
9 minute read
Tech Facilities
Selected work
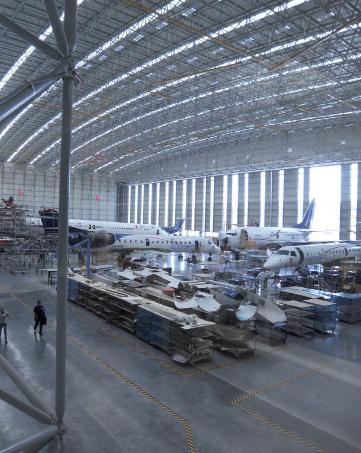
Delta Air Lines / AeroMexico
Joint Maintenance Facility
Queretaro, Mexico
Owner Delta Air Lines / AeroMexico
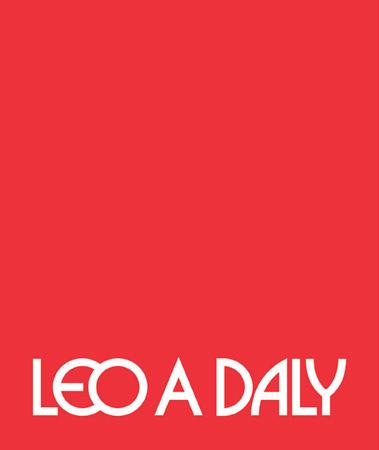
Size 500,000 SF
Cost $32,000,000
Scope Programming, Concept Design, Design Review, Construction Oversight
Completion
January 2015
LEO A DALY was selected to provide concept designs and programming for Delta Air Lines and AeroMexico’s new joint maintenance facility in Queretaro, Mexico. We teamed up with contractor GMI to create an innovative, cost-effective, and low-maintenance design for the 500,000-square-foot joint facility. Using GMI’s innovative hub-and-spoke space frame system, designed for clear spans, construction costs were kept low and future upkeep to a minimum. The three-hangar concept provides for up to nine narrow-body aircraft positions, or four larger, wide-body aircraft positions.
One of the largest design-build projects in Mexico, the development includes three hangars, new landside access service drives and loading docks, support shops and mechanical rooms, personnel support spaces, a recreation building, and an executive/administrative suite. In addition to programming and concept design, the firm incorporated numerous sustainable design strategies, including photovoltaic solar panels that generate 75 percent of the facility’s power, daylight harvesting, rainwater capture systems for gray-water reuse, aircraft-wash wastewater recycling, and the use of locally manufactured materials where possible.
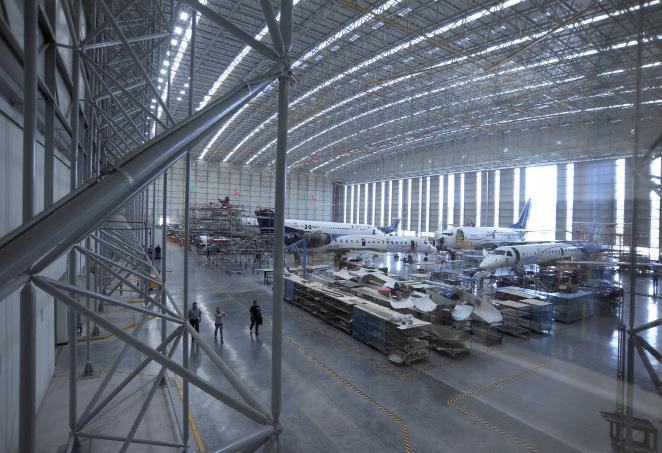
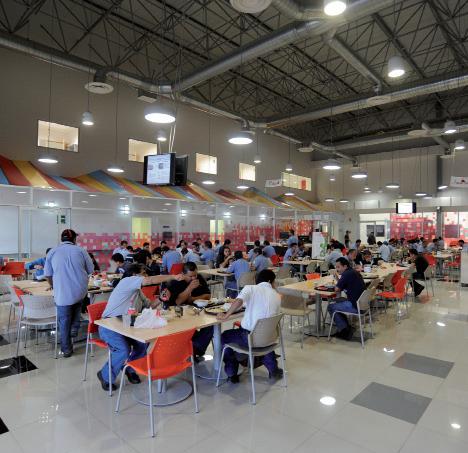
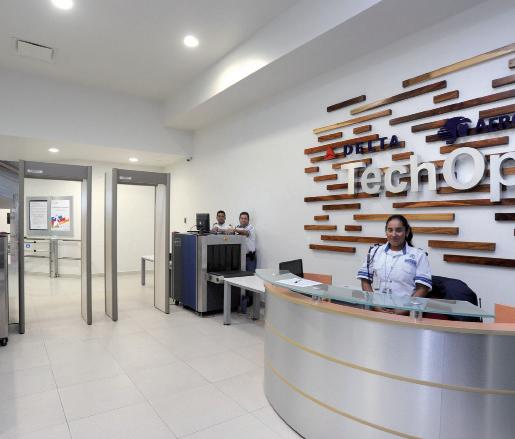
Fieldale Farms Corporate Hangar
Gainesville, Georgia
Owner Fieldale Farms
Size
14,500 SF
Cost $2,400,000
Scope Concept Design, Design Review, MEP
Engineering, Construction Oversight
Completion
July 2018
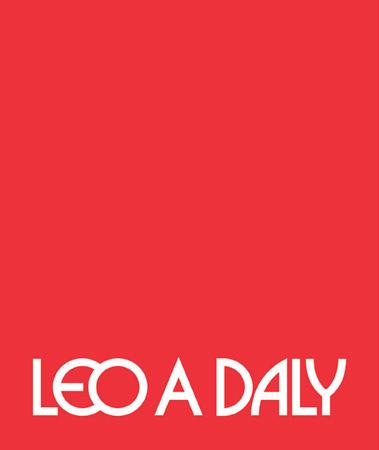
With the acquisition of additional aircraft, Fieldale Farms moved from leased space at Lee Gilmer Memorial Airport to a new, two-bay corporate hangar. The project features a 12,000 SF hangar bay designed for two Falcon 2000 aircraft, with an additional 2500 SF of support space.
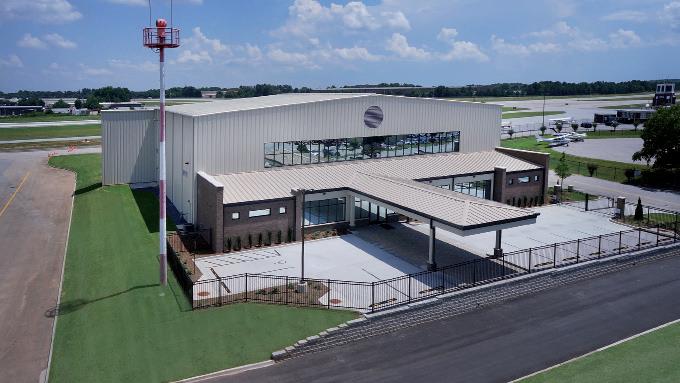
The hangar bay includes a gas fired radiant heat system and two large “Big Ass” fans for ventilation. State of the art LED lighting systems and controls illuminate the hangar floor and clear story windows on the north wall across the back wall of the hangar provide natural light creating a welcoming presence within the hangar bay. The hangar doors are configured as a fully powered bi-parting anchored group door system.
The local Building Authority waived requirements for a separate fire protection system for the hangar bay but required an increased fire separation rated wall between the hangar bay and the support spaces located in the “lean-to” frame across the back wall of the hangar.
The hangar was built with a custom design pre-engineered building structure for the hangar bay and conventional stick built framing for the lean to and vehicular drop off canopy.
This design-build was completed in association with JVC Construction.
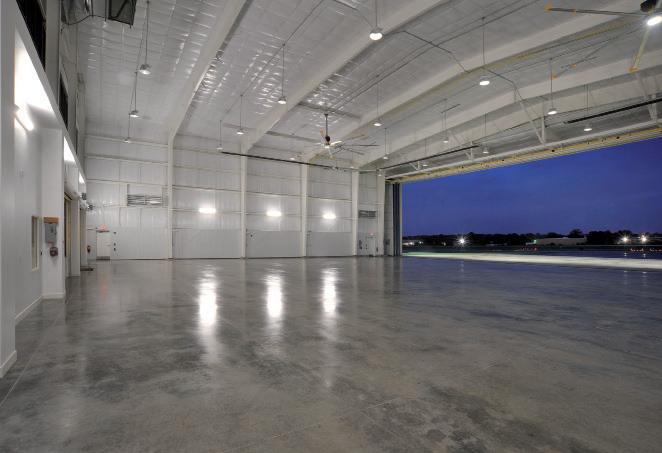
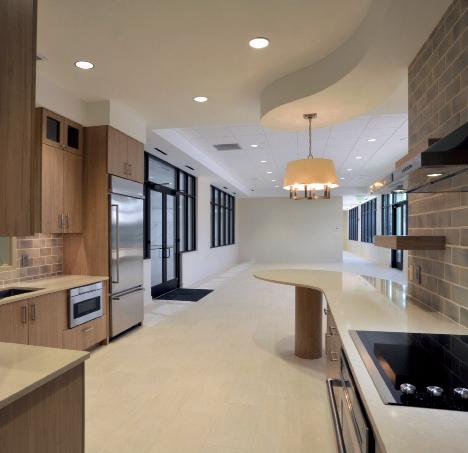
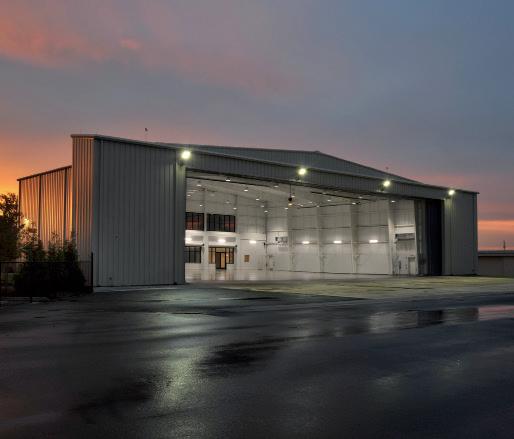
MWAA Washington Dulles International Airport Police Range and Training Facility
Dulles Airport, Virginia
Owner Metropolitan Washington Airports Authority
Size
7,200 SF
Cost
Confidential
Scope
Architecture, Engineering
Completion
March 2017
The Metropolitan Washington Airports Authority (MWAA) facility provides the tactical and classroom training facilities for the multi-site airport police force and two other multijurisdictional users near Washington DC. The project includes a 7,200 SF classroom training building for use by both the Authority and Arlington County police and sheriff forces that contains:
• two instructor offices
• two armory rooms
• two general purpose classrooms
• one defensive tactics training area
• one outdoor gun cleaning area
• kitchenette
• restrooms
• shower and locker rooms
• a climate controlled range material and ammunition storage facility
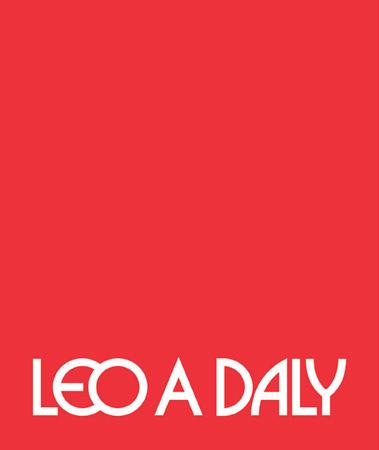

• a defensive tactics training space
• armorer’s spaces
• two 50-yard, 18 lane ranges
• one 300-yard, 11 lane rifle range, and
• the relocation of 14 explosive storage containers and the site development for 75 cars and associated road improvements.
The range, which is operated year round to meet the needs of the department, was designed to achieve acoustical compliance with MWAA’s Design Manual 2010 standards for facilities of this type.

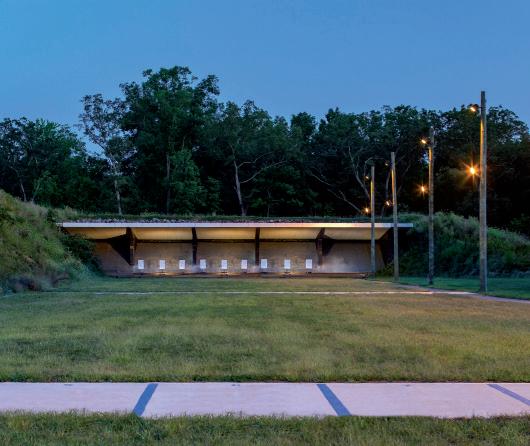
The 26.4 acre site sits within a unique wildlife-rich environment paying careful attention to mitigate migratory patterns and environment of local wildlife and noise sensitivity to surrounding areas. The project additionally planned for a future third 50- yard range, expansion of the 300-yard range to 500 yards with engineered berms as well as potential development of additional training structures, including a shoot house and gas house for tactical training.

Zaxby’s Corporate Hangar

Winder Barrow County Airport, Athens, Georgia
Owner
Zaxby’s
Size
19,000 SF
Cost
$2,700,000
Scope
Architectural Planning and Design, Interior Design, Structural, Mechanical, Plumbing, Electrical, and Fire Protection Engineering
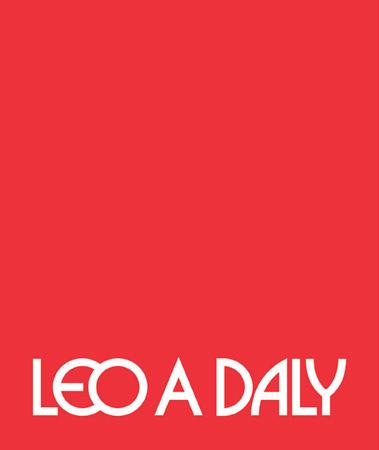
Completion
March 2015
LEO A DALY designed a new corporate hangar for Zaxby’s Corporation at the Winder Barrow County Airport outside their headquarters complex in Athens Georgia. The project consists of a 19,000 SF, $2.7 million Group III hangar designed to hold a variety of aircraft including three Beachcraft 1900 or a Gulfstream V aircraft.
The north-facing hangar doors are remotely controlled anchored group bi-parting doors with polycarbonate vision windows that allow in the soft north light. The hangar bay includes service utilities for light maintenance operations. The hangar bay uses a gas fired radiant heating systems, an exhaust system, and two “Big Ass” fans to enhance air circulation. The hangar support spaces include:
• Pilot offices
• Large lobby gathering space
• Breakroom/kitchen
• Restrooms
• Pilots shower facility
• Pilots lounge and flight planning area
• Conference room
• Storage/shop area
Site work for the project included a new access road, new taxiway extension, aircraft ramp space, parking for 24 cars and a covered porte cochere drop off area on the landside for passengers.
US Coast Guard OPBAT (Operations Bahamas and Turks) Hangar
Great Inagua, Bahamas
Owner
United States Coast Guard Facilities
Design & Construction Center
Size
18,750 SF
Cost
$25,300,000
Scope
Full Architectural / Engineering Services
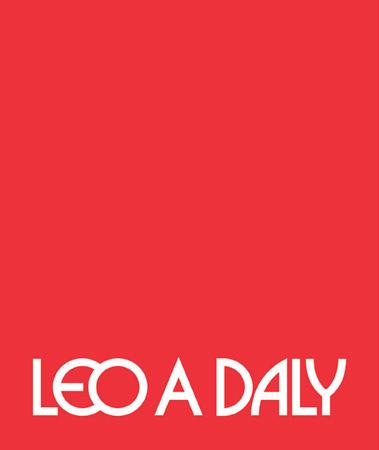
Completion
January 2013
Delivered design-build, LEO A DALY provided a Category 3 berthing hangar for two United States Coast Guard (USCG) HH-60 helicopters, with ancillary support structures including a four-bedroom modular barrack and a hazardous materials building. The scope of work included the demolition of the existing facility devastated by a recent hurricane and construction of a 18,750-SF, two-bay hangar with 28 foot clear height. The project included a 5-ton bridge crane, high expansion foam fire suppression system, 400hz and 28volt DC power services, airframe washdown area, maintenance and shops, and staff support areas. In addition to the HH-60 helicopters, the hangar also accommodates the HH-65 Dolphin and the CASA CN-235 medium-range twin-engine transport plane.
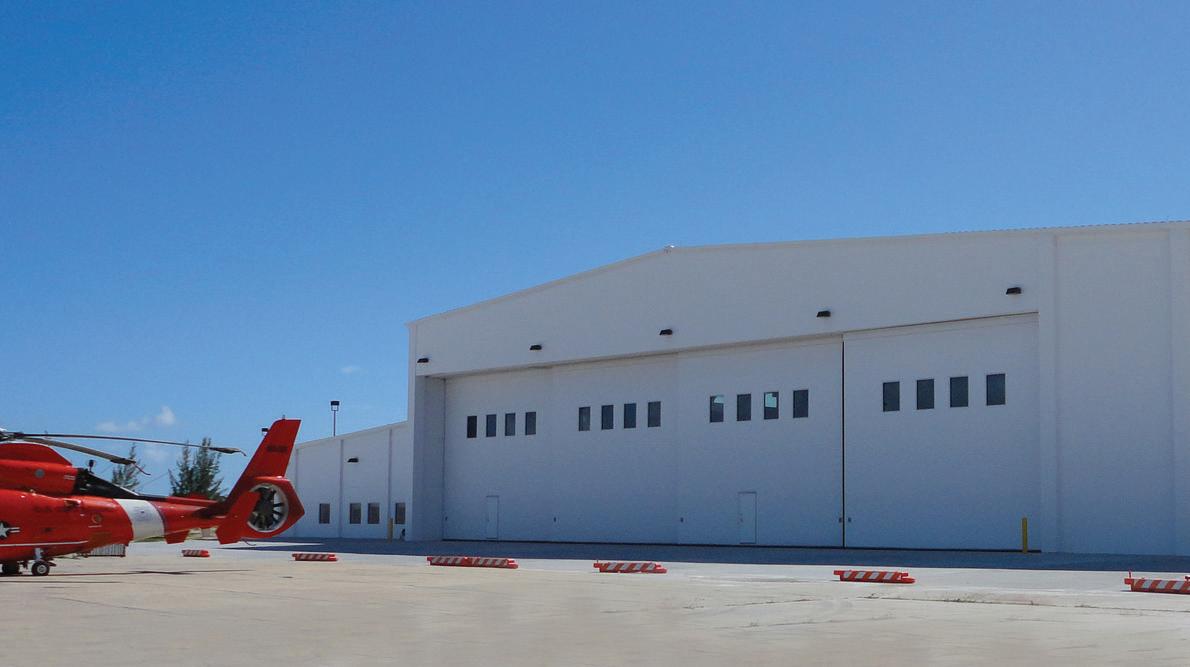
The project utilizes photovoltaic arrays covering the roofs of the existing seven barracks and the one new barrack to offset the high cost of local utilities. It was designed to USGBC LEED certification standards.
Unique Challenges
The isolated location created numerous challenges with material delivery and experienced craftsmen. A unique precast concrete structural system was utilized to provide a durable, corrosion resistant, maintenance free facility that can withstand 150mph winds and debris. The system has concrete H pile foundations and columns with inserts of precast concrete panels. The four 28-foot high by 32-foot wide hangar doors are also constructed of precast concrete allowing the entire facility to withstand catastrophic storms. The double sloped steel truss roof structure is integrated with the precast concrete structure and clad with a 4-inch thick composite standing seam metal roof system.
Ellsworth AFB Main Fire / Crash Rescue Station
Ellsworth Air Force Base, South Dakota
Owner Department of the Air Force
Size
32,300 SF
Cost
$6,300,000
Scope
Programming, Architecture, Engineering, Site Utilities, Interior Design Awards
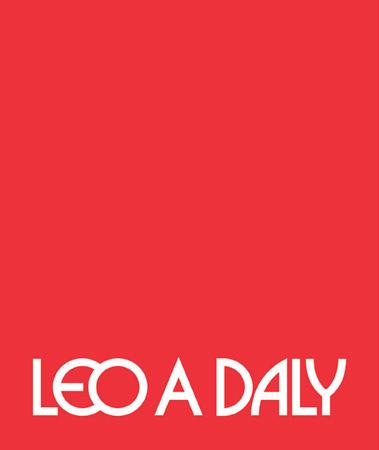
2002 Facility Design Merit Award, Air Combat Command
2001 Facility Design Merit Award, US Air Force
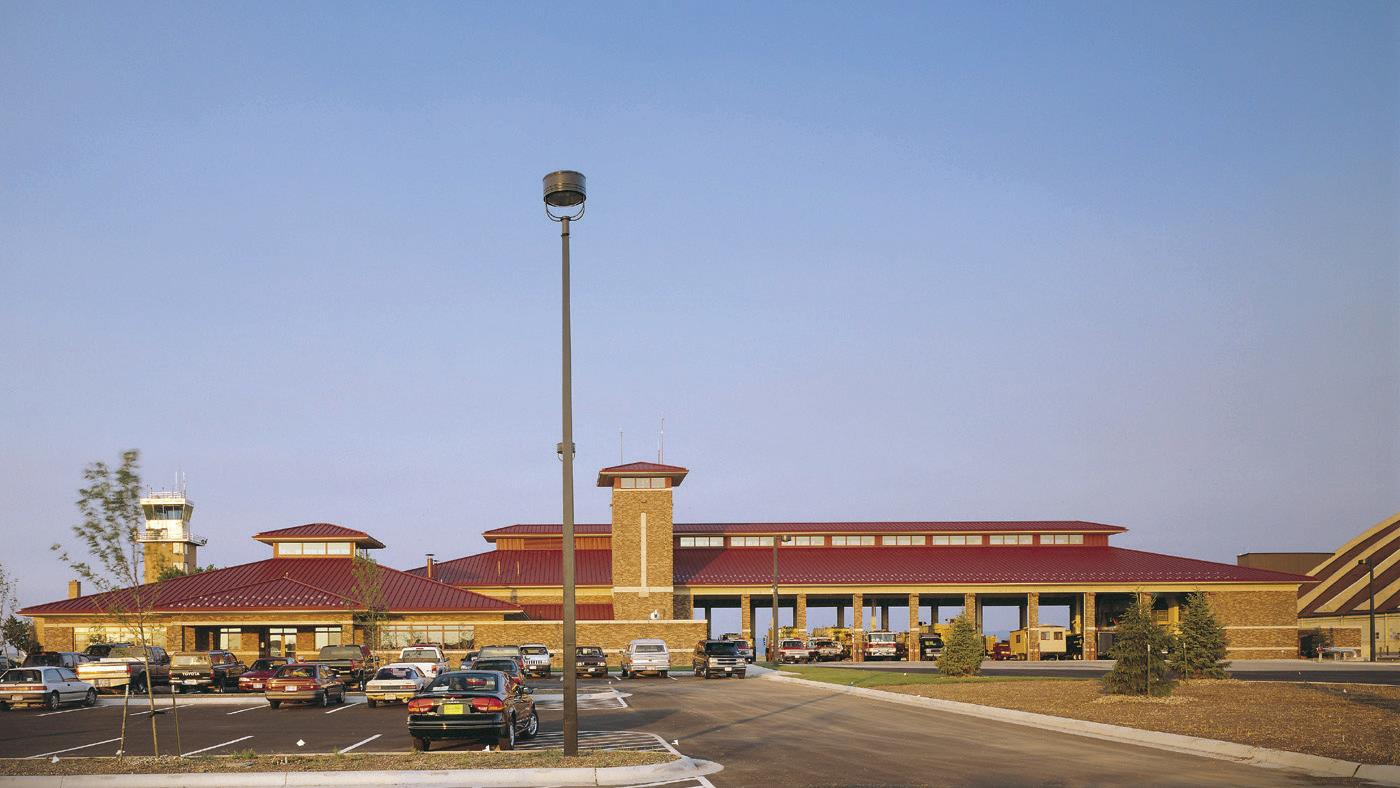
2000 Concept Design Honor Award, Air Combat Command
The main fire/crash rescue station at Ellsworth Air Force Base is comprised of operational spaces to store and maintain 22 emergency response vehicles, living space for 23 on-duty staff and administration/training space to develop and manage personnel.
Designed to minimize response time, the facility is located adjacent to the flightline, midway between the Pride Hangar and Base Operations. Half of the apparatus bays have direct access to the flightline and the other half are on axis with Lemay Boulevard, the primary east/west linkage between the flightline and other base facilities.
The apparatus bays are used for maintenance on equipment and vehicles. The bays have an extensive equipment/vehicle exhaust removal system, and a 10-ton overhead crane and rail system. The bays also include maintenance shop areas for fire extinguishers, personal protective and oxygen equipment, supply and equipment inventory storage and control and electronic communication equipment.
Myrtle Beach International
Airport, Aircraft Rescue and Fire Fighting Facility
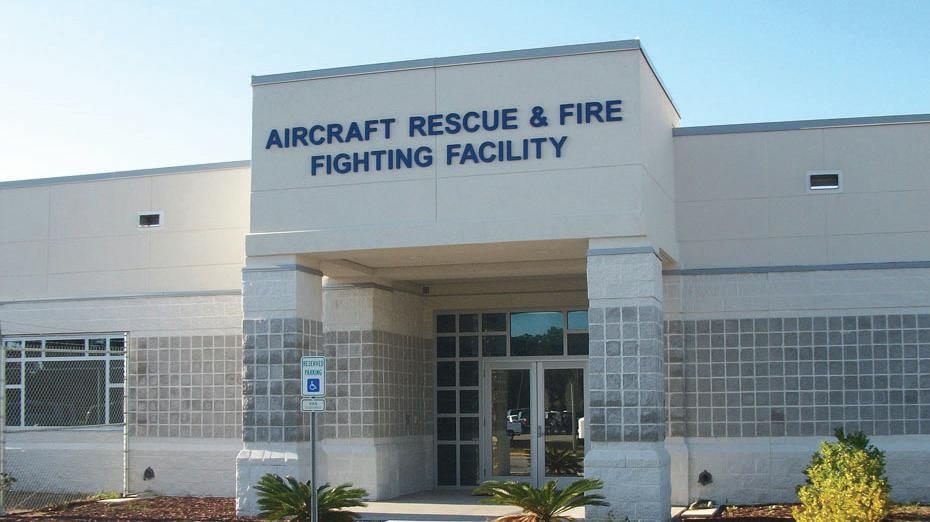
Myrtle Beach, South Carolina
Owner Horry County Department of Airports
Size 32,300 SF
Cost
$6,000,000
Scope
Architecture, Construction Administration
Completion
December 2009
Myrtle Beach International Airport had an outdated ARFF in need of replacement and updating to the most current safety and operational standards. LEO A DALY served as a consultant for overall architectural programming, schematic design, design oversight, analysis of funding eligibility, and FAA coordination.
Project issues included phased project planning, considerations for future expansion, assembly of team specialists relating to adjacent fuel farm issues, and airspace analysis. Operations at the ARFF include provisions for water rescue services and vehicle maintenance. Facility design and construction will comply with the following FAA AC procedures and standards:
• 150/5220-4B - Water Supply Systems for Aircraft Fire & Rescue Protection
• 150/5210-15A - Airport Rescue & Firefighting Station Building Design
• 150/5070-6B - Airport Master Plans
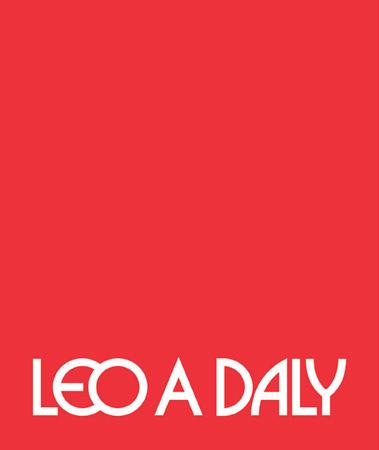
• 150/5300-13 - Airport Design
• 150-5320-6D - Airport Paving Design & Evaluation
• 150/5320-5C - Surface Drainage Design
The project was delivered through a construction management process, with MB Kahn as the prime.
Greenville-Spartanburg
International Airport (GSP) Aircraft
Rescue and Fire Fighting Facility (ARFF)
Greer, South Carolina Owner Greenville-Spartanburg
International Airport
Size 24,000 SF
Cost $9,000,000
Scope
Architectural Design, Mechanical, Plumbing, Fire Protection and Electrical Design Services, Structural and Special Systems Design

Completion Date
October 2020
When Greenville-Spartanburg International Airport (GSP) needed to replace its existing Aircraft Rescue and Fire Fighting Facility (ARFF), they activated their on-call design services contract with WK Dickson, who partnered with LEO A DALY to design the new 24,000 square foot ARFF. The new facility replaces one that was built in 1962 and was a third of the size recommended for an airport like GSP. The department has 23 certified aircraft and rescue firefighters, 18 of whom are also emergency medical technicians, assigned to the ARFF to provide land and airside firefighting and emergency services.
The facility includes five drive-through apparatus bays housing 10 trucks, 10 private dorm rooms, training room, industrial kitchen, day room/ living area, fire administration offices, workshop, computer room, and support spaces for this land and airside emergency department. The ARFF was sited to allow dual access to both airside and landside with drives on both sides of the apparatus bay. The interior is designed to limit access by the general public, while granting access to the building occupant/ users via secured doorways. The ARFF’s design complements the surrounding campus structures, forming an integral part of the fabric for the overall airport.
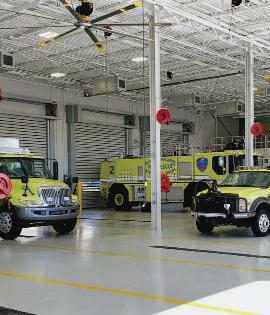
Multiple filtration units are used to remove exhaust fumes, while the controlled ventilation system provides additional safety measures. Direct-fired infrared heaters are used to spot heat the apparatus bays, improving efficiency.
In addition to providing expanded creature comforts for the firefighters, the new ARFF is also better positioned closer to the middle of the runway in order to respond to emergencies on the runway and across the nearly 3,700-acre airport campus. GSP, which handles 2.6 million passengers each year, is served by six major airlines offering more than 100 total daily flights and serves as a major hub for air cargo. The new facility is credited with giving GSP the space and flexibility to meet GSP’s needs well into the future.
The project was funded through a combination of airport funds and monies received from an Airport Improvement Program (AIP) grant from the Federal Aviation Administration.
Hangar 101 Repairs RFP Preparation, Naval Air Station (NAS)
Jacksonville, Florida
Owner Fleet Readiness Center
NAVFAC Southeast
Size
812,435 SF
Cost
$45,200,000
Scope
Design-Build RFP
Completion
January 2019 (design)
LEO A DALY was awarded a NAVFAC SE Task Order to complete a Design-Build RFP Package for the rehabilitation of existing Hangar 101 (WW II era), Naval Air Station (NAS). LEO A DALY prepared the package in accordance with NAVFAC Design-Build Masters, FC 1-300-09N Design Procedures, and the requirements within Whole Building Design Guide. The RFP includes specifications and plans for the new work.
Hangar 101 at NAS Jacksonville was originally built in 1940. Since then, it has had numerous additions and internal modifications reflecting changes in mission and equipment.

LEO A DALY conducted an on-site investigation of the existing facilities, met with key project stakeholders, and documented the entire process in a report to the government.
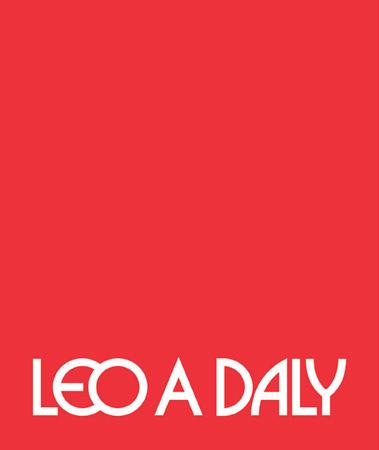
The RFP is for major repairs to the exterior and interior of the hangar. Exterior improvements include removing and replacing the original transite siding and windows. The roof will also be completely replaced including the existing wood decking. The interior of the hangar will be completely refurbished with new lights, heating system and fire protection system. The interior finishes of the hangar will be cleaned and repaired including the entire production floor. Several of the interior mezzanines will be renovated as potential bid options. The interior renovations will also address functional and ADA accessibility issues.
The renovation work is complicated by the duration requirement that the hangar will remain in use throughout the duration of the renovations. A temporary hangar will be constructed by the design-build contractor.