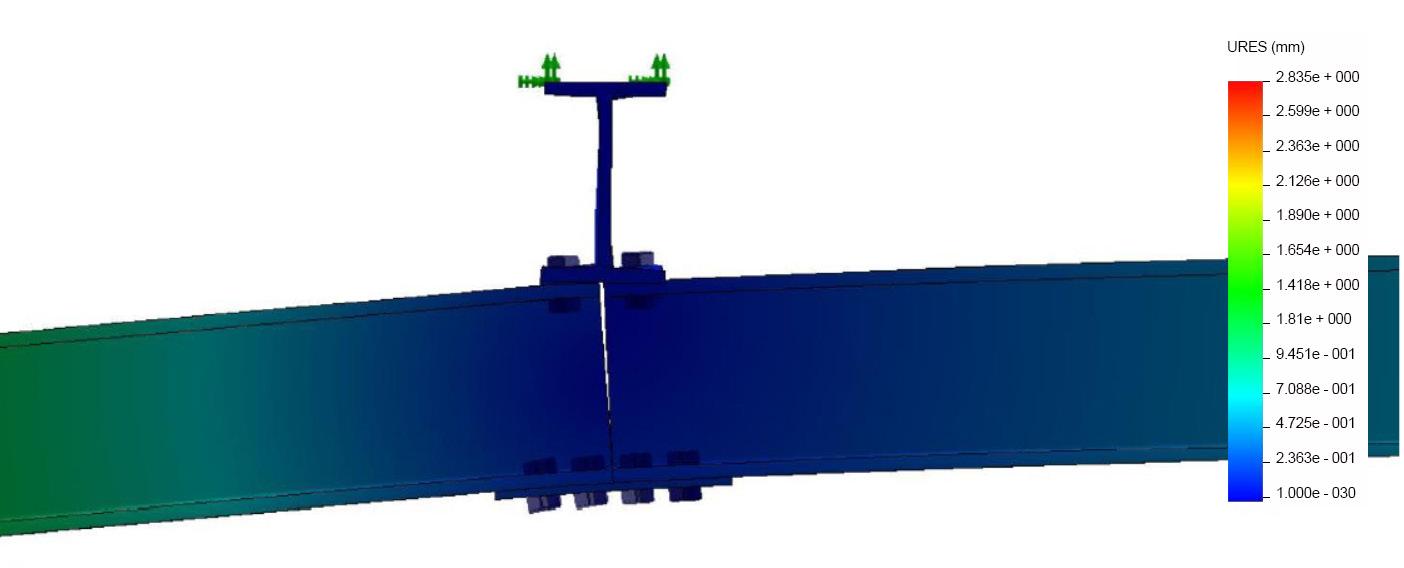
5 minute read
Design and finite element analysis of lifting equipment
An important note. This article is by no means intended to be a final or comprehensive overview of how any item should be designed or which standard(s) must be applied, but rather a basic overview of how FEA is one approach can be used to determine the safe parameters of a design.
In our modern world and society we live and work in today, and the requirements set before us in terms of legislation for meeting safety and environmental requirements, engineers developing new products and more so specifically lifting equipment must ensure their designs comply with strict design codes and applicable standards at all times.
Why can FEA be required?
The use of FEA assessments is required by most structural codes and standards, and as legislated in the case of lifting machinery which requires that all lifting machinery and lifting tackle are designed by a technically accepted standard(s), these standards among other detail the requirements for designers and engineers to be met such as material requirements, welding, NDT and eventually load testing. An example may be DIN 18800 – 2 wherein the standard requires the use of computer analysis that in turn must comply with further codes during the design of EOT crane structural steelworks, which requires that the analysis provide proof that all components and connections have the required loadbearing capacity and serviceability. Also, every country has a design code which sets out requirements for structural design and the applicable standards used. South Africa is no stranger to this and has, for example, SANS 10160 in parts, with part 6 for specifying the imposed loads for EOT cranes.
What is Finite Element Analysis - FEA?
Finite Element Analysis or FEA software as it is known is a representation of the continued, actual physical part being analysed in reaction to real-world situations and effects. The software creates a representation using nodes, which connects to illustrate form elements and under simulated loading an engineer or designer can determine if the designed product will break, tear, crack or perform as intended. What are the examples of different types of FEA simulation used? Absolute and Comparative FEA – As an example, if the design requires a rope and the designer has no idea how much load the rope would sustain, then a comparative analysis would be used.
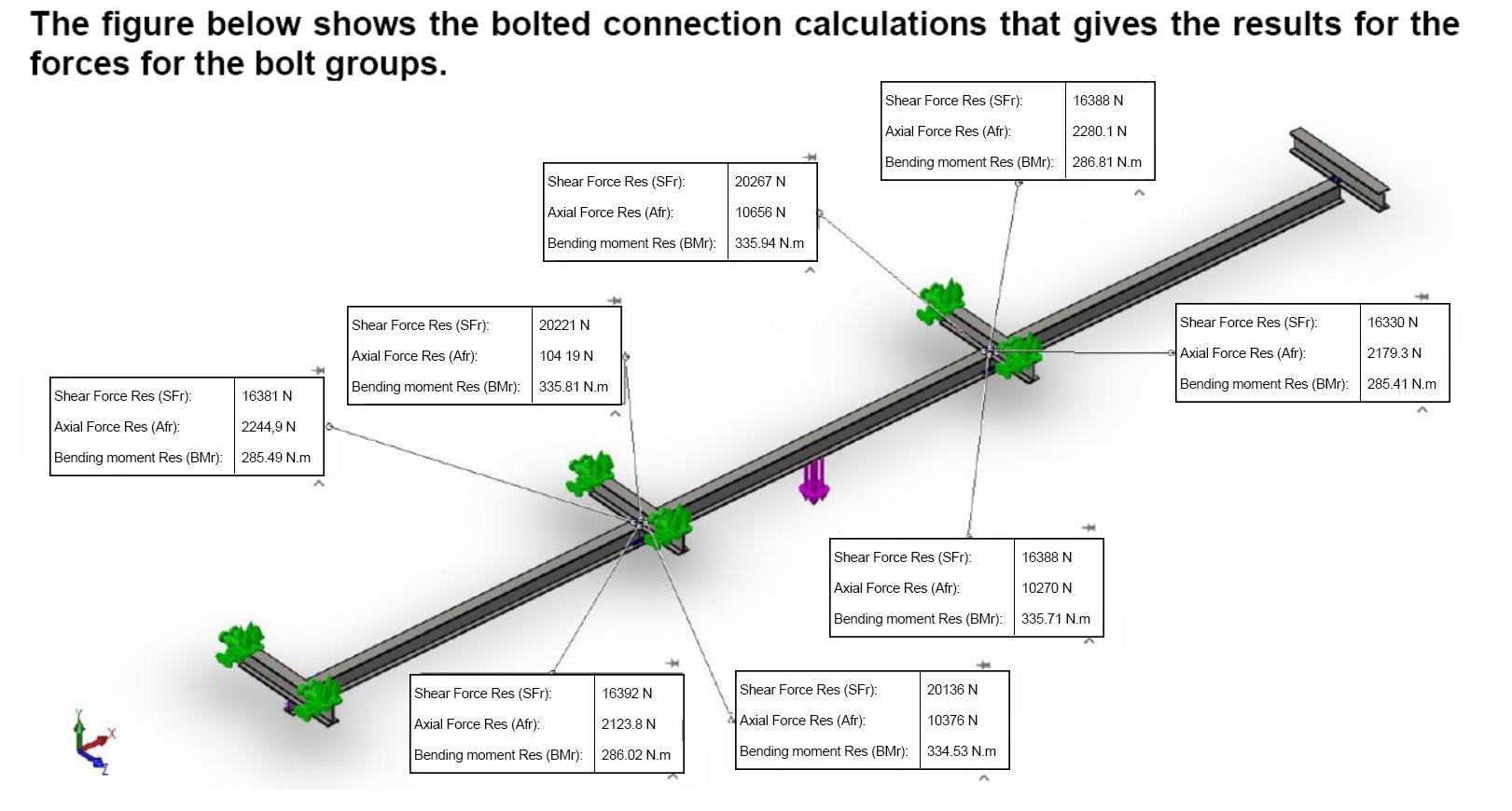
It is used when the designer wants to change certain conditions so that the product performs better than it already does. Dynamic and Static FEA – An example may be as to what the impact of acceleration might bring as a result.
This FEA application can simulate how fast or how slow loads are applied. Non-linear and linear FEA – An example is to test the elasticity of different objects. Linear analysis is used where there is a direct scalable relation between applied force and displacement and non-linear is to see if there has been any change to the initial condition on a design. We can use FEA in simulations such as fluid behaviour, thermal transport, wave propagation, growth of biological cells and even
solve physical requirements such as structural stresses, strain and buckling. The FEA results can then be compared against physical calculations that had been made by the designer or engineer to confirm findings and if required make changes to the design to better it.
Can anyone use FEA?
CAD operators or draughtsmen generally apply themselves to the design of the part or components, but with FEA the person executing the analysis must be competent and have a thorough understanding of engineering principles such as material properties, stress, for example, Von Mises stress as one, reaction forces and much more as well as how to apply and interpret them.
LMTTS as a company offers as one of their various services CAD design and FEA analysis. We often receive inquiries from clients for monorail designs and fabrication. Once the parameters have been established, structural steel is identified following design codes and other applicable standards and drawn into CAD as part. The part is transferred into the FEA software and data such as the material yield strength, density, Thermal conductivity, specific heat, ultimate stress etc is then fed into the analysis. Constraints and forces are applied and the software can then solve the application. Once the simulation has been run the results are displayed and can be exported for example on a word document for evaluation. In the case of a monorail, the engineer can evaluate the deflection against the values in the standard (s), a torsional failure which is a critical value in analysis and design of monorails as well as several other values.
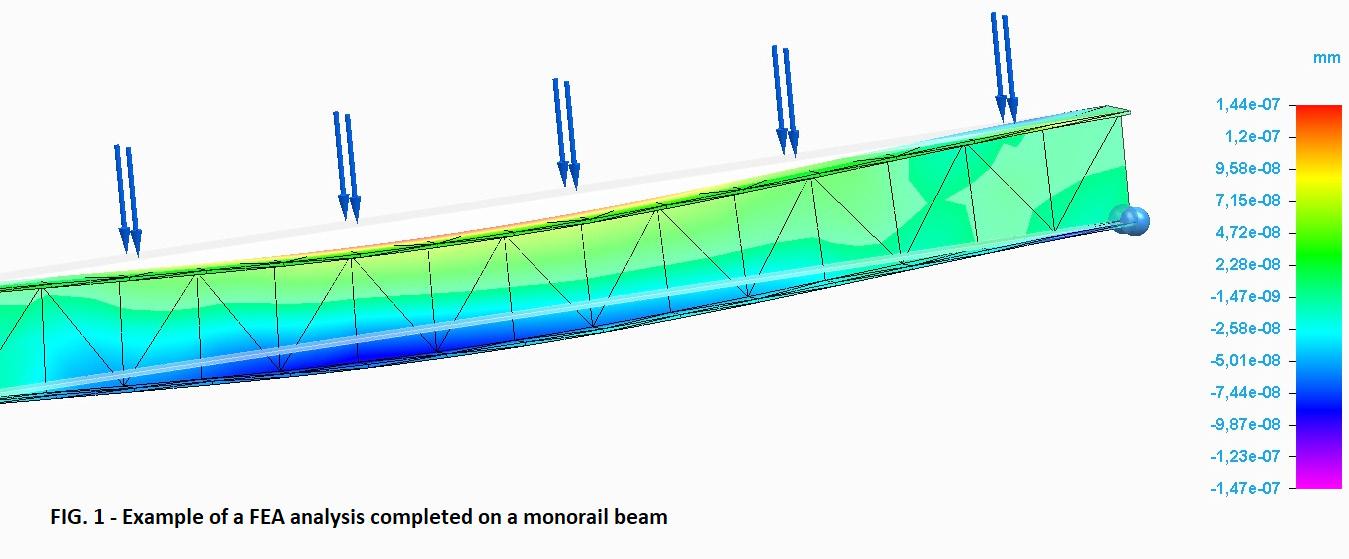
An important value would be the anchor points of a monorail which can either be welded or bolted and particular attention should be paid to this analysis.
Load Moment (Pty) Ltd,
Testing and training services Sishen (Pty)Ltd
• Mechanical & Structural Engineering – CAD design | FEA | Analysis | Core drilling • NDT and Welding – NDT testing (VT, MT, PT, UT), Thickness gauging, Hardness testing, Welding Procedures • Fabrication – Design and fabrication of under the hook lifting attachments (Spreaders, Work platforms etc.) • Project Management – Asset management, Project scheduling, Quality control, Life cycle costing • Plant design and fabrication – Structural plant design and fabrication • Inspection and Load Testing – Inspection and load testing of lifting machinery • Lifting equipment sales – Supply and sales of lifting equipment (SWR, Shackles, Webbing slings etc.) • Repairs and servicing – Repairs and services to lifting machinery • Hydraulic repairs and maintenance – Repairs and maintenance to Industrial hydraulic lifting equipment • Lifting and rigging – Lifting planning and execution • Training – Operator and SME training
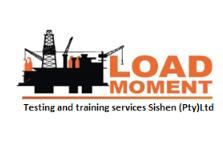
Kathu, Northern Cape, South Africa
LME no. 269 Level 2 B-BBEE