
3 minute read
IT RUNS IN THE FAMILY
from CL - July 2015
KORB WHALE still remembers when his workday began at 5 a.m. Like his father and his grandfathers before him, the Alma, Ont., dairy farmer would rise before dawn to herd cows into one of 12 milking stalls and attach them to the milking machine’s teat cups by hand—twice a day, every day of the year. Now, thanks to new farming technology, Whale can sleep till 7 a.m. while his 140 Holstein and cross-bred Norwegian Red cows are milked automatically by machines. As the cows wander freely through the barn, tracking necklaces monitor family their health and milking habits. it runs in the
Here’s how new technology is changing the way milk makes its way from Korb Whale’s farm to your table.
Advertisement
BY JENNY POTTER PHOTOGRAPHY BY ROBIN STUBBERT
(From far left) Three generations of the Whale family: Korb (holding Reagan), Kelley (holding Jack), Bruce, Rya and Deborah; cows enjoy their custom-mixed breakfast; the oldest barn on the farm, which houses calves; Deborah feeds a calf its mother’s milk; a cow enjoys a good back rub from an automatic scratcher.
The result: thousands of litres of omega-3–rich milk every day—something Whale, a seventh-generation dairy farmer takes pride in. “The milk quality is significantly better than it has ever been,” he says. “We’re doing the same thing we’ve always done—we’re feeding cows and we’re milking cows. We just do it at such a fine level now.”
Whale is typical of the modern dairy farmer—the pride he takes in his work paired with the advantages of new technology make all the difference in both the top-notch milk his farm produces and the quality of life he enjoys with his family. It’s a combination that helps ensure high standards for Canadian dairy products.
Meeting those standards used to be pretty labour-intensive. “You cleaned all the sta- bles by hand,” recalls Whale’s father, Bruce. “When I was really young, the milk was in milk cans that would be loaded onto a truck and taken to market.” Today, milk is piped directly from the cow through a filtration system, where it is immediately cooled to 4°C, to preserve quality and freshness, and housed in a stainless-steel tank. Between 7,000 and 8,000 litres of milk are picked up every two days and tested rigorously for any impurities before they’re accepted at the processing plant.
Despite the flexibility and efficiency that technology has brought to the business, Whale needs two full-time employees to keep up with the demands of farming. Every morning, for instance, one staffer mixes seven custom meals for the cows, depending on their health, age, milk production and lac tation stage. Whale’s parents, Bruce and Deborah, help feed the calves. “We are raising generations of animals,” he says. “They become part of your family.”
Whale’s human family, meanwhile, soaks up farm life and provides a playful distraction from work. His elder daughter, Rya, 4, loves animals, especially cows, while Jack, 3, is mad for tractors. “It’s a neat education for them to be around animals, machines and life in general.” That education takes a break at lunchtime, when staff and the whole family—including Whale’s wife, Kelley, and one-year-old Reagan—enjoy their midday meal together.
While dairy farming is how Whale and his father put food on the table for their families, they’re also helping nourish Canadians with the milk they produce every day. “We take pride in growing food and we take pride in growing quality food,” says Bruce. “It’s a societal responsibility.”
That responsibility carries on till 7 or 8 p.m., and even then, Whale can expect the occasional text from the barn computer to come check on a machine or a cow. “This isn’t just a business and a lifestyle,” says Whale. “We take care of these animals and we care about them.”
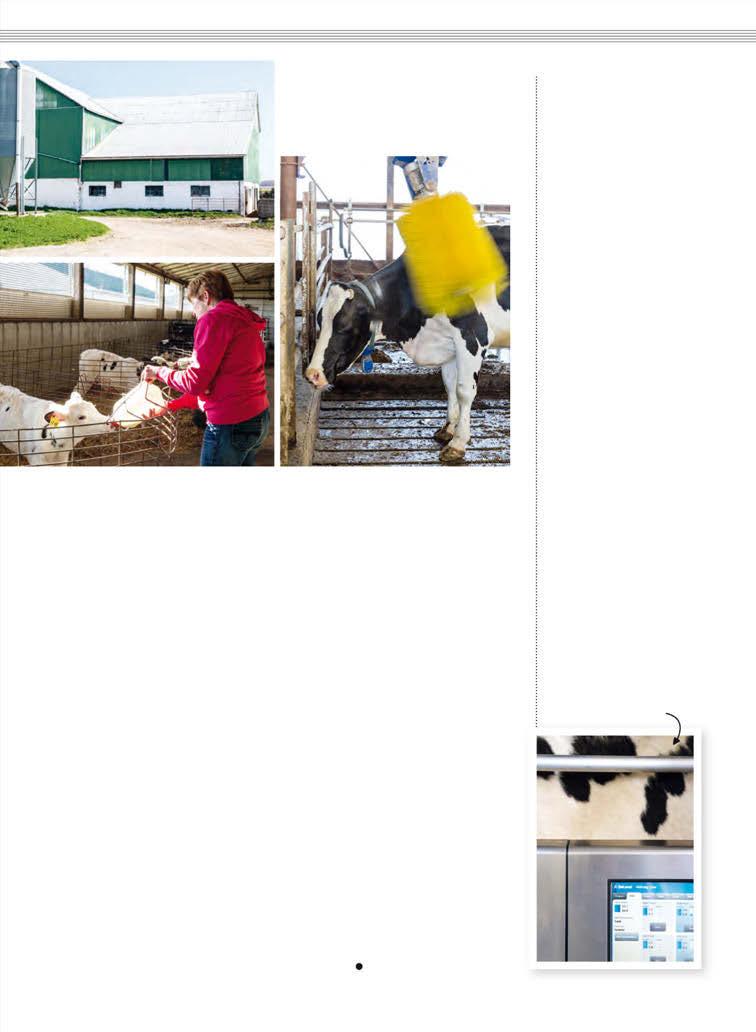
MAKING MODERN MILK
NUTRITIOUS AND FREE FROM ADDED HORMONES
MILKING THEMSELVES
HAPPY COWS
WEARABLE TECHNOLOGY
The high-tech milking machines record the details of each cow’s milk production and health.