,” VMI’s specialist explains. These steps are designed to make the mixture more homogeneous and the process more effective, allowing for a wider range of hydration, from 40% to 110%. The HPM works directly above the VERYMIX, and continuously transfers hydrated raw materials into the mixer underneath, where the dough is mixed to the required consistency. “Its horizontal design, in addition to taking up less space and providing a better seal, eliminates the risk of clogging,” adds Gay.
To maximize efficiency, the VERYMIX offers a wide range of mixing parameters that can be used according to the production criteria, and quality required: the mixing rotor is adapted to the dough, the bowl shape is optimized for continuous operations and times and mixing intensities are adjustable. This level of process control allows for flexibility: “Classical sponge and soft doughs, as well as firm doughs, with or without fermentation times and frozen doughs can now be prepared efficiently.”
Mélanie Gay, Marketing & Digital Development, VMI
Very accurate dosing
The VERYMIX continuous mixer automates powder and liquid ingredient dosing as well as scrap dough management. Flour, salt, sugar, powdered milk, gluten, improvers and other raw materials are weighed by three stainless steel load cells. These load cells can be fed automatically by intermediate hoppers, or by manual loading hoppers (big-bags). Water, egg, milk, liquid yeast, flavorings, liquid sugar and brine are also precisely dosed. The system features dosing pumps and electromagnetic or mass flow meters to weigh liquids.
The quantity of scrap to integrate can also be dosed: “Scrap dough should not be neglected: for bread, it can amount up to 25% of the weight of the flour and for some puff pastry, it can even surpass 50%,” Gay highlights. The VERYMIX continuous mixers make it possible to automate the flow management towards resting phases or for a transfer to the line, while also reintegrating the dough scraps. For its latest improvements to the system, ”According to the mixing phase, VMI has worked particularly on the shape of
its tools and tanks, specific to premixing, kneading or fermentation steps.” The latest addition to the VERYMIX is a mobile cleaning in place (CIP) station which can be connected to the liquid dosing stations: “Since they are so flexible, CIP systems make it easier to manage standard cleaning protocols, and limit production downtimes when changing product,” she highlights.
The new modular Codos® kneading system
Consistent, high quality of any type of bakery goods starts with a perfectly prepared dough. Zeppelin’s new CODOS® mixing and kneading system brings innovations for continuous operations to help achieve it consistently. After modernization and reworking, the Codos® system concept has been repositioned and introduced to the market as Fresh-Up, a modular mixing and kneading system with new components. The complete system consists of a CODOS® tower, a DymoMix® and a CODOS® NT kneader.
CODOS® tower – liquid and solid matter dosage to feed the continuous system
The CODOS® tower is the initial unit in the CODOS® system. It consists of a storage container with a mixing tool and a differential weigh feeder positioned underneath to produce a
ADVERTISEMENT
continuous and constant mass flow of powdered raw materials. “Mostly cereal flours are dosed in the bakery. Other raw materials such as starch, proteins or dextrins for gluten-free products can also be processed. The Codos® tower also includes the water dosing and temperature control as well as dosing for other liquids such as yeast suspension or oil,” explains Dr. Christian Faber, Senior Technology Consulting, Zeppelin Systems. Liquids are continuously metered together with powdered raw materials. The pumps used for dosing liquids and the flow meters as well as the necessary valves are located on liquid panels on the CODOS® tower. The panels with the aggregates and instruments are also modular, highly accessible and can easily be replaced, he details.
DymoMix® – special hydration
The DymoMix® hydration system can be used as a premixer in the Codos® system and as a complementary production step between dosing and kneading of doughs or other further processing steps. “The special feature is that powdery components are hydrated with water or oil, immediately forming a homogeneous mixture. This procedure allows the production of improved-quality dough. Hydrating with water or oil is accomplished by a specially-designed
www.heuft1700.com
THIS IS
BAGUETTE.
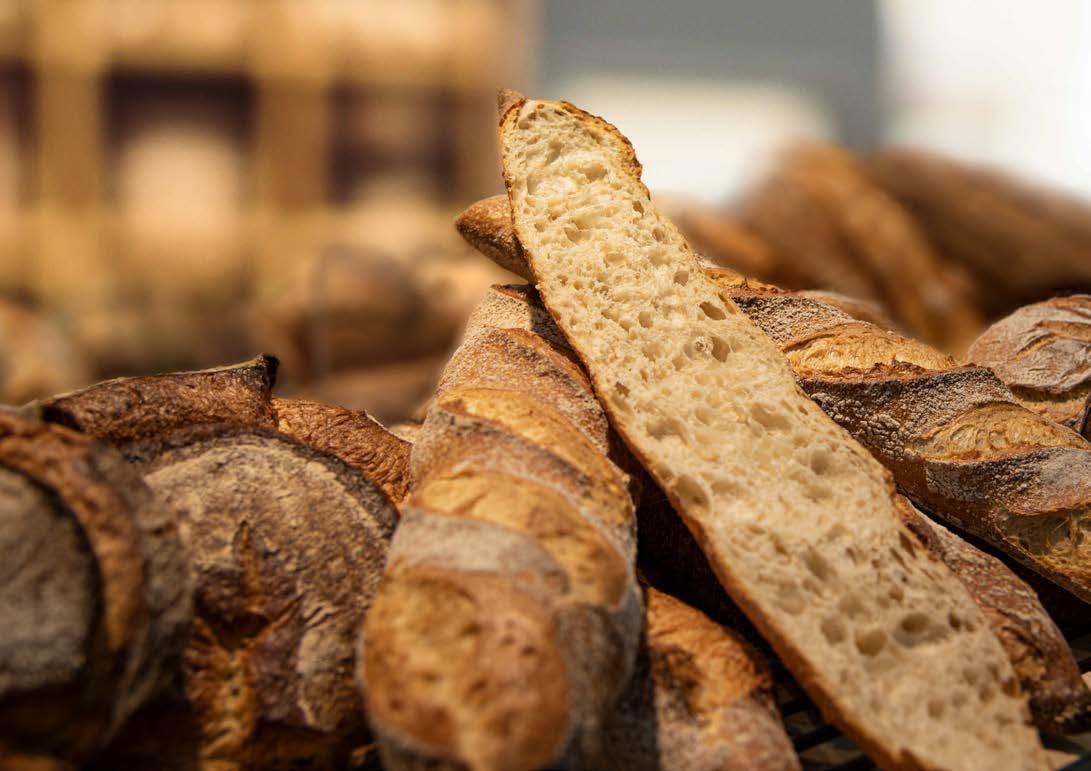
BAKED IN AN ARTISAN HEUFT THERMAL OIL OVEN.

nozzle built into the rotating shaft of the unit. This forms a liquid film through which the powdered particles must pass, becoming hydrated. Unlike conventional systems, a highpressure water jet is not used for hydration. As a result, even with low moisture contents, a high-quality product can be produced, ready to be processed immediately without intermediate steps,” the expert elaborates. The CODOS® tower and DymoMix® and CODOS® NT kneaders can be used in different combinations, for different applications: + For the production of pumpable pre-doughs or liquid doughs that are to be fermented (e.g. liquid sponge or sourdoughs) + For the production of premixed bread or roll doughs, which are continuously kneaded in the CODOS® NT kneader
CODOS® NT – ensuring a gentle kneading process
The dough is formed in the horizontally operating continuous CODOS® NT kneader. “Special helical interlocking twin shafts apply the energy required for kneading to the dough. This forms the gluten structure of the wheat dough. The bow shape of the kneading attachments on the twin shafts ensures gentle kneading without cutting the dough. The energy input required for the specific product can be controlled via the speed of the kneading shafts, as can the dwell time of the dough. Thanks to a double-walled, temperature-controlled trough design, the dough always maintains the desired temperature. This allows the specified temperature of the dough to be maintained within narrow limits,” Faber explains.
Dr. Christian Faber, Senior Technology Consulting, Zeppelin Systems
Process control, improvements
Chilled laminated dough is required to make a croissant. In this case, the flour is kneaded with ice water so that the dough temperature is 18 °C or even lower. Alternative cooling solutions such as CO2 or ice are not required for temperature control with CODOS® NT kneaders, leading to savings in the cooling process. For hamburger buns, however, a warm dough of about 28-30°C is needed. In this case, the mixing water temperature is automatically controlled so that the dough has the correct temperature after kneading.
Depending on the recipe requirements, ingredients can be added at any point of the mixing and kneading process. “For example, to produce a high-quality pretzel dough, it is necessary to add the high fat content after mixing but before kneading.“ Process flexibility also allows control of the dwell time of individual components. As a result, sensitive raw materials such as fruit chunks or flakes can be fed at the end of the process and incorporated with minimal impact.
With an output range between 500 and 6,000 kg/h, the new generation of CODOS® NT is a step up in terms of capacity and efficiency over previous models. Advantages include precise temperature control, raw material metering accuracy, and low energy and maintenance requirements. Faber: “The high-torque water-cooled servo motor offers savings on energy and space. It is also flexible and easy to use, requiring fewer controls. The design incorporates ease of operation and maintenance without the need to disassemble the shaft. A hood was incorporated for quick access to replace seals, bearings or couplings.” These are the only parts that require regular replacement, minimizing maintenance costs. Hygiene requirements were also taken into account, such as a fully automatic cleaning system.
The main area of application for the CODOS® system are monolines, where production can run around the clock. The same system can be used for doughs with broadly differing requirements and characteristics. The new CODOS® NT line is currently available in two different sizes: CODOS®NT 160, with a dough capacity from 500 kg to 3 t/h, and the CODOS®NT 200, with capacities from 2t to 6 t/h. +++
© Zeppelin Systems