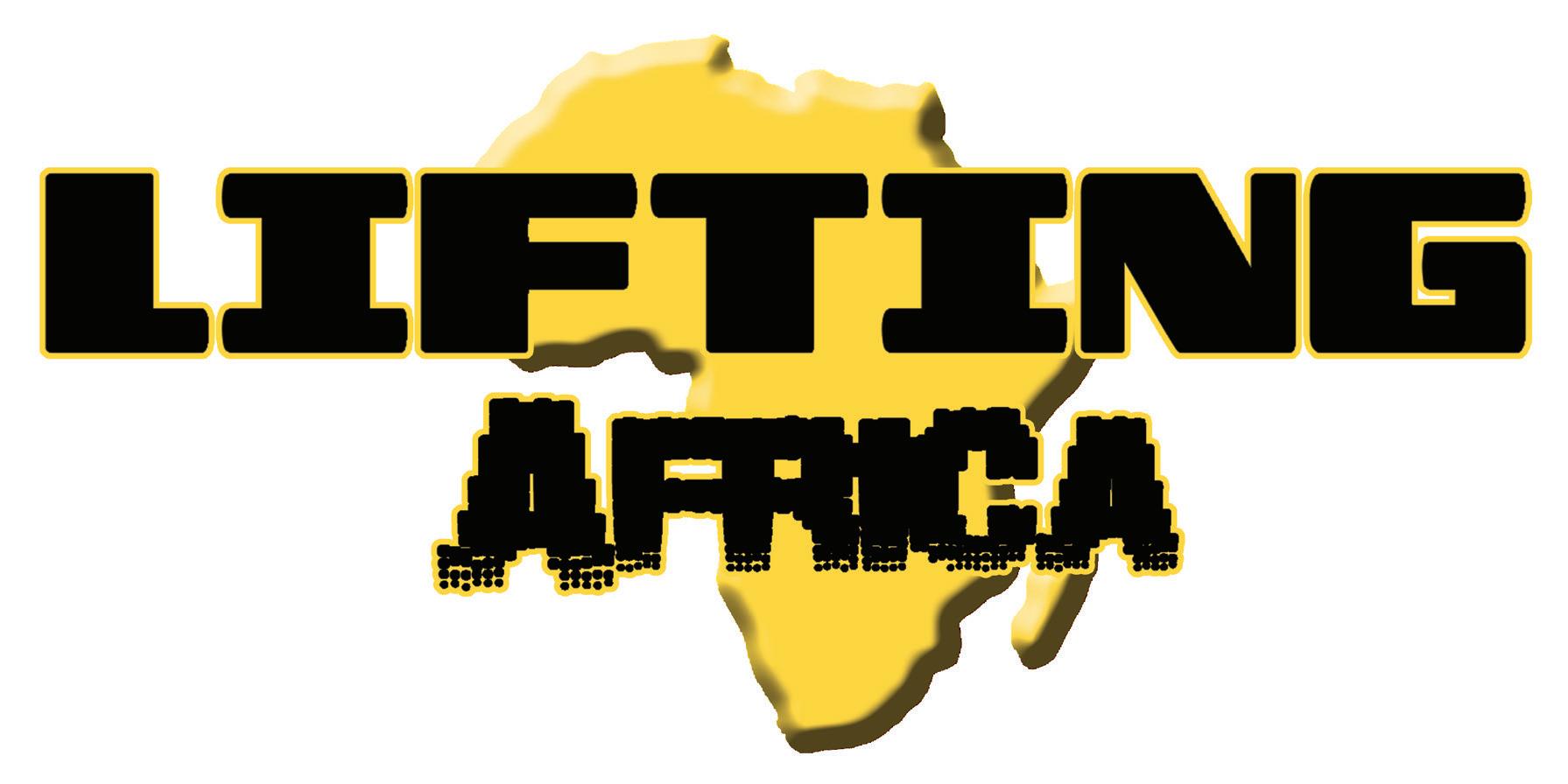
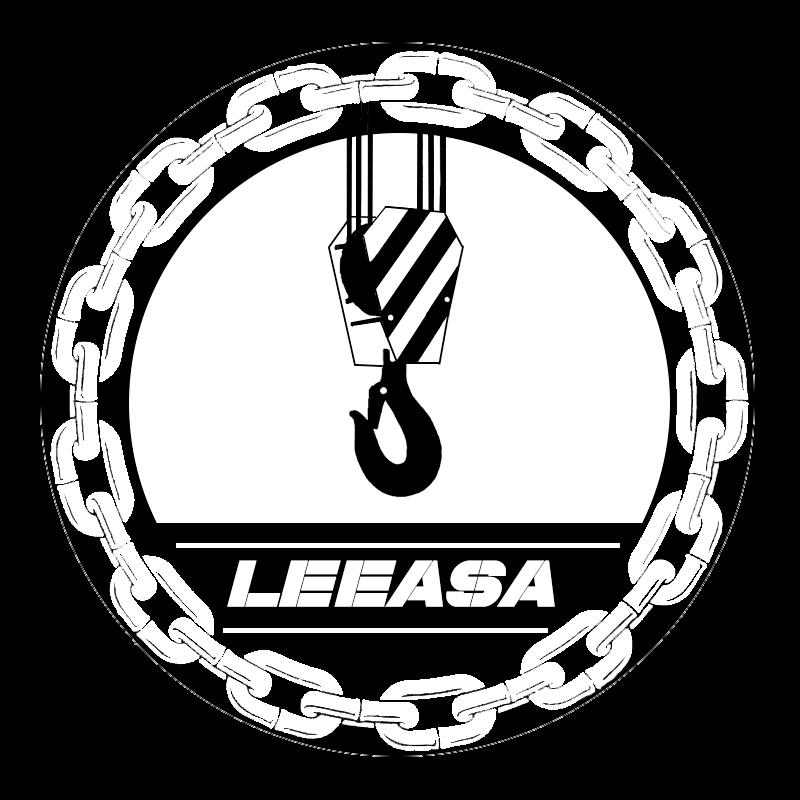
Every day across South Africa, machinery hums, structures ascend and loads are lifted and moved, almost like it’s second nature. Yet, navigating the labyrinth of regulations and legalities around lifting equipment can feel like deciphering hieroglyphics. Within this landscape, industry association LEEASA plays a pivotal role, steadfast in its commitment to keeping safety at the forefront of operations. Lifting Africa finds out more.
Opening LEEASA’s website reveals the clear focus for 2024. Front and centre is the organisation’s newly launched Vetting Guide, a document to ensure that endusers of lifting equipment and their service providers are compliant with legislation and confidently so.
According to Ashley Davis, LEEASA Chairman, the guide serves as a cornerstone to foster a culture of safety and excellence within the lifting industry. “Most end-users of our equipment are unaware of regulations guiding LMIs and LMEs when choosing a reputable partner to service equipment. This guide is about making it easier
for equipment owners to know if their LMIs and LMEs are compliant with the law.”
LEEASA director Kyle Graham emphasises that ensuring compliance in the industry is no longer a “nice-to-have” but a necessity. “Initially, the industry was structured for self-regulation, but it became evident that little to no regulation was being enforced. Recognising this gap, we understood the importance of ensuring that endusers and responsible parties were fully informed about their legal obligations when selecting a service provider for on-site work. Many companies were unaware of
their legal responsibilities concerning inspections, testing, and certification of their lifting equipment, while service providers were engaged in tasks beyond their competency. This posed significant risks to both compliance and safety for end-users,” he says.
Enhancing industry dynamics: creating value that counts
The vetting guide aims to clearly outline the requirements and necessary documentation for appointing a service provider to conduct on-site work, ensuring all activities adhere to legislative mandates and standards specified under the OHS Act. Its primary goal is to mitigate risks by engaging reputable service providers with the appropriate competencies, documentation, and equipment needed to execute tasks by regulatory standards.
The document has significantly benefited the industry by providing stakeholders with vital information, enabling them to vet documentation and select service providers with the requisite scopes and valid certifications. Moreover, it underscores the importance for all LMIs/ LMEs to educate clients on compliance requirements and operational procedures to ensure adherence to legislative mandates and relevant standards.
According to Vice Chairperson Andries Agenbag, such documents developed by industry organisations play a critical role in fostering transparency, standardisation, and, ultimately, safety across the sector, serving as invaluable resources for stakeholders and regulatory bodies.
“Ensuring widespread distribution of the guide is paramount, aiming to reach as many end-users as possible across all the sectors that utilise lifting machines,” he says. “Additionally, we are developing complementary technical guides that we will send out throughout the year that will provide further detailed information tailored to specific categories, guiding end-users on compliance requirements and operational procedures related to lifting machinery.”
For LEEASA, these initiatives are crucial, mainly as LMIs may not consistently relay necessary information to end-users, often focusing solely on promoting load tests without comprehensive guidance on compliance obligations.
“One must not forget,” says Davis, “but the responsibility falls on the end user to ensure that equipment
undergoes inspection and load testing by a reputable LME employing an LMI. End users bear the onus and are held accountable for engaging service providers with the correct scopes of competency. They play a crucial role in regulating the industry by reporting discrepancies and ensuring that all stakeholders are on track.”
With this perspective in mind, LEEASA is advocating for increased collaboration, not only among its members but also with lifting users and government entities.
“Collaboration is essential; we must all work together to enhance compliance and safety standards within the lifting industry,” says Davis.
The industry faces several challenges, including a need for modulation, insufficient transparency, and a lack of understanding regarding legal requirements among registered persons or LME business owners. These hurdles underscore the importance of comprehensive education and regulatory frameworks to address gaps in compliance and promote transparency within the sector.
“Some companies quote and carry out work outside their scope. There are also companies that “take shortcuts” when testing certain applications. It is essential to ensure that the entity carrying out the work has the correct equipment and scopes before appointing the service provider,” explains Graham.
Davis and Agenbag emphasise that the devil is indeed in the details: “Working together, we must tackle these challenges, ensuring clients are fully aware of their legal obligations and are educated about the requirements and testing procedures.”
Already, efforts are paying off. According to Council Member Surita Marx, requests for the Vetting Guide and other similar documents are increasing. “The Department of Labour has expressed interest in having LEEASA present at its national conference and has requested additional copies of the Vetting Guide for distribution. This recognition underscores the importance and relevance of LEEASA’s initiatives in promoting safety and compliance within the lifting industry.”
LEEASA, +27 (0) 79 658 5602, admin@leeasa.co.za, www.leeasa.co.za
Mr. Aaldrik Graham Kiewiet
Mr. Alan Victor Botha
Mr. Albert Anthony Freeme
Mr. Alfa Janes Grouws
Mr. Amogelang Gilbert Mmusi
Mr. Ananias Zhou
Mr. Andrew John Ferguson
Mr. Andries Aucamp
Mr. Andries Josias Agenbag
Mr. Armand du Plessis
Mr. Johan Frederick Herselman
Mr. Johannes (Jaco) van Biljon
Mr. Johannes Hendrik Snyder
Mr. Johannes Jurgens Marais
Mr. Johannes Mnyameni
Mr. Joseph Johannes van Huyssteen
Mr. Justin Henry Brown
Mr. Kebareng Daniel Molausi
Mr. Kesekang Segole
Mr. Khathutshelo John Phalandwa
Mr. Henry Oswald Kerr
Mr. Ian O’Hara
Mr. Israel Mooketsi
Mr. Jacobus Rudolph Kruger
Mr. Jaen Pienaar
Mr. Jan Frederick van Niekerk
Mr. Janus Jacobus Van Biljon
Mr. Jetro Mzwandile Ngwenya
Mr. Warren Naude
Mr. Weddington Chimbane Moyo
Mr. Werner De Bruyn
Mr. Werner Hermann Schroer
Mr. William Henry Pepler
Mr. Yogandren (Donny) Soobramoney
Mr. Zenzele Siphamandla Ntshakala
“These records are up to date at the time of going to print”
The capital equipment buying decision carries risk. There is cost and, quite often, a deadline. The scale of financial outlay must be carefully considered: if incorrect choice leads to equipment underperformance or, worse, failure, a replacement will have to be bought. Care and caution are the watchwords.
Choosing a factory crane is especially tricky. Condra, a leading manufacturer of overhead cranes and hoists, offers the following advice to smooth the buying process and minimise risk:
First, quantify the cost of lost production in the event of a breakdown.
Always high, this figure can become unimaginably so if long shipping times are needed for component parts to arrive, the equipment lying idle during this period.
Yet the negative impact of crane breakdown can be minimised if technical support using locally held spare parts is immediate.
Condra’s advice is to ask all wouldbe crane suppliers about their spare parts holdings – where are they stocked and, if abroad, how long would be the time delay between breakdown and spares arrival? If the answer is measured in weeks or months, be wary. Condra guarantees delivery of its own spares within 48 hours in South Africa, and in five days anywhere else in Africa. Still, buyers at the time of equipment purchase are often dazzled by the glamour of European brands, or seduced by the low price of a Chinese-built machine.
However, if a breakdown requires replacement of an end-carriage
or crab, how long will it take for that component to arrive from the manufacturer? What will be the shipping time? How much production will be lost, and at what cost?
A second factor related to breakdown is the degree to which the crane may be described as robust.
This is important because of the heavy-handed nature of many operators. Local environments are usually less forgiving than those in Europe, placing more stress upon the strength of the crane’s build.
Condra addresses this issue through a design philosophy focused on
strength and durability. Its success is reflected in the company’s solid reputation for mechanical reliability under corrosive and abrasive environments, and under wide extremes of temperature, humidity and altitude.
One example of the company’s robust crane design is to be found in rigid frame alignment, the girders being bolted to the end-carriages to ensure that accurate wheel alignment is maintained throughout operation, reducing wear on the wheel flanges.
A third element to be investigated is design expertise. All OEM equipment manufacturers design in-house, but the important question to ask is where that expertise is located.
How readily accessible is the design office, and how willing are staff to discuss adapting product capabilities to the requirements of a particular application?
If the manufacturer is located in Europe or China, then African customers will not have easy access to qualified consultation.
By contrast, Condra claims advanced levels of design flexibility and staff availability.
The company’s design office is located at the main factory in Johannesburg, with qualified staff on had at a second works in Cape Town.
There is direct representation in Durban. Europe is serviced and supplied from a subsidiary company in Gabrovo, Bulgaria.
With regard to technical support, Condra’s network of authorised agents has been in place for years.
South Africa is fully covered, and there are qualified technicians at agents in Namibia, Kenya, Botswana and Zambia.
The company is currently establishing service relationships with representatives in Mozambique, Zimbabwe, Tanzania and Angola.
Internationally, Condra has agents in South America, Australia and the Middle East. Condra’s advice: Think, before you buy. Do the necessary homework. Take your time, and
always remember the old adage: Buy in haste, repent at leisure. It bears considering, coming as it does from a market leader with an almost 60-year pedigree in lifting applications across manufacturing, warehousing and mining.
Condra claims a local product content higher than any other overhead crane supplier in central and southern Africa, with an adaptable product range for all applications: hook duties, grabbing, magnet, ladle, bucket or stacking applications, and operation manually, electrically, or in combinations.
Typical configurations include single-girder and double-girder overhead travelling cranes, portal and semi-portal cranes, and cantilever cranes (pillar, jib, wall or walking). Hoists are manufactured in a number of standard models from 1 ton to 500 tons. Automation is optional across the range.
Condra, +27 (0) 11 776 6000, sales@condra.co.za, www.condra.co.za
Tadano Ltd is set to revolutionize the construction equipment industry with the launch of the Tadano EVOLT eGR-250N. This fully electrified rough terrain crane, boasting a maximum lifting capacity of 25 tons, is a pivotal addition to Tadano’s commitment to reducing carbon emissions and embracing sustainable practices.
Scheduled for release exclusively in the Japanese market on December 8, 2023, the EVOLT eGR-250N is the culmination of Tadano’s dedication to environmental responsibility and the realization of their Green Solutions strategy. The company
aims to reduce CO2 emissions from their machines by 35% by 2030, ultimately striving for complete climate neutrality by 2050.
EVOLT - Evolution Meets Voltage
The EVOLT series represents
Tadano’s electrified product lineup, symbolizing the evolution of construction equipment towards a more sustainable and environmentally friendly future.
World’s first fully electric rough terrain crane
Breaking new ground, the EVOLT eGR-250N is the world’s first fully electric rough terrain crane put into practical use, exclusively available in Japan. It seamlessly executes all crane and travel operations using a battery as the power source, setting a new standard for eco-friendly construction equipment in the Japanese market.
Same basic performance as combustion engine model
The EVOLT eGR-250N maintains the exceptional lifting and running performance of the conventional GR series, tailored for the specific needs of the Japanese construction industry. With a maximum lifting capacity of 25 tonnes, a working radius of 34m, ground lifting height of 44.2m, and a maximum speed of 49km/h, operators can expect the same reliable performance as the diesel engine model, ensuring
a smooth transition to electrified machinery without compromising functionality.
In addition to environmental benefits, the EVOLT eGR250N introduces a significant reduction in noise levels during travel and crane work, providing added value for use in noise-sensitive Japanese construction sites.
Equipped with two high-output motors boasting a maximum output of 97kW (132PS) and a maximum torque of 2500Nm (255kgfm), the EVOLT eGR-250N delivers improved acceleration performance and smooth running. This design minimizes shock during gear changes, significantly reducing operator stress and ensuring a more comfortable and efficient work experience.
The heart of the EVOLT eGR-250N lies in its efficient lithium-ion battery with a total capacity of 226kWh. A full charge enables an average day of crane work and driving in the Japanese construction landscape, offering versatility and productivity on the job site. The lithium-ion technology not only provides a reliable power source but also aligns with Tadano’s commitment to sustainability by significantly reducing the carbon footprint associated with traditional diesel-powered cranes.
With an eye on convenience and efficiency, the EVOLT eGR-250N adopts CHAdeMO for quick charging and AC200V three-phase commercial power connection for normal charging. This allows crane work to be seamlessly performed while plugged in at the site, ensuring continuous operation without unnecessary downtime. Quick charging takes approximately 2.5 hours, while normal charging requires approximately 8 hours.
The EVOLT eGR-250N offers an impressive battery autonomy, with crane work lasting approximately 5 hours and traveling approximately 42km on a full charge. For crane work only, the autonomy extends to approximately 11 hours, and for driving only, approximately 70km.
Enhancing safety and efficiency, the EVOLT eGR-250N offers the optional LIFT VISUALIZER. This feature utilizes a suspended load monitoring camera, allowing operators to monitor suspended loads directly from above. Particularly useful in blind spots such as rooftop work, the LIFT VISUALIZER, in conjunction with the AML control system, displays crucial information on work status, load moment, 100% stop position, and more on the monitor, improving overall work safety and efficiency.
Tadano Group, Damien.Bizjak@tadano.com, www.tadano.com
What is the main purpose of conducting inspections on lifting machines and equipment?
To ensure risk is being mitigated through the identification of gaps/ defects and hence subsequent hazards, both physical and systemic. Effective inspections therefore, enable the owner to ensure his/ her assets are safely operated and maintained through the identification, assessment and therefore management of risk.
There are various types of inspections that are required and referred to by the Driven Machinery Regulations and international standards in terms of lifting assets. Overhead Cranes and hoists typically require the following main inspection types:
• Pre-use Inspections (usually daily and performed by the crane operator)
• Frequent Inspections (Quarterly intervals and performed by an experienced Technician)
and scope. Common knowledge and industry trends show that the effectiveness of these different inspections is often reduced during implementation, essentially leading to a culture of complacency.
The requirement and scope for a Major Inspection is described in SANS 10375 and SANS/ ISO 12482. Major Inspection is also referred to as “Special Assessment” in some international standards (ISO 12482 and ISO 9927-1), including previous versions of SANS 12482. Major Inspections are however the most common term used. Both SANS 10375 and ISO 9927-1 have been scheduled under the Occupational Health and Safety Act, 1993 and forms part of the incorporated safety standards as per Government Notice No. R. 542 dated 24 June 2015. The Department of Employment and Labour is therefore ensuring crane owners adopt 10 yearly Major Inspections as part of their inspection regime and strategies.
cranes without working maintenance records.
• An increase in the frequency of defects / failures
• Significant deterioration in the condition of the crane
• Significant increase in load
• Significant modification to the crane (especially modifications to the load path)
• The OEM has indicated a specified operational lifetime of the crane or minimum interval for a Major Inspection
• Periodic Thorough Inspection (performed annually by a Lifting Machinery Inspector and includes a load test)
• Exceptional inspection (performed in exceptional occasions for example when the crane is modified, or an incident has occurred)
• Major inspection (performed by an Expert Engineer or the Original Equipment Manufacturer)
Each of the aforementioned inspections has a different frequency, inspector competency
Serial Hoists, Loader-, Towerand Mobile Cranes require a Major Inspection at intervals not exceeding 10 years and all other cranes (including Overhead Travelling Cranes) at intervals not exceeding 20 years as per SANS 12482-1.
Any of the following scenarios shall typically expedite the initiation of a Major Inspection (thus earlier than the specified Major Inspection intervals):
• The crane reaching its End of Design Life (EODL)
• Re-commissioned or imported
• The crane is taken into operation for which there is no information on earlier operations and/or
• Where the instructions are not available or are deemed inappropriate or inadequate by a competent person
Important point: The initiation of these types of inspections remains the responsibility of the user/owner of the equipment.
A Major Inspection shall be carried out (or the results to be assessed and approved) by an Expert Engineer. An Expert Engineer is a Professional Engineer (typically mechanical) with adequate experience in the operation, design, construction and maintenance of lifting equipment such as cranes or the equipment being inspected.
The purpose
The purpose of a Major Inspection is to address risk from a holistic point of view, assessing the crane, in its entirety and comparing that to its original design envelope.
Throughout a crane’s useful life, it may undergo various modifications, changes in usage or maintenance strategies, all possibly affecting the overall reliability and safety of the asset. Some aspects of Major Inspections include the following:
• Identifying components that require particular attention in subsequent periodic inspections (such as non-OEM modifications).
• Communicating and quantifying risk of significant findings and defects emanating from the inspection and providing perspective on corrective actions.
• Summarising repairs and actions required to permit further safe use of crane.
• Identifying and providing scope for further investigations, dismantling and/ or additional tests.
• Reporting on “lockout” findings (to prevent further use).
• Providing a scope for any General Overhauls (GO) required on mechanisms.
• Result of the Design Working Period (DWP) analysis, where the theoretical duration of service (allowable design criteria) is compared to the actual cycles/ hours seen by the mechanism.
• Specifying the date or period for the next Special Assessment/ Major Inspection. Some companies in the mining industry have already undertaken steps to ensure compliance with SANS 10375 in terms of the requirements
for a Major Inspection to be performed on lifting machinery. CrEng would like to inform all crane owners and lifting custodians to make themselves aware of the requirement for Major Inspections on lifting equipment, that has been adopted in international and local SANS standards and that should form part of a holistic maintenance strategy of your lifting equipment. In order to address the inherent and secondary risks relating to the operation and maintenance of one’s assets, you need to be aware of what “gaps” can creep in at any stage of the Crane’s Useful Life. For this, one needs to look at the asset holistically and independently, getting perspective from the right stakeholders and industry best practices.
A Major Inspection is not just another tick box item to get done, but is a physical 10-yearly Inspection of the lifting machine and thorough assessment by a multi-disciplinary team of experts, which includes an analysis of the useful life of the crane and its design envelope.
Major Inspections are therefore a means of ensuring defects are repaired, maintenance practices are improved and legal compliance is adhered to. If done right, risks are then identified, quantified and addressed, leaving stakeholders with peace of mind.
CrEng, +27 (0) 84 740 7875, admin@creng.co.za, www.creng.co.za
Palazzani Industrie, which has always been attentive to the versatility of its products, Ragno, in addition to the already well-known hydraulic winch, offers an alternative accessory, with a simple and fast assembly system: the lifting hook instead of the basket.
In some working scenarios, such as construction sites or maintenance interventions, it can be requested to lift loads and materials of a certain weight with just the movement of the boom and with little time available to do the job. Thanks to the lifting hook, this operation is possible in total safety!
The main advantage of this accessory undoubtedly lies in
the ability to transform in a few moments and without the use of particular equipment an aerial platform with basket into a Spider with the function of a mobile crane, capable of lifting interesting loads, such as materials buildings or antennas. The lifting hook has a max capacity range from 270 to 310 kg according to the Spider Lift model.
In fact, the replacement of the basket with the lifting hook has been specifically designed to be carried out simply, quickly and safely by the operator. Precisely for this reason this option is particularly suitable for those who need to lift materials within their own work site and need to easily go from spider lift to spider crane. The use of the lifting hook instead of the basket is the ideal alternative solution for carrying out material lifting operations quickly and safely.
To ensure a safe working environment during lifting, it is essential that operators acquire a thorough understanding of the specifications relating to the
outreach, the required height and the load to be lifted before starting any activity.
This information must be carefully verified and aligned with the working diagramme reported in the reference manual, to avoid to exceed the maximum load, since in the event of overload, the movements of the platform will be inhibited, requiring the execution of safety procedures to unload the lifted weight and returned within the permitted limits.
To use the lifting hook instead of the basket, the operator must carefully follow the assembly instructions described in the supplied manual. The process consists of a few simple steps and involves the rapid disassembly of the people basket through the fixing system, followed by the assembly of the hook support plate.
If you also find yourself in this type of situation, the lifting hook instead of the basket is the one for you!
Palazzani Industrie, info@palazzani.it, www.palazzaniindustrie.com
Providing a specialised
recruitment service to the lifting equipment industry.
LIFTING MACHINE INSPECTORS
Active ECSA Registration Essential.
Nationwide
All scopes welcome.
FIELD SERVICE TECHNICIAN
REF: C543/G
Earthmoving Mechanic / Auto
Gauteng
R25 000 - R30 000 Basic Salary + Benefits.
SALES REPRESENTATIVE
REF: C222
Gauteng Pinetown Equipment Hire Sales experience. R300 000 - R500 000 Per Annum + Car Allowance + 50% Medical Aid contribution + Pension + Commission.
REF: C442
Electrician / Millwright Experience with working on Mobile and or Crawler Cranes.
REF: C543
Gauteng
Truck Mounted Crane Sales. R24 000 Basic Salary + 10% Commission on all new sales + 50% Medical Aid contribution + Petrol Allowance.
REF: C424
Lifting & Rigging Equipment Sales. R25 000 CTC + Company Vehicle.
Cape Town
Heavy Equipment Mechanic with Trade. HV switching certificate.
Millwright / Electrical or Mechanical
Northern Cape (Gamsberg)
R35 000 - R45 000 Basic Salary + Benefits.
Earthmoving equipment experience.
HIGH VOLTAGE TECHNICIAN www.liftingplacements.co.za
There is often a misconception that a tailor-made machine designed and built to fit specific job requirements will be more expensive than a standard, unmodified machine. On the face of it, a standard machine might seem cheaper, but that may only be so when you compare the purchase price of both machines.
To make a valid comparison, one must look at the bigger picture and take into consideration the savings that can be realised from a purpose-built machine, which can cut down work time considerably and do the job more efficiently than a standard machine.
Tailor-made machines, also known as custom or bespoke machines, offer several benefits for various industries and applications.
In the case of heavy lifting machines, adaptations to the standard machine can provide advantages such as perfectly fitting the intended application, ensuring optimal performance and efficiency.
Lenny Naidoo, Acting National Operations Manager at CFAO Equipment SA’s Heavy Lift division, which sells big forklifts to container handlers and the ports industry, says custom machines can be engineered to streamline processes, leading to higher productivity
and reduced downtime. “While the initial investment for custom machines can be higher, they often lead to long-term cost savings by improving efficiency and reducing operational costs. Tailor-made machines can be designed to meet changes in production requirements or new processes, making them adaptable to evolving needs,” says Naidoo.
Most often the request for a tailormade machine comes from the customer who needs more than what a standard machine offers.
Konecranes tailor-made a tyre handler to be used in the mining industry in Chile, Australia and South Africa. Strong and agile, the tyre handler is designed to carry extremely heavy wheels that cannot be lifted even by a few men.
The Heavy Lift division received a request for a specialised piece of equipment which came from a company that worked with long,
heavy pipes. A Konecranes heavy lifting forklift was modified with the addition of a special pipe handling attachment to move the pipes around.
Naidoo says it is important for customers to use solutions that are tailored for the elements of specific products and processes, as this will contribute to greater efficiencies and cost effectiveness.
“A custom-made machine can provide better solutions and quicker turn-around time, which is why we welcome customers who discuss their needs with us when they have a special operation that cannot be easily serviced by a standard machine,” says Naidoo.
Naidoo also cites the case of a customer who wanted a machine to lift very heavy concrete slabs, weighing 55 tons each.
Konecranes built a tailor-made 60ton machine with a 1,5-metre load
centre. A load centre on a forklift is the distance from the face of the forks to the load’s centre of gravity. A standard machine has a 1,2-metre load centre, but in this case, it was extended to cater for the heavy cargo.
“If it happens that we get multiple customer requests for the same specialised equipment, the tailor-made machine will then form part of the standard Konecranes range. It becomes easier to manufacture because the research and development, as well as the tooling, has already been done. The 60-ton forklift with the 1,5-metre load centre is now offered by Konecranes as a standard unit,” Naidoo says. He adds that using tailor-made machines has the advantage of providing a competitive edge to customers by allowing for unique processes or product offerings that are not available in off-the-shelf solutions.
CFAO Equipment SA, +27 (0) 11 571 0200, info@cfaoequipment.co.za, www.cfaoequipment.co.za
Factory Acceptance Testing (FAT) of an Enerpac JS-250 fitted with a bracing kit for German heavy lift company, LASTRO Heavylift, has been completed at Enerpac Heavy Lifting Technology in The Netherlands. The JS-250 Jack-up lifted a 660 metric ton load to a height of 15m during the FAT.
The Enerpac JS-250 system, comprising four towers, can lift loads up to 1,400 tonne to 5m and 1,000 tonne to 10m. The bracing kit includes four specially designed mid barrels, four adjustable braces and eight diagonal tension bars.
The mid barrels are added to the tower and the braces and tensions bars fitted at ground level.
The jack-up bracing arrangement is then raised synchronously as more barrels are added to the tower.
The bracing system is especially useful when side loads are expected, for example, when deploying the JS-250 Jack-up system on self-propelled modular transporters (SPMTs) during bridge construction.
In addition to the JS-250 Jackup, LASTRO has invested in the
enlargement and modernisation of its already huge equipment fleet with 200 tonne and 70 tonne Enerpac strand jacks, as well as a complete Enerpac SCJ-Series 100 cube system.
“With larger and heavier loads in often space restricted areas, the compactness of the Enerpac systems will allow us to offer an effective lifting solution that is quick to implement,” said Katja Marmann, CEO, LASTRO Heavylift GmbH.
“The Jack-up and Cube Jack systems are highly capable lifting systems for many projects where it’s not possible to use traditional cranes, especially inside factory and production buildings.”
Enerpac, +27 (0) 12 940 0656, africa@enerpac.com
www.enerpac.com
The 8-axle crane can complete hoisting work in the 700-tonne class or even higher with ease. It therefore has a nominal lifting capacity of 700 tonnes.
In a lifting capacity comparison, the LTM 1650-8.1 exceeds its predecessor’s capacity by between 15 and 50 percent, depending on its equipment package.
www.liebherr.com
Three key factors required of lifting equipment in production and manufacturing facilities are reliability, safety and reduced downtime.
The days of fixing a crane component after it breaks are long gone. It is simply an unaffordable and impractical way to maintain critical and hardworking equipment. Preventive maintenance is not a new concept, but the cost and safety savings that it offers are immeasurable. Konecranes and Demag, global
leaders in the supply and maintenance of lifting equipment offer Preventive Maintenance Programmes that will keep a customer’s equipment on track, safe and with minimal downtime thereby increasing uptime. These programmes are not just for Konecranes and Demag equipment, they offer the same standard of
preventive maintenance inspections to crane and lifting equipment of any brand.
“Those with critical or process cranes, standard cranes and light lifting equipment used in production who want to benefit from safe and reliable production processes will see the benefits and advantages of our preventive and predictive maintenance options no matter the brand of equipment” commented Ian Grobler, Sales Manager for Konecranes and Demag South Africa.
“Konecranes and Demag believe that prevention is better than cure, and while regulations state sixmonthly crane inspections suffice, our three-monthly Preventative Maintenance Programmes ensure that all the lifting components are analysed for general wearing, component condition and performance. This eliminates risk of a potential component failure or breakdown that can occur within the six-month regulatory inspection period. This reduces equipment downtime not only in the short term, but also in the medium to long term, which minimises operational costs” said Grobler.
What is the preventive/predictive maintenance program The Preventive/Predictive Maintenance Program has been designed to improve equipment safety, productivity and sustainability through systematic applications of preventive maintenance inspections, compliance inspections where applicable and routine maintenance.
The benefits are numerous and include:
• Reduction of downtime and increase reliability
• Safety and production risks are documented and recommendations for corrective actions are provided
• Recommendations for improving the safety, productivity, application or useful life of the asset are provided
• Includes frequent and periodic inspections to satisfy regulatory requirements thereby keeping your lifting equipment fully compliant
• Contributes to maintenance planning and decision making with inspection and maintenance information available on yourKONECRANES.com customer portal, at any time on any device • Operating data from TRUCONNECT provides insights into crane usage
Grobler said “Our Preventive Maintenance Programme also embraces smart, data driven maintenance via our MAINMAN Planned Maintenance option which utilises visual inspections and maintenance work to help satisfy manufacturers’ maintenance recommendations. This type of maintenance is based on time and usage and helps maintain equipment performance and availability”.
Konecranes and Demag offer a suite of online, App and remote connectivity services for equipment information data in real time to their customers.
• YourKONECRANES online portal gives you quick and easy access to your crane maintenance information. Usage, maintenance data and asset details are linked, giving a transparent view of events and activities over any selected time interval. Aggregated data can be viewed, analysed and shared quickly, for a single asset or an entire fleet. It can be accessed at any time from any place.
• TRUCONNECT is a suite of remote service products and applications to support maintenance operations
and drive improvements in safety and productivity. It is an important building block in delivering Lifecycle Services in Real Time and the foundation for our Predictive Maintenance Programmes and is linked to the yourKONECRANES customer portal.
TRUCONNECT additions include brake and wire rope monitoring as well as oil analysis, critical component and design life analysis.
• Konecranes CheckApp for daily inspections has been designed to help crane users quickly and easily record their findings when performing pre-shift and/or prelift inspections. It gives you a digitalised and cost-effective way for recording and retrieving daily inspection data that can be used for internal auditing and compliance.
“Our sole objective through our Preventive Maintenance Programme is to ensure that crane and lifting equipment components are optimally maintained, no
With a lifting capacity of 13 tons, the RTH 13.26 is the telehandler that holds the world record for lifitng capacity. Magni telescopic handlers are leaders in the heavy capacity rotos sector, setting new records thanks to the constant development of performance and technology.
At the forefront of this is the RTH 13.26, the flagship of the world of telehandlers. With a maximum capacity of 13 tons and a lifting height of up to 26.20 meters, the RTH 13.26 redefines performance on site.
It’s not just its power that makes this the ultimate champion: let’s find out what makes it unique in the world.
First and foremost is its unparalleled capacity of 13 tons, which puts it in a class of its own, satisfying a wide range of heavy lifting requirements in a variety of sectors.
Its maximum lifting capacity at maximum lifting height of 8 tons is also unrivalled.
With its 26.20 meters, the RTH 13.26 is a symbol of strength and
versatility. Not only does it increase productivity on site, it also opens up new possibilities for industries that require precise movements at great heights. The telescopic boom extends and retracts extremely smoothly, providing operators with the flexibility needed to navigate complex job sites effortlessly.
What sets the Magni RTH 13.26 apart is its remarkable rotating capability. The 360-degree rotating feature allows for precise positioning of loads without the need to reposition the entire machine. This not only saves time but also increases efficiency, making it an ideal choice for tasks that demand swift and accurate material placement. Just one more reason why the RTH 13.26 is synonymous with versatility and efficiency.
All these features come together in
a single machine that guarantees maximum safety for the operator. In fact, the RTH 13.26 is equipped with advanced features such as intuitive controls, stability systems, and operator aids. This ensures that operators can maneuver the machine confidently, mitigating risks and creating a secure working environment. In the competitive world of heavy-capacity rotos, the RTH 13.26 stands out for its record-breaking performance, combining innovation, power, height, versatility and safety: a machine that not only meets the needs of an industry with everincreasing demands, but also expands the possibilities for action, demonstrating the revolutionary power of Magni TH in the field of material handling.
Magni SA, +27 (0) 11 383 2227, info@magnisa.co.za, www.magnisa.co.za
Nowadays, most components in safety-critical applications are designed redundantly: Switches monitor each other, control systems are safety-oriented and multi-channel. In rope-driven systems, however, there is no double protection for the main component - the rope.
Although ropes are subjected to a periodic visual inspection during operation, this can only detect external damage, which usually has a poor probability of being found. Heavy greasing and poor accessibility or lighting conditions downgrade the results of this inspection method even further. In addition, modern steel cables usually no longer show signs of fatigue on the outside. Instead, wire breaks occur inside the rope, invisible to the eye.
In order to enable the operator to safely operate steel wire ropes and use their main component, the rope, until it is ready to be discarded, a method was developed decades ago with which steel ropes of all types can be tested easily, quickly and efficiently across the entire rope cross-section in a nondestructive manner: Magnetic rope testing (MRT). Today, this method is the standard procedure for the non-destructive testing of steel cables and is used worldwide in many different areas of application: from cable cars to shaft hoisting systems, crane systems, leisure facilities and structures such as bridges or stadiums. Internationally, the method is recommended in
many common standards, such as ISO 4309: Cranes - Wire ropesMaintenance and repair, inspection and discard. Whereas Magnetic Rope Testing devices used to be large, heavy and complicated to operate, today’s devices are simple and easy to use. The ROPESYS rope testing device developed by the German company ROTEC GmbH is the benchmark today. The handy system consists of a permanent magnet unit with an integrated test head. The complete measurement data processing takes place in the testing device itself, so that no external cabling or electronics are required. The measurement data is analyzed in real-time and displayed wirelessly on any WLANenabled end device. Access via any browser means that the test device is independent of the operating system and does not require any local installation. After the rope inspection, the user receives a meaningful report at the touch of a button, and the data can be synchronized and backed up in a cloud storage.
The highlight of the system is the unique multi-channel sensor head, which comprehensively scans the rope 360°. In addition to basic
output channels, which indicate wire breaks, wear, and corrosion, for example, a three-dimensional image of the rope can be created, which makes it much easier to assess the condition of the rope. Geometric faults, such as unevenly distributed strands, can also be easily detected.
The system works as standard in a speed range of 0 to 5 m/s and can also be adapted to faster-running installations such as shaft hoisting systems.
In addition to the classic mobile version, ROPESYS also offers the option of permanent installation. In this case, a rope testing device is implemented in the rope drive and then checks the rope 24/7 in realtime. The rope condition of single or multiple arrangements can also be displayed to the system operator in real-time.
The system is fully certified and has already been used hundreds of times worldwide by many renowned testing organizations and rope operators.
LogiMAT 2024 will see the first showcasing of an extensive lineup of material handling products from Bobcat. The global rebranding and integration of Doosan Industrial Vehicle (DIV) under the Bobcat brand with its range of forklift trucks and warehouse equipment, will provide even more solutions to help Bobcat customers to accomplish more.
From 1st January 2024, all of the company’s material handling equipment has been produced in the signature Bobcat colours – white and orange.
The Bobcat brand is world famous for an extensive range of compact machines, which are used in construction, the agricultural sector, landscaping, demolition and many other industries. Bobcat loaders and telehandlers, which can be equipped with attachments such as pallet forks, buckets, grabs, bale clamps or dump hoppers, are often used for material handling and logistics tasks. So the addition of a complete range of IC and electric forklift trucks and warehouse equipment is a natural extension to the Bobcat range.
“Through our unwavering commitment to innovation and excellence, we have significantly broadened our product portfolio to not only meet the needs of our loyal customers but also to inspire and empower new customers to conquer their toughest challenges,” said Scott Park, CEO and Vice Chairman of Doosan Bobcat. “With an expanded range of solutions, we’re empowering even more customers to accomplish more.”
At LogiMAT 2024, the Bobcat product display will include diesel and electric forklifts, reach trucks and warehouse equipment such as pallet trucks and stackers. The display will also include Bobcat’s TL25.60 super compact telehandler, which allows
work in tight spots without compromising performance, thanks to the machine’s compact dimensions and excellent manoeuvrability.
The Bobcat material handling products on the stand at LogiMAT include:
Diesel forklifts:
• D160S-9
• D50SC-9
Electric forklifts:
• B25NS
• B20X-7 Plus
• B80NS
Reach truck:
• BR16J-9
Warehouse equipment:
• BPL18S-7 pedestrian pallet truck
• BPR20S-7 ride-on pallet truck
• BDR13S-7 double stacker
• LSM12N-7 pallet stacker
These models are representative of products from the comprehensive Bobcat range for the logistics and material handling market, which include various lines: a series of diesel forklift trucks with lifting capacities from 2 to 16 ton; a series of LPG forklift trucks with lifting capacities from 2 to 7 ton and a series of electric forklift trucks with lifting capacities from 1.2 to 10 ton. The latter segment also includes a line of electric forklifts with three wheels for light work from 1.2 to 2 ton.
As mentioned above, the warehouse solutions include pallet trucks, stackers and reach trucks.
https://www.bobcat.com/mea/en/doosan-forklifts-become-a-part-of-the-bobcat-family | www.bobcat.com
We combined the innovation and durability you expect from Bobcat equipment with decades of experience in designing reliable material handling equipment from Doosan. We’re incorporating the built-to-last and easy-to-maintain Bobcat DNA into solutions for intralogistics and distribution facilities to boost their profi ts. Bobcat forklifts are here to empower you and your business to accomplish even more.
Container yards are essential for the global transportation of goods, and the cargo handling equipment that gets utilised within them is critical to make the handling process as seamless and efficient as possible. Furthermore, as space becomes less available and more expensive, port and terminal applications must use it as effectively as possible.
Such conditions have paved the way for the reach stacker – a lifting machine that can reach out to more than one rail and stack higher to maximise space.
Featuring an extending boom, reach stackers allow operators to create deeper and higher stacks of containers instead of just vertical stacks, single deep.
Pushing the boundaries of handling technology, Konecranes, a leading ports and terminals heavy lifting equipment provider that delivers innovative solutions to help overcome handling challenges, has a reach stacker that uses space optimally by stacking containers three rows deep and five high.
Lenny Naidoo, Acting National Operations Manager at CFAO Equipment SA’s Heavy Lift division, which sells big forklifts to container handlers and the ports industry, says the Konecranes reach stacker can certainly be regarded as a revolutionary machine as it has changed the way things were previously done in container yards.
Besides lifting containers and moving them around, the Konecranes reach stacker is a multifunctional machine that can be used to empty or load a container.
“The pick-and-carry option makes the Konecranes reach stacker incredibly versatile, especially for break-bulk cargo operations. The extending boom and large lifting capacity make it an industrial workhorse. Konecranes reach stackers can also be customised for specific industry needs by providing special spreaders, incorporating steel grabs, lifting magnets, vacuum grippers and coil C-hooks, among other appropriate attachments,” says Naidoo.
The Konecranes reach stacker also has smart load-sensing hydraulics that sense the load and adapt the lifting power to the weight of the load.
The truck provides maximum power only when it is really needed, so it consumes less fuel while at the same time reducing emissions and noise. One of the challenges
facing operators of heavy lifting equipment is downtime, which can run into weeks or even months when a machine breaks down. Konecranes offers predictive maintenance which utilises condition monitoring, advanced inspections, and data analytics to predict component or equipment failure.
TRUCONNECT Remote Monitoring is a key element of predictive maintenance. It is used to collect equipment condition and usage data that, combined with inspection and maintenance information, enables a comprehensive view and analysis of equipment condition, maintenance and operation. Driver behaviour is also monitored, for example, an alert is sent if the machine is bumped.
Naidoo says the Konecranes reach stacker also incorporates Flow Drive, which cuts down emissions and decreases fuel consumption by up to 25%, while increasing the time spent on active operations. The solution delivers concrete
benefits to everyday operations, such as a precise, smooth ride, reduced noise and less cabin vibration and a significant boost in overall productivity.
A reverse camera is also available to get rid of blind spots to help drivers move large tonnages in a safe and efficient way.
Recent amendments to Safety of Life at Sea (SOLAS) regulations and the need to mitigate any potential risk has seen the maritime industry becoming increasingly stringent, with operators now required to provide carriers with a Verified Gross Mass (VGM) for each loaded container before being loaded onto a ship.
To ensure its global customers meet these requirements, Konecranes has launched its digital Static Weighing Systems solution. Reach stackers can now hydraulically measure the weight of lifted containers before they are loaded onto a ship, with 1% fullscale accuracy achieved in less than five seconds.
This data is then automatically transferred and stored in the yourKONECRANES cloud-based service. A VGM declaration is generated using the data gathered and the document can be printed in the cab of the reach stacker, or in the office.
Naidoo says one of the most significant challenges in reach stacker operations is limited visibility, which can lead to accidents and equipment damage. To address this, Konecranes reach
stackers offer innovative camera and sensor systems, and impressive OPTIMA cabin solutions that provide real-time and superior visibility for operators, reducing the risk of accidents and equipment damage.
“With operators spending up to eight hours behind the controls, ease of operation and comfort are paramount. Konecranes reach stackers have ergonomically advanced cabins that offer comfort and superior visibility.”
“The seat features compression suspension, while cabin heating, ventilation and air conditioning
ensure operator comfort. Furthermore, all controls are accessible to the right of and above the operator, greatly improving the driver’s posture,” says Naidoo.
Konecranes reach stackers are ultimately the result of years of experience, research and development to determine the best solutions for a very specific handling requirement. Today they are most certainly at the forefront of handling technology.
CFAO Equipment SA, +27 (0) 11 571 0200, info@cfaoequipment.co.za, www.cfaoequipment.co.za
Before you buy, know who is really behind your rigging hardware
While rigging manufacturers are supposed to meet certain performance ratings and government regulations for safety, some do not. It is important to know where your hardware comes from.
There are two types of supply value chains to be aware of:
Vertically integrated
• Control over supply chain and quality of raw material source
• Internal engineering
• Product innovation and new product R&D
• In touch with industry trends
• Single-source manufacturer
• Control of product scheduling and manufacturing process
• Typically has long industry legacy
• Responsibility of quality and safety of products as a single owner
• Protected distribution network
• Fewest handoffs
• Most accountability
Outsourced/non-integrated (private branding)
• Unknown quality of raw material source
• Multiple manufacturing processes and standards
• Off-the-shelf private branded products
• Lack of product life cycle commitment
• Unknown manufacturer
• Limited scheduling and manufacturing controls
• Market trend chasers, lack of product knowledge
• Lack of distribution network, direct to customer sales
• Limited control over key aspects: safety, quality, responsibility
• Lack of accountability
Vertically integrated supply chain
Vertically integrated product supply chain manufacturing provides complete control of the manufacturing process from raw material to finished goods. This control ensures product inspection throughout the manufacturing process affording a high level of quality and consistency across all product lines.
Remember, not all ‘branded’ products are manufactured by the brand owner.
Characteristics of a vertically integrated supply chain
• Controls the process from raw
materials to finish good, ensuring a high level of quality and consistency due to multiple inspections
• Responsibility of quality and safety as a single owner
• Most direct line to the manufacturer
• Fewest handoffs
• Highest level of accountability
Outsourced/non-integrated supply chain
This type of product supply chain has limited control over the manufacturing process, including inspections and raw material quality.
A single product can go through multiple manufacturers before it is ready for sale.
Characteristics of a non-vertically integrated product supply chain
• Lack of control of raw material traceability
• Multiple parties are responsible for quality and safety...who has ownership?
• Varying manufacturing standards
Know whose product you are using
When buying rigging equipment there are always concerns about cost, quality, and safety. Uppermost should be safety because every lift is critical. Not only can the wrong choice put your company in jeopardy, it can result in serious injury or death of your employees. What to ask your rigging provider
1. Question: Are material certifications complete and transparent, showing the mill and country of origin of the steel used?
Buy only from a manufacturer that indicates both raw material and finished good country of origins information and other elements as required by local and federal standards.
2. Question: Are third party material test certificates available for your rigging equipment? Are they in the name of the supplier or another third party manufacturer?
It is important that your certificates allow tracing the material back to the original producer of the raw material.
Know who is manufacturing the material used in the rigging equipment you are using.
If other third party manufacturers are listed, make sure you research and exercise due diligence before using the products.
3. Question: What percent of your supplier’s products are re-sold or partially assembled?
To prevent putting your company in jeopardy by risking life and load, you should know whether your supplier is a highly vertically integrated product supply chain manufacturer or a so-called manufacturer that private labels from an outsourced manufacturer.
What you get when you buy Crosby Crosby is considered a vertically integrated product supply chain manufacturer for the following reasons:
Customer service
• Full-time, knowledgeable district sales representatives available in your area
• Well-trained, fully equipped
customer service department
• Engineered products group for all special product needs (design, manufacturing, and applications)
• Technical support team to explain products and services
• Management team dedicated to core customer service values Research and development
• Development of manufacturing processes for improved product performance
• Enhanced material toughness and properties through raw material selection and proper metallurgical processing
• More efficient product designs, utilizing less raw material and common design
Complete product line
• Blocks for every application
• Forged wire rope clips 1/8” to 3 ½” (3mm to 90mm)
• Shackles from 1/3 to 1550 metric tons
• Standard hooks from 1/3 to 300 metric tons
• Complete assortment of forged links, rings, forged swivels and thrust bearing
• Products available in both carbon and alloy steel
• Roll forged sheaves
• Cold Tuff® sleeves and other swaging products
• Custom designed products
Engineering
• Properly selected materials
• Heat treating (Normalized, Quenched & Tempered®, Cold Tuff®)
• Superior strength, impact toughness and fatigue performance
• Extensive expertise in CAD, finite element analysis, non-destructive testing and failure analysis of products
• Active participants in industry standards development professional committees
• ISO 9001 Certified
Manufacturing
• 95% of product lines are vertically integrated
• Modern facilities and state-of-theart processes
• Extensive and unique capabilities allow us to provide the quality and ype of fitting our customers require
• Traceability of each product throughout manufacturing process via a Product Identification Code (PIC) system
Risk management
• Comprehensive product literature
• Formal product instruction and warning program
• Individually bagged and tagged products with application information
• Training videos
• Product training seminars
Value-added services beyond the sale
World-class training
• Online courses and on-site safety clinics
• Numerous comprehensive course offerings
• Third party accredited training provider
• Live courses and seminars
Digital footprint marketing
• Social media
• Comprehensive website
• Online catalog
• Access to CAD files
Industry stewardship
• American Wire Rope Association
• Specialized Carriers and Rigging Association
• North American Crane Bureau
• National Association of Tower Erectors
• Association of Equipment
Manufacturers
• Association of Crane and Rigging Professionals
• Association of Energy Service Companies
• Steel Erectors Association of America
• American Society of Mechanical Engineers
• American National Standards Institute
• Lifting Equipment Engineers Association
• National Commission for the Certification of Crane Operators (NCCCO)
Distributor support
• Largest and most capable distribution partners
• 4,500+ authorized distributors worldwide
• Broadest and deepest inventory
• Wire rope, chain, and synthetic sling fabrication
• Design and fabrication of customer lifting solutions
• Extensive testing capabilities
• Engineering support
• Local inventory and service Product certification
• Online certificate retrieval system
• 900,000+ certificates issued to date
We bring the proof to you
To demonstrate Crosby’s superior product quality and extend the reach of our world-class training program, we offer on-site safe rigging clinics with the customdesigned Rig Safe, Rig Smart Truck (North America) and Trailer (UK). Practical training includes live load demonstrations conducted by Crosby trainers offering insight on key aspects of safe, effective, and efficient rigging. Our clinics include 30-45 minute toolbox talk style presentations, live loads with load cells, and product load test demonstrations.
Crosby Group, marcom@thecrosbygroup.com. www.thecrosbygroup.com
The currently installed RL crane has been in use on the Unity Platform since the 1990s and has proven itself over time. After more than 30 years of reliable service, INEOS FPS were looking to replace the crane, and following a technical visit to Liebherr’s manufacturing site in Rostock, selected their RL 650.
Rostock (Germany), January 2024
– INEOS FPS has selected Liebherr to supply its Unity Platform with a new crane. The RL 650 will fulfil all material handling for the offshore platform, from food and provisions to spare parts supply.
The Unity Platform is located in the North Sea in 122 metres of water and is operated remotely from an on-shore control centre. Teams regularly visit the platform to carry out periods of intensive maintenance work.
Commenting on the decision to install a replacement Liebherr crane on Unity, Jason Duncan, Project Lead at INEOS FPS, says: “During our productive dialogue, we were able to convince ourselves of the advantages of the RL series. The fact that the entire crane solution is designed and manufactured inhouse speaks for the consistently high quality of Liebherr cranes and their impressive longevity. The Unity Platform is a strategic asset to the UK and reliability is important to our customers and our business.”
With the acquisition of a new RL 650, INEOS FPS are using one of the most advanced cranes in the Liebherr product range in the offshore sector. The streamlined, compact design with the capacity to lift 15 tonnes and an outreach of 30 metres meets the needs of the Unity Platform operations.
The RL series reflects all of Liebherr’s experience in the offshore industry.
Customers from all over the world have influenced the product development and their insights and expertise have driven development forward at Liebherr. Liebherr RL cranes excel in offshore conditions, offering stability, versatile loadhandling capabilities.
Their design and construction ensure reliable performance in exacting conditions, making it a valuable asset in harsh offshore environments including those in the North Sea.
A professional partnership built on mutual respect
“We are pleased that INEOS FPS’ positive experience of our product has led to the acquisition of the RL 650 as the replacement crane for Unity. The relationship between INEOS FPS and Liebherr is one based on trust and the decadeslong collaboration between the two companies demonstrates the importance of building and maintaining long-term business relationships,” adds Matti Basan, Senior Sales Manager Offshore Cranes.
Offshore cranes, such as those in the RL series, are specially designed, built and maintained to operate in challenging marine environments. The RL 650 is an ideal choice for demanding offshore tasks while meeting industry’s stringent requirements.
HP Cranes Consulting and Engineering
Tel: +27 (0) 11 740-9725/28/33
Email: donavon@hpcranes.co.za
Web: www.hpcranes.co.za
HP Cranes
Henry And Debbie Spamers @craneshp @Hp_Cranes
:
Manufacturing and Modification of Cranes
Erection, Servicing & Load Testing of Cranes
Sling Inspection
Designing of Electrical Panels
Factory Maintenance
Supply, Installation of Standard & Specialized
Radio Control Systems
Hiring of Mobile Cranes and Load Test Weights
WE COMMIT OURSELVES TO:
A Service That Meets The Requirements of Our Clients
Provide Well Managed, Trained and Motivated Personnel
Meeting any Regulatory and Statutory Requirements
Applicable to Our Business
The Development and Maintenance of a QUALITY SYSTEM
Designed to Ensure Continuous Improvement and Meeting
The Requirements of CertX SA ISO 9001 : 2015
THE FOUNDER OF H.P CRANES
HENRY SPAMERS, CEO WITH HIS SON DONAVON SPAMERS WORKS DIRECTOR
Teufelberger-Redaelli, a global leading brand bringing together two historic companies in the steel rope business, has achieved a new Guinness World Record with Flexpack, the world’s heaviest steel rope, weighing 495.9162 tons, has a nominal diameter of 160mm and a Minimum Breaking Load of 2166mT with a nominal length of over 4 kilometres.
The rope secured its fifth consecutive GWR in the engineering and technology field and was produced at the TeufelbergerRedaelli facility in Trieste. The manufacturing process spanned 7 months, involving over 50 resources in design, procurement, processing, and deployment.
The new design of this steel rope provides a perfect combination of factors tailored to meet the most challenging subsea applications, such as offshore abandonment and recovery, and pipe laying operations The new design optimizes all axial and transverse forces to which the rope is subjected.
With unique features and applications, Flexpack has become the rope of choice for major players in the offshore industry, with over 65,000 tons of high-performance wire ropes ranging from 76mm to 160mm in diameter supplied for offshore applications. TeufelbergerRedaelli has produced over 1323 kilometers of ropes. This new rope specifically will be used for abandonment and recovery missions on winches with a Safety
Working Load of 750/1000 tons in subsea operations conducted in ultra-deep waters. With this new milestone, an internationally unparalleled recognition following a series of Guinness World Record successes since 2010 by Teufelberger-Redaelli.
This achievement extends and confirms across all sectors in which the Group operates. Recently, Teufelberger-Redaelli secured significant contracts, including recent significant contracts in the cable car industry, such as the Point de La Masse in France (2021), Nebelhornbahn in Oberstdorf, Germany (2021), Tires-Malga Frommer (2022), the Kotor-Kuk route in Montenegro (2023), and Cima Grawand – Maso Corto (2023). .
Teufelberger-Redaelli systems are also applied in single-span bridges like Storebælt Bridge, Tana Bru, Dalsfjord Suspension Bridge, Tillf Bridge, and Strömsund Bridge, as well as in pedestrian/cycle bridges like the Dubai Canal walkways, Scioto River Pedestrian Bridge in Ohio, and Sky Bridge 721-Dolni
Morava, the world’s longest suspended bridge.
Teufelberger-Redaelli ropes have found application in famous projects worldwide, including the London Eye and the High Roller Ferris wheel in Las Vegas, as well as in applications for large facades and structures like the Shed Cultural Center in New York and the Diversity Garden in Canada. They are also used in large football and Olympic stadiums such as the Miami Dolphins’ Hard Rock Stadium, Motera Cricket Stadium, and stadiums in Cairo, Valencia, and Budapest.
“We are thrilled and very proud of this new record, which celebrates not only our project management capabilities and continuous improvement of our products but also our ability to provide the best technologies to our customers,” emphasized Markus Würcher, Chief Executing Officer of TeufelbergerRedaelli.
Teufelberger-Redaelli, alice.bongiovanni@redaelli.com, www.teufelberger.com
Devoted to supplying scalable heavylifting solutions for a global market, Raimondi delivers international experience and technical versatility following the Italian tradition of excellence.
Raimondi’s high-performance cranes are easy-to-install and operate, and offer a radius of 76m with lifting capacities ranging between 3 and 24 tonnes.
Customer-centric, on-demand services include overnight spare parts delivery, field support for commissioning, and onsite application engineering with remote diagnostics.
www.raimondi.co
export@raimondicranes.com
Zoomlion’s 3,600-ton crawler crane ZCC89000 sets two world records for single lifting weight and lifting speed
Zoomlion Heavy Industry Science & Technology Co., Ltd. (“Zoomlion”, 1157. HK) recently achieved a remarkable feat with its 3,600-ton ZCC89000 crawler crane. Between January 3rd and 8th, the crane broke two world records for the heaviest single lift and fastest lifting speed during the installation of three slurry bed reactors in Zhejiang Province, China.
This critical operation was part of the construction of a slurry bed residue hydrogenation plant, which is a key component of Zhejiang Petroleum & Chemical Co., Ltd.’s 300-million-ton-per-year No.3 New Material Engineering Project. With a net weight of 3,037 tons and a net height of 67.57 meters, the slurry bed reactor is the world’s largest single-weight forging and welding hydrogenation reactor. It plays a crucial role in the slurry bed residue hydrogenation plant, which, upon completion, will enable the facility to achieve green, low-carbon, and precise refining operations with high efficiency.
Zoomlion, in collaboration with the construction company, has implemented eight significant upgrades to the 3,600-ton crawler crane. These improvements, along with various innovative hoisting
technologies, have successfully addressed complex challenges such as considerable heights, heavy weights, restricted lifting areas, and long-distance load travel.
The total hoisting weight of the three reactors amounted to nearly 10,000 tons, and the ZCC89000 completed the installation in six days. The lifting moment of the main crane reached 92,800 tm with a counterweight of 3,160 tons, the model offers six travel modes, including the pioneering “T-shaped” travel path allowing it to achieve a greater pickup range in a narrow operating area. This milestone breakthrough of the petrochemical construction industry not only broke the world records for single lifting weight and lifting speed, but also advanced the construction schedule by two months, boosting significant
economic and social benefits. The mega-scale project is currently the largest of its kind in the field of refining and chemical integration under construction in China, and it’s also the world’s largest investment in a single industrial project. Upon completion, it will become a super petrochemical industrial base with an annual refining capacity of 40 million tons of oils, 11.8 million tons of aromatics, and 4.2 million tons of ethylene.
Following this significant achievement, Zoomlion’s cranes will proceed with further hoisting and installation work, ensuring the project’s timely and high-quality completion.
Zoomlion, ding@zoomlion.com, www.en.zoomlion.com
We conduct the follow Lifting Equipment Training Courses:
• On line Management, Technical & Legal Compliance
• Lifting Tackle Inspection
• Chain Block and Lever Hoist Operation, Safety & Inspection
• Advanced Slinging & Inspection
We supply the following:
• Lifting Tackle Inspection Registers
• Lifting Tackle Wall Charts
• Lifting Tackle Plant Surveys, Audit & Reports
• Lifting Tackle Code of Practice
We will assist you to implement and maintain a Total Safe Lifting Program in your Plant or Operation
Piet Otto : 082 372 4595 / mail : potto@icon.co.za
Website : www.phakamisasafety.co.za
Becker Mining South Africa has chronicled a record year in 2023 of the sales success of Kito electrical and manual hoists, with a particular focus on Kito L5 lever hoists.
“Becker Mining has distributed and supported Kito electric chain hoists, manual hand chain blocks and lever hoists in Africa since 1986,” says Rick Jacobs, Senior General Manager (SGM) for Consumables, Becker Mining South Africa. “In spite of recent challenges in the industry - including the effects of the Covid-19 pandemic, an erratic power supply, the depreciating Rand exchange rate and ongoing strike action – Becker Mining recorded its best Kito sales numbers last year.
“Growth in sales indicates an increased demand for dependable and safe lifting equipment, that is enhanced by reliable technical support services. We attribute this success – largely in the mining sector, in platinum, gold, iron ore and coal - to Kito’s robust design and high safety standards.
“The Becker team takes great pride in the esteemed Kito range, which is manufactured in Japan to stringent quality and safety specifications. These robust hoists are designed for safe and stable operation in many light and heavy-duty applications in diverse industries. Typical applications are in mining, construction, shipbuilding, food, beverage and pharmaceutical processing, manufacturing and general industry, as well as in chemical and petrochemical plants and the wind power sector.
“We have noted a particular growth in demand for Kito L5 lever hoists, which have been developed to improve efficiencies and enhance safety. In the event of excessive overload lifting, the integrated overload limiter is automatically activated and the lever slips, preventing injury and damage. “Other advantages of this low
headroom series are reduced size and weight of the hoist that allows effortless handling and easy storage yet is a much stronger unit than previous models. The L5 lever hoist is also easier to operate, even in confined working spaces.”
There are seven hoists in this series, with capacities from 0,8 T to 9 T and a standard lift of 1,5 m, Nonstandard lifts are also available from Becker Mining.
Kito hoists are manufactured from high-grade alloy steel with solid construction and increased material thickness for a high-strength frame. Nickel coated DIN approved Grade 100 (1 000 N/mm²) load chains have been introduced for improved resistance against corrosion and wear and the design of the hook latches has been improved to ensure the tight engagement of latch and hook, to ensure operator safety.
A new shape and thicker material create a strong lever handle. Cap nuts fasten the gear case and brake cover, protecting the screw from damage and enabling easy maintenance when necessary.
Kito’s original free chain adjusting mechanism improves working efficiency and safeguards against inadvertent freewheeling under load. The reliable mechanical brake system incorporates two dry, asbestos-free brake pads and four braking surfaces and for enhanced safety, two brake pawls are standard.
Becker Mining also supplies a full range of Kito accessories, designed to enhance the performance of Kito hoists. These components include universal trolleys, available in plain or hand-geared configurations, to provide smooth, precise and
easy traversing and positioning.
To ensure hoists are in pristine condition and always operate effectively, specialists recommend they are tested regularly at Becker Mining SA’s workshops, or at any certified repair centre.
The company, which is committed to the highest standards in quality and safety, offers technical advisory, repair, test and backup services throughout Africa. A specialised consulting, training and support facility ensures optimum efficiency of a wide range of equipment and total safety for workers.
Becker Mining’s critical solutions encompass high-performance, fit-for-purpose energy distribution, automation and communication, as well as transportation and roof support systems.
Included in the range are intrinsically safe (IS) and flameproof underground electrical reticulation products, as well as fluid transfer, rigging, rope attachment, steel arch tunnel support and chairlift solutions. An important feature of all Becker Mining systems is they are designed to facilitate future upgrades.
Becker Mining South Africa, +27 (0) 11 617 6300, info@za.becker-mining.com, www.za-becker-mining.com
as
This partnership marks a significant milestone for us, as we bring to our customers this cutting-edge technology and innovation from Hoeflon, a renowned designer, manufacturer, and supplier of compact cranes, Based in Barneveld, the Netherlands.
Hoeflon Compact Cranes, also known as mini cranes, spider cranes, or compact crawlers, are revolutionising the way heavy lifting is done in confined or hard-to-access spaces.
These compact cranes are ideal for tasks such as placing glass with precision or accurately positioning steel beams and pipes. What sets Hoeflon Cranes apart is their exceptional lifting capacity, being the only compact crane capable of lifting more than its own weight. The possibilities with Hoeflon Compact Cranes are truly endless!
Trusted by professionals worldwide, the Hoeflon series perfectly complements our existing range of used and refurbished mobile cranes. This collaboration allows us to offer our customers in South Africa/Africa access to top-of-the-line compact crane solutions that cater to a diverse range of industry and lifting requirements.
At Fastlift Cranes, we take pride in being a leading supplier of quality used cranes in South Africa/Africa. This new partnership with Hoeflon further solidifies our commitment to providing our customers with the best-in-class lifting equipment and solutions.
We are excited about the opportunities that this partnership brings and look forward to serving our customers with the exceptional performance and reliability of Hoeflon Compact Cranes. Join us as we continue to elevate the standards in the crane industry in South Africa/Africa and beyond.
For more information about our range of Hoeflon Compact Cranes and how they can benefit your operations, contact us at Fastlift Cranes. Experience the power and versatility of compact lifting with Hoeflon!
Assuring you of our best service and attention at all times.
Genie and its products receive honors for sustainability, innovation, and cost of ownership
Genie was recognized by industry associations, government groups, and the media with more than a dozen awards in 2023. This included an award for the company’s sustainability initiatives, as well as Leadership in Energy and Environmental Design (LEED) Gold certification for its manufacturing facility in Monterrey, Mexico.
Genie was selected by an independent panel of judges for the 2023 International Awards for Powered Access (IAPA) Sustainability Award for implementing innovative solutions, projects, or programs that demonstrate how the company is adapting its business and/or products to environmental issues. One of those achievements was the prestigious LEED Gold certification from the U.S. Green Building Council, which was awarded to the Terex Genie Mexico facility.
“Across our industry, jobsites and our customers are increasingly looking to manufacturers to help them reduce their environmental impact and reach their sustainability targets,” said Will Westley, Genie VP Sales & Support, who was on hand to accept the IAPA Sustainability Award. “Genie’s product portfolio is already 70% electrified, which helps lower
jobsite emissions and reduce noise pollution. But our commitment to sustainability — and to helping our customers achieve their goals — goes deeper. It also is reflected in initiatives like our carbon reduction projects, recycling and energy efficiency activities, and an increasing use of clean energy technology across our global manufacturing and office footprint.”
To that point, of the seven products named to various “best of” lists, several are electric- or hybridpowered.
Genie® Lithium-Ion GS™ scissor lifts received the Editor’s Choice Award from Rental magazine. Tested for reliability and use in extreme environments, Genie Lithium-Ion batteries have been specifically designed for MEWPs and are certified by the independent certification organization Underwriters Laboratory (UL) against fire, electric shock and
explosion.
The hybrid S®-60 FE and electric S-60 DC boom lifts were chosen by an independent panel of rental industry professionals for the LLEAP Awards presented by Lift & Access magazine. According to the judges, the boom lifts received Gold for their “amazing technology that provides safety, agility, and selfcontaining power source.”
In addition, the electric S-60 DC was named “Intelligent Product” during the CMIIC (China Machinery Industry Internet Conference), which aims to recognize enterprises and products that have made outstanding contributions to the industry. The S-60 DC’s versatile performance and lower ownership costs helped it edge out the competition after three stages of online voting.
Likewise, the Z®-45J DC articulating boom lift received two awards
during the T50 Global Aerial Work Equipment Industry Summit, an annual event focused on MEWP products and technological innovations in the industry. The Z-45J DC was named Best Electric Articulating Boom Lift and received Lowest Cost of Ownership Award.
Other T50 Summit awards went to:
• SX™-135 XC™ for Best Telescopic Boom Lift;
• Harry Zhu, VP/GM Commercial, Greater China, for Outstanding Contribution to the Industry; and
• Genie was named on the Top 5 List for Global Telehandler manufacturer and Top 10 List for Global MEWP manufacturer.
Finally, the GTH™-1256 12,000 lb / 5,443 kg capacity telehandler and 13 ft / 4 m platform for boom lifts, both introduced to the market in 2023, received awards. The GTH-1256, available in the North American market, was designed to improve durability, lower total cost of ownership and provide maximum productivity on the jobsite. It was recognized by both Equipment Today and Construction Equipment magazines.
The Genie 13 ft / 4 m platform for Genie XC boom lifts in North America and the EMEA region (Europe, Middle East and Africa) received Innovative Iron award from Compact Equipment magazine. The platform adds more than 60% additional room in the platform,
increasing the versatility of rental companies’ boom lift fleets while boosting jobsite efficiency.
Goscor Access Solutions, +27 (0 11 393 6437, accesssolutions@goscor.co.za, www.goscoraccesssolutions.co.za
In the ever-changing landscape of the construction equipment industry, staying ahead of the curve is crucial for success. And JLG Industries recognizes the significance of adapting to emerging trends, including those that lie ahead for us in 2024.
There are four major trends shaping the construction sector for 2024. They include labor challenges/ shortages, the rise of megaprojects, electrification of large construction equipment, and data-driven decision-making. Let’s delve a little deeper into each emerging trend.
The construction industry has long grappled with a shortage of skilled labor, and the situation is becoming increasingly dire. According to a report by the Associated General Contractors of America (AGC), as of 2022, 88% of construction firms in the U.S. reported difficulties in filling key positions. (AGC Workforce Survey)
To add insult to injury, it’s no secret that Baby Boomers make up a large percentage of today’s workforce, and those workers are edging closer and closer to retirement age – amplifying the shortage trend. Nearly 41% of the construction industry’s workforce is expected to retire by 2031. (ADP) This increasing skilled labor shortage begs the
question, how do we increase our skilled labor force?
Training, apprenticeships, and certifications will help construction companies build the workforce they need. Inexperienced team members can be transformed into experts, and business owners can reward loyal employees by furthering their professional development. For example, the recently refreshed JLG University learning platform focuses on proactive training, offering customized learning paths, with ANSI-required safety training courses for machine operators, service technicians and supervisors. JLG is currently working to implement the program through trade associations and training centers, making it more accessible for professionals who use access equipment as part of their daily tasks, so they are ready on day one.
Megaprojects, characterized by their immense scale and complexity, are on the rise globally. Three notable sectors driving this
trend are electric vehicles or battery plants, data centers and chip or semiconductor plants. With the increasing demand for renewable energy and data storage, these megaprojects require specialized construction equipment to meet their unique challenges. Battery plants, essential for the growth of electric vehicles and renewable energy storage, demand precision and efficiency. A wave of planned vehicle battery plants will increase North America’s battery manufacturing capacity from 55 Gigawatt-hours per year in 2021 to nearly 1,000 GWh/year by 2030. This increase will support the creation of roughly 10-13 million all-electric vehicles per year, according to the U.S. Department of Energy.
The access equipment used in these battery plant projects must be versatile and capable of handling heavy loads, while ensuring safety and accuracy, as many plants will be built within auto manufacturing facilities. Data centers, on the other
hand, require access equipment that can navigate confined spaces and operate quietly to minimize disruptions.
Data centers are beginning to dot landscapes across the nation. Each has hundreds of servers and routers that send and receive data for everyday tasks like streaming content or handling high-speed financial trades. The change in work habits during the pandemic also fueled the need for more data centers. The U.S. had 2,701 data centers in 2022, the largest in the world, followed by Germany, according to data compiled by Statista.
While there haven’t been as many chip or semiconductor plants built as data centers, there is an uptick in an effort to strengthen semiconductor manufacturing capabilities in the country, driven
equipment industry is embracing the electrification of large equipment. Electric construction machinery, including access equipment, offers several advantages, including reduced noise and emissions, lower operating costs, and improved efficiency. According to a study by McKinsey & Co., the electrification of construction equipment is expected to grow at an annual rate of 8% to 12%, reaching a significant market share by 2030.
Electric equipment, which is quieter and odor-free, is also becoming increasingly popular in indoor construction and revitalization projects, such as in the renovation of airports or hospitals, as destructing and constructing indoors requires maintaining quiet and clean conditions. Equipment such as electric scissors, low-level access and compact crawler booms
increasing importance of datadriven decision making.
JLG is going beyond telematics, integrating advanced IoT systems that allow users to monitor equipment in real time, with its ClearSky Smart Fleet™ twoway fleet management and communication platform. Soon to be standard on most JLG equipment, a single connectivity beacon combines analyzers, telematics, productivity applications—as many as 25 distinct features—to deliver seamless back-and-forth interaction and information such as maintenance needs and repair data.
ClearSky also helps:
• Track individual machines on a crowded job site
• Understand fuel utilization
• Pinpoint maintenance and battery needs, measuring how many hours
Umholi
T: +27 (0) 11 914 2210/11
F: +27 (0) 11 914 2209
E: umholi@umholi.co.za
W: www.umholi.co.za
Kempston Controls
T: +27 (0) 140 776 2888
E: holyhead@kempstoncontrols.co.uk
W: www.kempstoncontrols.co.uk
CHAIN BLOCKS
Condra Cranes
T: +27 (0) 11 776 6000
E: sales@condra.co.za
W: www.condra.co.za
Cooper & Cooper Group
T: +27 (0) 11 493 4355
E: info@coopergroup.co.za
W: www.coopergroup.co.za
Palfinger Africa
T: +27 (0) 11 608 3670/1/2/3/4
E: sales@palfingerafrica.co.za
W: www.palfinger.co.za
CRANE HIRE
Johnson Crane Hire
T: +27 (0) 11 455 9222
E: PeterY@jch.co.za
W: www.jch.co.za
Liebherr Africa
T: +27 (0) 11 365 2000
E: info.laf@liebherr.com
W: www.liebherr.com
True Lift services
T: +27 (0) 83 710 5390
E: Trueliftservices@gmail.com
W: www.trueliftservices.za.live
Bell Equipment Southern Africa
T: +27 (0) 11 928 9846
E: susanmy@bell.co.za
W: www.bellequipment.com
Forklift Network
T: +27 (0) 10 023 1912
E: nicky@forkliftnetwork.co.za
W: www.forkliftnetwork.co.za
Jungheinrich
T: +27 (0) 10 596 8460
E: info@jungheinrich.co.za
W: www.jungheinrich.co.za
Kempston Controls
T: +27 (0) 140 776 2888
E: holyhead@kempstoncontrols.co.uk
W: www.kempstoncontrols.co.uk
Morris Material Handling SA
T: +27 (0) 11 748 1000
F: +27 (0) 11 748 1093
E: sales@morris.co.za
W: www.morris.co.za
Rhino Lifting Maintenance
T: +27 (0) 16 971 2348/49
E: sales@rhinolm.co.za
W: www.rhinolm.co.za
Yale Lifting Solutions
T: +27 (0) 11 794 2910
F: +27 (0) 11 794 3560
E: crm@yalelift.co.za
W: www.yale.co.za
Yale Lifting Solutions
T: +27 (0) 11 794 2910
F: +27 (0) 11 794 3560
E: crm@yalelift.co.za
W: www.cmco.com
DEMAC SRL
T: +39 (0)2 9784488
F: +39 (0)2 97003509
E: info@demac.it
W: www.demac.it
Econo Flex
T: +27 (0) 16 933 5705
E: econoflex@econoflex.co.za
W: www.econoflex.co.za
Econo Flex
T: +27 (0) 16 933 5705
E: econoflex@econoflex.co.za
W: www.econoflex.co.za
GregBev Enterprise
C: +27 (0) 82 854 5143
C: +27 (0) 72 395 4342
T: +27 (0) 53 285 0842
E: admin@gregbev.co.za
W: www.gregbev.co.za
GregBev Enterprise
C: +27 (0) 82 854 5143
C: +27 (0) 72 395 4342
T: +27 (0) 53 285 0842
E: admin@gregbev.co.za
W: www.gregbev.co.za
Yale Lifting Solutions
T: +27 (0) 11 794 2910
F: +27 (0) 11 794 3560
E: crm@yalelift.co.za
W: www.cmco.com
IY Safety & Inspections
T: +27 (0) 82 773 7019
C: +27 (0) 82 956 3176
E: bianca@iysafetyinspection.co.za
W: www.iysafetyinspection.com
Morris Material Handling SA
T: +27 (0) 11 748 1000
F: +27 (0) 11 748 1093
E: sales@morris.co.za
W: www.morris.co.za
3 60 5 Services
T: +27 (0) 72 207 7443
T: +27 (0) 64 687 7270
E: sales@3605services.co.za
W: www.3605services.co.za
Econo Flex
T: +27 (0) 16 933 5705
E: econoflex@econoflex.co.za
W: www.econoflex.co.za
GregBev Enterprise
C: +27 (0) 82 854 5143
C: +27 (0) 72 395 4342
T: +27 (0) 53 285 0842
E: admin@gregbev.co.za
W: www.gregbev.co.za
Integrate Lifting Specialist Africa
T: +27 (0) 12 141 3615
T: +27 (0) 86 571 4387
E: info@integrateliftingsa.com
W: www.integrateliftingsa.com
IY Safety & Inspections
T: +27 (0) 82 773 7019
C: +27 (0) 82 956 3176
E: bianca@iysafetyinspection.co.za
W: www.iysafetyinspection.com
Margisia Lifting Solutions
T: +27 (0) 14 763 1849
C: +27 (0) 83 992 2222
E: info@margisia.co.za
W: www.margisia.co.za
Rhino Lifting Maintenance
T: +27 (0) 16 971 2348/49
E: sales@rhinolm.co.za
W: www.rhinolm.co.za
J Express Crane Services
T: +27 (0) 11 864 8402
M: +27 (0) 83 425 5535
F: +27 (0) 11 864 8408
E: jexpress@telkomsa.net
Kempston Controls
T: +27 (0) 140 776 2888
E: holyhead@kempstoncontrols.co.uk
W: www.kempstoncontrols.co.uk
Levi’s Trio Engineering
T: +27 (0) 11 907 9258
F: +27 (0) 86 742 9410
E: admin@levistrio.co.za
W: www.levistrio.co.za
Morris Material Handling SA
T: +27 (0) 11 748 1000
F: +27 (0) 11 748 1093
E: sales@morris.co.za
W: www.morris.co.za
Liebherr Africa
Shosholoza Consulting
T: +27 (0) 14 495 1994
C: +27 (0) 79 391 2990
E: info@shosholoza.africa
W: www.shosholoza.africa
Yale Lifting Solutions
T: +27 (0) 11 794 2910
F: +27 (0) 11 794 3560
E: crm@yalelift.co.za
W: www.cmco.com
Cooper & Cooper Group
T: +27 (0) 11 493 4355
E: info@coopergroup.co.za
W: www.coopergroup.co.za
Condra Cranes
T: +27 (0) 11 776 6000
E: sales@condra.co.za
Econo Flex
T: +27 (0) 16 933 5705
E: econoflex@econoflex.co.za
W: www.econoflex.co.za
HP Cranes Consulting
T: +27 (0) 11 740-9725/28/33
F: +27 (0) 11 740 8416
E: admin1@hpcranes.co.za
W: www.hpcranes.co.za
IY Safety & Inspections
T: +27 (0) 82 773 7019
C: +27 (0) 82 956 3176
E: bianca@iysafetyinspection.co.za
W: www.iysafetyinspection.com
J Express Crane Services
T: +27 (0) 11 864 8402
M: +27 (0) 83 425 5535
F: +27 (0) 11 864 8408
E: jexpress@telkomsa.net
V & S Automation/Cranes
T: +27 (0) 10 442 7478
C: +27 (0) 82 787 2343
T: +27 (0) 11 365 2000
E: info.laf@liebherr.com
W: www.liebherr.com
NON DESTRUCTIVE TESTING
Chimaera
T: +27 (0) 84 506 1209
E: ndt@chimaera.co.za
W: www.chimaera.co.za
OVERHEAD CRANE
By Carpel SRL - Italy
T: + 39 (0) 39 532 0952
F: + 39 (0) 39 532 0825
E: info@bycarpel.it
W: www.bycarpel.it
Kempston Controls
T: +27 (0) 140 776 2888
E: holyhead@kempstoncontrols.co.uk
W: www.kempstoncontrols.co.uk
KL Cranes and Lifting Equipment
T: +267 397 4853
C: +267 71344438
E: annelieze@klcranesbot.com
W: www.klcranesbot.com
Morris Material Handling SA
T: +27 (0) 11 748 1000
F: +27 (0) 11 748 1093
E: sales@morris.co.za
W: www.morris.co.za
E: victor@vsautomation.co.za
W: www.vandsautomation-cranes. co.za
ACROW
T: +27 (0) 11 824 1527
E: info@acrow.co.za
W: www.acrow.co.za
Lifting Placements
C: +27 (0) 61 063 1687
E: info@liftingplacements.co.za
W: www.liftingplacements.co.za
REFURBISHMENT
Kempston Controls
T: +27 (0) 140 776 2888
E: holyhead@kempstoncontrols.co.uk
W: www.kempstoncontrols.co.uk
REMOTE CONTROLS
Giovenzana International
T: +39 (0)39 5951 1277
E: giovenzana@giovenzana.com
W: www.giovenzana.com
T: +27 (0) 11 864 8402
C: +27 (0) 83 425 5535
F: +27 (0) 11 864 8408
W: www.condra.co.za SERVICES
J Express Crane Services
E: jexpress@telkomsa.net
J Express Crane Services
T: +27 (0) 11 864 8402
C: +27 (0) 83 425 5535
F: +27 (0) 11 864 8408
E: jexpress@telkomsa.net
Haggie
T: +27 (0) 11 601 8400
E: distribution@haggie.co.za
W: www.scaw.co.za
CB Lifting
T: +27 (0) 22 719 1437
E: info@cblifting.co.za
W: www.cblifting.co.za
Haggie
T: +27 (0) 11 601 8400
E: distribution@haggie.co.za
W: www.scaw.co.za
Umholi
T: +27 (0) 11 914 2210/11
F: +27 (0) 11 914 2209
E: umholi@umholi.co.za
W: www.umholi.co.za
Combi Lift
T: +27 (0) 11 900 8010
E: victor@solutions-4u.co.za
W: www.combilift.co.za
Kemach Forklifts
T: +27 (0) 11 826 6710
E: info@kemachjcb.co.za
W: www.kemachjcb.co.za
Manitou
T: +27 (0) 10 601 3000
E: info.msa@manitou-group.com
W: www.manitou.com
Liebherr Africa
T: +27 (0) 11 365 2000
E: info.laf@liebherr.com
W: www.liebherr.com
MH Dawood Plant Services
T: +27 (0) 11 496 1007
F: +27 (0) 11 496 1198
E: info@mhdawood.co.za
W: www.mhdawood.co.za
LMI Academy
T: +27 (0) 11 475 5876
E: info@lmi-academy.co.za
W: www.lmi-academy.co.za
T: +27 (0) 82 506 5899
T: +27 (0) 73 089 0624
E: sinky@mclstraining.co.za
W: www.mclstraining.co.za
Phakamisa Safety Consultants
T: +27 (0) 11 462 9620/1
F: +27 (0) 11 462 9620
E: potto@icon.co.za
W: www.phakamisasafety.co.za
Crane Clinic
T: +27 (0) 11 902 7379
E: reception@craneclinic.co.za
W: www.craneclinic.co.za
Palfinger Africa
T: +27 (0) 11 608 3670/1/2/3/4
E: sales@palfingerafrica.co.za
W: www.palfinger.co.za
Smith Capital Equipment
T: +27 (0) 11 873 9830
E: mail@smithcapital.co.za
W: www.smithcapital.co.za
Dymot Engineering
T: +27 (0) 11 970 1920
F: +27 (0) 11 970 1979
E: pa@dymot.co.za
W: www.dymot.co.za