
13 minute read
Feature
A Snapshot into Substrates: Components Used by Tennessee Producers
By Walker Harrell¹, James S. Owen Jr.² , Alicia Rihn³, Karl McKim¹, Amy Fulcher¹
¹University of Tennessee, Department of Plant Sciences, ²USDA-ARS Application Technology Research Unit, ³University of Tennessee, Department of Agricultural and Resource Economics
This is part one of a two-part series reviewing substrate components and their costs in 2023 – 2024.
Container substrate, what we often call potting mix, is a mixture of organic and inorganic soilless components that include pine bark, peat, wood fiber, coir, compost, and sand that are amended with lime, mineral nutrients, or pesticides (Figure 1).
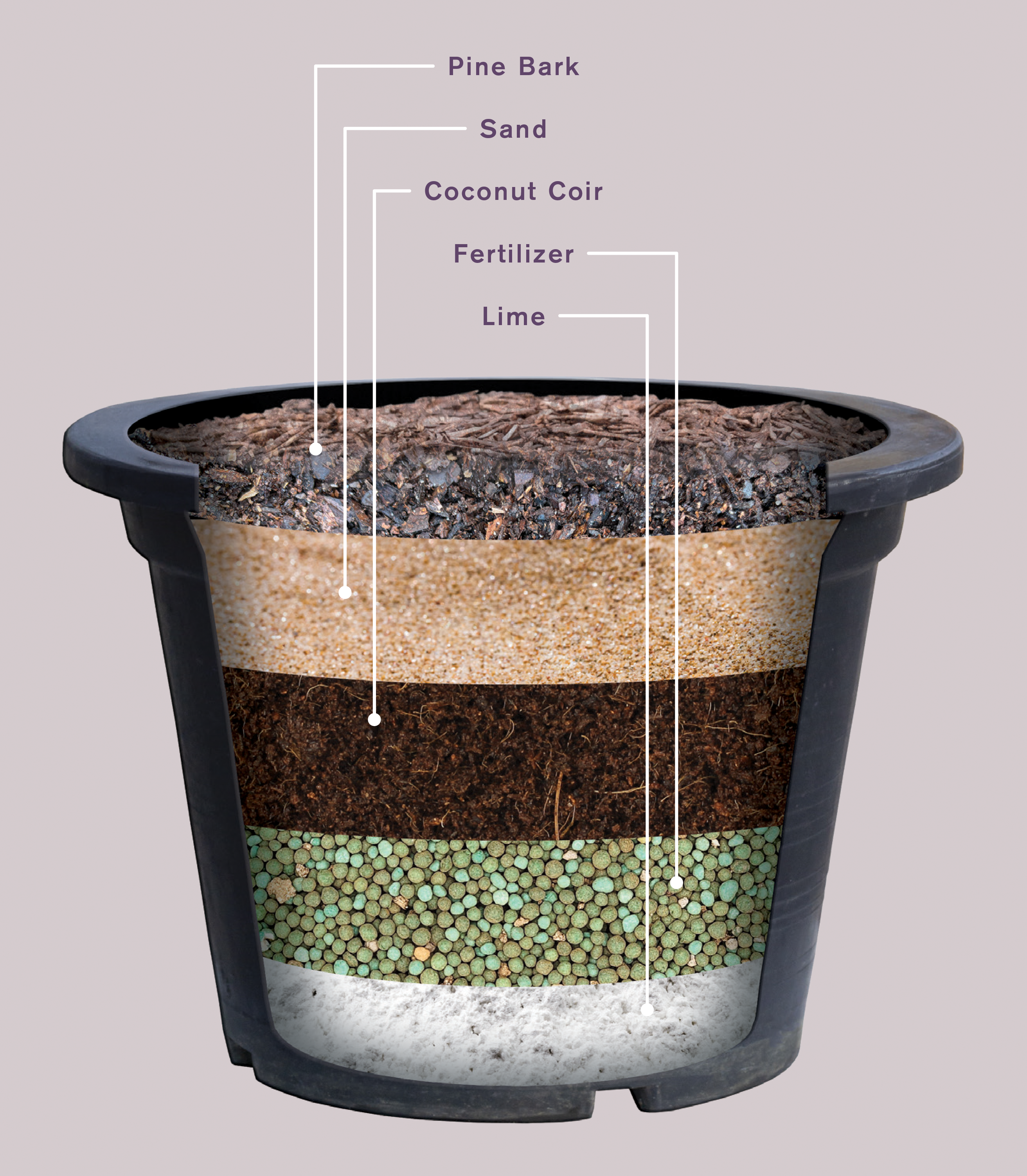
••••••••
Components: organic and inorganic materials that compose the bulk of the substrate volume, and along with container height, influence its physical properties
Amendments: agrochemicals that are added to a substrate to adjust or maintain pH, provide nutrients, or control pests. Amendments can influence the substrate solution’s electrochemical properties, for example pH, electrical conductivity and oxidation state.
••••••••
The substrate anchors plants, provides a reservoir for water and mineral nutrients, and ensures adequate oxygen for root growth. The substrate mixture and potting method directly determine the quantity of substrates used, their static physical properties (total porosity, container capacity, air space, and bulk density), and chemical properties (pH, electrical conductivity).
••••••••
Static Physical Properties characterize substrates and allow them to be compared:
• Total Porosity is total pore space; air space plus container capacity
• Container Capacity is the maximum water holding capacity; % volume at drainage; total porosity minus air space
• Air Space is the maximum pore space filled with air; determined at container capacity; total porosity minus container capacity
• Bulk Density is the dry weight divided by the total volume of the sample
••••••••
When mixing substrate, one part plus one part does not equal two parts; but instead forms a unique substrate with its own distinct physical and chemical properties. The resulting blend may be fluffy, resisting compaction, or dense in which the substrate can become tightly compacted at the time of potting, or a combination of fluffy and dense.
The substrate in the container and the cultural practices used will directly affect water and nutrient use, crop performance, and shipping weight. Substrate consistency is the key to success. For a given crop, the right combination of substrate, fertilizer, and irrigation scheduling needs to be determined. Any changes in suppliers, substrate components’ appearance, substrate’s chemical properties, measuring methods, or mixing methods may result in needed changes to the substrate blends or production practices. Consistency requires continued communication with allied suppliers and personnel. Simply put, a consistent and well-understood substrate is important for profitable production.
Pine Bark
The main substrate component used in southeastern US nurseries is pine bark from Loblolly or longleaf pine (Figure 2). Aged or fresh pine bark is hammer milled or screened to less than half an inch. Aged pine bark, also referred to as stabilized, is a result of bark being wind-rowed for 1 to 6 months. Aging allows the bark to break down into smaller particles. Harrelson et al. (2004), Laiche (1974), and Handreck and Black (1994) reported that aged pine bark produced larger plants than fresh pine bark. The larger plants were likely a result of increased water and nutrient storage. Original bark particle size, age, moisture content, processing technique, and screen size determine the texture or amount of fine, medium, and large particles. Bark texture will govern the substrate’s physical properties. A rule of thumb is that a greater proportion of smaller particles will increase water retention and decrease air space; whereas a greater proportion of coarse particles will decrease water retention and increase air space. The age of the bark also determines starting pH and the substrate’s resistance to a change in pH. The pH of pine bark is between 4.0 and 5.0 but can vary based on age and wood content.
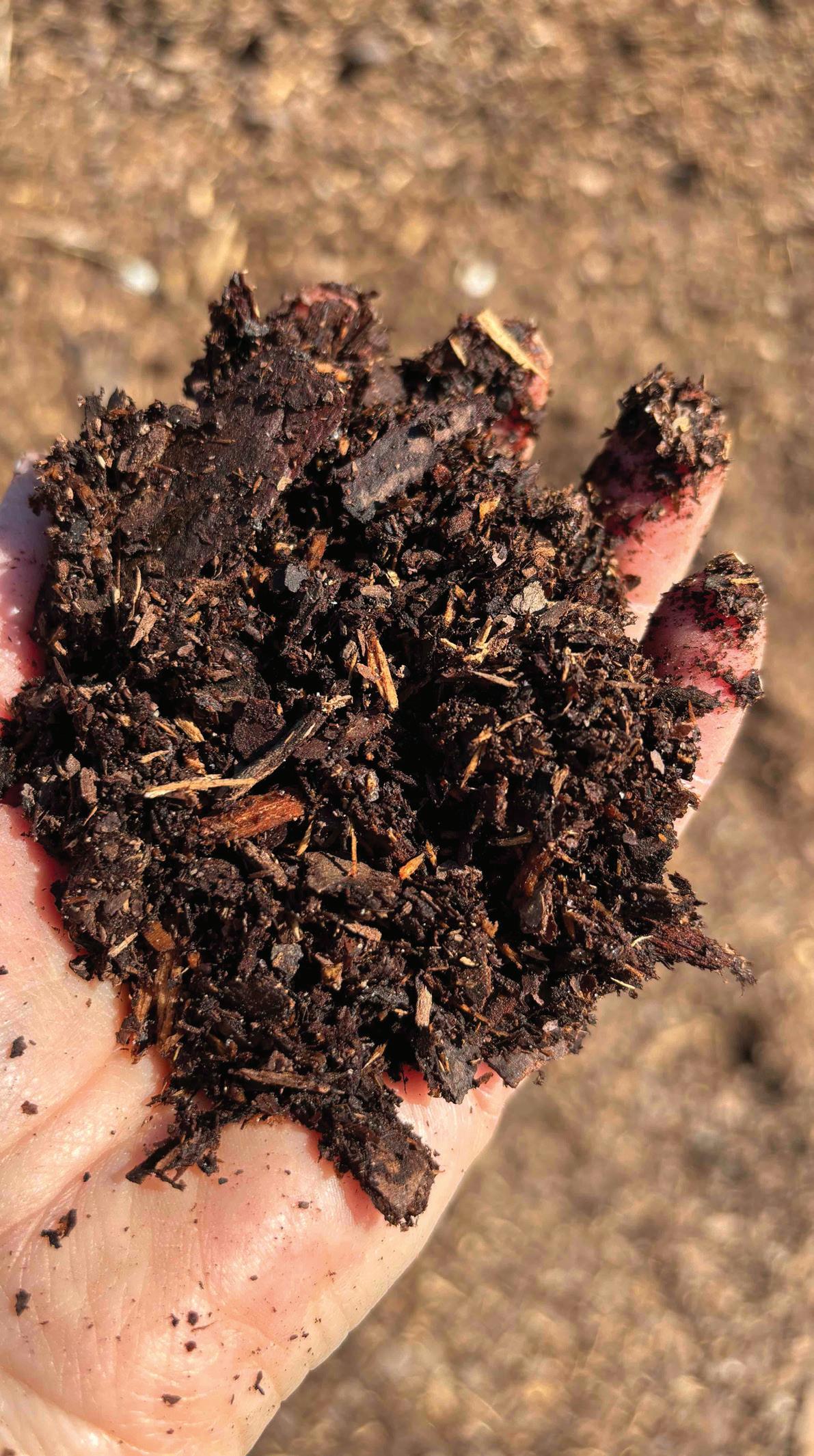
Pine bark will also contain wood or sand with neither being detrimental to crop production. Remember the mantra – consistency is key! Consistency includes the composition of delivered bark including wood and sand. A grower can receive up to 10% sand by volume if bark is wind-rowed or stored on the ground (Dr. Brian Jackson, personal communication). Softwood, either intentionally or inadvertently through the milling process, will comprise on average 10% (5% to 25% range) by volume of the bark you receive (Dr. Brian Jackson, personal communication). Softwood will become darker in color over time as it becomes stained from bark tannins making it unnoticeable to the user and consumer. Unprocessed softwood has less lignin than bark, which can affect the rate of particle breakdown and substrate pH.
Bark consistency can vary due to variable feedstock being provided to the supplier, moisture content at the time of supplier processing, or the storing process. This variability can be addressed by purchasing, or on-site screening, bark into two or three sizes or textures: fine, medium and coarse. These textures can then be recombined in exacting proportions at the time of blending to better control the substrate’s physical properties.
If pine bark will be stored at the nursery for prolonged periods it should be in piles less than six feet tall and turned and irrigated regularly to prevent the bark from becoming anaerobic or lacking oxygen. Anaerobic bark will be dry, have a low pH, and high electrical conductivity. Improperly aged bark that has become hydrophobic is unusable in its current condition.
Dolomite, or dolomitic lime, is commonly used to amend pine barkbased substrates. If adding lime, granular micronutrients should also be added. In addition to improperly stored bark becoming hydrophobic, bark can become hydrophobic after potting, repelling water and decreasing water retention (Airhart 1978; Pokorny 1979). Incorporating commercially available surfactants at the time of potting can prevent this issue. If observed during production, drenching with a liquid surfactant can break surface tension, allowing bark to rewet. During irrigation experiments at the University of Tennessee, a 75% pine bark 25 % peat moss substrate became hydrophobic during production of hydrangeas (Hagen et al. 2014). Substrate components that are less prone to becoming hydrophobic may be more suited to conservative irrigation schedules, those that allow the substrate to dry considerably between irrigation events, than other substrate components.
Peat Moss
Canadian Sphagnum peat is a fibrous substrate component commonly used alone or in combination with bark to produce liners, hydrangea, azalea, and other pH- or water-sensitive nursery crops. Its prominence in horticulture as the ‘gold standard’ is due to its unmatched physical and chemical properties. Peat is shipped in compressed towers or bales requiring specialized equipment before use. Peat increases water retention in bark-based substrates. Peat also has a naturally low pH of 3.0 to 4.5. However, like pine bark, peat can become hydrophobic (Michel 2015) and difficult to rewet. Therefore, peat should be stored moist in sealed pails, or have water added, to ensure fluffed peat does not dry out. Surfactants and dolomitic lime are typically applied at the time of mixing the substrate when using peat.
Layers of Sphagnum peat develop from slow-growing Sphagnum moss over thousands of years in Canadian bogs or wetlands (Figure 3). As peat accumulates beneath the living layer of moss, atmospheric carbon is captured and stored in the ground in a semi-permanent form. When peat is harvested, the bog and harvested peat are susceptible to decomposition that releases carbon into the atmosphere.
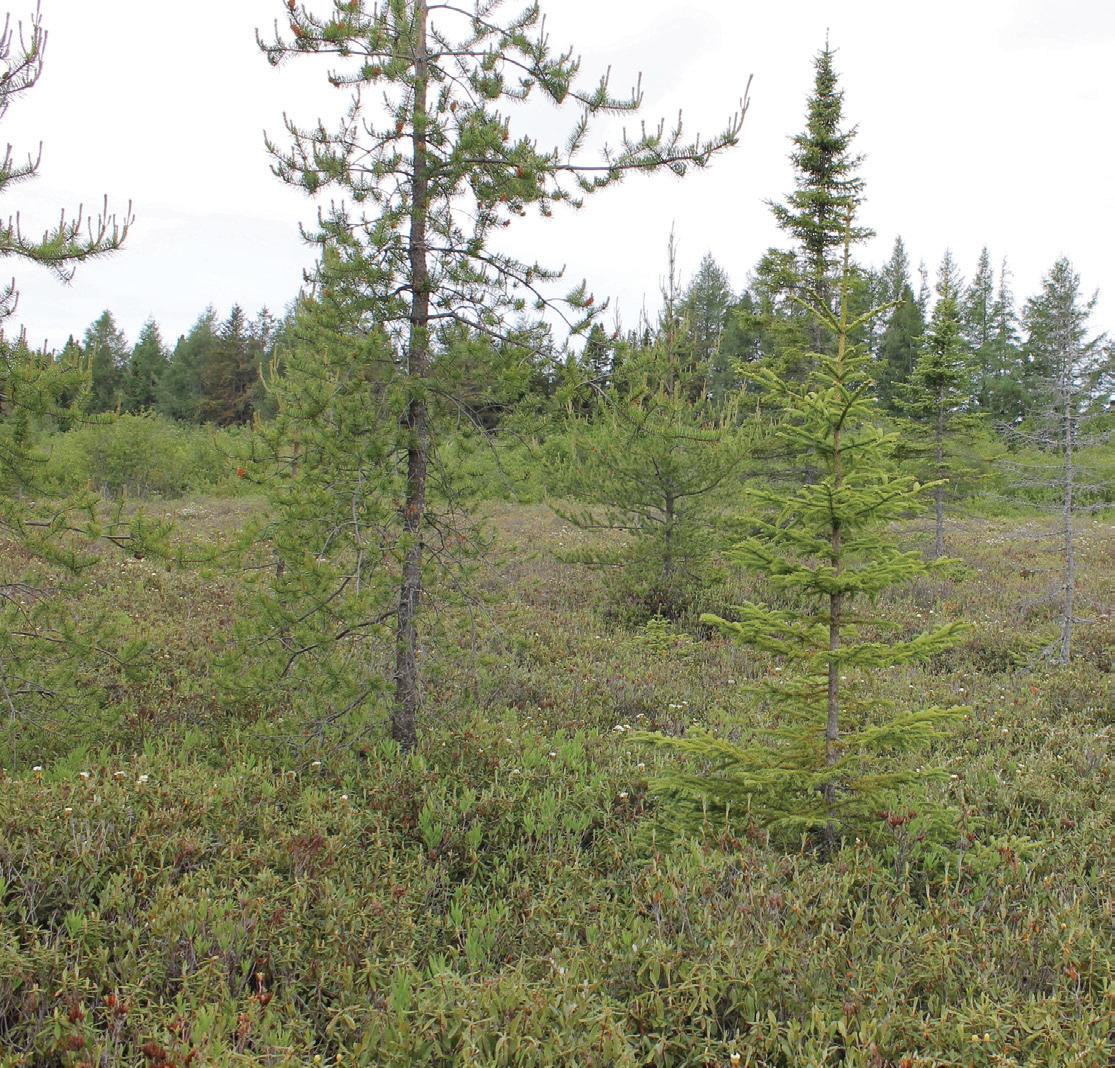
Horticultural use of peat has been featured in the national media. Peat, by definition, is a non-renewable resource, requiring >100 years to replenish. However, according to Dr. James Altland, United States Department of Agriculture, only 0.03% of the 294 million acres of Canadian peatlands, and according to Clarke and Rieley (2019) just 0.05% of worldwide peatlands are harvested for horticultural uses that produce edible, ornamental, and forest seedlings providing social, environmental, health, and economical benefits.
Production-related concerns surrounding peat today are availability and cost. Weather has repeatedly prevented adequate harvests to meet industry demand in North America. The lack of readily available peat as a substrate component will require the industry to rethink their dependence. In many cases, nurseries are purchasing premade substrates that include peat from allied suppliers or are exploring alternatives. In response, the horticultural industry is considering substrate components that can extend peat supplies, while still relying on peat as a substrate ingredient.
Other Substrate Components
Wood fiber is a renewable, abundant, and available substrate component. Wood fiber is created from defibrating softwood wood chips using a twin-disc refiner, extruder, or hammermill (Durand et al. 2021). Extruded or refined fiber undergoes heating during processing which can increase stability. Wood fiber is typically shipped in compressed bales that require specialized equipment before incorporation into substrate mixes. Wood fiber can vary in size and shape depending on processing and user preference. A wide range of wood fiber physical properties from differing processing techniques have been reported to improve water retention as well as aeration of peat-based substrates (Durand et al. 2021; Jackson 2018), demonstrating the diversity of the product. We hypothesize that adding fiber would be like adding finer bark to a barkbased mix, but not increase water retention as much as a peat or compost. However, wood fiber could decrease water flow through a coarser pine bark substrate. With ever-increasing adoption of wood fiber throughout the horticultural industry, more research is needed for wood fiber use in pine-bark based substrates for use in nursery crop production.
Coir refers to coconut pith, which is a by-product of processing the outer husks of coconut palms ( Figure 4a & b; Schmilewski 2009).” Brackish or salty water is commonly used for processing, which causes the pith to have high sodium or potassium levels (Agarwal et al. 2023). Leaching the sodium with freshwater is required to prepare the pith for horticultural use. The pith can also be pH buffered with calcium nitrate. Use of freshwater and calcium nitrate increases the cost to produce a high quality, production-ready horticultural substrate. Coir is typically shipped in compressed bricks that require water and time to decompress or specialized equipment to mechanically “fluff” before use. Research at the University of Tennessee and elsewhere has shown that coconut coir has tremendous water holding capacity and that much of the water is “plant available”, when compared to peat or pine bark (Basiri Jahromi et al. 2020). Additionally, coir does not become hydrophobic when dry. However, coir is not a direct replacement for peat. Coir has a neutral to high pH and different physical properties, and like all new components requires in-house evaluation before adopting nursery-wide.
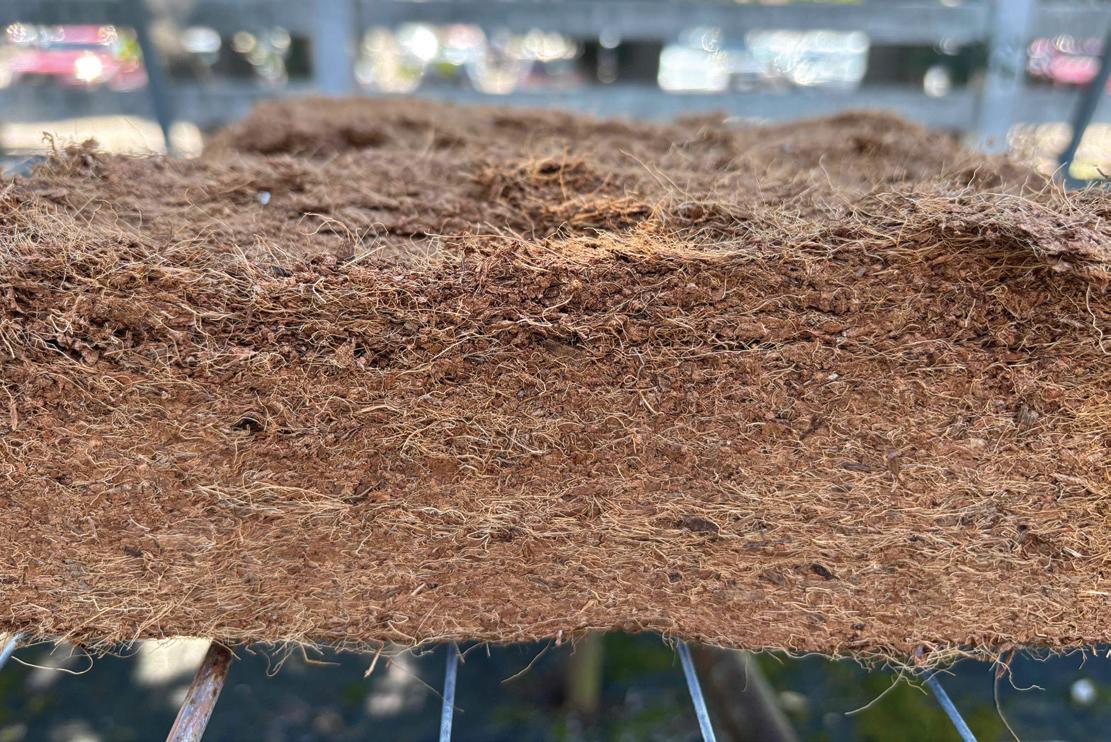

Compost is a viable, routinely used component of substrate as a smaller proportion of the total mixture. Compost usually has a neutral or high pH and will typically increase water retention. The compost feedstock; the process and time of composting and receiving, storing, and using the compost; must be consistent to ensure a reproducible, quality crop. Vermicompost, or worm castings or manure, is a compost that is locally available in Tennessee.
Lastly, washed builder’s sand is added to substrate to add weight, although that does not appear to result in reducing container blow over. Sand was once believed to increase drainage. We now know that sand will fill in larger pores to aid in water moving more slowly through the container profile and thus more completely wetting the substrate (Bilderback et al. 2005). Fine sands may clog substrate pores and retain too much water.
Chemical Amendments
Many nurseries also amend their substrates with dolomite or lime, micronutrients, controlled release fertilizer, or pesticides. The addition of dolomite or lime increases and helps maintain the substrate pH. Liming can decrease micronutrient availability. Granular micronutrients are typically added when using lime or dolomite. Testing irrigation water is important given that the water source may be alkaline (greater than 100 ppm) or contain mineral nutrients such as calcium and magnesium resulting in continual liming or adding essential nutrients when irrigating. Controlled release fertilizers are coated or otherwise include a barrier that releases mineral nutrients gradually, fertilizing plants over a period of months instead of agricultural-grade fertilizers, which generally release macro- or micro- nutrients over a period of weeks or even days. In rare instances, the controlled release fertilizer coating can be compromised when incorporated into the substrate depending on mixing equipment, substrate components, and mixing time, which results in more nutrients being released than expected at the time of potting. Pesticides are most often added to control insects such as fire ants or root rots.
Conclusions
A wide range of organic and inorganic components are used in container substrates. Understanding substrate physical and chemical properties and how these properties can change with changing feedstocks, storage conditions, and storage duration is critical to managing substrate consistency and making needed adjustments to production practices to produce uniform, high quality crops. All substrate components, including alternatives promoted to replace peat, have their own carbon, water, energy, or environmental footprint. This article highlights the potential to use a range of products, often by-products of other forms of agriculture, in container substrates and the need to develop a system by which substrates can be fairly evaluated and compared.
References and Resources for Additional Reading
Agarwal, P., S. Saha, and P. Hariprasad. 2023. Agro-industrial-residues as potting media: physicochemical and biological characters and their influence on plant growth. Biomass Conversion and Biorefinery 13:9601-9624.
Airhart, D.L., N.J. Natarella, and F.A. Pokorny. 1978. Influence of initial moisture content on the wettability of a milled pine bark medium. HortScience 13:432-434.
Basiri Jahromi, N., A. Fulcher, F. Walker, and J.E. Altland. 2020. Optimizing substrate available water and coir amendment rate in pine bark substrates. Water 12(2), 362.
Bilderback, T., S. Warren, J. Owen, and J. Albano. 2005. Healthy substrates need physicals too. HortTechnology 15(4):747-751.
Durand, S., B. Jackson, W.C. Fonteno and J.-C. Michel. 2021. The Use of Wood Fiber for Reducing Risks of Hydrophobicity in Peat-Based Substrates. Agronomy. 11(5), 907;
Fields, J., B. Jackson, and W. Fonteno. 2012. Pine Bark Physical Properties Influenced by Bark Source and Age. Acta Horticulturae. 10.17660/ ActaHortic.2013.1014.96
Hagen, E., S. Nambuthiri, A. Fulcher, and R. Geneve. 2014. Growth and water consumption of Hydrangea quercifolia irrigated by on demand and daily water use irrigation regimes. Scientia Horticulturae 179:132-139.
Handreck, K.A. and N.D. Black. 1994. Growing Media for Ornamental Plants and Turf. Univ. New South Wales Press, Randwick, Aust.
Harrelson, T., S.L Warren, and T.E. Bilderback. 2004. How do you manage aged versus fresh pine bark? Proc. SNA Res. Conf. 49:63-65.
Jackson, B.E. 2018. Substrates on Trial: Wood Fiber in the Spotlight. Greenhouse Management, September, 38(9):52-56. https://www.greenhousemag.com/ article/substrates-on-trial-wood-fiber-in-the-spotlight/
Laiche, A.J. 1974. Pine bark growing media-fertility studies for the production of container-grown ornamentals. MAFES Res. Highlights. 37:1-3
Michel, J.-C. Wettability of Organic Growing Media Used in Horticulture: A Review. Vadose Zone J. 2015, 14.
Pokorny, F.A. 1979. Pine bark container media – An overview. Comb. Proc. Intl. Plant Prop. Soc. 29:484-495.
Schmilewski, G. (2009) Growing medium constituents used in the EU. International Symposium on Growing Media 2007(819):33–45