
2 minute read
SCHÖCK ISOKORB FOR ICONIC NESTLÉ FACTORY SITE REGENERATION
No other UK product for concrete-to-steel applications satisfies the necessary loadbearing requirements, or meets the current and future thermal performance required by building standards (Part L), than the Schöck Isokorb structural thermal break T type SK.
It is a complete system structural thermal break and is used widely on Block B, a collection of nine buildings which make up around a third of the 1400 hundred or so new properties at the Hayes Village development. This is an extensive regeneration programme in Hayes, West London and is built on the original site of the locally iconic Nestlé Factory, which dominated the area for some 80 years before production relocated to Derbyshire. Hayes Village is situated along the Grand Union Canal, surrounded by nine acres of green space and includes play areas and allotments.
The Schöck Isokorb range of structural thermal break solutions is the largest in Europe and in the UK helps projects meet full compliance with the necessary Building Regulations (and the impending Future Homes Standard criteria where relevant).
LEFT The restored art deco main Nestle building adjacent to Block B
Original features from the Nestlé factory, including one of the listed art deco style buildings, are carefully woven into the fabric of the new development and although all the buildings have distinct characteristics, the existing factory buildings have inspired the overall design. As a result, the nine buildings that make up Block B are broken up into a series of elements and layers, each of a different brick tone and although very different in character, have façades with common themes. As a counterpoint to the solid masonry walls which wrap the primary steel frame, the metalwork of the balconies is used as a feature to enrich the façades.
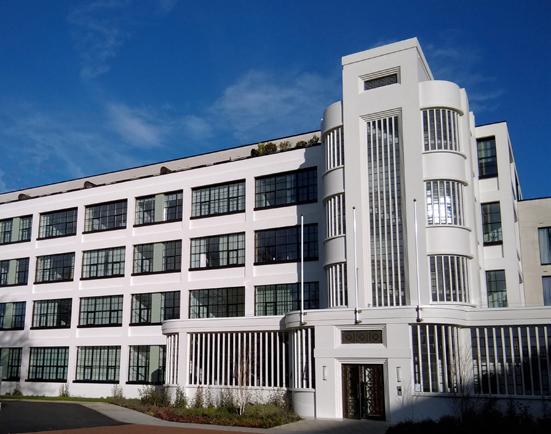
Minimising thermal bridging is critical
The entire project is built with sustainability in mind and minimising any risk of thermal bridging at the balcony detailing is critical for a number of reasons. Local heat loss will result in more energy being required to maintain the internal temperature of the building, while low internal surface temperatures in the area of any thermal bridge can cause condensation. This in turn is likely to result in structural integrity problems. Mould growth too is a possible risk, which in a residential situation can cause asthma and allergies. Incorporating the Schöck Isokorb T type SK minimises any chance of these outcomes, as it prevents the risk of thermal bridging between cantilevered steel constructions on reinforced concrete components.
A dependable and fully compliant product range
The Schöck Isokorb range of structural thermal break solutions is the largest in Europe and in the UK helps projects meet full compliance with the necessary Building Regulations (and the impending Future Homes Standard criteria where relevant). In addition to the Isokorb type used on this project, there are also so-lutions for concrete-to-concrete, steel-tosteel, renovation projects – and even a maintenance free alternative to wrapped parapets. All products have the security of independent BBA Certification, which provides NHBC approval. The tem-perature factor requirement (fRSI) used to indicate condensation risk at localised junctions, which must be equal to, or greater than 0.75 for residential buildings, is also easily met by incorporating the Isokorb.
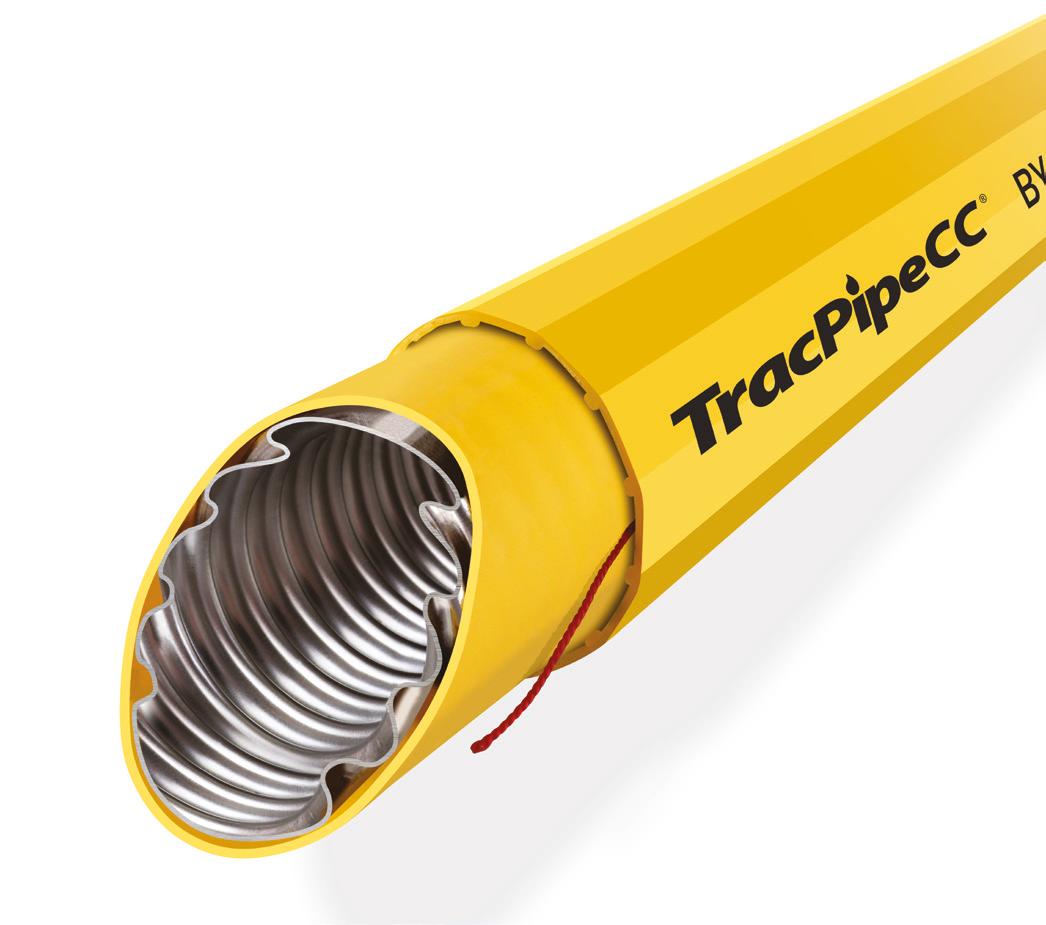
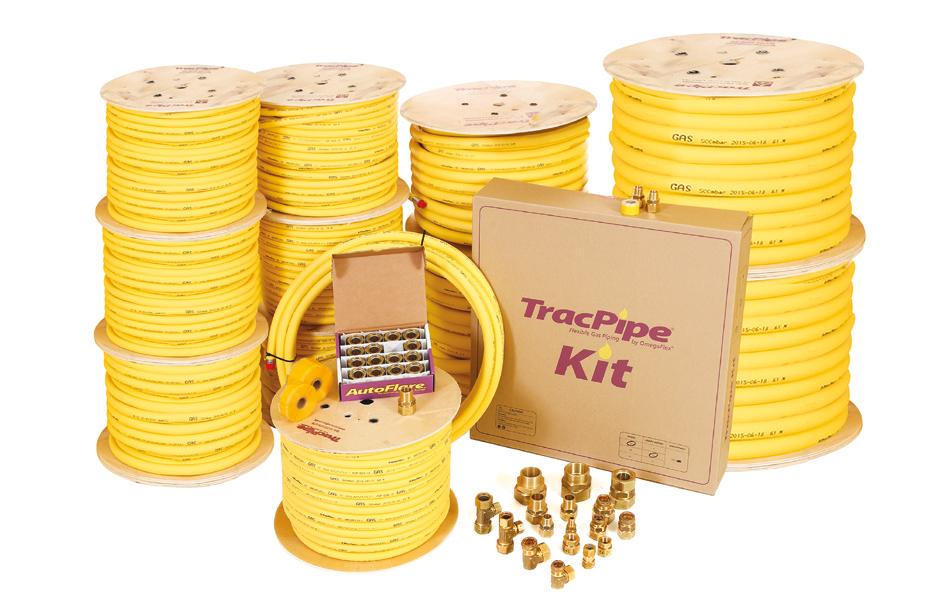
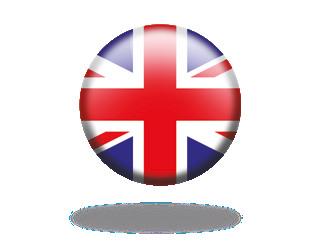