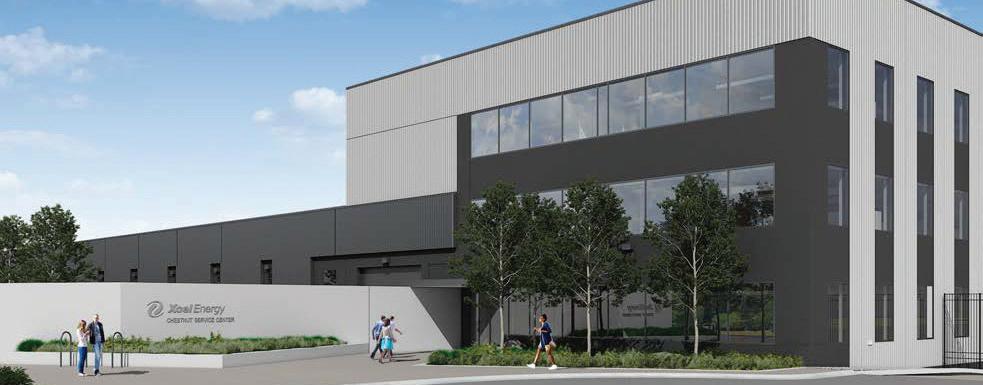
8 minute read
Xcel Energy, Product Testing Lab, Office, and Fleet Maintenance Facility, Minneaplois,
MN
Owner
Xcel Energy
Size
212,000 SF
Scope
Full Architectural and Engineering Services, Interior Design, Facility Assessment, Building Programming
This 212,000 SF Xcel laboratory and fleet service Center includes a storage yard, material storage, service vehicle garage, crew amenities, four stories of office and meeting rooms, and a 20,000 SF advanced analytical chemistry resources lab. Some of the critical programming components include:
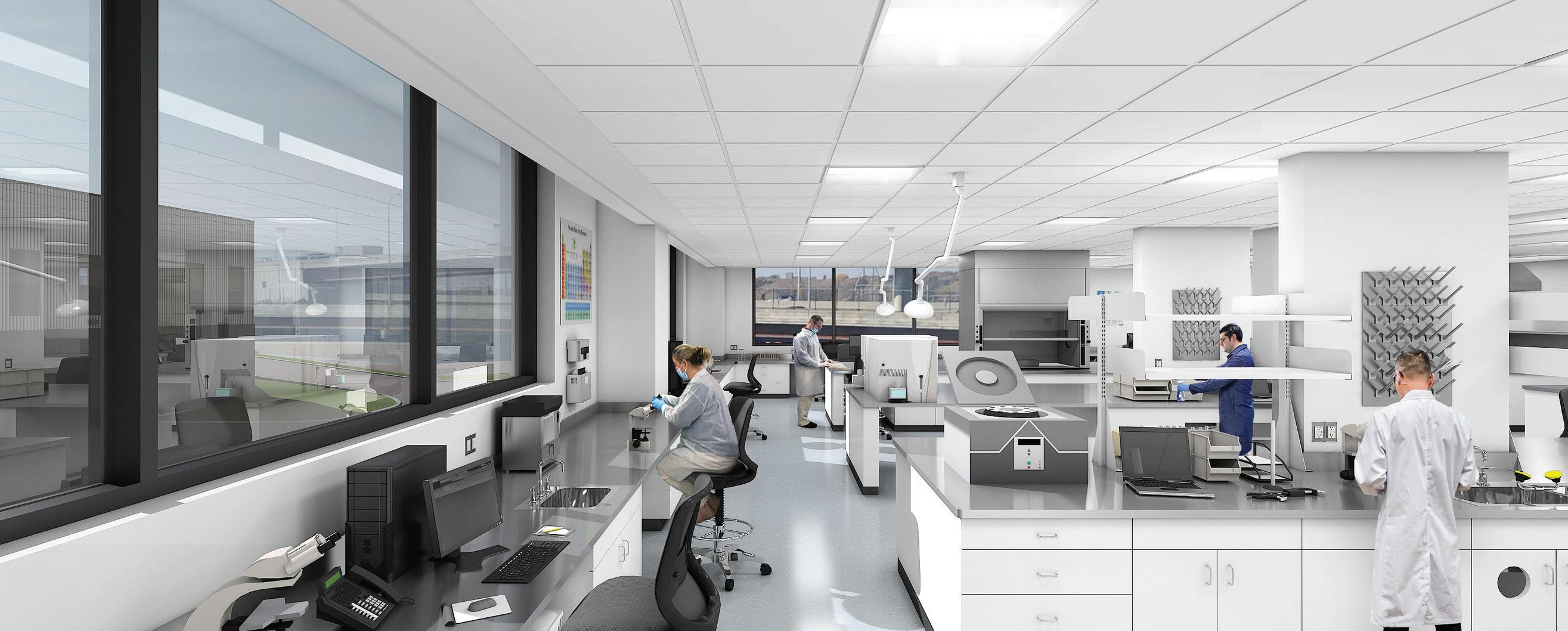
Hazardous Waste: It includes a hazardous waste storage and processing area of which was protected by a Aqueous Film-Forming Foam (AFFF) fire suppression system. Hazards present included flammable and combustible liquids of varying flash points. AFFF solutions contain chemicals that are potentially damaging to the planet and human health and the decommission of those systems is advised by many environmental agencies. LEO A DALY fire protection engineers designed a fluorine-free foam fire suppression system to replace the existing AFFF system and meet new design requirements for fluorinefree foam systems.
Labs and Hazardous Material: The facility design includes labs for testing and analyzing hazardous materials. Flammable and combustible liquids, dusts, and inert gases were all present. The design of the labs and gas storage rooms include provisions for maintaining maximum allowable quantities (MAQs) and control areas to ensure compliance with the building and fire codes
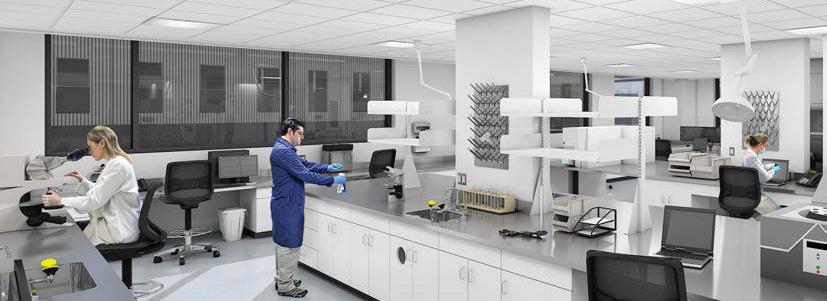
Sysco Freshpoint Expansion/Remodel
Orlando, Florida
Owner Sysco - Freshpoint West Coast Florida
Size
165,160 SF total 55,520 SF addition
109,640 SF renovation
Cost $17,000,000
Scope
Architectural design through construction administration services
FreshPoint West Coast Florida selected LEO A DALY for a renovation/ expansion of an existing produce processing and distribution center in Orlando, Florida.
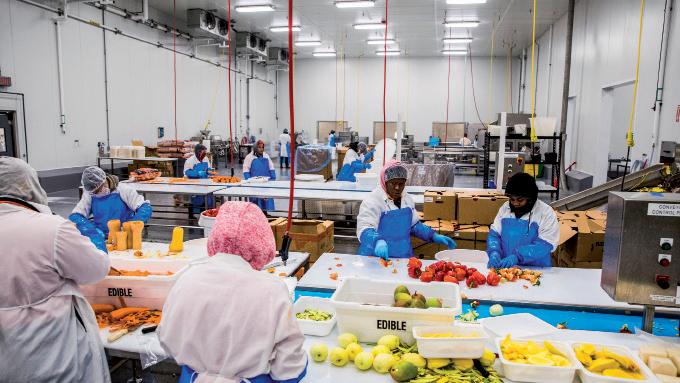
The project includes:
• 55,520 sq. ft. of new cooler consisting of multiple temperature zones, banana rooms, cold dock and dock offices. This area is anticipated to have future expansion and will need accommodations for that expansion.
• Renovated and expanded 29,580 sq. ft. of cooler, cold dock, and additional dock offices and ancillary spaces.
• Relocation and renovation 24,540 sq. ft. of produce cuts sanitary production areas, employee welfare areas, material handling equipment battery charging areas, maintenance areas, and other ancillary spaces.
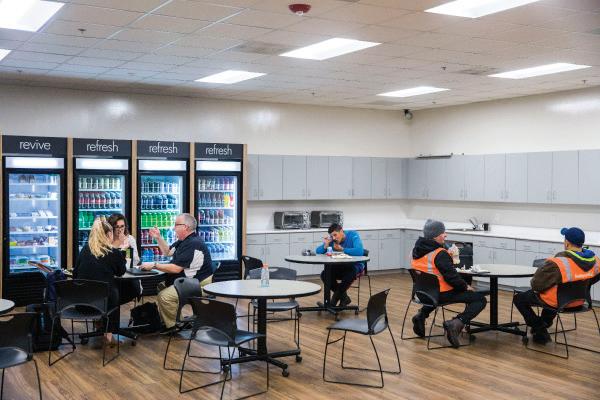
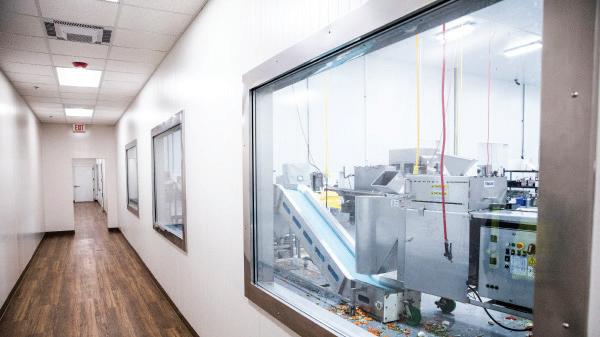
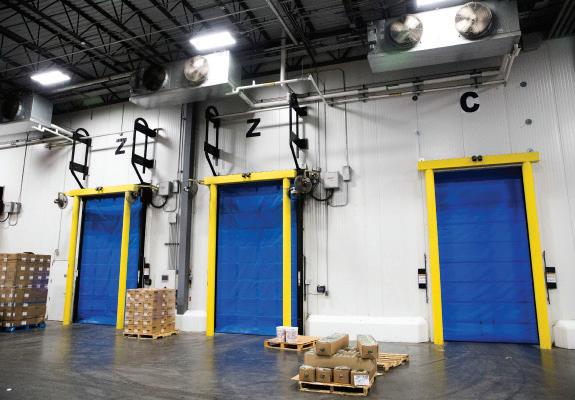
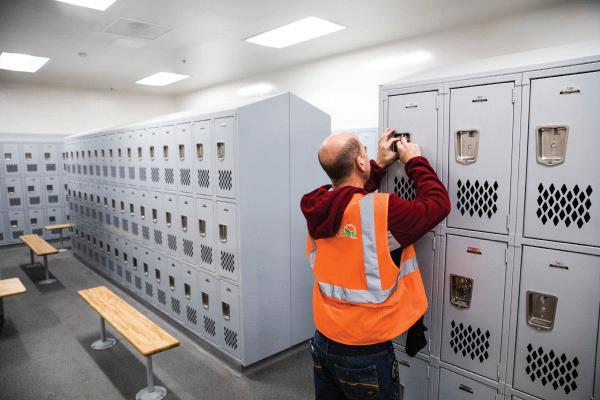

Dollar General, Alabama Distribution Center
LEO A DALY has a working relationship with Dollar General and was retained for the design of Dollar General’s 10th distribution center, a design/bid/build project in Bessemer, Alabama.
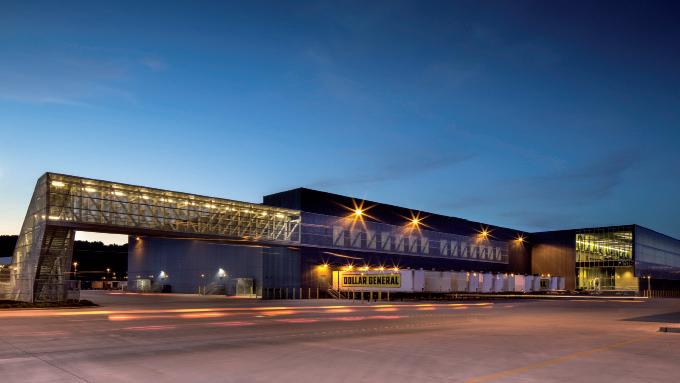
The center, located on 106 acres consists of five new buildings completed in spring 2012. Five separate buildings total approximately 975,000 square feet of new construction. The buildings include a 958,000 SF Dry Storage Warehouse/Administrative Office and Employee Welfare Building, 13,3000 SF Dispatch Office/Truck Maintenance Facility, 400 SF Receiving Truck Concourse Guardhouse, 300 SF Shipping Truck Concourse Guardhouse and 1,300 SF Pump House and 1,300 SF Pump House/Fire Protection Reservoir.
LEO A DALY also provided provisions for future expansion of 200,000 SF to the dry storage warehouse. Site work also included auto parking, truck circulation and parking, landscape, storm water detention/ retention, perimeter security fencing/gates, site lighting and all site utilities (domestic water, fire loop/hydrants, sanitary sewer, storm sewer, electrical power distribution and duct banks between all buildings).
Design; Architecture; Interior Design; Structural, Mechanical, Electrical, and Civil Engineering; Construction
The design explores the relationship of scale through a dialogue between employee and warehouse space. Paths are emphasized; pedestrian paths are accented with vehicular patterns that support product shipping and receiving.
Dollar General, San Antonio Distribution Center
LEO A DALY has a working relationship with Dollar General and was retained for the design of Dollar General’s 12th distribution center, a design/bid/build project on a 110-acre undeveloped site in San Antonio, Texas.
The center is a slightly smaller and modified replica of the prototype in Alabama also designed by LEO A DALY. The facility is comprised of a Climate Controlled Warehouse, Dispatch Office, Truck Maintenance Facility, Shipping guardhouse, Receiving Guardhouse and Pumphouse.
The warehouse portion of the distribution center is complete with racked storage areas, shipping and receiving dock (161 dock positions), administrative offices, employee welfare areas, trucker’s lounge, battery charging, and shipping/receiving offices.
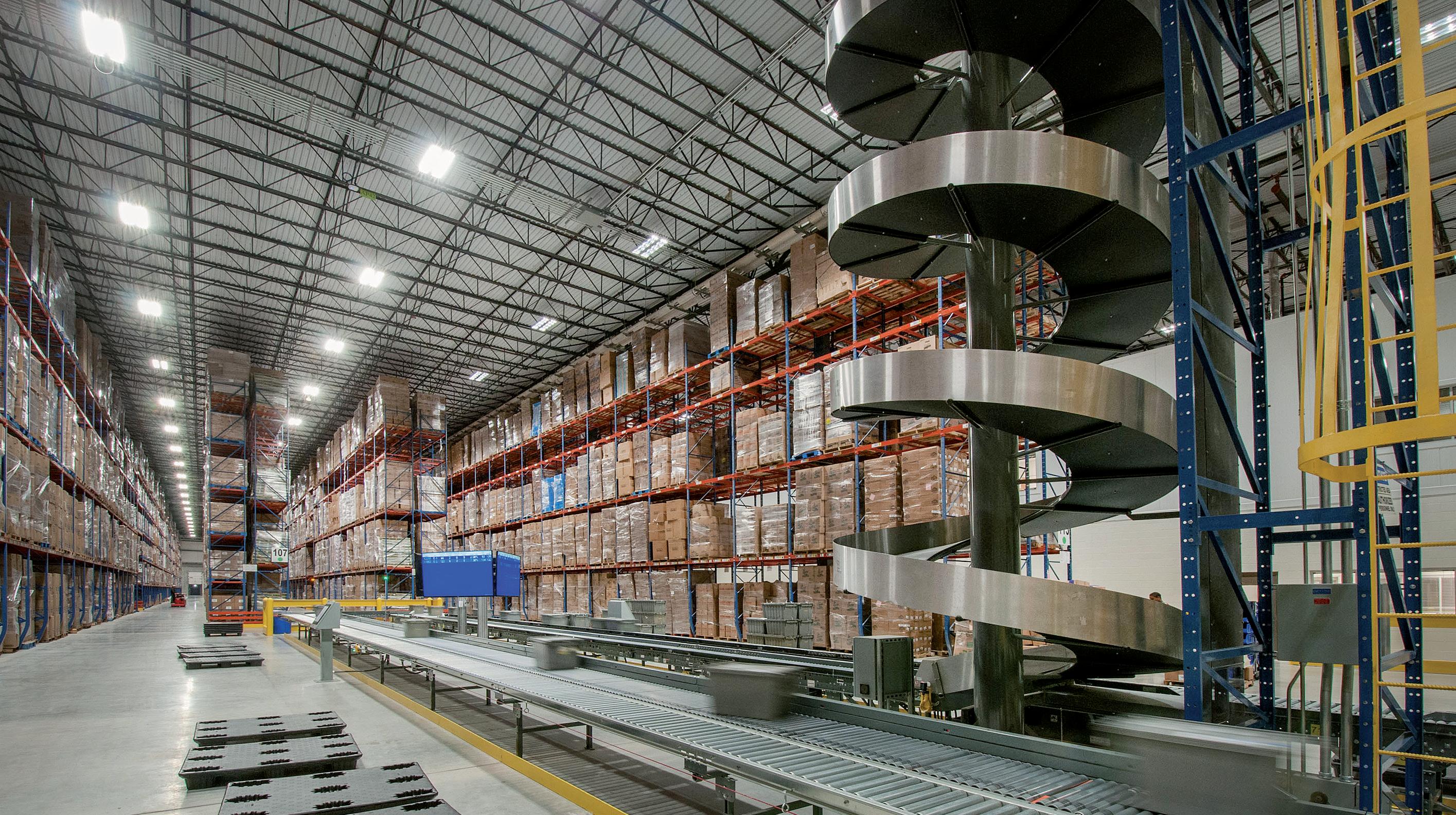
Site design includes utility design, stormwater and sanitary design, concrete truck circulation and parking, concrete automobile paving and parking, truck scale, perimeter fencing, and detention ponds.
Scope Design, Architecture, Interior Design, Structural, Mechanical, Electrical and Civil Engineering, Construction Administration
The central chilled water system is ammonia based and provides cooling for the large Climate Controlled Warehouse areas, significantly reducing energy use compared to commonly used package rooftop or other system types. The proposed system reduces annual energy consumption by 25% below ASHRAE 90.1 2007 baseline HVAC system types.
Second Harvest Heartland, New Distibution Center and Headquarters
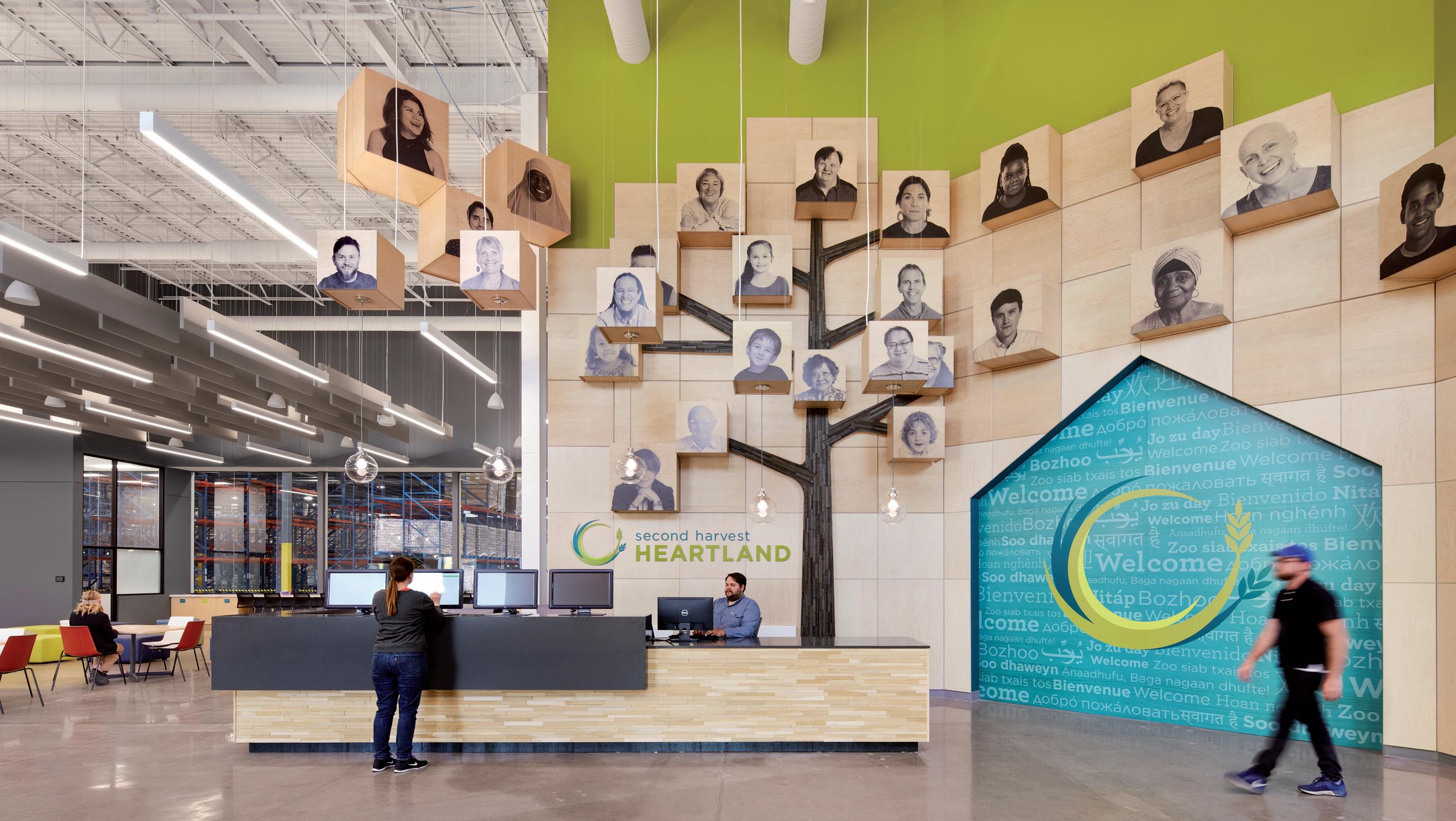
Brooklyn Park, Minnesota
Owner
Second Harvest Heartland
Size
220,000 SF
Cost
$14,000,000
Scope
Design; Architecture; Interior Design; Structural, Mechanical, Electrical, and Civil Engineering
LEO A DALY is assisting SHH with the design of a new 220,000 SF facility that will increase capacity for distribution within the region to 150 million pounds a year by 2035, and enable them to incorporate fresh produce into distribution.
To take advantage of the changing sources of food and accommodate the expanding roles of volunteers, SHH needs new facilities, vehicles and equipment to haul store and prepare perishable food for distribution. The proposed project is comprised of four main components in one new facility: 25,000 SF Volunteer Center; 10,000 SF of community program support spaces; 30,000 SF office and support area for 200 employees and 50 office volunteers, and 150,000 SF of high pile rack storage distribution center with five temperature zones.

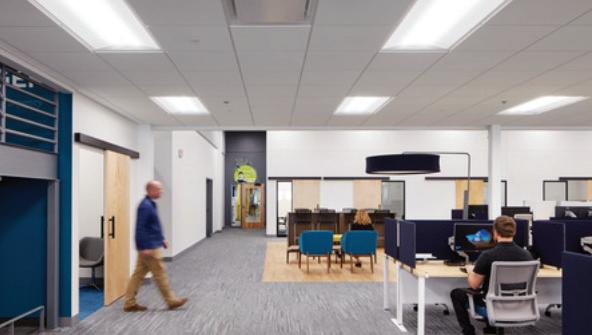
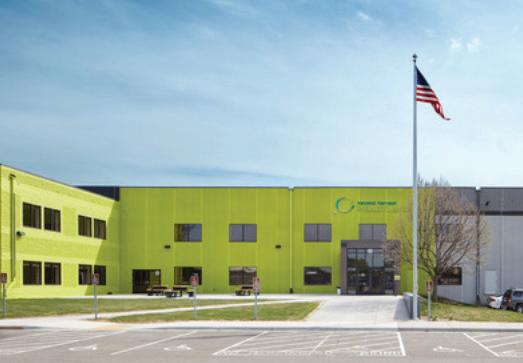
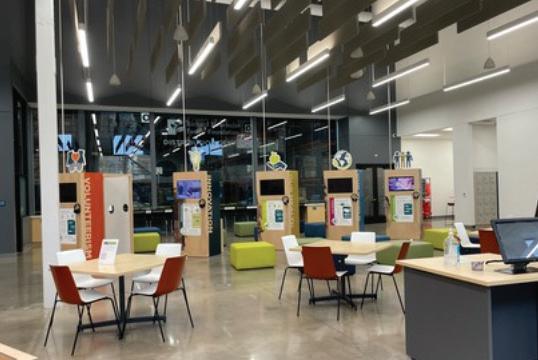
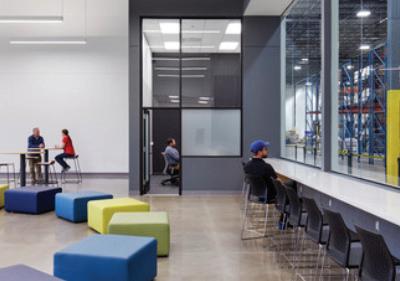
Kroger, Cincinnati Fresh Distribution Center
Blue Ash, Ohio
Owner
Kroger
Size
435,000 SF (total)
40,000 SF new freezer
90,000 SF remodeled dry grocery, maintenance, office and dock
150,000 SF existing Dry Grocery
Conversion to Cooler
100,000 SF freezer remodel
10,000 SF office remodel
Cost
$28,000,000
Scope
Design, Architecture, Interior Design, Structural, Mechanical, Electrical and Civil Engineering
Kroger is the largest supermarket chain and the second largest retailer in the U.S. and they continue to grow. A distribution center was needed in the Cincinnati area and they purchased a former Nash Finch warehouse for repurposing.
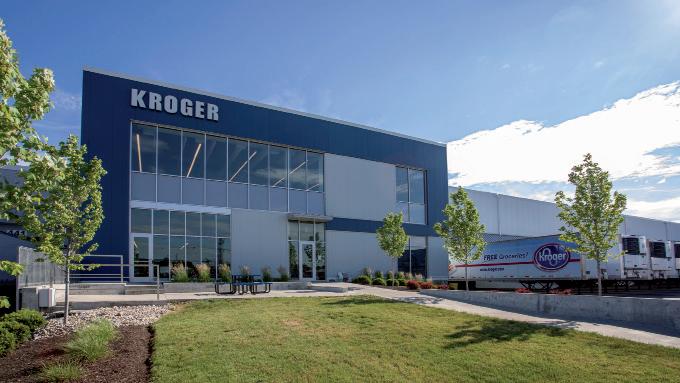
LEO A DALY led the design of the renovation of the existing 390,000 SF distribution center to suit Kroger’s unique program. The renovation included modernizing of approximately 217,000 SF existing dry grocery storage warehouse, truck maintenance space, office, employee break area, and dock. The team also converted approximately 150,000 SF of the facility to perishable cooler space and added a 45,000 SF of addition to include a freezer, cooler and mechanical room. The existing 1960’s warehouse posed a variety of code related challenges to the team including dated fire safety and fire suppression solutions.
Kroger had identified the crucial need to address the cost of employee retention within their new facility. Implementing a strong workplace strategy goal for the project was imperative. The team focused on increasing brand identity through a fresh and vibrant palette and emphasizing key employee amenities to increase Pride-of-Place.
RMR Group, Multi-Location Site Assessments
Various Locations
Owner RMR Group, Confidential Tenant Locations
11 locations in the following states: Texas Georgia, Florida, Arkansas, Ohio, Tennessee, Oregon, South Carolina, Arizona
Within the Food, Distribution and Manufacturing market, we are seeing an increase with clients to densify properties for best use closer and closer to urban cores. This trend maximizes property value as well as takes advantage of a larger urban work force.
RMR Group saw an opportunity in their existing sites to optimize for denser industrial uses. To do this they needed an analysis of existing sites to understand the potential uses with the goal of repositioning the remaining unused portion of property for future development.
LEO A DALY evaluated eleven sites across the country weighing the advantages and disadvantages of each site. The evaluation included regional analysis for leveraging major transportation systems, local jurisdictional requirements, maximum site and building development based on survey information, and rough order of magnitude pricing allowing for regional factors. Nine out of eleven sites would have an existing tenant remaining on part of the property. Another part of LEO A DALY ‘s tasks was to recommend subdivisions of several of these sites for broker’s evaluation of a phased development approach. The sites were evaluated for the following potential uses: distribution center, fulfillment center, industrial uses and data center.
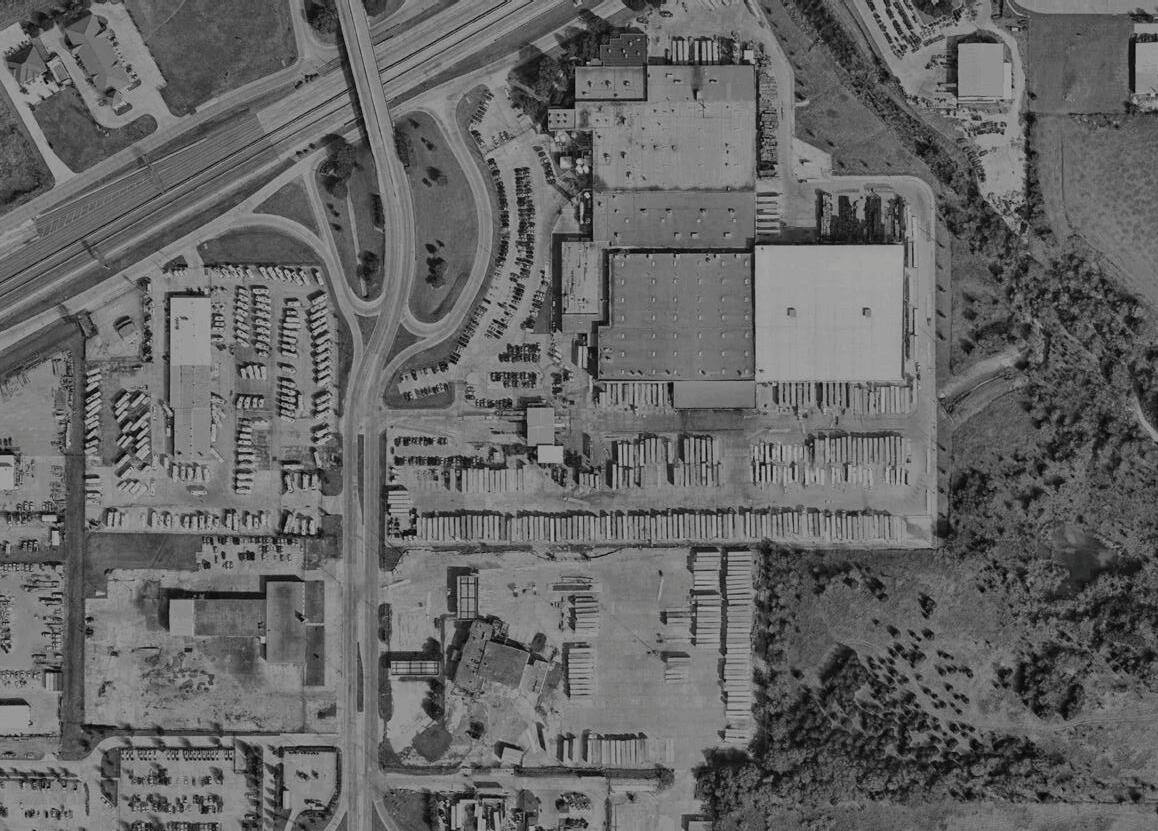
Arthrex, Corporate Headquarters
Naples, Florida
Owner
Arthrex, Inc.
Size 132,000 SF
Cost
$15,929,000
Scope Architecture
Arthrex is a global medical device company that has pioneered the field or arthroscopy and has developed over 1,000 innovative products each year. In 2004, LEO A DALY provided Arthrex its full architectural services to provide new office space, research areas, and a warehouse facility designed to house highly technically trained surgeons from all over the world. Today, LEO A DALY is replacing the current headquarters to meet the needs of its growing client base.
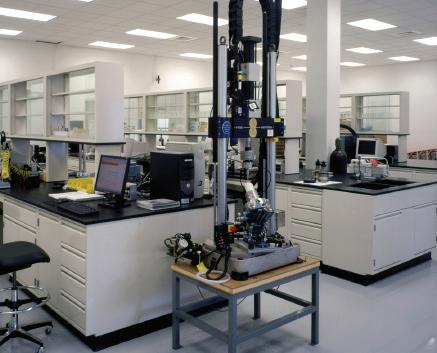
We completed an expansion study, which provided direction for a new master plan and ultimately a new campus to support multiple functions. The design process was initiated with a comprehensive programming exercise which included an understanding of the Arthrex organizational structure, identification of space standards, functional adjacencies and growth projections. A comprehensive analysis of product flow determined necessary adjacencies of critical spaces as well as those spaces requiring functional separation. These requirements are carefully addressed within the plan with dedicated parking and vehicular service areas sited to provide appropriate access. The main entrance to the corporate office is designed to create a first impression of quality to visiting physicians who are trained within the complex.

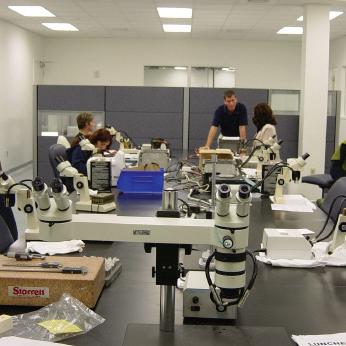
Historically, Arthrex maintains an employee turnover rate of less than two percent annually. Correspondingly the quality of the work environment was a critically important factor in designing the complex. Recognizing the positive benefits that natural light plays in the efficiency of the work place, the building is designed to capture a significant amount of natural light. By strategically locating circulation against exterior walls the plan captures and distributes natural light deep within the adjoining spaces by utilizing the concept of “borrowed light” and light shelves. Flexibility is at the core of the design concept. As the needs of Arthrex evolve over time, the facility is designed to change and adapt in a corresponding fashion.
Toro Company, Corporate Headquarters and Product Development Lab Expansion
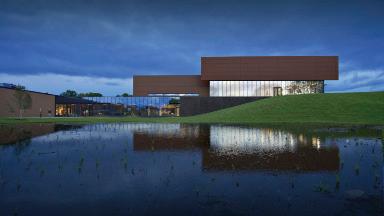
Bloomington, Minnesota
Owner
The Toro Company
Size
Phase 1 - 75,000 SF
Phase 2 - 399,000 SF
Cost Confidential
Scope
Needs Assessment, Programming, Architecture, Interior Design, Civil, Structural and Electrical Engineering
LEO A DALY was commissioned to conduct a needs space assessment for various departments within Toro headquarters and to define the scope for expansion of the PDL (product development lab). The Assessment reviewed the overall operations and sequential workflow of systems and product development activities. The immediate observation was identified; the organizational workflow had not been refined or improved as advances in technology, increases in equipment, process improvements occurred and in fact, five subsequent additions housed the newer operations, but had not adequately folded into the workflow in the proper sequence. Consequently, the organizational flow was disjointed and based upon past traditions. The resultant was a re-thinking of operations, the reorganization of departments
The design work began with a comprehensive assessment and evaluation of all facilities for code, infrastructure, maintenance and hazardous classifications. A full space program was developed, optimum adjacencies were graphed, trends in new product labs identified, and a range of solutions were explored; some simple, others more invasive. The resulting project was a multi-phase renovation. Phase 1 entailed a new administrative office facility, which forwards the brand of Toro and provides employees with contemporary amenities such as dining, fitness, green roof and outdoor spaces. Phase II includes the full and incremental reorganization and renovation of the product development lab, product evaluation department and design engineering. Specific workplace environments include: media studios, media editing, AG lab, instrumentation, additive manufacturing, industrial design, electrical lab/shop, technical training room/shop, Residential Lawn Care shop and package engineering.