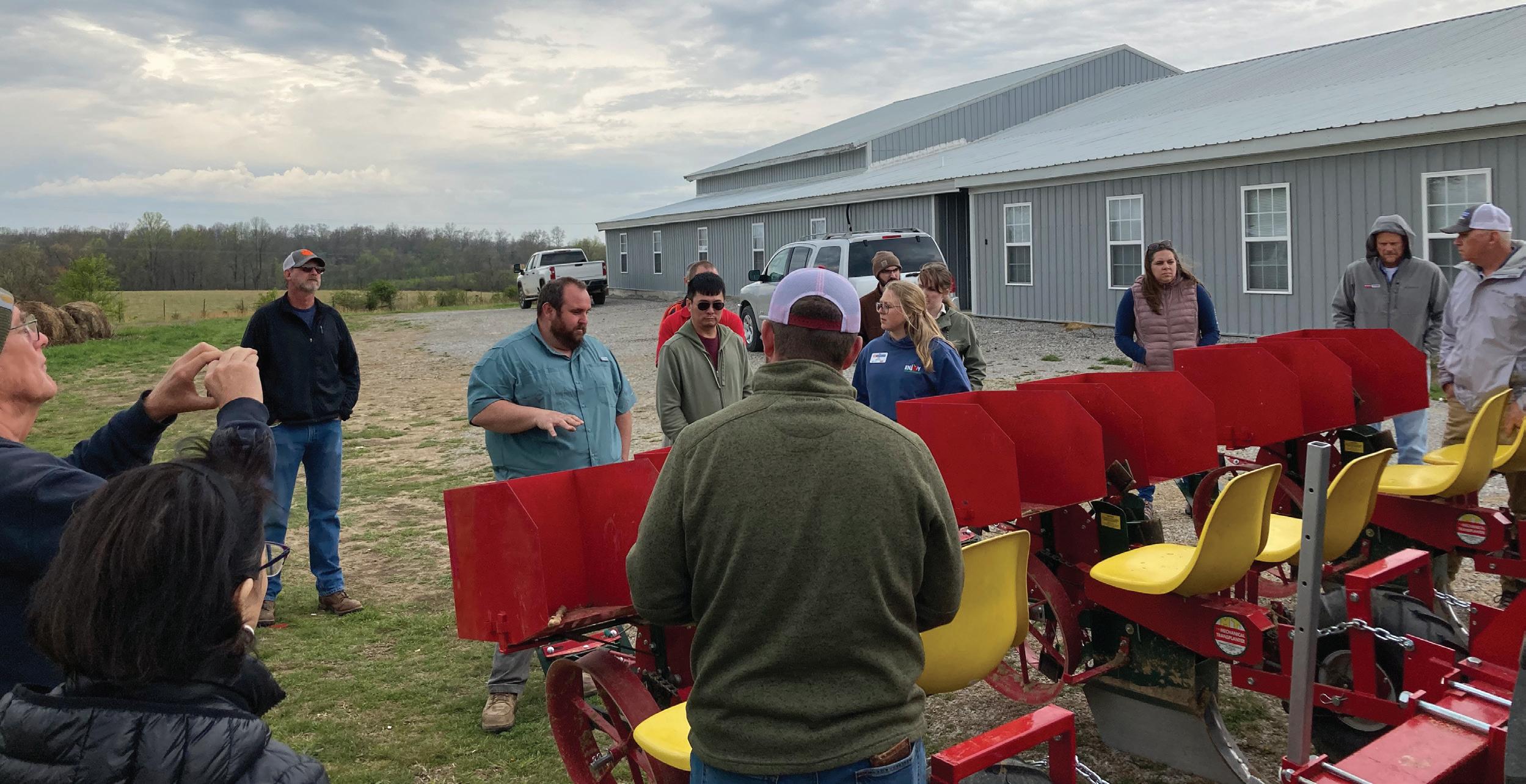
11 minute read
Cover Story
From Chasing to Solving Labor Scarcity
Part II: Advances in Automation within Tasks for Field Production
Advertisement
By Amy Fulcher 1,a, Alicia Rihn 1,b, Laura Warner 2, Anthony LeBude 3 , Margarita Velandia 1,b, Natalie Bumgarner
1 University of Tennessee: a Department of Plant Sciences, bDepartment of Agricultural and Resource Economics, c School of Natural Resources; 2University of Florida, Department of Agricultural Education and Communication; 3North Carolina State University, Department of Horticultural Science
Athree-part series of articles was developed to provide information to the Tennessee nursery industry and the automation manufacturers who serve the green industry that could guide them in the development, commercialization, and adoption of automation options. The overall goal is to help prepare nurseries for an increasingly labor-scarce future. In Part I “Current Automation Adoption by the U.S. Nursery Industry,” use of a range of container- and field-production automation was described. In Part II “Advances in Automation within Tasks for Field Production” we evaluate the portion of a given task that is automated, focusing on field production. In Part III “Outcomes from Adopting Automation and Perceived Helpfulness Analysis,” we will examine nursery producer perceptions of helpfulness associated with specific pieces of automation and outcomes from using automation. In Part II, like in Part I, we use automation to refer to both automation and mechanization interchangeably.
The portion of a given nursery task that was automated varied by task. The most automated field production task was harvesting, which was 56% automated (Table 1). Even harvesting bare-root liners can be very physical labor, especially when the soil is wetter than desired (Figure 1). Considering the physical labor required to dig a tree by hand and the finished weight of a balled and burlapped tree, it is not surprising to see automation incorporated into this task. Yet there is room for increased automation, considering that roughly half of the task is still accomplished with manual labor. The next most automated task was weed management, which was 51% automated. Tractors and ATVs are already in use in field production, and a wide production block spacing is already established to accommodate these vehicles. These wider aisles also accommodate the use of mechanical weed control and sprayers making post emergence herbicide applications.
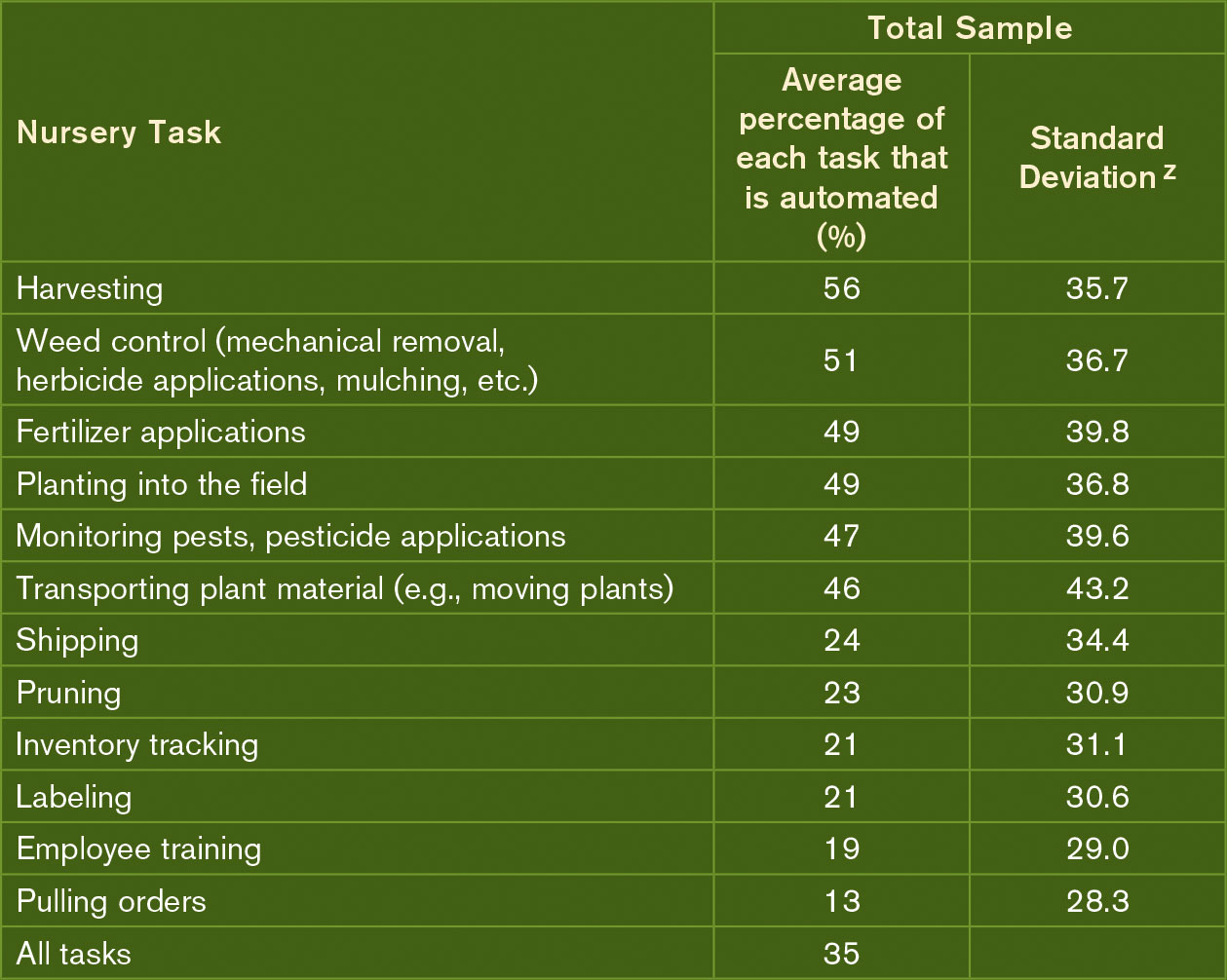
Table 1. Percentage of different field nursery tasks that respondents stated were automated in 2020.
z Standard Deviation (the variability observed among task automation estimatesthat were reported by survey participants)
Monitoring for pests and making pesticide applications were collectively 47% automated (Table 1). The reported percent of task automated likely reflects the use of air-blast sprayers, other tractor PTOoperated sprayers, and the Enviromist post-emergence herbicide applicator (Micron Group, Bromyard, Herefordshire, England). Mixing and filling tanks and the need to operate tractors and ATVs that pull sprayers likely explain the 53% of this task that is performed by workers.
Currently, there is no commercialized system for automated pest scouting in nursery crops. Although technological advances, such as image recognition and machine learning, make this a possibility in the near future. For example, Dr. Mahmud, a TSU agricultural engineer, recently helped develop an experimental automated fireblight detection system. In Part I, we saw that sprayers equipped with Smart-Apply® Intelligent Spray Control System™ (Smart Apply Inc., Indianapolis, IN) and SmartSpray (Durand Wayland, LaGrange, GA) already are in use at just 3% of nurseries. These technologies, therefore, represent a commercially available but under-adopted technology. An automated herbicide applicator for nursery production also is currently in development at Carnegie Mellon in partnership with Hale and Hines Nursery.

Figure 1
Photo Credit: Amy Fulcher
Planting and fertilizer application were both 49% automated in field nurseries in 2020. While a mechanical planter is often used to move soil, many laborers are still required to plant a crop. Workers cut bundles of bare root liners and prune roots or remove liners from containers to prepare them for planting. Other workers transport liners to the planting site, hand prepare liners for workers on the setter, place the liner in the furrow, straighten liners and firm the soil around them. One additional worker operates the tractor that pulls the setter. Some growers are adopting larger planters to achieve greater efficiency; however, these planters require more people working to prepare and simultaneously plant the increased number of liners (Figure 2). Therefore, while efficiency is gained and more plants can be planted in the same amount of time, the reliance on labor is ever-present. Even an applicator that broadcasts or applies a band of fertilizer requires an operator to drive and refill the hopper. Depending on the choice of fertilizer selection and its potential expense, for example high-cost controlled release field fertilizers, the application method may rely entirely on manual labor to provide a per-plant application made with a spoon or cup, similar to applications in container production.
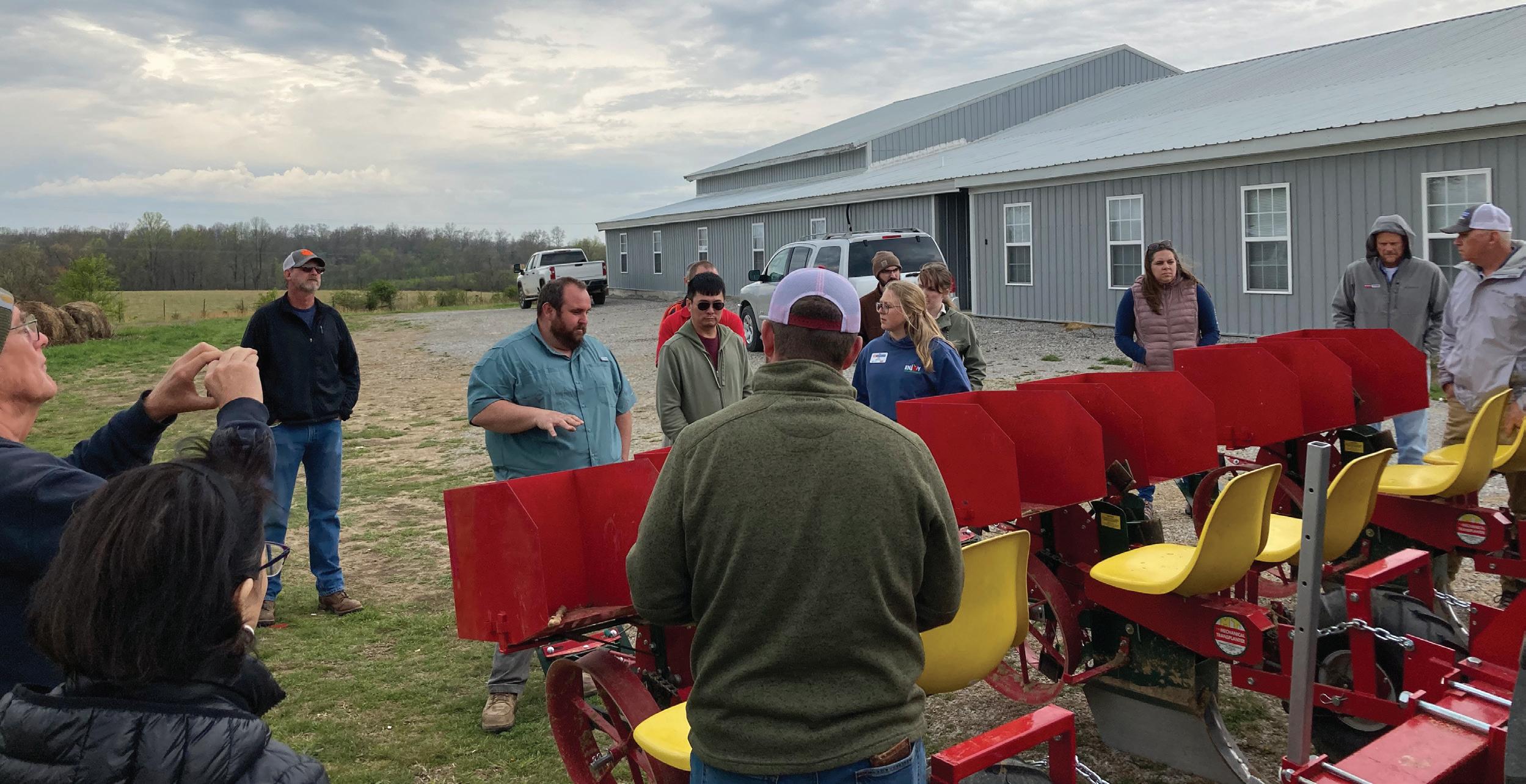
Figure 2
Photo Credit: Amy Fulcher
Transporting plant material was 46% automated. Tractors pull wagons, however, wagons are usually loaded and unloaded by hand. Tree Boss® (Tree Equipment Design Inc, New Ringgold, PA) and other articulating ball-handling equipment may expand the plant handling tasks that can be automated. Portable conveyers have been adopted rapidly in container production and may have a place in transporting bareroot liners considering their weight is not unlike container crops (See Below).
••••••••
Conveyers… They Are Not Just for Container Nurseries
An Ohio, U.S. nursery producing bare-root nursery crops is using telescoping conveyers (MaxxReach®, FMH Conveyers, Jonesboro, AR) at their docks to eliminate the need for workers to walk each armload of liners to the front of the shipping container, making this task more efficient. In much the same way that portable racks have improved labor efficiency required to move groups of small container crops, telescoping conveyers and similar technologies have the potential to dramatically improve loading efficiency of field-grown crops. Sources: McClellan, 2018a and Spirgen, 2019
••••••••
How a Tennessee Nursery’s Investment Paid Off Big
Turner and Sons Nursery is a bareroot and container operation in Tennessee, where labor is at a premium and for which labor costs recently nearly doubled. That caused John, Terri, and sons Lee-Allen and John Adam, to start thinking about more efficient ways to complete tasks. They recently acquired four tying machines (Figures 3 a and b) at a cost of $7,300 each that bundle trees approximately four times as fast as their workers could bundle by hand. The tying machines allowed the business to re-allocate 2-3 workers from their limited workforce to assist with grading or harvesting trees. While expensive, the tying machines have helped Turner and Sons Nursery extend their limited workforce and complete tasks on time.
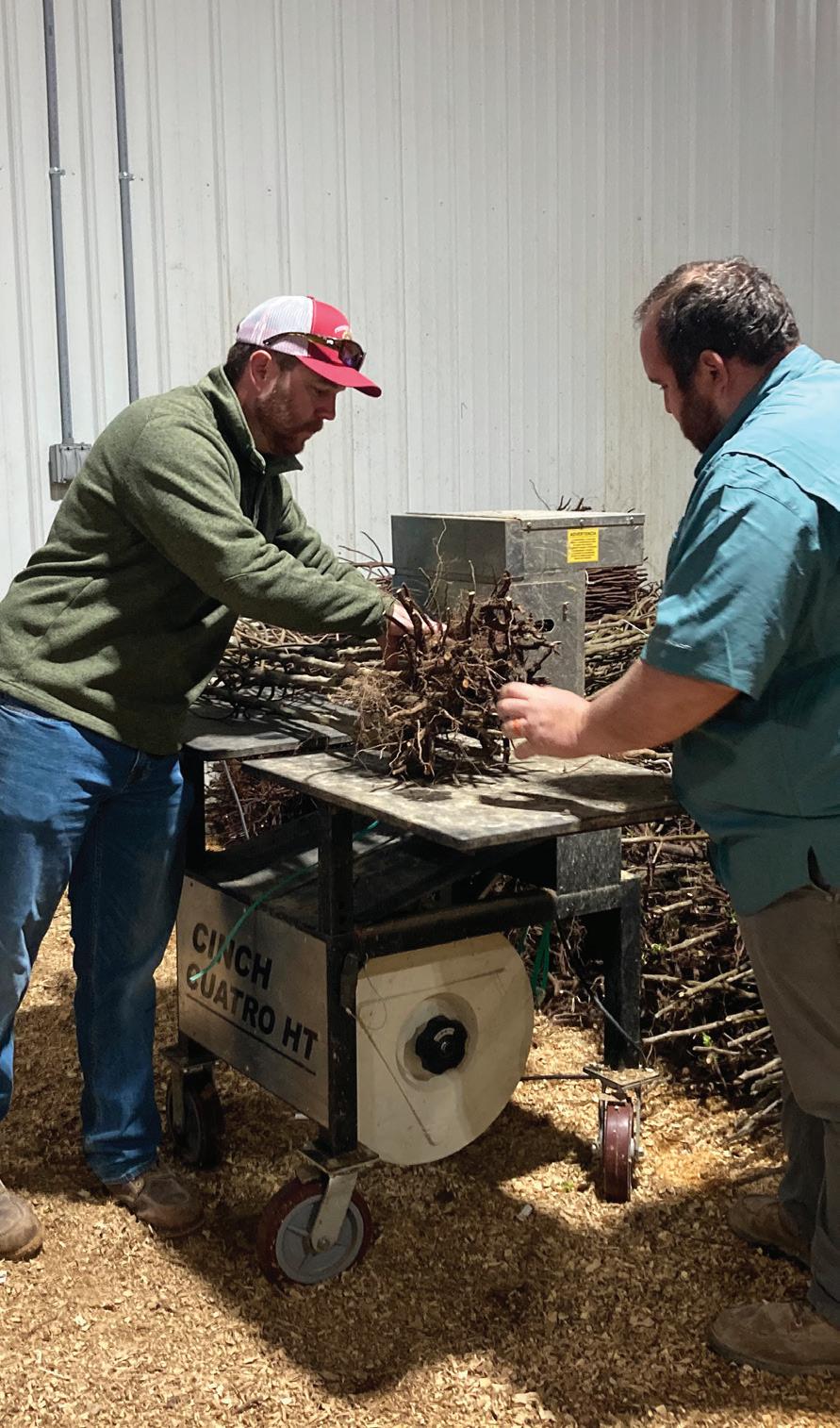
Figure 3a
Photo Credit: Amy Fulcher
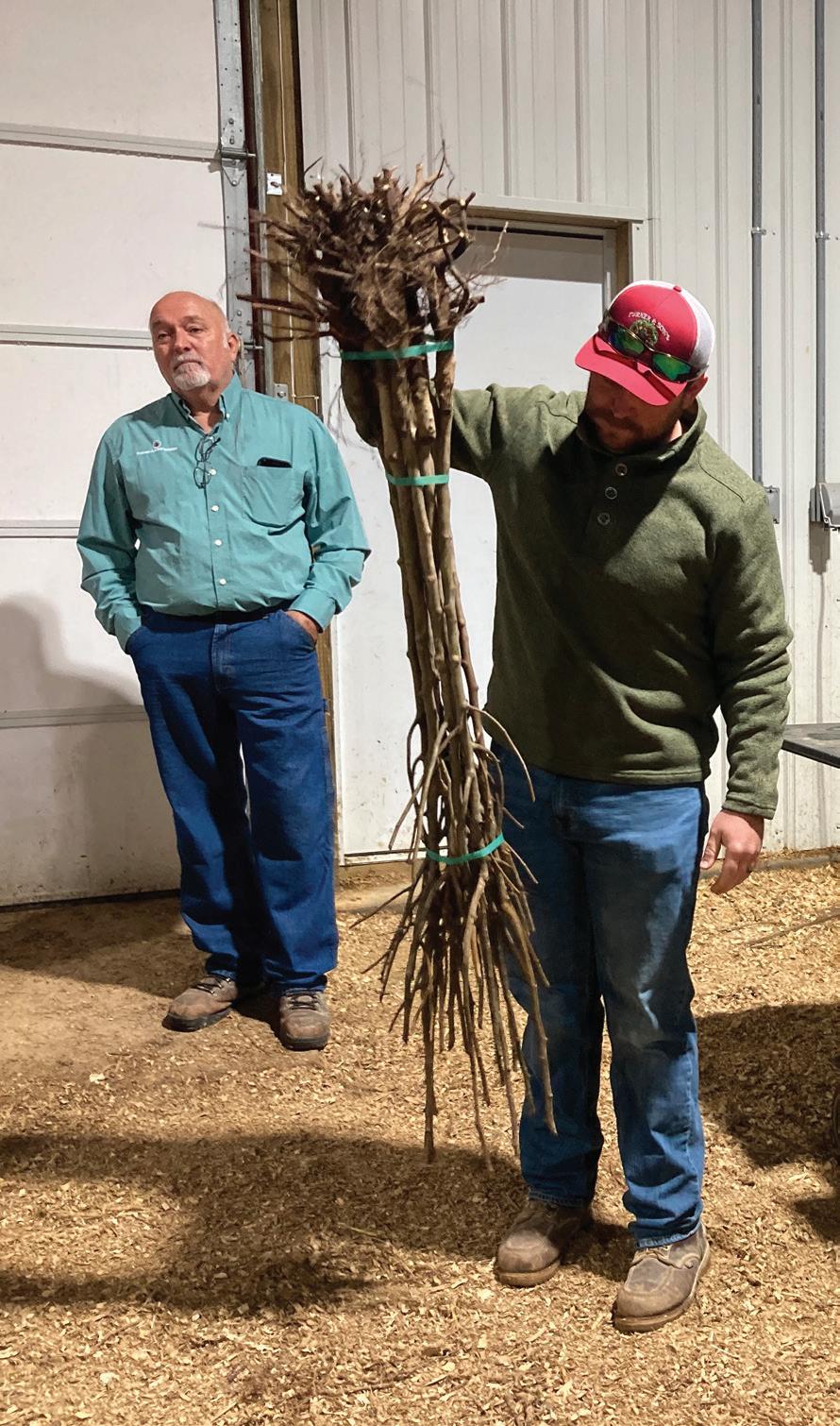
Figure 3b
Photo Credit: Amy Fulcher
••••••••
Root and Shoot Pruning Advances Save Labor, Money, and Reduce Injury Hazards
An Oklahoma nursery now uses a custom root pruner instead of hand pruning bare root liners that has helped their operation reduce the number of employees required for that task from roughly 27 employees to three. At Hale and Hines Nursery, a single employee with a gantry-style pruning machine (Figure 4, page 22) is now able to prune as many plants as four workers. After adopting this gantry-style pruner, pruning expense was reduced by approximately $0.10/plant. This pruner had a pay-back-period of two years based on use on just one of the two crops it is used to prune. These pruning machines demonstrate the effectiveness of automation and mechanization in addressing the nursery labor shortage. In both cases, nurseries were able to re-allocate workers to other, non-automated tasks. On a recent visit to Cherrylake Tree Farm in Groveland, Florida, nursery workers were using battery operated pruners with a protective glove to simultaneously eliminate hand and wrist strain while also protecting the worker from severing fingers. Workers also stated they felt they could prune faster and make a cleaner, better, more controlled cuts with the electric pruners. Similar pruners include Infaco Electrocoup Battery Pruner F3015, and Bahco Electronic Pruner BCL22, and Zenport EP2. The Infaco wired model costs approximately $1,300 and requires charging the batteries and sharpening blades about every three days.
••••••••
Pruning is 23% automated at field nurseries in the U.S. (Table 1), similar to container nurseries (25% automated). Most nurseries have crews of several workers who prune blocks of shrubs at a time. Many crops must be pruned multiple times per season. With a reduced workforce, there is an opportunity to increase the portion of this task that is automated and then reallocate that labor to tasks that are not easily automated. Additionally, in listening sessions, growers listed pruning as a particularly helpful task to automate given their expectation that improved efficiency could increase timeliness in completing the task, aid in improving crop uniformity, and enhance predictability in crop scheduling (e.g., to promote flowering during a targeted sales window). Some nurseries have experimented with automated pruning systems. For example, motorized, gantry-style mechanized pruners require two workers: a driver and a worker walking behind with shears to remove any missed branches (Figure 4). Other growers have custommade or modified large combine-style multi-row pruners that better meet their production needs.
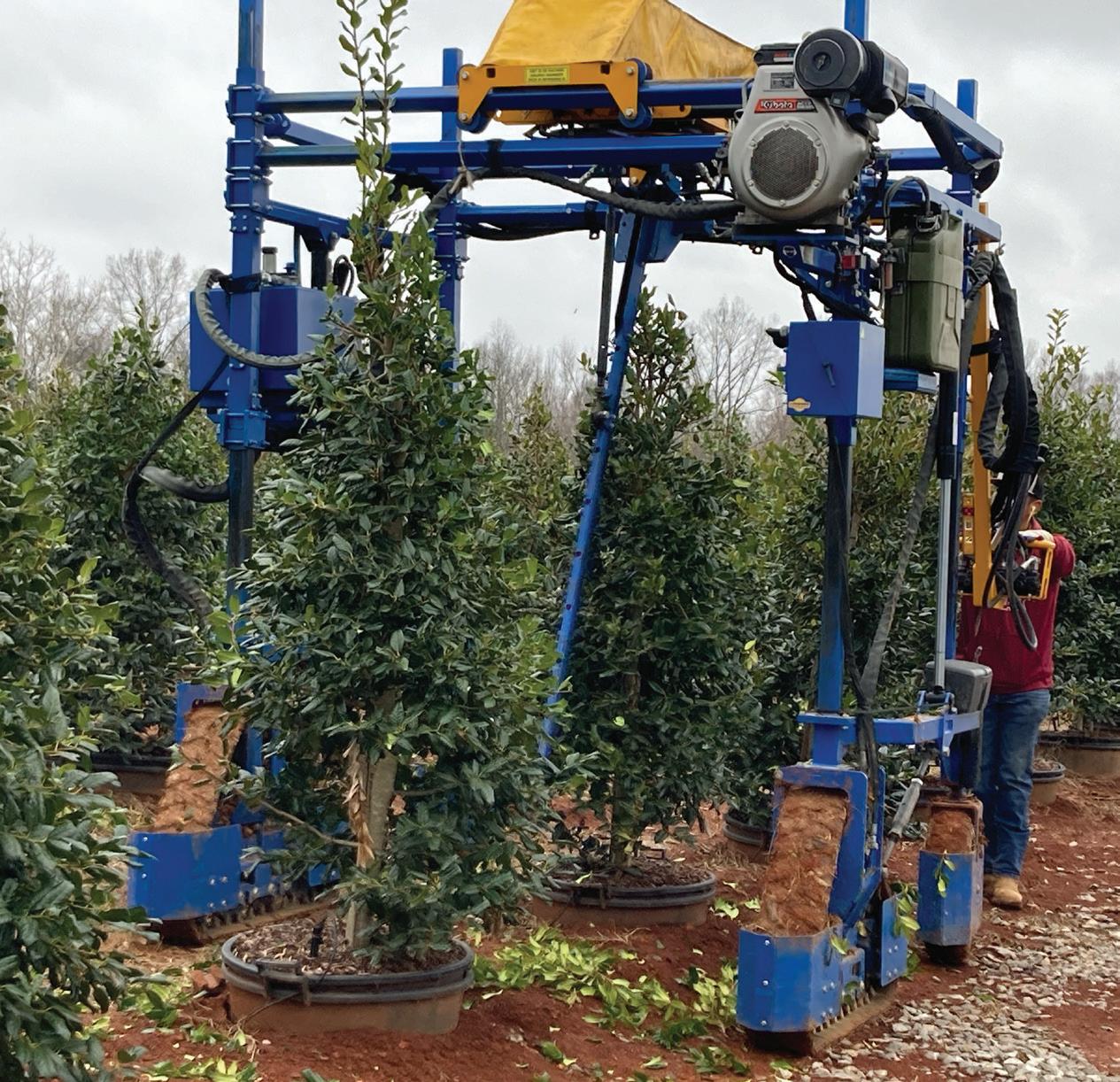
Figure 4
Photo Credit: Amy Fulcher
Employee training, labelling, pulling orders, and inventory tracking tasks each are less than 21% automated. Some online programs exist for training employees, including various pesticide certification trainings, and programs such as the University of Tennessee Original and Advanced Tennessee Master Nursery Production programs www. tnmasternursery.com. Labeling is a highly repetitive, low skill task. Automated labelling could allow workers to be placed in more enriching tasks that add more value to the crops, possibly aiding in worker retention. Inventory management requires years of experience to correctly identify plants, gauge their health, and assess additional growth that will occur before harvest. Repeated counts and the changing status of individual plants due to sales and changes in health and size make inventory assessments a time-intensive task. Recently, container producers have experimented with sensors connected to a monitor that detects and accounts for each plant as it is potted (ScoreBoard System, AgroNomix, Oberlin, OH). This technology could be adapted for field production and include GPS location of crops. Currently, Smart Guided Systems (Indianapolis, IN) offers a laser-based inventory system that can be mounted on an ATV or tractor and detects individual plants in the field. Other image-based technologies that may set the stage for counting the number of plants at a nursery or in a given production block include research by Dr. Hao Gan, UT Agricultural Engineer, and collaborators who developed experimental systems that detected both fruit and flowers. Pulling orders is just 13% automated and, like inventory, represents a task that integrates plant identification skills, discerning plant quality and grade, calculating anticipated future growth, and tagging. The judgment-based skills may be harder to automate. Collectively, the overall percentage of automation for all field production tasks is low at 35%, an amount similar to automation in container production (33%). Laborers are needed in nurseries to ensure the quality of the plants produced and perform tasks that require a significant amount of judgment or are otherwise difficult or expensive to automate. Likewise, tasks may be impractical to adopt due, for example, to infrastructure constraints. However, automation offers an opportunity to alleviate the labor strain and aid in production efficiencies, reduce employee injuries and physical strain, improve worker satisfaction, and maintain quality standards of the end products. This opportunity has never been greater because more technological developments and automated products are being introduced each year. University scientists, Extension personnel, and engineers are working with industry stakeholders to better integrate automation technologies in nursery production and ultimately help nurseries remain sustainable for the long-term. This is an exciting time to be in the nursery industry!
References and Additional Resources
LEAP Labor, Efficiency, Automation and Production. Virtual Nursery Automation Tours. https://www.nurseryleap.com/virtual-nurseryautomation-tours.html
McClellan, M. 2018a. Ahead of the curve. Nursery Mgt.: GIE Media, Inc. https://www.nurserymag.com/article/willowbend-nurseries-automation/
McClellan, M. 2018b. Don’t wait, automate. Nursery Mgt.: GIE Media, Inc. https://www.nurserymag.com/article/five-tips-automation/ McClellan, M. 2021. Money matters. Nursery Mgt.: GIE Media, Inc. https://www.nurserymag.com/article/how-are-nurseries-spending-cash/
Spirgen, K. 2019. Rack ‘em up. Nursery Management. https://www. nurserymag.com/article/racks-instead-of-boxes-cultivate-19/.
Acknowledgements
The authors acknowledge Lauren Fessler and Lilia Provoda for technical assistance, Dr. Jim Brosnan, Mr. Heath Nokes, and Dr. Annette Wszelaki for review of an earlier version of this article. The coauthors also acknowledge the LEAP Advisory Board, Cherrylake Tree Farm, Decker’s Nursery, Turner and Sons Nursery, and Hale and Hines Nursery for their generous contribution to the LEAP project and for sharing their nursery’s experiences with automation. USDA NIFA SCRI award 202051181-32137 and USDA NIFA Hatch Projects TEN 00575.