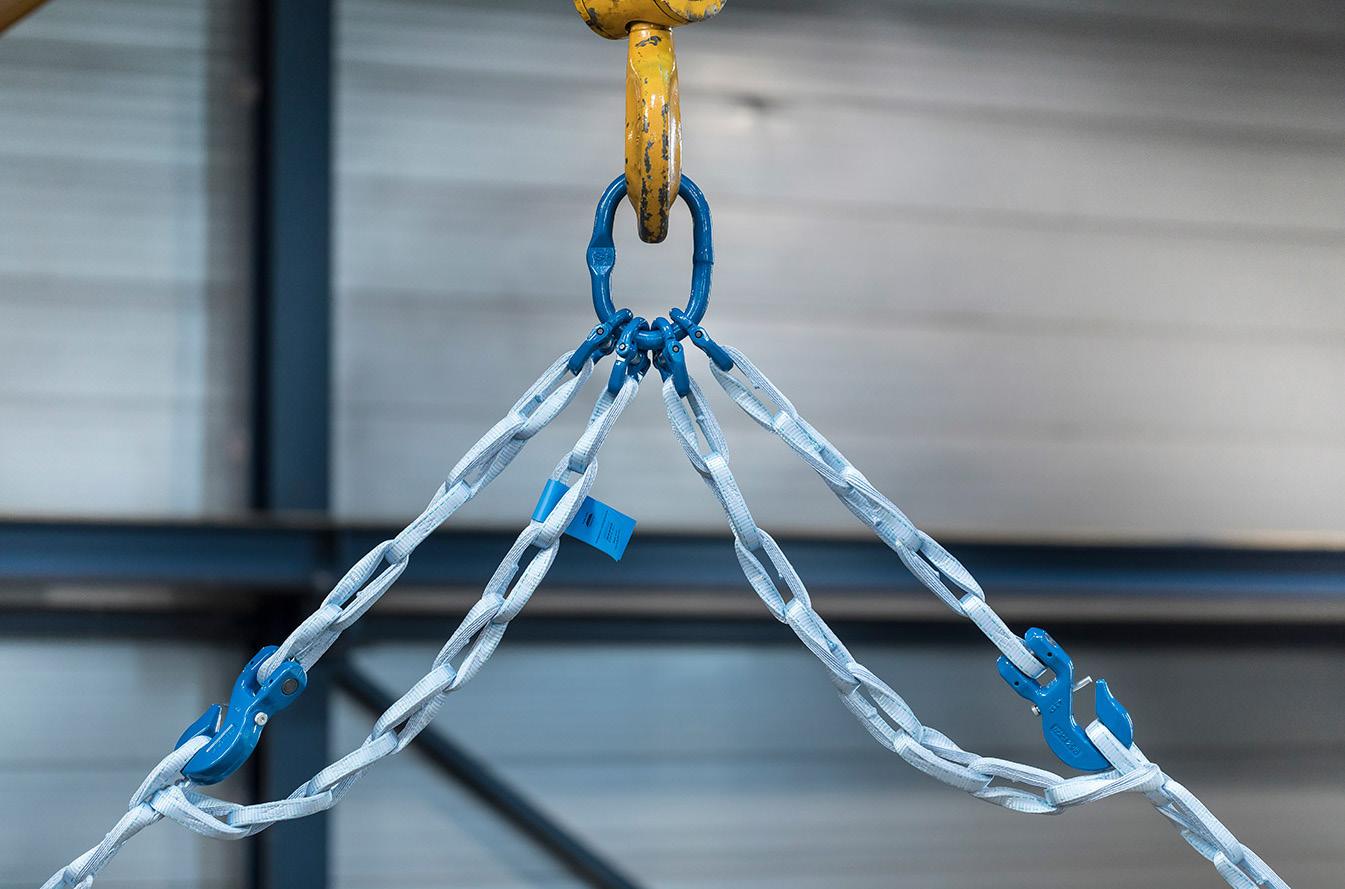
4 minute read
Chaining for the future – synthetics leads the way
Bigger, heavier, higher – this is increasingly the reality lifting and lashing experts need to deal with while increasing productivity and not compromising safety. Synthetic link chains have marked a massive leap forward for lifting and lashing technology. Lifting Africa finds out more.
Ask Roan Retera, Van Beest general sales and marketing manager, why to opt for synthetic link chains and the answer are quick. “They are soft, quiet, easy to handle, and safe.” The company manufactures Green Pin Tycan – a synthetic link chain created from the world's strongest man-made fibre, Dyneema. “It really is the next step in the evolution of chain,” he said during a recent online event where he highlighted why more and more operators were considering a move away from traditional chains. According to Retera, the synthetic product has all the performance and flexibility of a steel chain but at a fraction of the weight. Noncorrosive, non-conductive and completely waterproof, it even floats.
Features of synthetic chain
“Synthetic chain allows companies to achieve a safer working environment for their crew. The soft touch and light weight reduce the risk of bad backs, cuts, bruises or hearing damage," said Retera. “They are also not as noisy to work with and therefore any potential hearing damaged is also reduced.” Easy to use and up to eight times lighter than a steel chain of comparable strength the product is light enough for one person to work with all day long allowing one to use staff more efficiently across operations. Retera said that companies who had made the switch to synthetic chain were reporting reduced sick leave, fewer delays and lower transport costs. “Ten meters of steel chain with a load limit of five tons when weighed comes in at 38kgs. The same ten meters of synthetic chain with the same load limit only weighs 6kg. The impact on the workers carrying chains on site all day is tremendous.” Describing it as the next generation lifting equipment Retera said products made from Dyneema were also waterproof and did not absorb water and resistant to UV, oil, dirt, diesel, grease and non-oxidizing chemicals. “It can easily be cleaned with a high-pressure hose. These synthetic chains offer all-round easy use. It does not rust or corrode; it is rugged and makes for much easier working conditions.”

Case studies
Seaway Heavy Lifting opted to use the synthetic chain as lashing for the transportation of 85 piles each weighing in at around 150 tons and 16 meters long. According to product manager Erik-Jan van Lit, the weight of the chain used for the job came in at only 10kg making it a much easier operation all round. “This resulted in much higher productivity as it was so much easier to work with. They also did not require a crane on sight to lift the chain as would have been the case if they used traditional steel chain,” he said during the same online event. “The synthetic chain turned out be to faster and could be thrown by hand over the piles instead of having to be lifted by a crane. There was also no need for ladders to be climbed to guide the chain over the piles. It was therefore a much safer operation as well.” Van Lit said Seaway also found no damage to the piles on completion of the job. “Steel chain on a metal pile could have resulted in some scratching of the cargo,” he explained. Another company that has opted to use a synthetic chain instead of steel was a bulk terminal operator in Amsterdam. “The cargo is removed from the ship with a grabber but they have to use telehandlers to empty at the bottom of the vessel. These telehandlers are lifted into the hull of the ship and predominantly steel chain was used. One can imagine the noise of dropping and dragging chain on a steel bottom vessel,” said Van Lit. “The telehandlers are now lowered into the vessel hull using synthetic chain and again the damages have been reported to be significantly reduced not to mention that noise pollution is far less.”
Benefits
According to Retera, these are but two examples of many. “The two biggest benefits to users of synthetic chain are efficiency and safety. Due to the lightweight and softness of the product injuries are reduced, while the efficiency gains are a direct result of the higher productivity that is achieved.” Several end users had reported that due to the lightness of the chains jobs previously reserved for two riggers was now easily be accomplished by only one. “These chains are proving to be very cost effective as well.” Retera said four sizes of the chain was currently available in their range with steel fittings developed and designed along with the synthetic product. “There are special connecting links that have to be used with the synthetic chain,” he concluded.
www.greenpin.com/academy Van Beest,
sales@vanbeest.eu, www.vanbeest.com
