
3 minute read
Main principle: durable
Diane has developed a dimensionally stable peelboard whose surface consists of hard-wearing polymer. If needed, there is a peelboard suitable for every industrial line.
+Proofing boards have existed in the USA and also in Europe for a long time, but the processes were very much aimed at the artisan sector (wooden boards, plastic boards, cloths). However, requirements relating to stability and hygiene have become ever higher with the growth of industrialization in the area of proofing. Thus there is a rising demand in Europe for new boards, although the old “simple” boards still exist. Incidentally, the term “peelboard” originates from the English-speaking world.
The demand for peelboards is accelerating compared to the demand for baking trays. One reason for this is the trend towards baking on hearth or stone plates, even on a large scale. Cloths or fabric coverings are also in decline for hygiene reasons. The most important reason, however, is the opportunity to automate proofing processes by using loading and unloading systems for proofing carriers. The dimensional stability of the proofing carriers is a decisive precondition for this, and it is a requirement that is a matter of course for Diane.
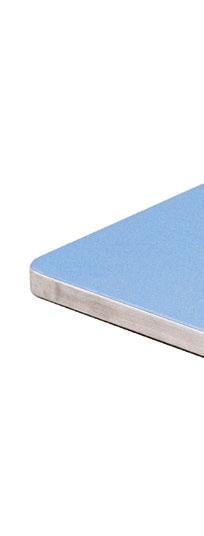
So that explains the increased emergence of peelboards, which is why Diane, already well-known as one of Europe’s most modern producers of trays and pans, is now launching two newly-developed peelboards. They will be offered under the Blue Board ® name. There is one shallow version with a double-sided worksurface and an aluminum frame, and one “high” version with stainless steel frames for fully automated plants.
American peelboards were initially simple wooden boards, cheap, with a tendency to deform, and not very hygienic. After that, plastic boards came into use, although these did not withstand the mechanical and temperature-related requirements in bakeries for very long. Nowadays, peelboards made by Diane consist of a frame, a dimensionally-stabilizing interior, and surfaces usable on one or both sides. If the boards are transported on roller conveyors, as a rule they are flat and both sides are usable. Recesses for stoppers or carriers are often necessary in factories that have automated transport from loading to the oven transfer point, which is why they have only one usable surface. There are certainly quality differences in the workmanship of the various components.
According to the company’s founder Roger Messio, Diane’s new board is the only one whose surfaces are cut from a special material. A material that completely prevents dough pieces adhering by means of different particle sizes and without a silicone or Teflon coating. “In addition,”, according to Messio, “our fabrication processes are designed to adapt the basic dimensions, the height and the fabrication of the boards precisely to any line and its requirements.”
The special surface material consists of acrylonitrile-butadiene-styrene copolymers (ABS), a plastic that combines mechanical stability and chemical resistance, and is often used for housings and other moldings, as well as for Lego bricks. Their stability can be marveled at in any child’s playroom.
As a rule, for shallow boards that are more likely to be moved by hand, the frames are made from a peripheral aluminum strip. Depending on the design of the line and/or loader, the choice for automated handling is stainless steel frames, which allow enough space underneath for stoppers or carriers.
In the case of the higher frames, an aluminum trough shaped according to requirements is first of all recessed into the finished frame. Into that goes an aluminum honeycomb structure which ensures that a 600 x 800 mm tray, despite its stability, weighs no more than 5.9 kg. After that, the surface material is glued on with a special adhesive that is commonly used in aircraft construction and can be exposed to a very wide range of temperatures without embrittling. Thus ABS withstands temperatures from -35°C up to +50°C.
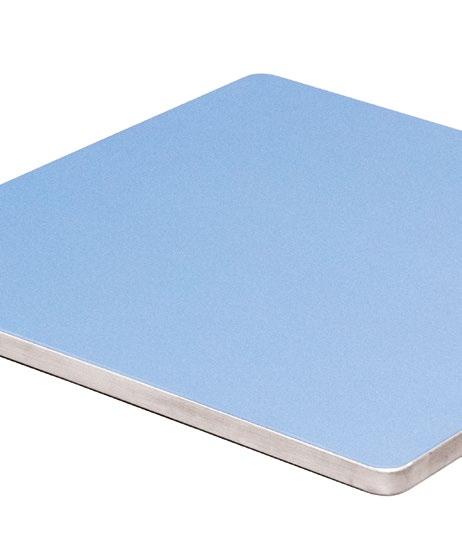
With particularly large trays, internal bracing ensures additional rigidity so they do not warp or distort. In the case of shallow trays, ABS is glued onto both sides of the honeycomb structure.
Such peelboards are usually brushed off and are then clean. Anyone who wants to use water to clean them or even to immerse them in a cleaning solution can also obtain watertight peelboards. In such cases, the frame and the lower trough are glued together. This stops any penetration of water. The frames can either be provided with codes for automatic recognition, or the peelboards are passed over an induction loop on the line that reads out a hidden internal code.
According to Messio, the request to develop particularly stable peelboards that are guaranteed to be flat came from customers and machine builders. Industrial plants in Switzerland, Germany Poland and Turkey are already running the Diane peelboards. +++
We Bundle The Power Of Elements

WHERE THE ELEMENTS ARE IN HARMONY WITH YOUR BREAD.
Follow us on our digital channels.
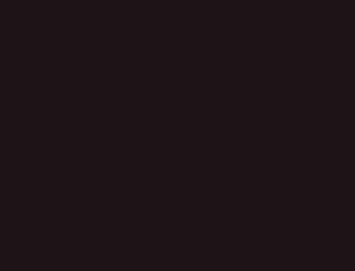
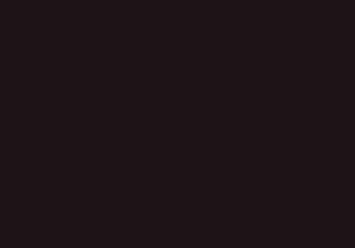