
5 minute read
At AJM Engineering size is irrelevant
COVER STORY At AJM Engineering size is irrelevant
This South African SME is proof that SME’s can – and do – pack a big punch. Lifting Africa spoke to general manager Marco Marques to find out more.
With a raging pandemic, disrupted supply chains and overall tough economic times the manufacturing sector has faced its fair share of serious challenges over the past year. Innovation, agility and flexibility have become the order of the day as manufacturers manoeuvre their way through the new normal that is 2021. It has not been easy on most companies, but maybe more so for small to medium-sized enterprises (SMEs) that simply don’t have the cash reserves and capacity of large businesses and multinationals. At AJM Engineering the focus, however, has not been on what the business can’t do, but rather what it can achieve and the message is very clear – don’t underestimate SME’s. They pack a powerful punch. “Covid-19 and the contracting economy has undoubtedly put pressure on our operations like on many other companies, but we have also realized that as a small to medium enterprise, we are very agile and flexible and able to meet our clients’ needs quickly and efficiently.” Using the company size to its advantage AJM Engineering, says Marques, is small enough to still care, but big enough to deliver to its clients no matter what the request. The company has become renowned for its quality products in the lifting industry and works not only in South Africa but around the world.
Support local
Buying locally manufactured products holds several benefits. Not only that but companies such as AJM Engineering hold the know-how and capability to compete internationally. “We have a vast amount of knowledge and experience in our business that allows us to not only serve the local market but also internationally.” The company has delivered solutions around the world including to Russia, Saudi Arabia, Australia and throughout Africa. “We took an approach to manufacture more locally several years ago. As a business, we have an intimate knowledge of our client’s needs and hold very close relationships with them. Delivering solutions that meet those needs was clearly what the market required and our ability to deliver those solutions was enhanced by building a local manufacturing footprint.” For the past seven years, for example, the company has been designing and manufacturing steel wire rope hoists locally. These days it manufactures not only hoists and cranes, but a range of other equipment also for the rail maintenance industry such as lifting jacks and specialized platforms. “Local manufacturing is not only better for the economy of the country and creates more employment, but it also made sense for our company as we were able to introduce efficiencies to our operations and improve our service to our clients,” says Marques. Allowing for far more bespoke solutions, lead times have also reduced significantly. “We just don’t have the long lead times that one will typically see on an imported product that spends an average of six weeks at sea over and above the time to manufacturer the product.” According to Marques, lead times at AJM Engineering average two to four weeks depending on the availability of raw material. Another major boon, he says, has been the ability to meet customer needs. “We are not stuck on specifics, but rather can manipulate any given unit and deliver a bespoke solution that is specific to
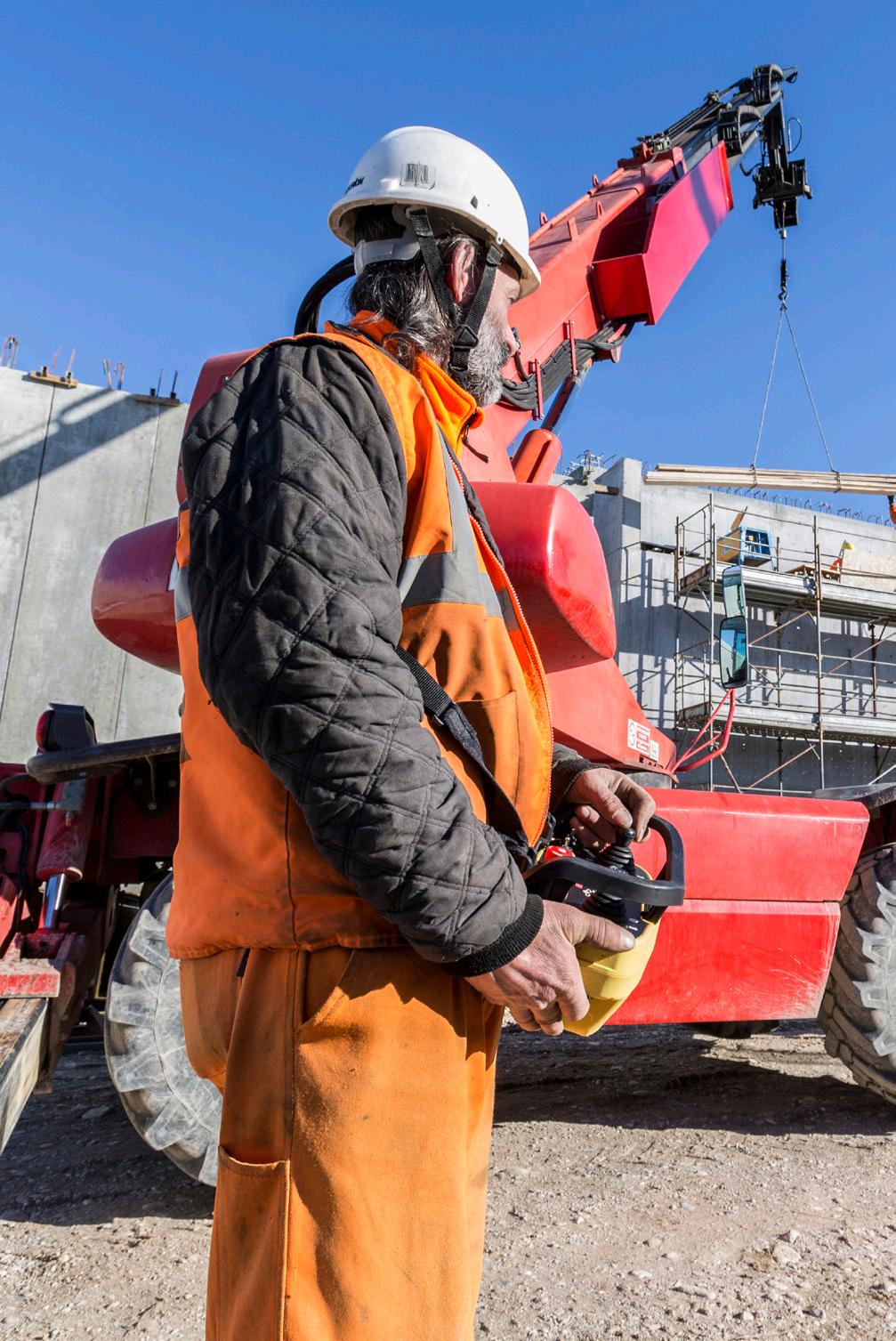
a customer’s requirements. We do ’standard’ designs, but we can also easily manipulate that to customer specifications.” Whilst the overall trend in the country more often than not is still to import, the outbreak of a global pandemic has highlighted the importance of local manufacturing. Whilst It has always been easier and cheaper to just import but the sudden disruption to supply chain and ocean freight has cast a new light on the importance of local manufacturing capability. “We are one of only two companies that we know of that manufacture steel wire rope hoists locally,” says Marques. “We believe it is far more advantageous to buy local. The experts are on hand to deal with any crisis or problem and the availability of product is far higher. From a maintenance and breakdown point of view, local manufacturing is far more sustainable and competitive.”
Diversification
Remaining robust and able to meet market needs has seen AJM Engineering diversify its range of capabilities in recent years. One of these developments was the establishment of a sister company, AJM Radio & Controls (R&C) with Fanie du Toit as one of the directors and general manager. Considered a market leader in supplying industrial radio remote control and automation solutions, this company has seen significant growth since its establishment. It’s a complex business and not as easy as just fitting a radio remote control onto a machine. “More often than not one has to reverse engineer the machine before one can fit the radio remote control. This then often requires the redrawing hydraulic circuits and electrical circuits. Having the knowledge on the capability of a vast array of machines is essential,” explains Du Toit. Radio remote controlled machines are a growing trend as it delivers safer operations. Due to this, there is tremendous scope and AJM Radio and Controls are encountering more and more requirements for machines to be fitted with these devices. “Automation is probably the fastest growing trend as there is a real push from all industries for safer and more reliable operations.” Removing people out of harm’s way means removing them out of the machines. “We are incredibly proud of the knowledge base and experience we have built up within R&C over the past decade.”

AJM Engineering,
+27 (0) 11 453 0728, info@ajmengineering.co.za, www.ajmengineering.co.za

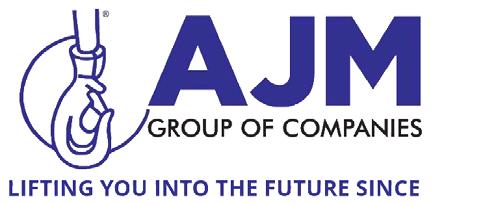