
1 minute read
ELECTRICAL DRIVES
Industrial servos, 300 W
The pictured experiment stand is not included in this equipment. It can be added on request for an extra charge.
DC servos have a wide range of applications, highly dynamic control was only possible with them for a long time. In many applications, they have been replaced by permanently excited synchronous machines. This is because of the higher maintenance cost and lower efficiency of direct current machines. A modern, angle-oriented speed control requires an incremental recording of the rotation angle.
The learner analyses the set-up and function of a DC servo drive on the DC drive. Measurements and calculations are used to attempt to optimise the drive for its applications.
Objectives
Optimising control loops
2 and 4 quadrants control
Static speed control
D ynamic speed control
Highly dynamic speed control
Position control
Step response
Electrical Drives
Industrial servos, 300 W
AC servos with asynchronous machines are the cheapest solution for speedcontrolled drives. They are, however, not as dynamic as direct current machines or permanently excited synchronous machines. One cause for this is the electric time constant from the stator-rotor constant. Another is the dependence of the torque on the slippage, which has a dampening effect on acceleration.
The set-up of an AC servo with an asynchronous machine is analysed. Measurements and calculations are used to attempt to optimise the drive for its applications
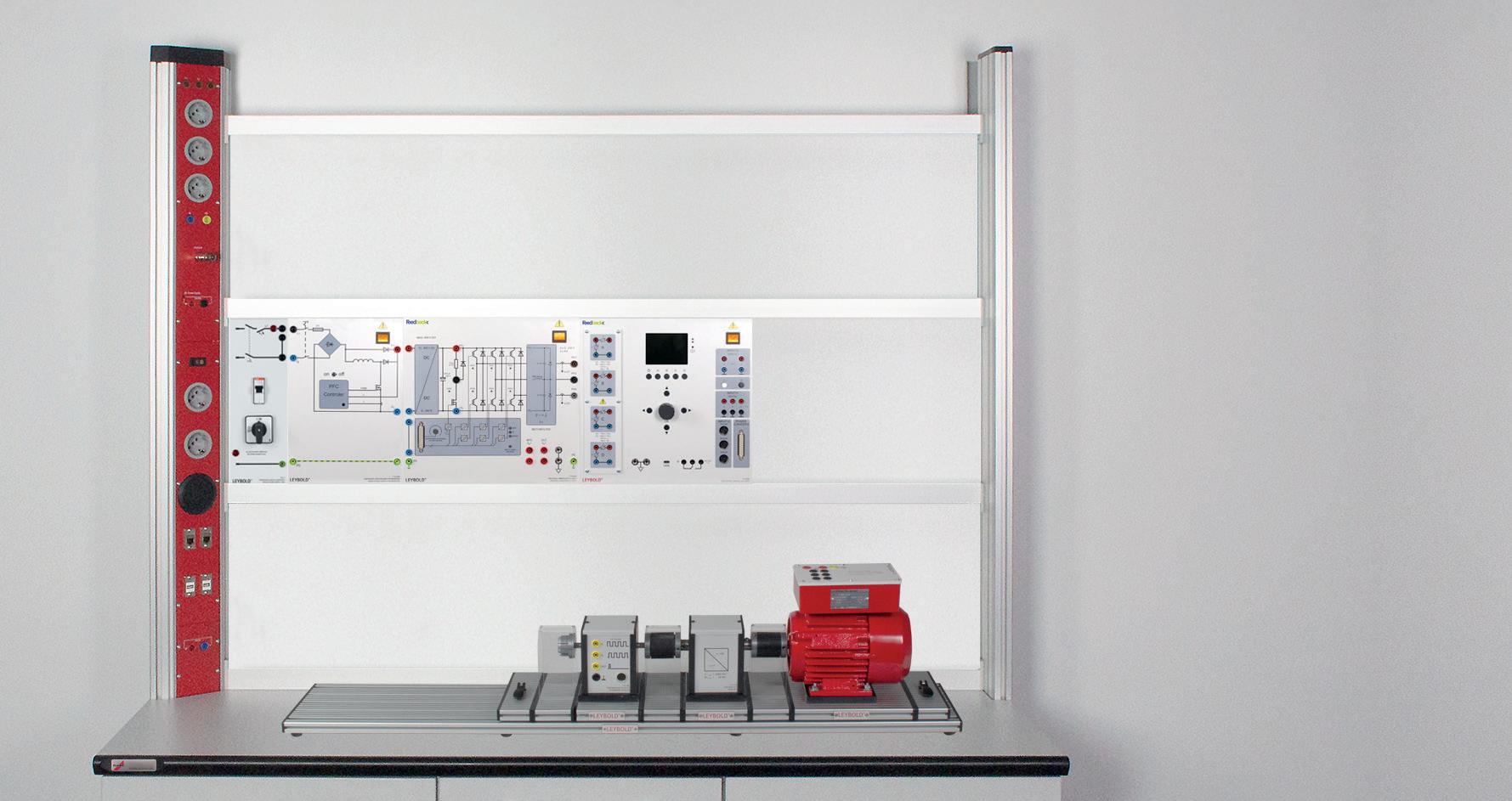
C alculating the control difference
A nalysing loads with step of reference variable
A pproaching stability limits