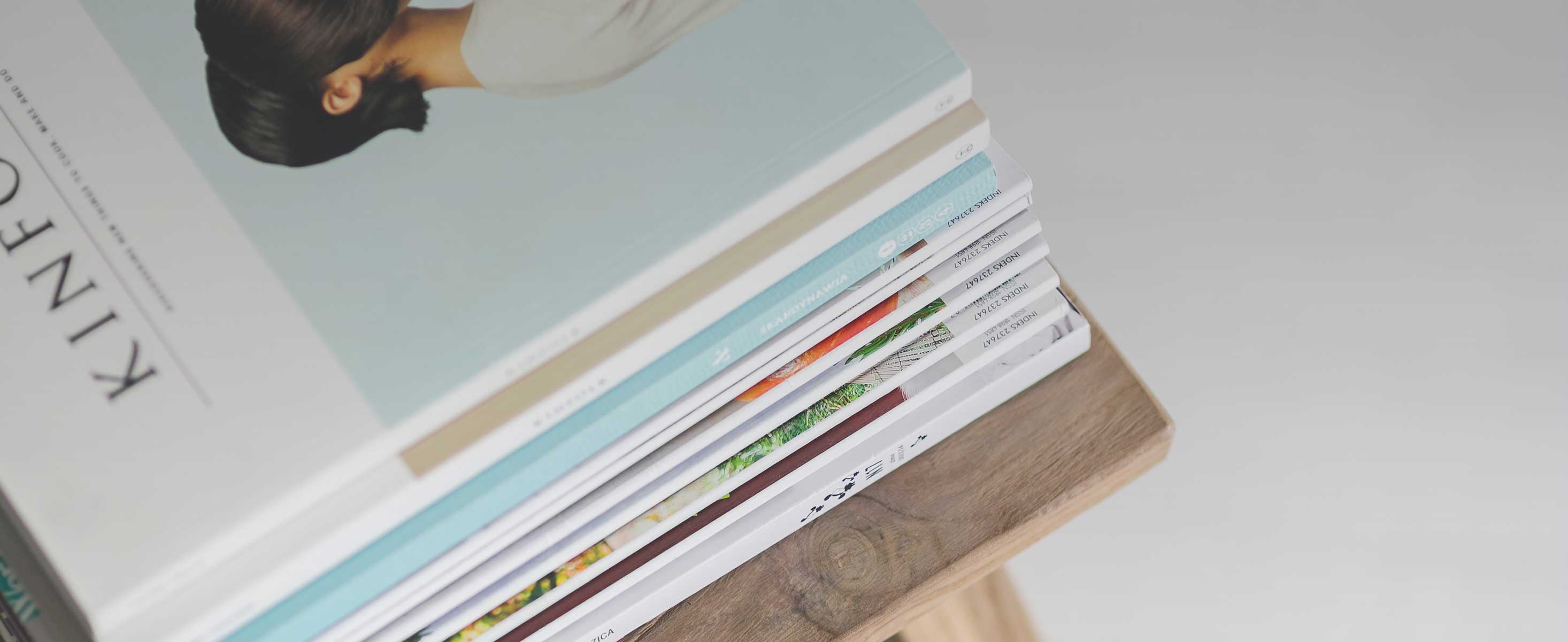
7 minute read
Feature
Labor of Love – Part 2: Addressing Labor Shortages and Factors Affecting Business Strategies
By Alicia L. Rihn – Assistant Professor in the Department of Agricultural and Resource Economics at The University of Tennessee
Advertisement
Amy Fulcher – Professor in the Plant Sciences Department at The University of Tennessee
and Anthony LeBude – Professor in the Horticulture Department at North Carolina State University
Labor continues to be a challenge in the U.S. including the green industry as unemployment rates are near 3.5% (U.S. Bureau of Labor Statistics, 2022). Our first article in this two-part series (see the Fall 2022 Tennessee Greentimes issue) addressed labor trends in green industry firms for the U.S., the five-state region surrounding Ten nessee, and the state of Tennessee. Overall, there was a decline in the number of employees reported across the industry. To help address this challenge, this article focuses on actions taken by green industry firms and potential strategies to address labor shortage issues. Results from two national studies are presented. The first study was conducted in 2019 and asked firms about their employment practices in 2018. The second study took place in 2021 and asked about employment practices in 2020.
Several actions that green industry firms reported they had taken to address labor shortages in 2018 were identified (Figure 1). In the U.S., paying higher wages was the primary action taken by green industry firms (40% of the sample; green blocks), followed by nothing (34%; blue blocks), adopting labor-saving technologies (25%; yellow blocks), training employees to improve skills (22%; gray blocks), other actions (13%; orange blocks), and adding employee benefits (9%; peach blocks). In the five-state region (GA, KY, NC, SC, TN), similar trends were observed. However, doing nothing, adopting labor-saving technologies, and training employees to improve skills were more closely distributed at 46%, 45% and 44%, respectively, with the five-state region training employees twice as frequently as was observed nationally. Additionally, other actions and adding employee benefits were both being adopted by 31% of the sample, more than 2.4 and 3.4-fold greater, respectively, than was observed among the national response. A different frequency was observed for Tennessee firms. Paying higher wages was still the most often used tactic at 51% of the sample, followed by adopting labor saving technologies (48%), training employees to improve skills (47%), doing nothing (45%), adding employee benefits (45%), and other actions (32%). Tennessee firms are adding employee benefits at a 5.0 and 1.5-fold greater frequency than national and regional firms. These results suggest that firms in Tennessee and the five-state region may have lagged behind the nation for creating competitive benefits packages that can attract and retain employees, yet now are making gains.
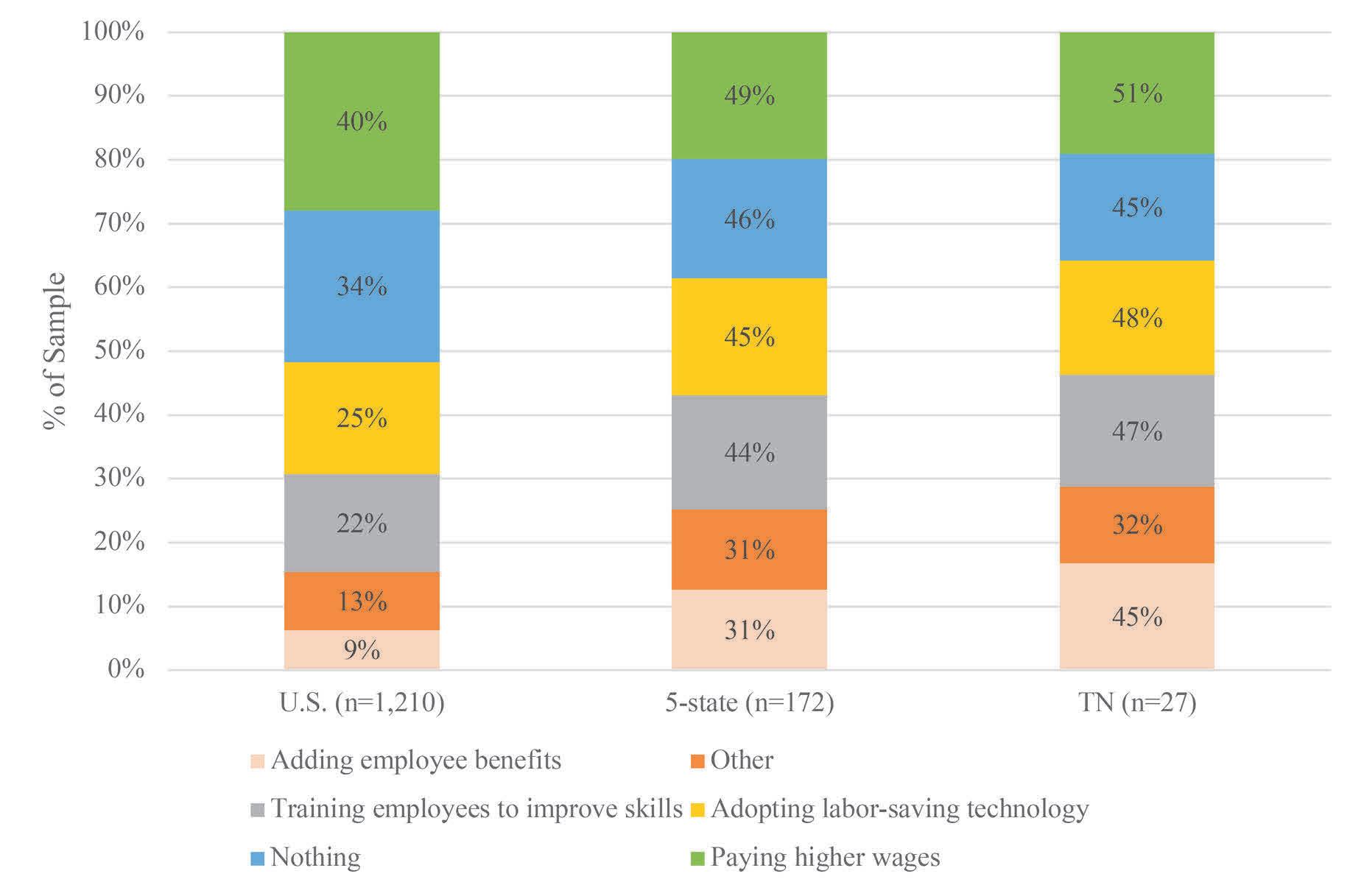
Figure 1. Actions Reported to Have Been Taken by U.S. Green Industry Firms in 2018 to Address Labor Challenges. States represented in thefive-state region include GA, KY, NC, SC, and TN.
The 2021 study, conducted for the 2020 season, provided additional options for nursery growers to explain actions that they had taken to address labor concerns. Consistent with the previous study, U.S. nurseries indicated that paying higher wages was the primary action taken to address labor issues at 66% of the sample. Fifty-six percent of the sample indicated they were adopting labor-saving technologies, followed by training employees to improve skills (45%), reducing production of labor-intensive crops (38%), adding benefits (29%), adopting LEAN processes (28%), shifting high-skilled labor to more low-skill/manual tasks (27%), applying or already using H-2A labor (27%), putting expansion plans on hold (23%), increasing outsourcing (21%), and scaling back the operation (14%). Approximately 26% of respondents indicated that they were not experiencing labor scarcity. In 2020, fewer firms reported “doing nothing” compared to the prior survey, while paying higher wages and adopting labor saving technology were reported by more than half of firms. The change in response may be due to firms adopting strategies at a greater frequency in 2020 than in 2018 or could reflect practices shared by a different sample of respondents. Anecdotal observations support that these changes are occurring across nurseries as they attempt to fill numerous vacant positions.
In the 2018 study, U.S. green industry firms provided a gauge for the level of importance that the different factors had on their business strategies. They indicated importance using a five-point scale where 1 represented “not at all important” through 5 that was a “very important” part of their business strategy. Importance levels differed within the U.S., five-state region, and Tennesse1). Regardless of location, market demand and weather uncertainty were rated as most important, followed by own managerial expertise, labor costs, competition/price undercut ting, and ability to hire competent hourly employees. In Tennessee, water supply, environmental regulations, and other governmental regulations were all rated as moderately important. In the U.S., these factors were rated with slightly lower importance. In the five-state region, water supply was viewed as moderately important, but both types of regulations were only slightly important. Other factors that were rated slightly important across the areas were balance of power with buyers/customers, land, ability to higher competent management, equity capital, debt capital, and balance of power with suppliers/vendors. Market uncertainty may influence adoption of automation. While many growers have some capital available for investment now due to strong demand during the pandemic (McClellan, 2021), anticipated uncertain market demand complicates investing in automation and making expensive infrastructure changes often needed to accommodate new equipment. Many firms invest in automation with plans to increase production. Even the threat of demand decreasing, such as from an economic downturn, may alter decision-making.
Based on these findings, the matrix in Table 2 was developed as a decision aid tool for growers who are exploring their options to address labor challenges. Options broadly fall into three categories: those that make more efficient use of a limited work force, those that aim to recruit or retain labor, and a third category that addresses new or alternative labor supply. The matrix provides an overview of how these different actions could impact business outcomes, including recruitment and maintaining staff, company culture, performance, expense, infrastructure changes, and long-term sustainability. Tennessee nursery owners and managers can utilize this tool when navigating the options for addressing an insufficient labor pool.
Summary
Although labor challenges are occurring throughout agriculture and other industries, many green industry firms are being proactive and taking steps that are intended to mitigate potential labor shortages. To date, green industry firms primarily rely on employee-related actions such as increasing wages and providing professional development opportunities (i.e., training) and production efficiency and labor reduction-related actions (i.e., adopting technologies, reducing production of labor-intensive crops). Tennessee nurseries interested in making capital improvements that include purchasing labor-saving automation can apply to the Tennessee Department of Agriculture’s (TDA) Tennessee Ag Enhancement Program to participate in the 35% cost share program. Growers wishing to train existing or new workers can refer employees to the University of Tennessee’s (UT) Tennessee Master Nursery Producer (TMNP) programs. Pending application approval, UT and the TDA partner together to offer enhanced levels of cost share to growers with TMNP certification. Given the diversity of green industry firms and options available to them, each operation needs to carefully consider what they can implement as long-term strategies to attract and keep good employees as well as supplement the insufficient workforce available through automation, other technologies, or an alternative work force supply. An important note is that economic conditions are continually changing, and that these conditions also impact consumer demand for ornamental plants. At the time of these surveys, the economy was strong and demand for ornamental plants was high. Firms should continue to monitor the economy and adjust production practices to accommodate changes.
Acknowledgments and Resources
This research was supported by USDA SCRI grant #2020-51181-32137 and USDA National Institute of Food and Agriculture, Hatch projects TEN00581 and TEN00575 and NCState02809.
McClellan, M. 2021. Money matters. Nursery Management. GIE Media Inc. https://www.nurserymag.com/article/how-are-nurseries-spending-cash/
Rihn, A.L., A. Fulcher, H. Khachatryan. 2021. A ten-year review of the southeast U.S. green industry, part I: Labor and firm characteristics. University of Tennessee Extension Publication W 1026.
Rihn, A.L., A. Fulcher, H. Khachatryan, A. LeBude, L.A. Warner, S. Schnexnayder. 2022. A ten-year review of the southeast U.S. green industry, part II: Addressing labor shortages and internal and external factors affecting business strategies. University of Tennessee Extension Publication W 1080.
Velandia, M., A. Fulcher, K. Jensen. 2021. Labor use and challenges faced by Tennessee nursery and floriculture producers. University of Tennessee Extension Publication W 984. https://extension.tennessee.edu/publications/Documents/W984.pdf