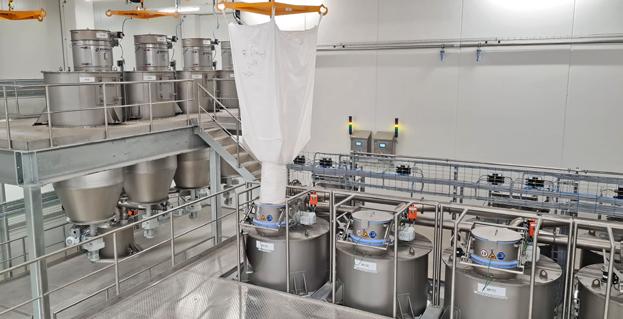
3 minute read
A very special order
In the spring of 2023, Ölz der Meisterbäcker put its expanded production into operation. When it came to raw material handling, the Austrian plant baker relied on Zeppelin Systems for solutions.
By Denise
+Ölz der Meisterbäcker, headquartered in Dornbirn, Vorarlberg, is Austria’'s market leader and produces more than 100 different baked goods with around 1,040 employees. In 2022, Ölz generated sales of around EUR 240.2 million, up 12.8% from the previous year. The export share of the company, which is managed by the third generation of the family, is 43%.
When the plant baker started up its extension in Wallenmahd in spring 2023, two new production lines for yeast dough pastries, toast and sandwich breads also went into operation. For raw material handling, Ölz relied on a solution from Zeppelin Systems. This means that there are now three systems from the Friedrichshafen-based specialist in operation at the bakery in Wallenmahd.
“Ölz commissioned us with the complete raw material supply for the new hall, including a connection to the silos in the existing plant,” explains Ingo Pütz, Director Sales, Food Plants at Zeppelin Systems. “This was also a very special order for us – in terms of scope, requirements and schedule.” The plant manufacturer not only supplied individual components such as silos, screening machines, etc., but also took over the mechanical installation as well as the complete control scope including control cabinet construction and software development. It took just two years from kick-off to acceptance. The fact that such a large project proceeded quite quickly and smoothly was also due to Ölz’s thorough preliminary planning. In addition, both project partners were able to draw on their experience with the first two plants.
”This was a very special job for us, too - in terms of scope, requirements and schedule.”
Organization is everything
Changing batches, different dosing accuracies of the raw materials as well as different container sizes require wellthought-out raw material management. Ölz set high standards for the new production lines at Wallenmahd. “The customer had very precise ideas at the start of the project,” recalls Ingo Pütz. What was required was a plant that was as compact as possible. The Zeppelin Systems engineers were involved in the planning at Ölz at an early stage and were able to coordinate with the building planner. “We jointly designed a 3D model of the plant in which we had already positioned all the equipment in great detail. And we were able to implement it almost 1:1 like that,” confirms project manager Roman Kreher from Zeppelin Systems. Another component of the order was a simulation of the processes based on the basic recipes. “From this, we gained some insights that were incorporated into the planning,” reports Denise Mohr, who had supervised the process engineering design of the plant since the beginning of the sales phase.
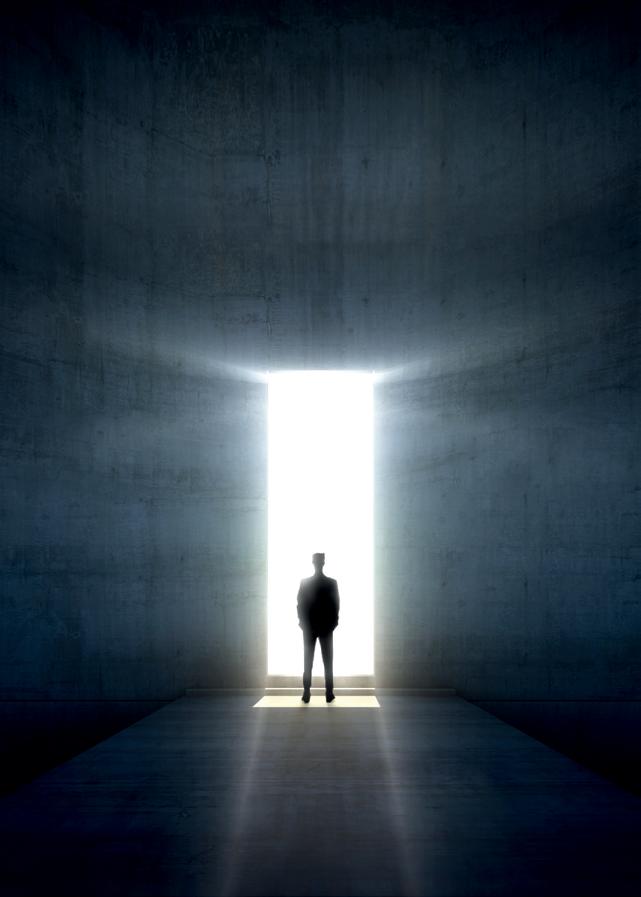
The aluminum storage silos are almost 16 meters high, in which large quantities of flour, sugar and salt are waiting to be used. Special flour blends are in pole position in the station for medium components, ready to be mixed into the dough at any time.
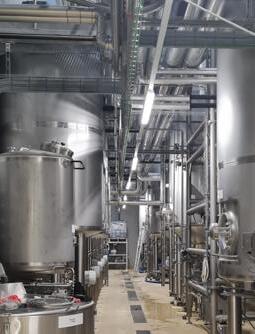
”Together with Ölz, we designed a 3D model of the plant in which we had already positioned all the equipment in great detail. And we were able to implement it almost 1:1 like that.”
Individual requirements
Ölz stocks ingredients that are required in smaller quantities, such as seeds and kernels, in sacks. In order to be able to act as flexibly as possible with the frequently changing recipes, the employees weigh these small components manually. “The Zeppelin Systems experts adapted the concept for handling the small components to our requirements,” reports Walter Maurer, plant manager of the Ölz Bakery in Dornbirn-Wallenmahd. We wanted a user-friendly solution here, with which the employees can work error-free. This is particularly important for ingredients that only make up a small proportion of the recipe.” A highlight of the plant is located on the upper floor: mobile manual feeders, under which containers and scales are located. The operator is shown via a screen what needs to be filled into which small ingredient containers. One floor below is the removal facility with a manual weighing station. “This mixture of 'manual and automatic' speeds up and simplifies the handling of the small components – and above all, the method enables high dosing accuracies,” explains the plant manager. To prevent employees from filling incorrectly, an RFID transponder chip is mounted in the base plate of the manual infeed chute. Only when this is positioned at the correct transponder is it released for filling.
Quality assurance has a high priority
In order to meet the requirements for a consistently highquality product, Ölz attaches great importance to quality assurance. Rotary screening machines, for example, allow grain sizes to be precisely verified. They are located directly below the silos for large components. This compact design saves time because the product can be transferred directly from the silo to the pneumatic conveying system. “We already stock sifted flour in daily silos,” reports Walter Maurer. “That pays off with the many different batches.” Container cleaning with a semi-automatic CIP system also contributes to the high quality of baked goods. In order to be able to trace all cleaning steps, the control system records the processes and stores the data.
The large bakery also relies on the expertise of Zeppelin Systems engineers when it comes to explosion protection: a bursting disc is fitted to the sugar silo as a structural
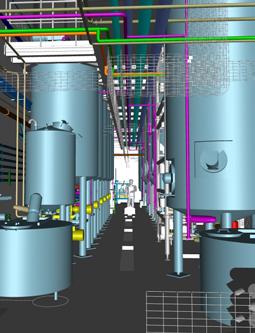