
4 minute read
Ashworth: Process automation with the SmartSpiral
Real-time is the right time
Every aspect of the process and its related equipment is closely analyzed to identify new ways of increasing efficiency. When proofing, cooling and freezing bakery goods, this means constant monitoring to prevent unplanned downtimes. For this, smart tools are the key.
+A versatile piece of equipment that can be used for all processes requiring controlled temperatures is the spiral. For this technology, Ashworth developed the SmartSpiral® Monitoring System, an application that provides real-time monitoring of multiple spirals, even over different facilities. It manages maintenance to identify performance issues, prevent failures, consequently minimizing downtimes and service.
The system is designed to monitor parameters that are difficult to monitor in harsh environments, such as a freezer during operations or a bottom bearing on a Lotension spiral cage, for example. The SmartSpiral® monitors trends over time as well as instantaneous changes. Various kinds of data can be obtained and managed with the SmartSpiral®, depending on the system and its requirements. “Every system is unique, so we establish a baseline for each monitored parameter as a step of the installation,” explains Chris Trinch, Senior Product Engineer for Ashworth. Data is continuously collected, with a data point established every three minutes. These data points are used to establish trend graphs. “Over time, the system calculates SPC data to provide +/- 3 sigma ranges for all monitored sensors. Once calculated, the 3 sigma limits are noted on the graphical displays,” he adds. Moreover, performance parameters are defined within preset limits, to trigger warnings when parameters are outside of these presets. When it encounters deviations, the system automatically sends a notification as soon as an alarm is registered. Data is recorded and analyzed for such ‘alarms,’ which are saved for an evaluation of the overall status of the system. Data is monitored for the bottom bearing, the cage drive, the outfeed drive, temperature, and belt tension. Sensors can also be added and monitored based on specific process requirements. In addition, up to three more sensors can be added to the system, upon request.
The evolution of the trend graphs indicates the health of the system. Trend data is graphically available on the connected smart devices to monitor the system’s operation in minute detail, to maintain/ increase process efficiency and to identify areas that may require adjustments or intervention. As it monitors basic parameters, the SmartSpiral® uses the data to create an image of the entire system’s performance which becomes the backbone of predictive maintenance.
Follow the QR-Code to watch the video
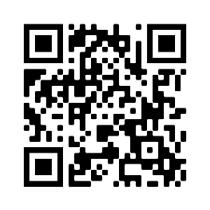
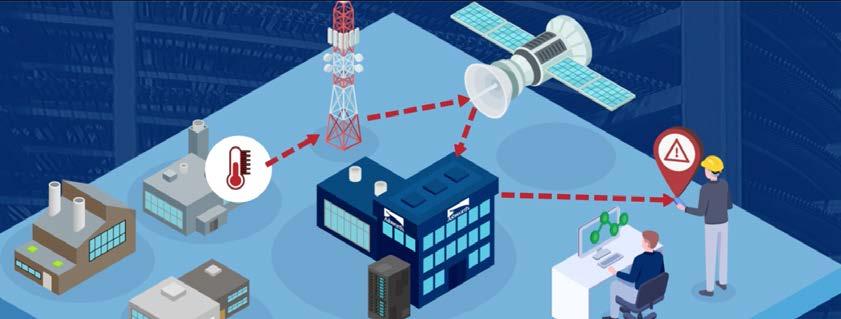
© Ashworth
Valuable data
The working environment of a blast freezer is inhospitable for most operators. The SmartSpiral® Monitoring System is particularly suitable for cooling and freezing conditions because it is built to withstand harsh environments, including below-freezing temperatures. It transmits system data to the smart devices it connects with for safe viewing, outside the freezer.
Motor power, temperature, and bearing noise are among the process parameters that are frequently monitored. Motor power brings insights on how hard the system is working, bearing noise levels indicate whether the bearing needs lubrication or replacement, and temperature changes can show in detail the efficiency of the cooling systems as loads change. All the data acquired helps to effectively plan production schedules and accurately anticipate all routine operations needed, from cleaning to maintenance or any intervention that might be required to continuously improve the processes.
While it performs ideally for conditions such as freezing temperatures, the SmartSpiral®’s use can be adapted to fit the needs of other processes, too. This is why it was designed as an open platform. “For example, a user could elect to monitor an oven with various temperature sensors and a sensor on the main drive motor,” Ashworth’s specialist illustrates.
Smart and safe data
The system notifies plant engineers and managers about potential system failures before they actually pose a production problem. The messages issued include information about the fault identified, the date and time of detection, as well as the system ID and the location of the facility. Information is provided online, via a webpage, as well as via weekly performance emails. As the system operates independent of a company’s Intranet, no access to company servers is necessary, so company data is never at risk.
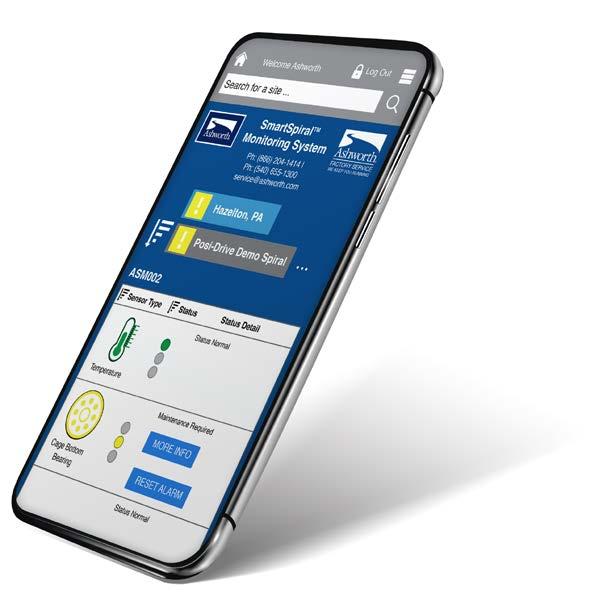
In this way, it can help minimize or entirely prevent spiral system malfunctions such as bearing failures, high belt tension, improper maintenance, motor failure, gearbox failure, etc. The SmartSpiral allows the operator to determine predictive maintenance priorities, thanks to the data reports it compiles. It clearly shows when parts of the system are changing, so that they can be addressed. For example, a failing bottom bearing can be seen via the reported alarms and be replaced before failure. “It enables planned downtime versus unplanned downtime that creates havoc with employees, product, and profits,” Trinch highlights.
The SmartSpiral System sets up a baseline for the system and looks for deviations. How to handle a case of a false alarm, though? “False alarms can sometimes occur, but we do our best to minimize them. Because data is presented in trend graphs, false alarms should show as
‘outliners’. Should multiple ‘outliners’ be present, an investigation of the issue should follow to verify the correct operation of the sensor,” the specialist recommends.
The solution can be retrofitted and implemented to match the production parameters and it immediately contributes towards minimizing unplanned, costly events that could disrupt operations. +++
© Ashworth