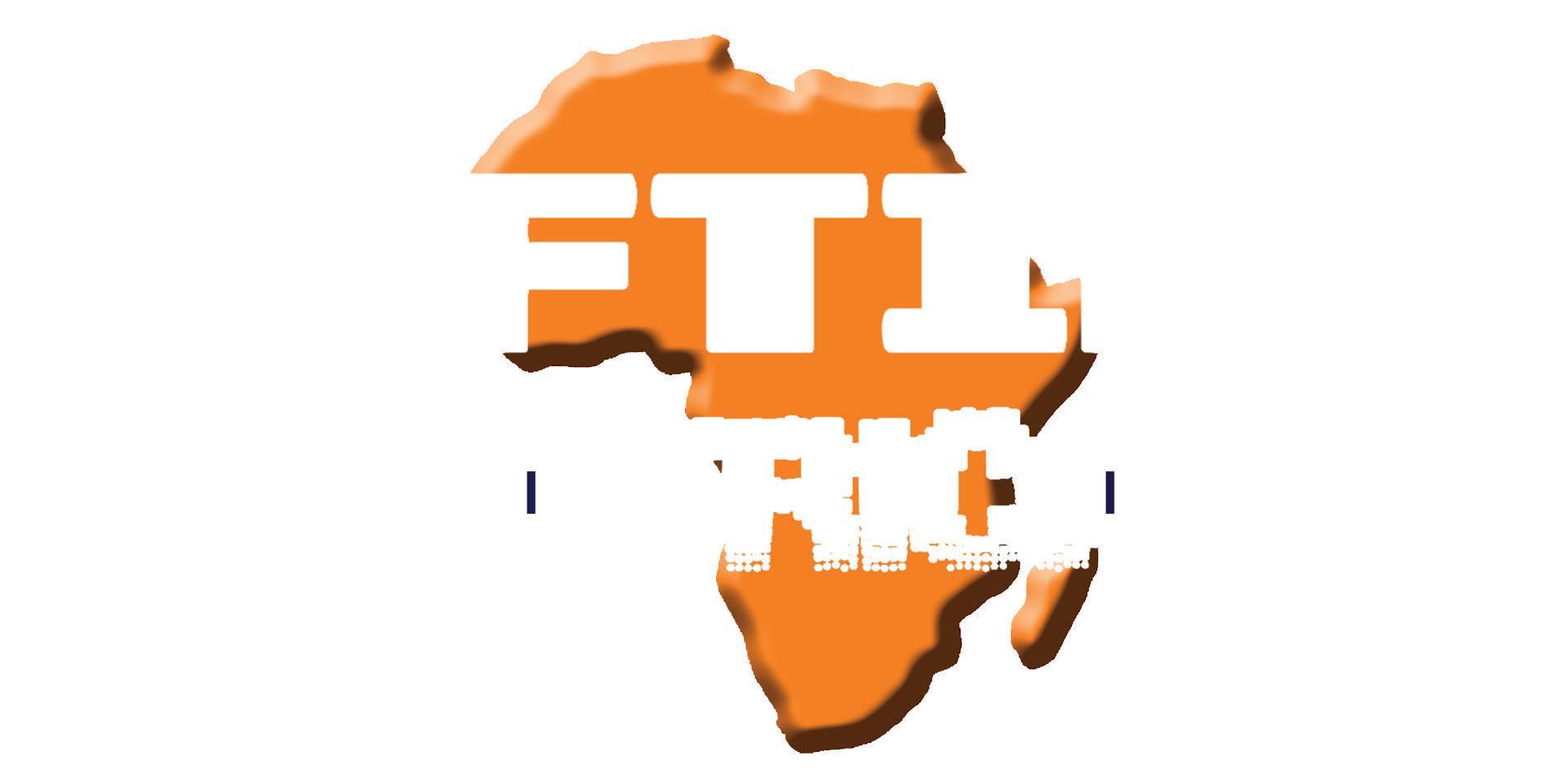
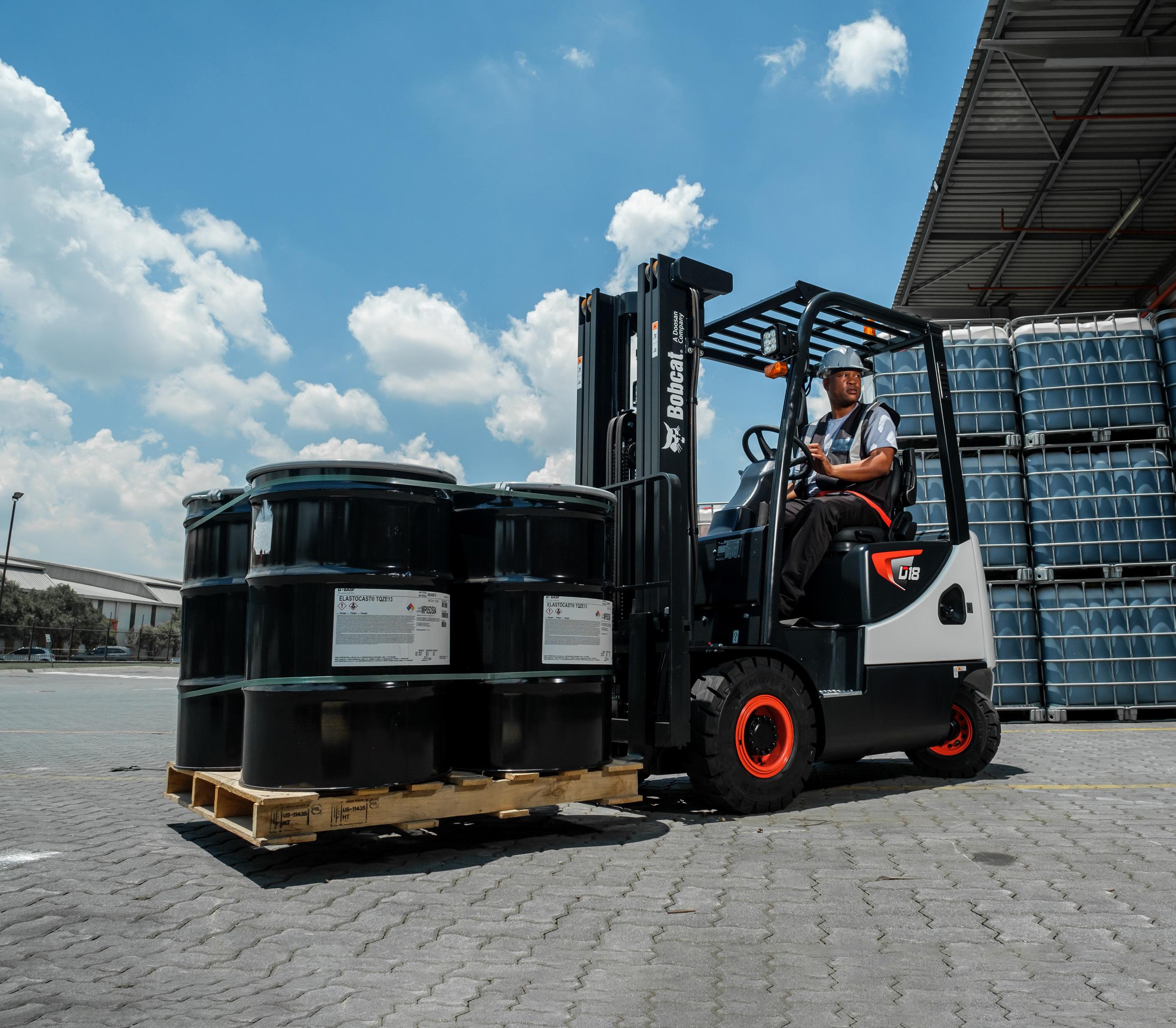
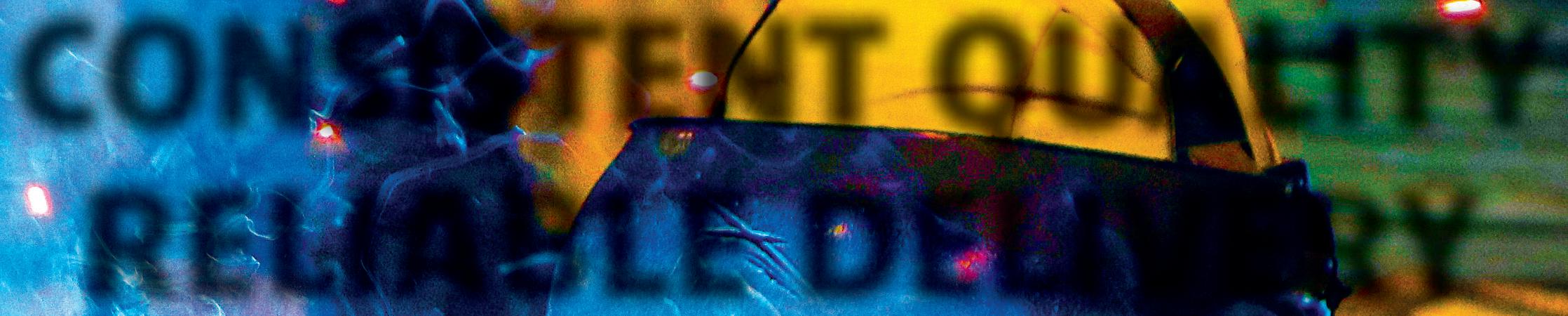


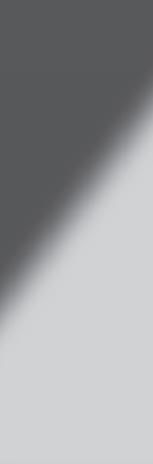



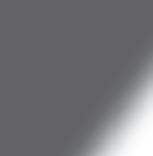
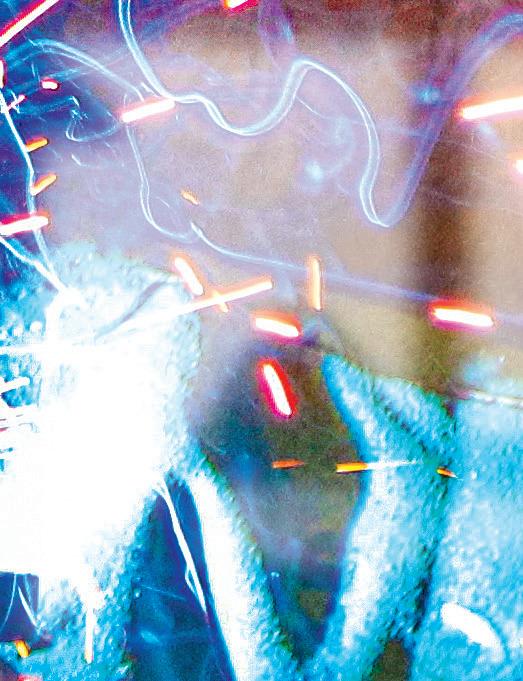
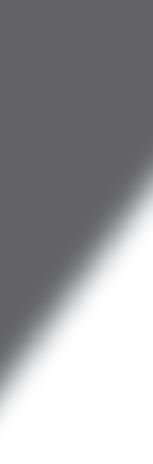
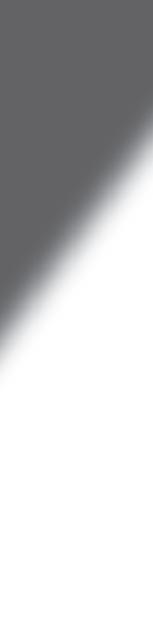
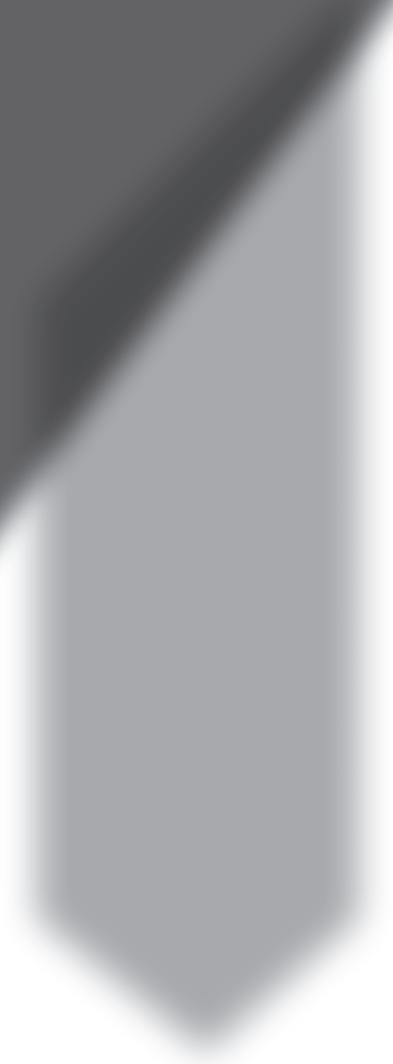
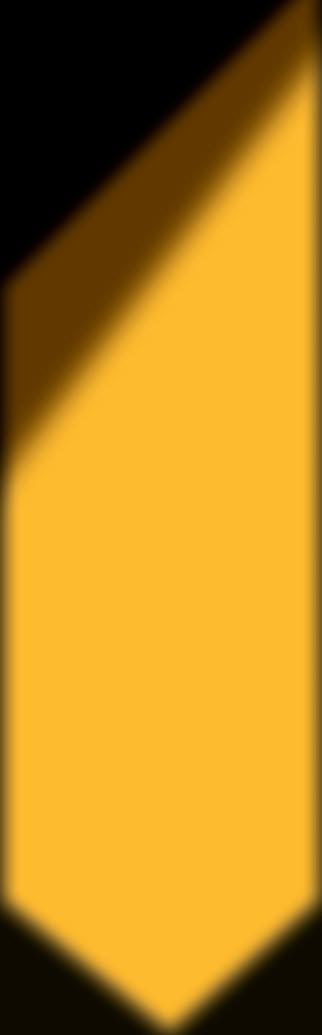



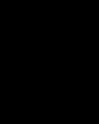





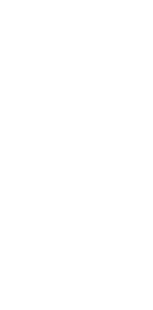
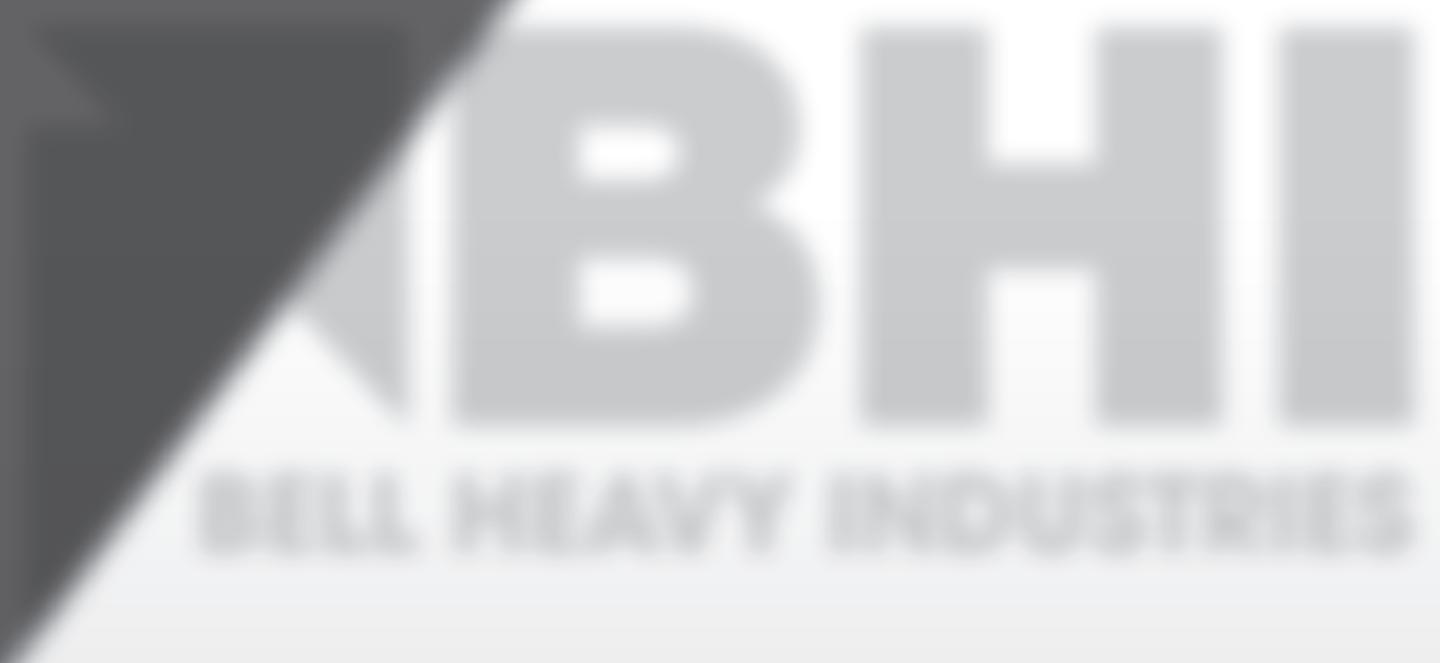




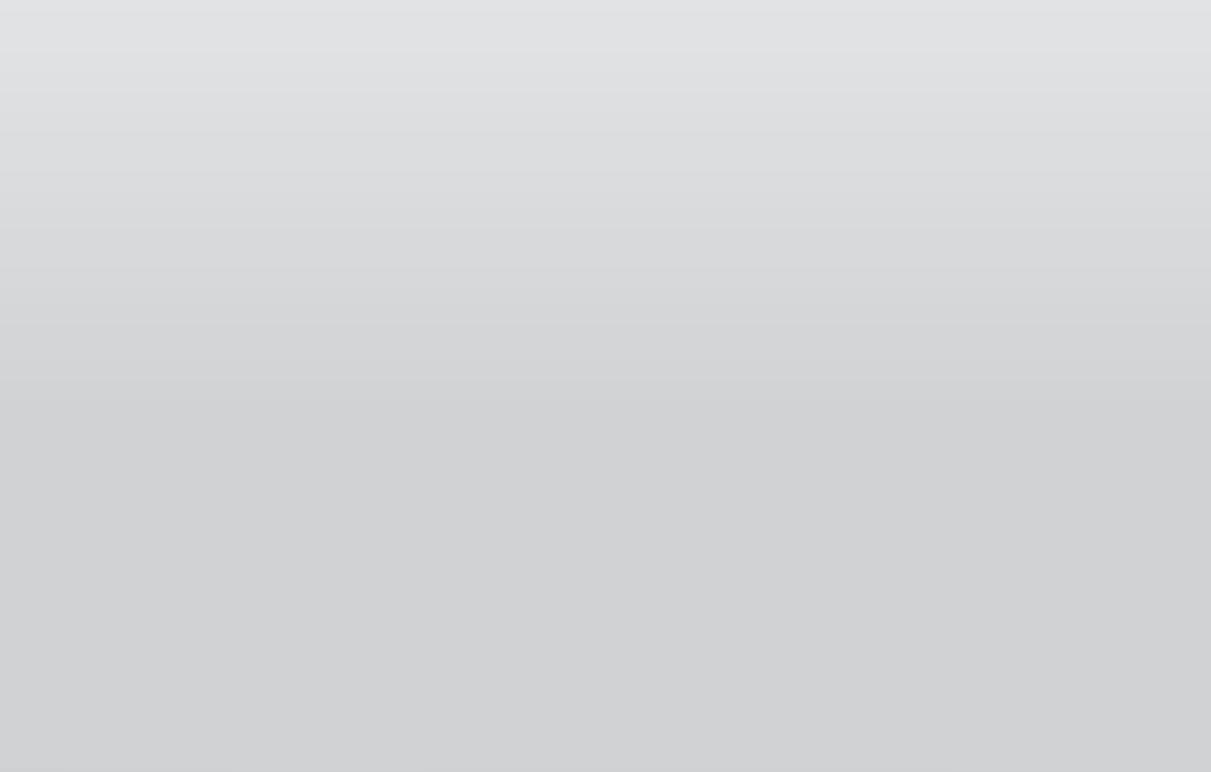




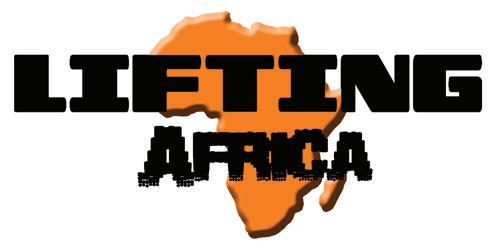
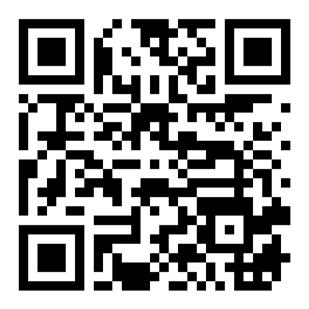
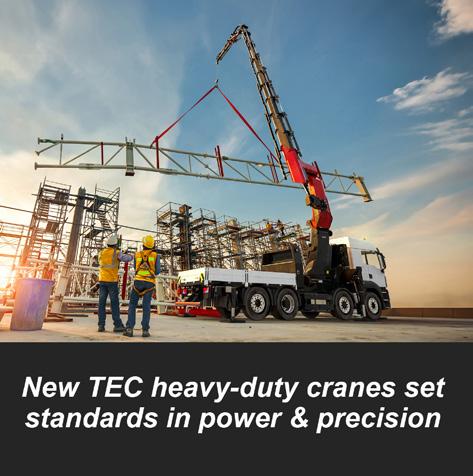
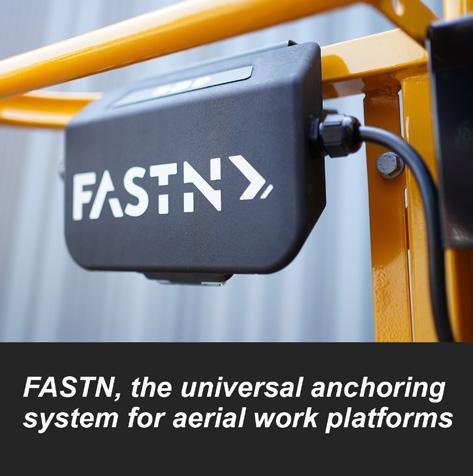
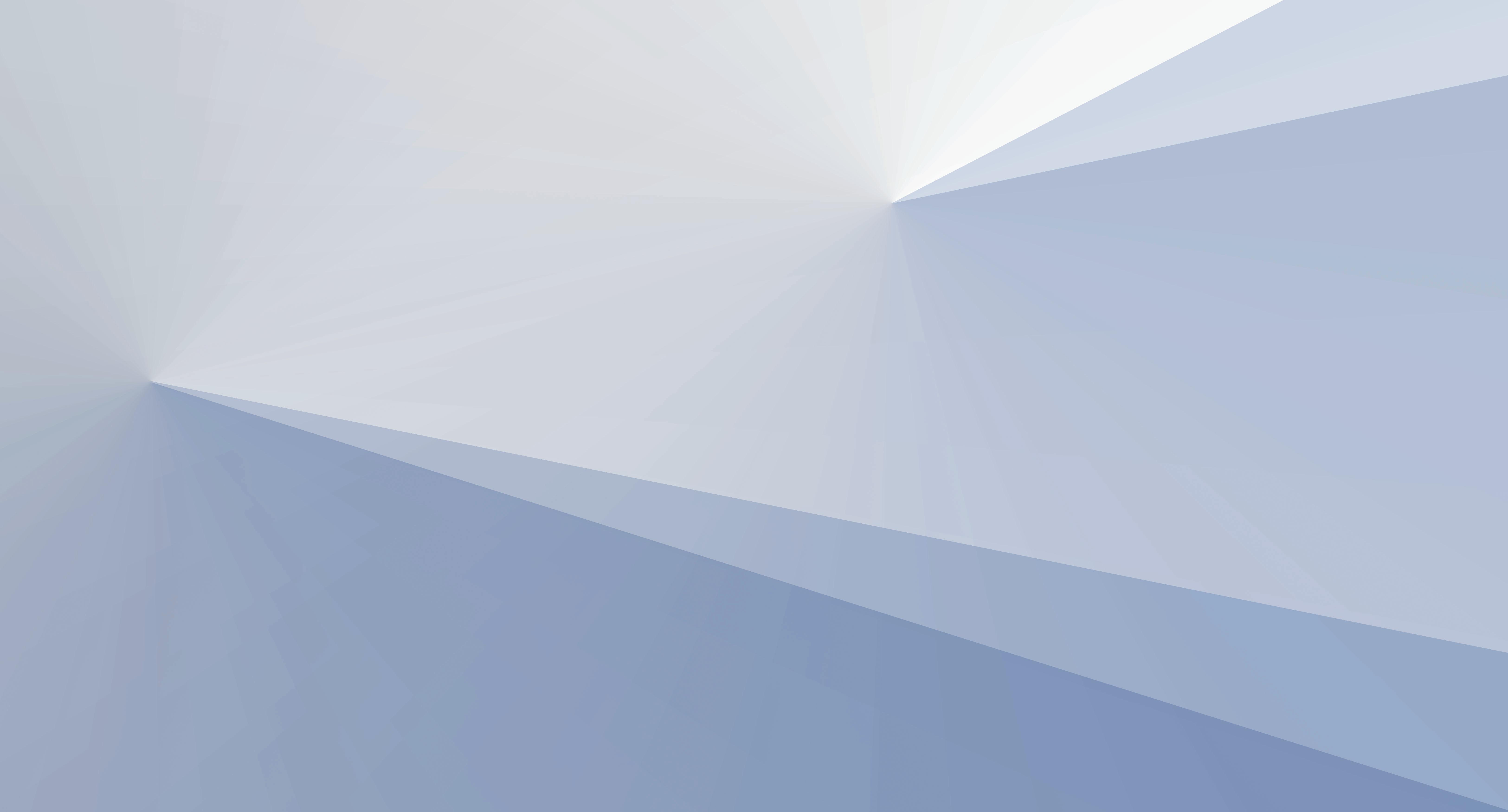
Meeting customer requirements and expectations while staying abreast of evolving industry trends is paramount in today’s dynamic business landscape. Goscor Lift Trucks’ (GLT) that has been providing trusted equipment solutions for 40 years, dedication to innovation and customercentric approach continues to set the bar high. Lifting Africa spoke to the company’s Director of Business Development, Patrick Barber, to learn more about recent developments at GLT.
In an era of rapid change, innovation is the cornerstone for lifting companies like GLT, empowering them to adapt, thrive, and meet evolving market demands with cutting-edge solutions. “In our industry, we are seeing ongoing technological developments by original equipment manufacturers (OEMs) aimed at improving machine efficiency,” says Barber, emphasising the importance of staying abreast of ongoing change.
“While lithium-ion technology is already in use and gaining traction, there’s also ongoing research into other technologies, including more efficient forms of fossil fuels and greener alternatives.”
According to Barber, they expect to see even further technological advancements within the next five years.
“Companies are exploring various avenues to make machines more efficient and environmentally friendly,” he says. This comes as more and more customers recognise the dual imperative of enhancing efficiency while minimising environmental impact. The need to create machines that perform better and contribute positively to the environment, aligning with evolving consumer preferences and regulatory requirements, remains a driving force across the sector.
“At GLT, we continue to drive innovation,” says Barber. “We always ensure that our product solution offering aligns with customer requirements and expectations. Our professional approach ensures that we provide
the best advice and the correct machine specification for each application to avoid unnecessary frustration and downtime. Access to the Goscor Group allows customers to buy equipment from our operating businesses (Cleaning Equipment, Earthmoving Equipment, Compressed Air, Power Products and Lift Trucks).”
Goscor provides its customers with four decades of extensive equipment sales experience, supplying the highest quality equipment at competitive prices.
Barber underscores Goscor’s commitment to customer satisfaction, citing its tailored solutions, extensive support, and access to top-tier equipment brands as critical competitive advantages. “Our holistic approach ensures that our customers receive unparalleled support and the lowest total cost of ownership,” he assures. “Operating with the world’s greatest equipment brands available to the African continent, customers are ensured complete peace of mind with the backing of skilled and experienced factory-trained technicians, comprehensive parts holdings, and a national footprint. This ensures 24/7 support for the equipment we provide and results in customers ultimately enjoying the lowest total cost of ownership over the lifespan of their equipment.”
Ongoing investment in its operations is a critical component of GLT’s success. Not only in the product range but also in expanding the footprint. “Our Johannesburg branch is gearing up for a significant shift as we relocate to new premises in mid-2024,” reveals Barber. “This move reflects our commitment to growth and efficiency, consolidating our operations under one roof to better serve our clientele.”
Another of Goscor’s recent endeavours involves rebranding its premier forklift brand, Doosan, under the iconic Bobcat name. This is in line with the global Doosan Bobcat rebranding strategy.
“Bobcat forklifts have a rich history dating back to 1968 when the first forklift was manufactured in South Korea under the Daewoo brand,” explains Barber. “In 2005, Doosan acquired the company, forming Doosan Industrial Vehicle (DIV) in 2011. In 2021, Doosan Bobcat took over the entire organisation, including manufacturing facilities in Incheon (Korea),
Yanta (China), and Lübben (Germany). Presently, the company operates in over 90 countries.”
The market has embraced the change with outstanding reception of the machines.
“Since the introduction of Bobcat-branded forklifts earlier this year, customer response has been overwhelmingly positive. The allure of the Bobcat brand has sparked excitement among our clientele,” notes Barber, emphasising the brand’s enduring appeal and reputation for excellence. “The current rebranding initiative does not entail a change in the equipment’s manufacturing or technology. Instead, it is simply a shift in branding, from the infamous orange Doosan branding to the white Bobcat branding, with the same high-quality machinery now bearing the iconic Bobcat name. The aesthetic appeal of the Bobcat-branded forklifts is self-evident - the core functionality and quality of the machines remains unchanged.”
The company also recently acquired the agency for Movexx electric tugs, which has broadened its offering to the industry, allowing efficient operations and the lowest total cost of ownership. This strategic acquisition further cements GLT’s position as a leader in delivering efficiency and cost-effectiveness across diverse operational landscapes. With increasing interest in Goscor’s products across Southern Africa and further afield on the continent, the company is poised for expansion. “Our expanding footprint, coupled with growing demand, positions us for continued success,” says Barber, indicating that through its network of sister companies, GLT has the necessary support to assist its growth plan.
Recognised for its extensive range of electric, gas and diesel-powered forklifts and exceptional after-sales service, GLT has established itself as a dynamic forklift company offering comprehensive warehousing solutions. “By staying attuned to customer needs and leveraging our extensive experience, we tackle challenges head-on, ensuring seamless operations and maximum value for our clients,” affirms Barber, who has been with Goscor for over two decades
and is well acquainted with the process of forklift rebranding. “Amidst the rebranding and other developments, the company remains steadfast in its commitment to driving positive change and exceeding customer expectations,” concludes Barber.
Goscor Lift Trucks, +27 (0) 10 594 4339, lifttrucks@goscor.co.za, www.goscorlifttrucks.co.za
After a rapid start, 2024 shows no signs of slowing down. So far, the journey has kept us on our toes with each passing month presenting new challenges and opportunities for growth and innovation in the lifting sector.
Behind the scenes, the LEEASA team continue to work hard, day in and day out, to deliver enhanced value to our members, and the commitment to excellence does not waver. Only when we all work together can we navigate the complexities of our industry, always striving to exceed expectations and set new benchmarks for excellence.
This includes an ongoing focus on education, driving knowledge and skills commitment to ensuring legal compliance and best practices within the lifting industry. Recognising the critical importance of clarity and transparency, we have spared no effort to enlist the expertise of leading subject matter experts and engineers to deliver user-friendly and informative guides for our industry. The contributions of these experts have been instrumental in developing resources such as the Vetting Guide, which serves as a comprehensive roadmap for end-users and responsible parties alike. By outlining the legal obligations and requisite documentation necessary when engaging service providers, we aim to ensure that all work conducted adheres to the highest safety and compliance standards.
Similarly, we’ve developed the Monorail Beams and Jib Cranes Guide to tackle the confusion around testing these critical components. This guide empowers endusers and inspectors with clear protocols, ensuring safety standards are met confidently.
But, the year is far from over, and there are still plenty of exciting things on the horizon. We are looking forward to our participation in the upcoming Electra Mining 2024 event taking place from 2 – 6 September at the Johannesburg Expo Centre.
As the most significant mining, electrical, automation, manufacturing, power, and transport trade show in Southern Africa, Electra Mining presents unparalleled opportunities for networking, education, and collaboration. Our presence at this prestigious event underscores our unwavering commitment to advancing industry knowledge and fostering meaningful
connections within our community. We can also tell you that preparations are well underway for the twoshow. This year will also once again see forklift drivers take each other on showcasing their skills and abilities.
which aims to recognise and reward highly skilled and safety-conscious forklift operators, will take place daily. Each competitor will have twenty minutes to complete will receive a trophy and a cash prize and be crowned
show’s final day. There will also be a daily educational slot for a Forklift Proof Load Test and Racking Proof Load
As much as things remain constant, they also evolve. As South Africa gears up for its upcoming elections, LEEASA is also poised for some change. The imminent Annual General Meeting (AGM) will bring forth the election of change and adjust accordingly. We are grateful for your steadfast support and dedication to our common goals. Let’s press forward with determination and innovation,
Feel free to reach out to the board members if the need
Administration: Desiré Davis: admin@leeasa.co.za
Marketing: Xane Roestroff: production @leeasa.co.za
Yours in SAFE LIFTING, Surita Marx and the rest of the LEEASA team
Mr. Aaldrik Graham Kiewiet
Mr. Alan Victor Botha
Mr. Albert Anthony Freeme
Mr. Alfa Janes Grouws
Mr. Amogelang Gilbert Mmusi
Mr. Ananias Zhou
Mr. Andrew John Ferguson
Mr. Andries Aucamp
Mr. Andries Josias Agenbag
Mr. Antoni Frederik Janse van Niewenhuizen
Mr. Gavin Rayson
Mr. George Cornelius Krafft
Mr. George Khehla Kuhlase
Mr. Gerhardus Jacobus Oosthuizen
Mr. Gert Vos
Mr. Given Nyathi
Mr. Glenton William Rebello
Mr. Happy Tafara Tati
Mr. Harris Naidoo
Mr. Hendrick Rapule Mahuma
Mr. Hendrik de Jong
Mr. Milton Mhlanga
Mr. Mogakolodi Gregory Thamage
Mr. Mohamed Hoosen Dawood
Mr. Napo Michael Noosi
Mr. Nathaniel Happy Sambo
Mr. Neil Naude
Mr. Nelson Chaita Moyane
Mr. Nicolaas Theunissen Wynant
Mr. Nkosinathi Richard Mavimbela
Mr. Noel Nyamukoho
Mr. Octovias Lebakang Mabelane
Mr. Eugene Terence Redelinghuys
Mr. Evans Farai Chabata
Mr. Ferdinand Pieterse
Mr. Francois Dewald Blignaut
Mr. Francois Frederikus Le Grange
Mr. Francois Weideman
Mr. Frank Warrick Saayman
Mr. Frederek Gerhardus Opperman
Mr. Frederik Wilhelm Stonehouse
Mr. Marius van der Merwe
Mr. Mark Leonard Munnery
Mr. Mark Leslie O’Connor
Mr. Matthys Daniel Taljaard
Mr. Matthys Michiel Brink
Mr. Mboshoa Simon Skosana
Mr. Michael Fernandes De Souza
Mr. Michael John Hendry
Mr. Michael Lionel Roberts
Mr. Pastor Noosi
Mr. Paul Pillay
Mr. Peter Abraham du Toit
Mr. Petr Kluson
Mr. Petrus Abraham Bester
Mr. Phata Simon Mailula
Mr. Philippus Stefanus Kruger
Mr. Phillip Demetrius Kemp
Mr. Pieter Albert Schoeman
Mr. Ralph Errol Shamrock
Mr. Raphael Letsema Shobane
Mr. Reino Schutte
Mr. Robert Du Toit
Mr. Robert Wayne Milne
Mr. Rodney Bassingthwaighte
Mr. Roland Henry Murray
Mr. Ronald John Laing
Mr. Royden Stewart Turner
Mr. Rudzani Collins Masiagwala
Mr. Russel Henning Boshoff
Mr. Rutendo Job Sadomba
Mr. Sarel Petrus Jacobus Dreyer
Mr. Seth Laredo
Mr. Shimane Martin Diutlwileng
Mr. Siegfried Schrader
Mr. Stefan Ivanov Babatchev
Mr. Stephen Andrew McGregor
Mr. Steven Duvenage
Mr. Stuart Mark Love
Mr. Stuart Swart
Mr. Thulani Ndlovu
Mr. Timothy Tatenda Zindi
Mr. Tshisamphiri Moses Mukoma
Mr. Victor Manuel Batista Ferreira
Mr. Victor Thedor Sargent
Mr. Vishay Ramkaran
Mr. Warren Naude
Mr. Weddington Chimbane Moyo
Mr. Werner De Bruyn
Mr. Werner Hermann Schroer
Mr. Werner Snyman
Mr. Willem Abram (Bossie) Prinsloo
Mr. William Henry Pepler
Mr. William Peter Park
Mr. Wynand Byleveldt
Mr. Yogandren (Donny) Soobramoney
Mr. Zenzele Siphamandla Ntshakala
Mrs. Ruwaida Mahomed
Mrs. Surita Marx
“These records are up to date at the time of going to print”
In the modern world businesses face numerous challenges, including increasing customer demand and greater competition. It is therefore more important than ever for businesses to have an approach to drive efficiency in their operations and ensure customer satisfaction.
Developed when Toyota established the concept of lean manufacturing with the Toyota Production System, the TLLM approach focuses on continuous improvement in a business. TLLM incorporates two key concepts: Jidoka, a form of intelligent automation, and Just-in-Time, which focuses on eliminating waste in manufacturing processes and encouraging efficiency. Although a product of lean manufacturing, TLLM extends beyond the realm of manufacturing and is applicable to businesses in various sectors. TLLM’s primary goal is to ensure that waste is minimised in all business operations. But implementing TLLM also drives the profitability of a business, by looking at ways to provide
the highest quality products at the lowest cost and in the shortest time possible. Adopting the concept of TLLM helps businesses to think differently about their operations.
“Imagine TLLM as a house, with its roof symbolising business goals. You need to have the walls, pillars and a solid foundation to make sure that the house is in order. TLLM provides the components to build a strong house for your business to be sustainable and effective in the long term,” says Vuyokazi Bangazi, National Sales Manager for Toyota Material Handling, a division of CFAO Equipment SA that sells forklifts and value added solutions.
“Toyota Material Handling can assist our customers to implement the concept of TLLM in their business. Combined with the premium brand equipment that we provide, this collaboration will empower our customers to outshine their competition,” says Bangazi.
One of the important components in TLLM is the implementation of 5S, which includes the pillars or principles of sorting, setting order, standardisation, sustaining and shining. This system ensures that the workspace is clear, organised, and efficient, contributing to the overall effectiveness of a business.
TLLM also recognises and addresses seven types of waste, known as Mudas, that can hinder business efficiency. These include overproduction; waiting
or time on hand, including machine downtime and waiting for materials to arrive; excess inventory or information, for example paper archiving; and unnecessary transportation or bad timing in the movement of goods. Further Mudas include motion inefficiencies, processing errors, and making defects.
Implementing TLLM requires a strategic approach, starting with the foundational step of 5S implementation. Once this foundation is laid, businesses can move on to addressing the seven Mudas, identifying and addressing these wasteful elements to streamline their operations and maximise profitability.
In the pursuit of customer satisfaction, TLLM plays a crucial role. By eliminating waste and inefficiencies, TLLM contributes to quicker response times, improved customer experiences, and maximum uptime. The symbiotic relationship between efficiency and customer satisfaction creates a positive feedback loop, fostering sustained success.
make it a versatile tool for companies seeking to optimise their operations regardless of their sector.
By aligning with global TLLM standards, companies can benchmark themselves against industry leaders and continuously strive for improvement.
Toyota Material Handling has embraced TLLM for years, and we have a specific strategy in place to elevate its implementation in our company by 2025.
By measuring our performance against global standards and benchmarking ourselves against our peers, Toyota Material Handling continuously strives for improvement,” says Bangazi.
“Also, part of our strategy for the year ahead is to exceed our customers’ expectations, and TLLM will play a crucial role in solidifying our relationships with our customers.”
TLLM is not merely a business strategy; it is a phenomenon shaping the way organisations operate and strive for excellence.
TLLM plays a pivotal role in refining business operations by fostering a culture of continuous improvement. By identifying and addressing inefficiencies and waste, it allows organisations to enhance productivity and reduce costs.
As the journey continues, the TLLM phenomenon promises to redefine the landscape of business operations, creating a more streamlined, effective, and customer-centric future.
CFAO Equipment SA, +27 (0) 11 571 0200, info@cfaoequipment.co.za, www.cfaoequipment.co.za
“Toyota Material Handling takes the standard TLLM concept and personalises the approach for each customer’s area, expertise and production. We tailor make a solution based on our customer’s specific needs, no matter the type of business or in which industry they operate,” says Bangazi.
One of the remarkable aspects of TLLM is its universal applicability. While it originated in the manufacturing sector, its principles can be seamlessly applied to diverse industries, including retail, logistics, and warehouses. The simplicity and effectiveness of TLLM
It is heartening to see a growing trend in the warehousing and logistics sector for more eco-friendly operations that minimise harm to the environment.
As sustainability becomes increasingly important, there is a shift to replace traditional combustion engine forklift trucks with highly efficient, eco-friendly electric forklifts.
“The investment in electric forklifts transforms warehousing operations, by reducing harmful carbon emissions, enhancing energy efficiency, lowering noise levels and minimising downtime,” states Brenton Kemp, managing director of Criterion Equipment, exclusive distributors of TCM forklift trucks in Southern Africa.
“Our team of specialists works closely with all sectors of business to improve the efficiency and sustainability of each customer’s materials handling operations, by matching the correct forklift truck with exact requirements.
“Criterion Equipment’s flexible range of TCM forklift trucks includes the 4-wheel electric counter-balance FB-IX series, engineered for high productivity and safe operation. These versatile electric forklifts - known for reduced operating costs, greater controllability, low noise and modern ergonomics - have been particularly well accepted for use in warehousing and storage facilities. Of particular importance are impressive energy-saving features that improve productivity by ensuring low electric consumption and allowing longer working hours per charge.
“These machines are particularly well suited for use in warehousing and logistics for many other reasons - apart from low noise levels during operation, FB-IX forklifts have important safety features that mitigate the risk of accidents, ensuring a secure working environment.
“Versatile FB-IX machines are able to safely and efficiently handle various tasks - from loading and unloading goods to stacking and transporting heavy materials - in warehousing, logistics, manufacturing and construction.” The counter-balance FB-IX series - a Class 1 sit-down rider type machine, available with standard wheel bases and a load capacity range between 1,8 tons and 3,5 tons – offers smooth acceleration, precise control and excellent manoeuvrability, even in tight spaces. TCM FB-IX forklifts are available with the option of traditional lead-acid or Lithium Ion batteries for enhanced propulsion. Traditional lead-acid batteries are cost-effective and suitable for standard applications, while Li-Ion batteries provide extended life and enhanced performance, making them ideal for intensive operations that demand longer runtimes and reduced charging times.
There are three ECO modes available – Power (P), Normal (N) or Custom (C). In addition, selection of N mode and ECO mode together, provides up to 11 ½ hours of operation time before the next battery charge is necessary. Users are able to easily select the most suitable operating mode for travelling or load handling, to suit specific driving skills and working conditions.
The custom mode allows easy adjustment of the truck’s characteristics for efficient operation in all conditions. This includes control of acceleration and response of the accelerator and hydraulic lever, to suit the operator’s preferences. And to save unnecessary power consumption during truck idling, an ‘auto power off’’ facility cuts the power off automatically after 15 minutes of inactivity. This also acts as a safety feature to prevent possible accidents when the operator gets
back on the forklift.” Electric energy is efficiently recovered by the standard TCM regeneration system which includes accelerator-off, switch-backs, braking, slowing down on downhill and lift/tilt operations. The optional ‘smooth run system’ has two accumulators that absorb vibrations in the lift cylinder when going over bumps, to enhance safe and comfortable operation. This system also reduces shocks and noise levels during all stages of load handling – from no load to full load.
These robust forklift trucks have advanced design features for reliability and durability, including a rigid single-piece, integrated frame and side body. A cast steel bumper protects the rear frame from impacts that occur during busy operations, significantly extending the life of the machine. The IPX4 Index Protection (IP) rating prevents the ingress of water spray from all directions, even during outdoor operation in rainy conditions. The ergonomically designed operator’s compartment offers improved comfort, precise control and reduced fatigue.
In situations where operators need to get on and off the truck frequently – particularly in warehouse applications – the low-floor and wide-step designs, significantly reduce operator fatigue. Important design features include an adjustable seat, intuitive controls and excellent visibility.
Criterion Equipment’s range comprises all models of TCM forklift trucks, covering most forklift classes. These include Internal Combustion (IC) counterbalance trucks, electric counter-balance trucks, reach trucks, powered pallet trucks and rough terrain forklifts.
Mast configurations vary from standard two stage 3 m masts to high-reach three stage masts.
The company supports these machines with a technical advisory, spare parts, repair and maintenance service to ensure optimum performance from every machine.
Criterion Equipment , +27 (0) 11 966 9700, info@criterion.co.za, www.criterion.co.za
Mammoet is working with Rietveld, a specialist in fleet management and vehicle and machine safety systems, on a joint project to protect drivers and road users when mobile cranes are moving and maneuvering.
The project combines three different safety technologies and was commissioned by Mammoet to support its customers to meet stricter safety regulations. Testing is currently being carried out on one of its new Liebherr LTM 1070-4.2 70t mobile cranes.
The three-tier system includes Rietveld’s OmniVue 360° camera system. Using a combination of cameras installed on the crane’s chassis, it generates real-time first and third-person images of the vehicle. This gives the driver a full 360-view from both inside and outside the cab, enabling them to see what pedestrians and other roads users are seeing.
The second tier adds a series of sensors that detect people and obstacles within an adjustable safety radius around the crane. When the sensors detect a potential hazard, an acoustic signal alerts the driver. An LED warning panel also displays the section of the crane where the motion was detected.
The final tier, the ‘Halo’, draws a light boundary on the floor around the crane, giving those nearby a clear visual indication of the safe zone around it. This is especially important at sites where hearing protection is required. The boundary can be switched on and off manually and is set
to automatically turn off when a certain speed is reached.
Ferdi Kivanc, Project Coordinator EMD at Mammoet, said:
“By combining these three systems, Mammoet will improve safety, minimize accidents and damage, and give greater confidence to crane operators to create safer working environments. We see this as a comprehensive system that will not only enhance crane safety, but also operator training in the future. Initial tests are promising, and I am very proud of the results.”
Frank Kanters, Account Manager at Rietveld, added:
“When Mammoet approached us with what it wanted to achieve, we were delighted to offer our expertise. By working with its engineers to test the integration of our collision-prevention technologies, we have created something unique in crane safety solutions. We look forward to developing the system further and progressing to eventual rollout.”
Mammoet Southern Africa, +27 (0) 21 842 2762, sales.southernafrica@mammoet.com, www.mammoet.com
Double bogeys fitted to the end-carriages of this overhead crane represent the key to a puzzle recently solved by Condra: how to meet customer specifications while still being able to install the completed crane in a factory with no roof access and limited headroom.
Usually, installation of a crane of this type involves lifting the disconnected end-carriages onto the gantry first, then attaching the girders to form the frame of the crane, and finally lowering the crab and hoist into position from above.
The problem in this case is there is not enough factory headroom to do that, even though Condra has designed the crane with a lowered profile to achieve maximum lifting height.
Condra’s solution was to fit both 12-metre-span steel girders with bogeys at each end, four bogeys in all, and develop a different installation sequence. Fitting the girders with bogeys frees up an additional 20 millimetres of headroom through reduced wheel loading and smaller-diameter wheels on the end-carriages.
Integral bogeys also allow placement of the girders on the factory gantry as the first step. Moving the girders apart then delivers space to allow lifting of the hoist into position between them, instead of lowering it into position from above. Closing up the girders, then linking and fixing their bogeys results a completed crane with two double-bogey end-carriages.
Condra specialists will carry out this installation at the customer’s Johannesburg factory this month (April).
The unusually large rope drum on this hoist, seen here nearing completion at Condra’s Germiston factory, has been designed to hold and manage nearly 700 metres of rope, winding and unwinding it at high speed during very high lifts of 150 metres within a narrower-than-normal mineshaft. Careful calculation of rope drum dimensions and winding sequence was the focus of the drum’s design. Drum PCD (pitch-circle-diameter) is 1600mm. A 4:2 centre-lift reeving arrangement will avoid snagging the mineshaft sides.
The drum will carry 676 metres of
18mm rope, lifting and lowering loads at 30 metres per minute, almost ten times faster than lifts in standard overhead crane workshop applications.
Condra’s design team had to coordinate the drum width with a PCD and reeving arrangement that will precisely control and restrict lateral movement of the four ropes moving vertically as they lift or lower the load. The rope will wind onto or unwind from the drum in opposite directions as the drum rotates.
The hoist features improved drives, gearboxes and safety devices, and enhanced operation by remote control. Motor design is such that the load placed on the electric motor will remain manageable despite the non-stop nature of the work at the mineshaft.
Crab span is 6972mm with a wheelbase of 3400mm. Crab and hoist disassemble to fit into a standard 12-metre shipping container.
Condra (Pty) Ltd, +27 (0) 11 776 6000, sales@condra.co.za, www.condra.co.za
Konecranes launched its flagship Konecranes X-series industrial crane, the successor to its popular CXT model with a new compact design and safe, reliable technology that — thanks to its wireless upgrade capabilities — can adapt to customer needs now and in the future.
“The new flagship crane builds on a quarter-century of success for the CXT, which was launched in 2000 and to date has sold well over 100,000 units globally,” said Jussi
Luokomaa, Product Manager, ISE EMEA, Konecranes. “We expect to see good demand for the Konecranes X-series across multiple industries including general
manufacturing, making it a core product for the company for years to come.”
Connectivity for enhanced performance
The Konecranes X-series stands out not only for its lean, state-ofthe-art electrical architecture but also for its connectivity. Designed to be safe, compact and reliable, it can flexibly adjust to future customer requirements, maximizing the investment’s value. This adaptability is enabled by smart, connected components, allowing seamless software upgrades “over the air”— a first in the standard crane industry.
Customers have the option to initially purchase the crane and easily upgrade to additional Smart Features, enabling seamless incorporation of functionalities as business needs evolve. Additionally, troubleshooting and software updates can be conveniently conducted from floor level, minimizing potential downtime. With a focus on userfriendly design, the crane features a new ergonomic CANMAN radio with an integrated display, providing operators with freedom
of movement and essential information at their fingertips, while also offering stepless control for safer and more precise lifting experiences.Equipped with TRUCONNECT Remote Monitoring, the Konecranes X-series provides vital insights into crane usage and operation. This data, combined with maintenance information, empowers businesses to make informed decisions regarding maintenance schedules, safety and productivity enhancements. This innovation in connectivity underscores Konecranes’ commitment to enhancing productivity, reducing downtime, and leading in digital services, reflecting the growing importance of connected equipment in material handling. To date, Konecranes has 53,600 pieces of connected equipment globally.
A great crane needs a great hoist
What further distinguishes the Konecranes X-series crane is the new Konecranes S-series low headroom hoist. This compact hoist features excellent approach
dimensions and smooth stepless lifting with a load-dependent lifting motor, enhancing the user experience and reducing cycle times. The use of strong, lightweight, durable synthetic rope improves safety and handling compared to steel wire rope.
The X-series shows how Konecranes is shaping next generation material handling for a smarter, safer and better world. Through sustainable design and material choices, such as a more compact and efficient motor and synthetic rope, the X-series drives efficiency improvements. Features like a thrust rocker reduce steel consumption, and an optimized belt drive reduces wear, minimizing the overall environmental impact. The optimized design, with synthetic rope and guide rollers,
Looking for a quality Load Testing Company you can depend on? Well, look no further.
Here at 360 Load Testing Services (Pty) Ltd we are available where you need us, when you need us. In Africa we’ve been committed to being the best at what we do, serving clients by not just meeting their expectations, but exceeding them.
All Lifting Machine Inspectors that are utilized by 360 Load Testing Services are registered with the Engineering Council of South Africa (ECSA) and the Department of Labour (D.o.L) to carry out compulsory inspections and load tests of Lifting Machines and Lifting Tackle.
minimizing energy waste. With the X-series, Konecranes delivers a reliable solution while having an emphasis on sustainability.
The Design for Environment (DfE) approach guided product development, aiming to minimize environmental impact throughout the product lifecycle.
A strong focus on customers and commitment to business growth and continuous improvement make Konecranes a material handling industry leader.
This is underpinned by investments in digitalization and technology, plus our work to make material flows more efficient with solutions that decarbonize the economy and advance circularity and safety. Konecranes is now taking orders for the crane and expects the first deliveries to begin in Q4 2024 in Europe, Middle East and Africa,
2024 is upon us, and with it a whole new list of challenges. This is not something unique to the storage equipment market, but for all South Africans. With these challenges, some companies are ready to throw in the towel. Call it a day. There is no need to recount them all here, us South Africans live them day by day.
Challenges, however - the Acrow team believe - are just an opportunity to rise. To overcome and find solutions. That is the Acrow way.
“2023 was a good but difficult year for us,” say’s Sandra Moya, CEO of Acrow Storage Solutions. “We certainly did some new and interesting projects, such as The Foshini Group.” “As a team I think it’s something we as Acrow can be so proud of.
The complete process has been near flawless and the precision in the manufacturing and installation has been outstanding”, say’s Darren Penny, Acrow Project Manager at The Foshini Group installation.
The project is certainly something to be marveled at, consisting of two mammoth mezzanine floors. The first mezzanine was a pick module which was 112m long, 57m wide and a whopping 12m high. Occupying 6384 square meters of floor with a ground level and 3 levels. Impressively it consisted of 760 completed frames, 25 916 Beams and 2.63 km of main mezzanine IPE beams which fit together perfectly. The second mezzanine was 118m log, 87 wide and 5.6m high. Occupying 7625 sqm with a ground floor and two levels.
“It’s because of Acrow’s experienced team and trusted partners and suppliers this was possible,” says Sandra. “We expect completion by the end of January 2024.”
Acrow has also been mitigating some of the risks which have been plaguing the economy and all manufacturers for some time. “We recently invested in Solar installation at our manufacturing plant, allowing us to keep in control and minimize the risk of being without power,” says Sandra “whilst we outsourced the panels and installation, we manufactured the framing structure as we have the resources and experience in manufacturing these structures”.
Once more, showing that Acrow is truly committed to investing in their business to sufficiently support all levels of storage requirements, Acrow has recently invested in a 6kw laser, which is at the forefront of technology in the sheet metal sector. “Our customers have varying demands and always require bespoke and tailor-made solutions,” remarks Alessandro Zumerle, Operations Director at Acrow, “we sometimes must get creative to ensure that we can manufacture the products which are requested by our customers.
The new machines we are investing in, will ensure that we make these special products in less time, with high precision.”
Additionally, Acrow has also invested in various roll forming lines and welding machines to facilitate standard production.
The vision for 2024 is growth. Growth into new markets, and further penetration into the ‘more automated’ sectors of logistics. Acrow already has experience and many successful radio shuttle and mobile base installations, both nationally and internationally, “but there are some interesting projects in the pipeline,” comments Enrico Moya, “we are busy working with new technologies in the sector which will give customers both greater density to stock their products and higher flexibility to receive the stock they require. We are currently researching with international partners on these solutions which could really bring a solution to many of the problems faced by warehouses today”.
Acrow has further expanded and invested in their Scaffolding division. “We have all the tools, dies, jigs and machines to manufacture Acrow quick stage system and any formwork required by the market,” notes Sandra Moya. Acrow is situated in Wadeville Germiston, with a fully operational and technologically advanced 46 000m facility, has operational branches in Cape Town and Durban respectively. On the international front, Acrow boasts a branch in the United Kingdom, as well as a branch and manufacturing facility in Italy. With over 300 experienced employees, Acrow is able to design, manufacture and install any storage solution, from racking and shelving to more automated designs. Contact Acrow today for more information or a consultation, where one of their experienced sales consultants can work together with you and your team to find the best solution for you.
Manitowoc is proud to launch the Potain MCR 625 luffing jib tower crane. This heavy-duty crane is tailored to the unique demands of fast-expanding key markets across Asia, the Middle East, and Latin America.
It is a new design built at the Manitowoc factory in Zhangjiagang, China, but includes many features from the renowned MR 618, a popular crane in fleets across Europe and North America.
The Potain MCR 625 combines the robustness of a heavy-duty luffing jib crane with a remarkably compact footprint to deliver exceptional performance in urban environments. This enables contractors to take on grand projects in densely populated areas
with unprecedented efficiency and precision. “We are excited to introduce the Potain MCR 625, a crane that offers the perfect balance in power, precision, and compactness. By leveraging the proven design of the MR 618 and adding design elements for fast-emerging global markets, we are empowering contractors to tackle ambitious projects in urban environments with unprecedented efficiency and reliability,” said Leong Kwong-Joon, regional product manager for Potain tower cranes.
One key feature of the Potain MCR 625 is its moveable counterweights, which optimize load distribution throughout the structure.
This allowed Manitowoc’s engineers to design a highly compact crane, yet one that still offers strong lifting capabilities along the load chart and taller height under hook options.
The movable counterweights also ensure the crane remains well-balanced, allowing it to be erected on relatively slim 2.45 m mast sections for better on-site logistics and to facilitate installation on jobsites with limited space. Additionally, the MCR 625 can work with one or two-fall reeving
for faster hoist speeds and better productivity. There’s a maximum capacity of 32 t when configured for two-fall operation, while with one-fall it’s 17.5 t. The maximum jib length is 65 m, and a maximum tip load of 6.4 t at 65 m is available, enabling the crane to meet even the most demanding of high-rise project requirements.
Mounted on 2.45 by 2.45 m mast sections, the Potain MCR 625 can be configured with multiple jib lengths – either 30 or 40 m, and then in 5 m intervals up to the maximum of 65 m, providing contractors with the versatility to adapt set-up to project specifications. Even with its full 65 m jib, the crane travels in just 11 truckloads, minimizing transportation costs and logistical challenges.
The MCR 625 offers a choice of three hoists for further flexibility, all equipped with 603 m of wire rope. The crane will be sold across Asia, Australia and New Zealand, Africa, the Middle East, and Latin America.
The Manitowoc Company, crystal.chi@manitowoc.com, www.manitowoc.com
Limitless possibilities are what PALFINGER guarantees with its two new heavy-duty cranes: Outreaches of up to 38.7 meters are the result of the global market leader creating new premium heavyduty cranes for special and high load capacity applications with the PK 1350 TEC and PK 1650 TEC. The entire new TEC range combines maximum outreach, the highest lifting capacity and the greatest precision.
A pioneer for challenging heavyduty applications: the PALFINGER PK 1650 TEC. © PALFINGER
Complex tasks in urban areas and on large construction sites as well as heavier and larger loads require solutions that are smart and powerful. The new PALFINGER PK 1350 TEC and PK 1650 TEC heavyduty cranes are equipped with the very latest electronic controls and intelligent assistance systems. “As a technology leader, PALFINGER sets industry standards, always with the aim of using smart and connected solutions to improve the way customers work. The heavy-duty cranes in the TEC range are our latest example. Based on decades of experience and working together with customers and operators, we have created a completely new class of crane that combines the best hardware with smart software,” says Andreas Klauser, CEO of PALFINGER.
Higher and higher: PK 1350 TEC and PK 1650 TEC
More challenging structures, higher
buildings, maneuvering in limited spaces: the level of precision required by crane operators is constantly increasing. The premium heavy-duty crane PK 1350 TECincluding fly jib - has an outreach of up to 38.7 meters and a lifting capacity of 109.3 meter tons. With the same outreach, the PK 1650 TEC even achieves a lifting capacity of 124.8 meter tons. The intelligent PALTRONIC 180 control electronics and the LX-6 control valve ensure easy maneuverability. That is how TEC heavy-duty cranes provide operators with precise support during each task.
A special asset is its dual-circuit hydraulics, which ensure there is never a shortage of hydraulic power. This means that nothing stands in the way of demanding tasks that require several functions at the same time.
The TEC range sees PALFINGER completely redesign the loader crane, the company’s core product, by combining proven strengths with
intelligent technologies. All TEC models can be equipped with Smart Control, the intelligent crane tip control system.
It combines the crane movements in the background to achieve the exact position desired.
The Memory Position system stores up to four crane positions while the Leveling Assistant can save time by up to 80 percent while adjusting the setup.
“Following the launch of the PK 1350 TEC and the PK 1650 TEC, our TEC range now consists of a total of eleven models. Our modern and intelligent cranes, with load capacities between 23.5 and 124.8 tons, offer our customers a wide range of options for different types of work,” says Gerhard Auer, Global Product Manager Loader Cranes at PALFINGER. Orders can be placed now.
Palfinger Southern Africa, +27 (0) 11 608 3670, sales@palfingerafrica.co.za, www.palfinger.co.za
Polymer energy chain manufacturer, igus, has introduced a new lighter weight e-chain for cable management/protection applications with large unsupported lengths and high fill weights that was previously the domain of larger, more expensive energy chains.
The manufacturer’s “L” Lean variant has been specially designed for users for who its industry standard E4Q is too large. From the seventh robot axis in linear robot applications to machine tools, the igus E4Q-series energy chain has established itself in recent years in demanding applications with large unsupported lengths and high fill weights. The problem is that, in applications with medium loads (machine tools, woodworking, car washes etc.), the E4Q is oversized. One of the benefits is you have a larger inner fill area with the same outer specifications as the E4Q equivalent e-chain.
“To offer users the advantages of the E4Q in these applications as well and at a lower price, we developed the L version – the
E4Q.64L,” says igus South Africa managing director, Ian Hewat. “Depending on the width, the lowcost version of the energy chain costs between 15% and 20% less than the E4Q.”
To reduce costs, the igus designers have modified the E4Q’s design. The aim was to strike a balance between low dead weight and maximum robustness. The side links are narrower than those of the E4Q, reducing the weight. The bionic design, which dispenses with any material that has no loadbearing function, was retained. Tests in the igus test laboratory prove that the E4Q.64L has an approximately 30% greater breaking moment than the 14240 series, which is also used for unsupported applications. This results in up to
20% more length with the same fill weight. The chain can also be operated in two bending directions by replacing the outer link with a special RBR link. This gives it what is known as a reverse bend radius (RBR), which means that circular movements can be implemented (on a robot’s axis 1, for instance).
Unlocked on both sides, the crossbar can be lifted out with little effort. The other advantage is that an extensive product range of crossbar widths is directly available, so that the E4Q.64L has been offered in 29 widths between 100 and 500 millimetres since the start of market launch.
igus South Africa, +27 (0) 11 312 1848, ihewat@igus.net, www.igus.co.za
In January 2024, the first Bobcat-branded material handling units began rolling off the production lines at the organization’s plants in South Korea, China and Germany.
This milestone represents the culmination of a two-year global initiative, through which the full range of forklifts and warehouse equipment formerly produced by Doosan Industrial Vehicle (DIV) have been successfully rebranded as part of the Bobcat family.
The Bobcat brand is worldfamous for its extensive range of compact machines, which are used across multiple industries for a broad range of applications, including construction, agriculture, landscaping and ground maintenance. Bobcat’s compact loaders, wheel loaders and telehandlers can be equipped with attachments such as pallet forks, buckets, grapples and bale clamps, making them extremely popular among material handling and logistics professionals. The addition of forklifts (both internal combustion and electric) and warehouse equipment is therefore a natural extension to the company’s existing range. All material handling lines previously
manufactured under the DIV name have been brought into alignment with a single branded house, meaning that a diverse range of forklifts and warehouse equipment now sport the world-famous Bobcat colors.
The new range of Bobcat-branded material handling equipment comprises the following product lines:
• Diesel forklift trucks | lift capacities of 1.8 to 25 tons
• Liquified petroleum gas (LPG) forklift trucks | lift capacities of 1.5 to 7 tons
• Electric forklift trucks | lift capacities of 1.5 to 10 tons
• This segment also includes a line of three-wheeled electric forklifts designed for lighter applications, with lift capacities of 1.6 to 2 tons
• Warehouse solutions | pallet trucks, reach trucks and stackers
A global rebranding initiative
Rebranding equipment formerly produced by DIV was a truly collaborative effort, requiring the input of material handling departments from across Bobcat’s global network. This initiative necessitated more than 10,000 work hours and the direct involvement of approximately 100 employees. So, what did it take to complete this unprecedented exercise? In total, the global initiative required the rebranding of more than 200 products previously sold under the Doosan label. As
part of the project’s initial phase, these products were categorized under 36 ‘mother’ models according to their frames. They were then further grouped into six ‘grandmother’ models, which represented the main designs and machine types. From here, the 100-strong team developed and approved Bobcat branding for each of the six ‘grandmother’ models. They then followed the same process for the 36 ‘mother’ models before completing the exercise for all 200-plus individual products.
Vaclav Kratky, Senior Product Marketing Manager, Bobcat EMEA, said: “This marks a major milestone on our journey to bringing all our products under one roof as part of our one branded house strategy. Our unified approach will build further affinity with the Bobcat brand, both internally and externally, while growing our loyal customer base and creating new growth opportunities. In line with Bobcat’s world-famous brand DNA, this strategy will also allow for focused investment and increased marketing efficiency, facilitating the delivery of the same exceptional customer experience across all our organization’s product lines.”
Building on a strong heritage Bobcat’s newly rebranded material handling lines can trace their lineage back to 1968, when the first forklift truck was produced in South Korea under the Daewoo brand.
In 2005, Daewoo was acquired by Doosan, and DIV was founded in 2011 as part of Doosan Infracore.
In 2021, Doosan Bobcat purchased DIV and its assets. The deal included factories in Incheon, South Korea, and Yantai, China, which manufacture forklifts, as well as a facility in Lübben, Germany, which produces pallet trucks and stackers.
Bobcat’s incorporation of the former DIV material handling equipment represented an ideal fit, as both companies’ principles were so closely aligned. Bobcat is committed to protecting and enhancing DIV’s legacy by bringing simple and powerful machines to market, offering customers advanced solutions that are comfortable, dependable and environmentally friendly.
The newly rebranded material handling lineup will also benefit from Bobcat’s cutting-edge research and development (R&D) facilities, in-depth marketing expertise and comprehensive dealer network. By further expanding the division’s existing 140-strong dealer footprint in Europe, the Middle East and Africa (EMEA), and sustaining investment in innovation, Bobcat will continue to develop valuable and reliable material handling products that enable customers to perform their work efficiently and maximize their returns on investment.
“For more than 60 years, the Bobcat brand has been synonymous with quality, reliability and durability,” Vaclav Kratky added. “Our company has led the industry with tough, versatile, empowering and inventive equipment and solutions, and we continue to offer a world-class customer experience that distinguishes us from the competition.”
With the integration of the former DIV material handling lines, we are doubling down on the power
of the Bobcat brand. “This global rebranding initiative has resulted in a number of additional advantages for Bobcat customers, including an increased two-year warranty as standard for the majority of our products,” he continued. “Our standard warranties can be further enhanced with extension and financing programs, which begin from 0% for 24 months. As part of the project, we have also leveraged Bobcat’s industry-leading sales and service training programs and facilities to upskill our material handling dealers, which will enhance customer experience.”
Bobcat to showcase new material handling lineup at LogiMAT 2024 Bobcat intends to exhibit its extensive range of material handling equipment to a global audience for the first time at LogiMAT 2024, an international trade show for intralogistics solutions that will take place in Stuttgart, Germany, from 19-21 March.
The Bobcat product display will include both diesel and electric forklifts, reach trucks and warehouse equipment. It will also feature Bobcat’s TL25.60 supercompact telehandler, whose optimized dimensions and excellent maneuverability allow it to operate on confined worksites without compromising performance.
Redefining the future with hydrogen-powered forklifts
In January 2024, Doosan Bobcat demonstrated its unwavering commitment to a sustainable future by taking a major step towards the commercialization of hydrogen fuel cell technology. The organization’s inaugural hydrogen-powered forklift was unveiled at a ceremony at its Incheon factory. The 3-ton-capacity unit, which is equipped with a 20kW fuel cell, will soon begin work at Korea Zinc’s Onsan Refinery in Ulsan, South Korea.
While hydrogen-powered forklift prototypes have previously been produced by the industry, Doosan Bobcat is the first manufacturer to complete full development and deliver a commercially viable product ready for shipment. The organization aims to supply 30 hydrogen-powered forklifts in 2024, following the certification of a 3-ton 10kW fuel cell later this year. Plans are also underway to diversify the range with 2-ton and 5-ton models.
https://www.bobcat.com/mea/en/ doosan-forklifts-become-a-partof-the-bobcat-family
www.bobcat.com
We conduct the follow Lifting Equipment Training Courses:
• On line Management, Technical & Legal Compliance
• Lifting Tackle Inspection
• Chain Block and Lever Hoist Operation, Safety & Inspection
• Advanced Slinging & Inspection
We supply the following:
• Lifting Tackle Inspection Registers
• Lifting Tackle Wall Charts
• Lifting Tackle Plant Surveys, Audit & Reports
• Lifting Tackle Code of Practice
We will assist you to implement and
Magni Telescopic Handlers continues to launch innovations, with a machine offering incredible performance, the RTH 8.39, a rotating telescopic handler model that further extends the 8 tonne (17,600 pounds) range, taking its place alongside the 8.27, 8.35 and 8.46.
The outcome of a redesign of the 6.39, this new model offers improved load charts thanks to a lifting capacity increased by 2 tonnes (4409 pounds).
The distinctive feature of this model, like the RTH 8.35 and RTH 8.46, is its two extension modes, M1 and M2. These two modes give access to two different load charts, to maximise performance in all operating conditions.
The standard extension mode, M1, offers the operator the maximum reach and higher load capacities at the maximum height, while M2 mode restricts reach to provide increased load capacity. This translates into a lifting capacity of 8 tonnes (17,600 pounds) up to 13 m (42 feet), 400 kg (881 pounds) with horizontal reach of 27 m (88 feet) and 2.3 tonnes (5070 pounds) at maximum reach of 38.8 m (127 feet). Compared to the previous 6.39 model, the 8.39 delivers maximum load capacities at maximum horizontal reach 33% higher in both M2 and M1 modes.
Thanks to the introduction of this characteristic, the RTH 8.39 surpasses the sector standards with outstanding performances in all conditions, combining leading-edge engineering with the distinctive design of Magni products. Extremely rugged, it is the ideal solution for heavy-duty worksites thanks to agility, user-friendliness, reliability and precision, even at extreme heights.
Cab: Magni’s trademark safety, visibility and comfort
Common to the entire RTH range, the ROPS/FOPS Level 2 cab offers unrivalled safety and guarantees excellent visibility thanks to the extensive glazed areas and the slender steering column. What’s more, with the easy access system getting in and out of the cab is facilitated by a slight stagger between the turret and chassis.
To ensure the highest degree of operator comfort, the interior has hard-wearing panelling and quality finishes, produced by injection molding. The LED courtesy lights illuminate when the door is opened and gradually fade out once the machine is switched off. The airflows deliver effective defrosting in even the harshest weather conditions, while an adjustable sunblind provides shade on the sunniest days.
The lift up armrests create the space for a handy storage pocket on the right hand side. A case to protect the re mote control from wear and knocks is provided behind the seat. The RTH 8.39 is also equipped as standard with an air suspended, tilting premium seat with head rest.
(Magni Combi Touch System) on board control system
Consulted via the 12” touch screen, the RTH range’s software provides easy, intuitive use with user friendly icons to identify the various
functions. The various themed areas are accessed directly from the main menu screen, for a smoother, pleasanter user experience.
To enable work in compl ete safety, the Magni LLD (Live Load Diagram) system offers three different modes for displaying the load chart screen for effective control of the operating limits
• Standard,with all the load bands;
• Dynamic, showing the working area available in relation to the load lifted;
• Dynamic360°,for viewing the working area available from above, enabling greater precision in conditions of varying stability.
Like the other RTH range products, the 8.39 is equipped as standard with a rearview camera displayed on the MCTS monitor, activated automatically when reverse gear is engaged. With its dual extension capacity and consequent upgrades in performance, this mo del not only surpasses the industry standards but helps to redefine the concept of efficiency and versatility. The innovations made once again highlight the determination to develop higher and higher performing machines. By keeping faith with this approach, Magni TH continues to lead technological evolution in the lifting sector.
Magni SA, +27 (0) 11 383 2227, info@magnisa.co.za, www.magnisa.co.za
The 8-axle crane can complete hoisting work in the 700-tonne class or even higher with ease. It therefore has a nominal lifting capacity of 700 tonnes.
In a lifting capacity comparison, the LTM 1650-8.1 exceeds its predecessor’s capacity by between 15 and 50 percent, depending on its equipment package.
Safety is part of the Haulotte Group’s DNA and a key strategic priority. The Group’s mission is to ‘Take care of people’, life being the most precious asset, which is why all Haulotte teams are committed to protecting people working at height.
To meet this mission, the Group has developed, in an Intrapreneurship mode, an intelligent solution to tackle the major cause of fatal accidents on AWP: operator falls. Led by Catherine Perrier and Maxime Girard, the two intrapreneurs conceived the FASTN system to enable construction companies to support their ‘zero accident’ strategy by protecting their personnel and making construction sites a safer place to work. Equipment rental companies can also enhance their safety and digital technology offerings through FASTN.
Last Thursday, March 28th, the
“Grand Prix Matériel” ceremony took place during the 59th congress expo of the French professional equipment federation. The jury, composed of professionals and the chief-editor, rewarded the FASTN anchoring system with the ‘jury favorite’ award. The jury underlined 3 strong points to justify its choice: FASTN represents a reliable response to a major safety issue, the system is universal and can be adapted to all types of boom lift, and lastly, access to data enables risk analysis in the field.
Maxime Girard, Head of FASTN, shared his feelings the day after the ceremony: “It’s an honor to
receive the ‘jury favorite’ award for our FASTN solution! Our universal anchoring solution for AWP operators is easily installable on all brands and types of platforms. This will allow equipment renters to quickly equip their fleets with a unique system and thus meet the safety challenges of their clients; construction companies. The goal is to instill in operators the habit of fastening themselves as soon as they enter the basket of an aerial work platform, just as each of us does daily when getting into a car.”
A system inspired by seat belts FASTN works on the same principle as a car seat belt. The aim is to create a ‘reflex’ in the operator, a habit, so that when the operator enters the platform, they anchor their harness to the system, just as they would in a vehicle. The FASTN system consists of two ‘boxes’, connected, and installed in the platform’s basket.
The device thus detects 4 dangerous situations:
Harness detection: The operator is immediately alerted by a visual and audible alarm when operating the boom lift while not anchored
to FASTN. If the lanyard is not connected within a few seconds, the FASTN active anchorage also alerts the worksite with a flashing light and a louder alarm.
Anti-bypass function: If the operator attempts to bypass FASTN using something other than a harness carabiner, the active anchorage will detect inactivity and activate the wake-up function to alert the operator and the worksite of potential misuse. [pictogram] Operator wake-up function: When the operator is connected to FASTN and inactive for 1 minute, the system alerts the operator and the construction site of potential discomfort.
Wake up function: When anchored to FASTN, after 1 minute of inactivity, the system will alert the operator and the worksite to potential operator distress
Potential operator fall or ejection: During operation, if the system detects an abnormal load, FASTN alerts the jobsite to a potential operator fall or ejection.
Collecting and analyzing data: All
events are recorded by the FASTN control unit and provide key data for safety management.
This data can be integrated into dashboards and KPIs, contributing to identifying good or bad harness usage on site. FASTN helps construction companies manage safety on the site and implement appropriate prevention and training campaigns.
Falls: the leading cause of mortality when using an aerial work platform Falling from height has remained the leading cause of death in aerial work platform accidents for many years. From 2015 to 2023, IPAF recorded over 175 deaths*.
Haulotte, haulotte@haulotte.com, www.haulotte.com
Here at Niftylift Ltd, we’ve always prided ourselves on pushing the boundaries of what’s possible in the world of aerial work platforms. Our commitment to innovation and compact design has led us to a groundbreaking discovery that seems straight out of a Marvel Avengers movie.
In an extraordinary leap in technology—and with a bit of inspiration from Ant-Man—we’re thrilled to announce our latest product line: The MicroNiftys, powered by none other than reallife Pym particles!
When science meets superhero ingenuity
In our relentless quest to make our lifts even more compact and versatile, our R&D team stumbled upon a batch of Pym particles.
Yes, you read that right—the very particles used by Dr. Hank Pym himself to shrink or enlarge anything they touch.
After months of rigorous testing (and ensuring no ants were harmed in the process), we’ve successfully harnessed this technology to shrink our Niftylifts to micro proportions.
MicroNiftys: small size, giant performance
Imagine carrying a Niftylift in your backpack, zipping through congested urban jungles, or navigating the tightest of industrial corridors. With MicroNiftys, that’s not just possible—it’s your new reality. These pintsized powerhouses can be easily
transported in the palm of your hand and resized on the spot to tackle any job, no matter the height or complexity.
Gone are the days of worrying about transportation logistics or manoeuvring through narrow passages.
Our MicroNiftys ensure that you’re always ready for action, just like your favourite Avengers.
And when it’s time to get to work, a simple press of a button is all it takes to bring them back to full size, ready to reach new heights (literally).
In the spirit of Ant-Man, we’ve proven that great power can indeed come in small packages.
While our MicroNiftys might be small enough to dodge a raindrop, their performance is anything but minuscule.
This April, we’re celebrating not just our sense of humour but also our unwavering dedication to innovation.
Our MicroNiftys are a testament to Niftylift’s ongoing mission to offer unparalleled compactness and
efficiency. They provide a solution that’s about overcoming physical barriers and breaking the limits of what’s possible in aerial work platforms.
Join the miniature revolution
So, as we roll out our MicroNiftys, we invite you to think smaller to achieve bigger. Whether you’re navigating the quantum realm or just trying to squeeze through a tight spot on the job site, remember: with Niftylift, the only limit is your imagination (and maybe the laws of physics, but we’re working on that).
Stay tuned for more updates on our miniaturized marvels. And remember, in the world of miniature aerial work platforms, it’s not the size of the Niftylift in the fight; it’s the size of the fight in the Niftylift! Disclaimer: Please check the date before contacting customer service to order your very own MicroNifty. Our customer service team is equipped to handle many queries, but requests for Pym particles might just shrink their patience.
Niftylift Ltd, smaher@niftylift.com, www.niftylift.com
LevelRight is DICA’s newest solution for operators of boom trucks, cranes, concrete pumps, jacking applications, and other equipment with outriggers that must be operated in a level condition.
LevelRight users can easily adjust the overall angle from 0-10 degrees and adjust in two planes up to 5 degrees. The 24-inch diameter LevelRight will accept up to a 20-inch square or 24-inch round outrigger float. It has a rated capacity of 350,000 lbs.
“We first introduced a prototype of LevelRight at CONEXPO-CON/AGG last year, and the response was significant,” said Kris Koberg, DICA’s CEO. “It’s common for an operator to have to set up on uneven terrain, but on a hard surface where it’s more difficult to manipulate the ground under the outrigger, LevelRight is the perfect solution to ensure a safe and level set up.” LevelRight is made of SafetyTech
material with DICA SafetyTexturing on the top and bottom surfaces. It also has a built-in bubble level to provide operators with confirmation when they have a level surface under their equipment’s outriggers.
“With LevelRight, we wanted to make the right way of doing things an easy way of doing things. For crane applications, using supporting materials such as outrigger or crane pads as the base layer is required to distribute the load. LevelRight fits between the pad and outrigger float to ensure the outrigger is placed on a flat and level surface,” said Kerry Koberg, Sales Director at DICA.
“In situations where cribbing blocks are needed for extra height,
LevelRight can be used as the base under ProStack Cribbing Blocks to ensure the blocking is on a level surface,” he said.
A pre-production demo debuted at the 2024 World of Concrete Show. The response from Scott Sutherland, the Canadian Concrete Pumper, with AJ’s Concrete Pumping in Vancouver, British Columbia: “Problem solved, just like that! No more wedges, no more digging, no more shoveling. This is brilliant for leveling in two different axes.” Production units are now available for shipping.
Genie’s next generation TraX™ system has been redesigned to simplify maintenance while delivering the same “no compromises” performance customers have experienced from the market leading four-point track system.
Genie® TraX is available as a factoryinstalled option on four popular boom lifts — two with standard lifting capacity (Z®-62/40 and S®-80 J) and two with Xtra Capacity™ lifting capacity (S-45 XC™, and S-65 XC). This new Genie system is the only tracks system in the industry that can be fitted to highcapacity machines. By allowing the XC machines to maintain their dual capacity, the new Genie TraX increases the flexibility of the lifts, because it can be used on jobsites that require both additional lifting capacity and work on sensitive surfaces.
Four independent tracks ensure
smooth break-over on rough terrain.
Oscillating axles and the ability to swivel up and down by 22° enable the tracks to grip and climb over obstacles in the most extreme working conditions.
The redesigned TraX system comes in two sizes: a small frame (for S-45 XC machines) and a large frame (for S-65 XC, Z-62/40, and S-80 J lifts).
With 50% fewer serviceable parts than other track systems on the market, inspections are streamlined.
Aside from the rubber track and the frame, all parts are common between the small and large TraX systems, reducing parts inventory requirements for rental companies.
In addition, tracks can be swapped for tyres (time to swap varies depending on the model), providing greater flexibility in terms of resale options.
Additionally, Genie will offer aftermarket upgrade kits to convert 2024 and newer S-65 XC and Z-62/40 boom lift models from wheels to TraX (some restrictions apply). These kits will launch
at a future date.“Customers in telecommunications, oil and gas industries, quarries, tree care, and construction have been using TraXequipped boom lifts for more than 15 years in all seasons and terrains — from rocky slopes to sand and gravel pits, in snow and ice,” said Sean Larin, Global Product Director, Booms. “Redesigned TraX-equipped boom lifts have been rigorously tested in these environments and exceeded Genie’s high standard for durability and reliability,” he said.
Genie TraX systems offer an average of 72% less contact pressure compared with standard tire options. This is due to their broader weight distribution, which may provide more options to operate TraX boom lifts on sensitive, lowweight floors or in muddy terrain without placing mats or cribbing to support the machine’s weight.
The next generation Genie TraX System will be available for delivery globally in Q1 2024.
Goscor Access Solutions, +27 (0 11 393 6437, accesssolutions@goscor.co.za, www.goscoraccesssolutions.co.za
Uplifter PRO no device has more Uplifter in it!
Uplifter has been the undisputed market leader in the field of glass and window installation for more than 20 years and regularly impresses with high-end special solutions and far-reaching innovations for trade and industry.
From the initial idea to customerspecific production, everything is realized at the company’s own development and production site in Nabburg, Bavaria. From there, all machines and devices are shipped all over the world, even to Japan or Australia. The healthy expansion policy of company founder and Managing Director Martin Lobinger is bearing fruit and he will continue
to invest in qualified specialist staff and modern production halls in order to keep up with the growing volume of orders.
There is more groundbreaking news from the medium-sized company in the beautiful Upper Palatinate. Lobinger proudly announced: “Just in time for FENSTERBAU FRONTALE, the world’s leading trade fair for windows, doors and façades, his Uplifter team - THANK YOU TO ALL! - and the company can present Uplifter PRO there for the first time!”
Uplifter PRO - an interestingsounding name with unimaginable potential.
Two prototypes from this series celebrated their premiere at the trade fair in Nuremberg and could be intensively examined and of course tested on site - with a great response.
What actually distinguishes these prototypes so that they can call themselves Uplifter PRO?
The principle behind Uplifter PRO is easy to explain: PRO means
two devices in one machine! The principle “Stay as individual as your requirements on the construction site” is the basis of all Uplifter developments and so it is not surprising that Uplifter PRO is set to shake up the market!
Premiere prototype 1: This ground-breaking innovation has so far only been offered by Uplifter:
GW600 PRO = Glassworker with up to 600 kg load capacity + detachable, separately usable vacuum cup UPG600 with up to 600 kg load capacity
Two machines in one - both completely independent and fully usable! With the GW600 PRO, you get one machine, but double the benefits. Whether you need a small crane or a vacuum suction cup with a lifting capacity of up to 600 kg, with the GW600 PRO you have both and are always ideally equipped and as flexible as possible for every construction site and its requirements.
Transporting and assembling a
wide range of elements is child’s play with the GW600 PRO. Thanks to the patented quick-change system, the vacuum cross can be reattached to the glassworker in just a few seconds. All functions of the vacuum cross, such as turning, swiveling, side shifting and tilting, can be controlled directly via the small crane. The load arm can also be mounted in just a few minutes. For maximum operating convenience, two radio remote controls are included in the scope of delivery, one for the small crane and one for the vacuum cup.
Premiere prototype 2:
UPT350 PRO = assembly aid with a load capacity of up to 350 kg + detachable, separately usable UPG350 vacuum cup with a load capacity of up to 350 kg
The UPT350 PRO is the ideal transport and assembly aid for glass panes, doors or panels. This innovative device has been specially
developed for window installation and for use with fire doors. For fans of tool-free installation, the UPT350 PRO is the machine of choice: the UPG350 glass suction cup can be fitted and removed completely without tools. This is done within seconds; even transfer to a crane is possible without any problems, as the load arm remains on the
UPG350. The progressive principle of being able to use all devices as universally as possible stands for the significant innovative strength of Uplifter and its entire team.
Uplifter, matthias.minich@uplifter.com, www.uplifter.com
Around 250 kilometres north of the Arctic Circle, Liebherr is part of the largest construction project in Greenland’s history. Munk Civil Engineering is carrying out dredging work for two airport projects with the HS 8200 duty cycle crawler crane. The Arctic conditions and logistics pose a particular challenge.
Two airport projects are being realised in the coastal towns of Ilulissat and Nuuk in the western part of Greenland. To date, only propeller-driven aeroplanes could land here. The new airports will make it possible for larger aircraft to fly directly from the European or American mainland.
The new runway in Ilulissat is partly in the sea. A thick layer of clay sediment has to be removed from the seabed before it can be backfilled. Otherwise, settlement may occur over time. The Danish company Munck Civil Engineering, the main contractor for the two projects, is using the HS 8200 duty cycle crawler crane from Liebherr for this dredging work. “In one day shift, our extraction rate can be up to 1,000 m³ of excavated clay material,” explains construction manager Kevin van den Bos.
The 200-tonne duty cycle crawler crane is operating with a 35-metre long boom and a clamshell grab with a capacity of 3.5 m3. To achieve high productivity, the HS 8200 is equipped with Liebherr’s
Dredging Assistant, which shows the operator the position and fill level of the grab, the number and duration of work cycles or the handling performance in real time. The system also makes it easier to calculate the amount of material needed to fill the area for the runway. Munck Civil Engineering finds all the rock material used for this within the project boundaries.
“In total, we have to drill and blast around 5.5 million cubic metres of rock material. We then transport this to the construction section so that we can subsequently build a 2-kilometre long runway.” After dredging, the duty cycle crawler crane is equipped with a stone grab to place stones along the new runway as part of the coastal protection programme.
The average temperature in this region in summer is plus 8 degrees Celsius. In winter, it can drop to minus 35 degrees. “It is very important for us to complete the dredging work before the ice spreads in the bay and makes our
work impossible.” The duty cycle crawler crane was supplied with the Liebherr cold package to ensure that it is also operational in these very cold climatic conditions.
In addition to the icy conditions, the logistics are a major challenge. The region is only supplied by a ship once a week and also brings parts and equipment for Munck Civil Engineering. A large store and the ability to repair everything itself is therefore particularly important for the company in this remote region.
Munck Civil Engineering operates the HS 8200 six days a week in ten-hour shifts. Kevin van den Bos is delighted with the good performance of the duty cycle crawler crane, “The machine runs really well and has exceeded our expectations. We will finish even earlier than anticipated. That is really positive.”
Liebherr Africa, +27 (0) 11 365 2000, info.laf@liebherr.com, www.liebherr.com
Cranes (Pty) Ltd has been appointed as the official authorised dealer for Hoeflon
This partnership marks a significant milestone for us, as we bring to our customers this cutting-edge technology and innovation from Hoeflon, a renowned designer, manufacturer, and supplier of compact cranes, Based in Barneveld, the Netherlands.
Hoeflon Compact Cranes, also known as mini cranes, spider cranes, or compact crawlers, are revolutionising the way heavy lifting is done in confined or hard-to-access spaces.
These compact cranes are ideal for tasks such as placing glass with precision or accurately positioning steel beams and pipes. What sets Hoeflon Cranes apart is their exceptional lifting capacity, being the only compact crane capable of lifting more than its own weight. The possibilities with Hoeflon Compact Cranes are truly endless!
Trusted by professionals worldwide, the Hoeflon series perfectly complements our existing range of used and refurbished mobile cranes. This collaboration allows us to offer our customers in South Africa/Africa access to top-of-the-line compact crane solutions that cater to a diverse range of industry and lifting requirements.
At Fastlift Cranes, we take pride in being a leading supplier of quality used cranes in South Africa/Africa. This new partnership with Hoeflon further solidifies our commitment to providing our customers with the best-in-class lifting equipment and solutions.
We are excited about the opportunities that this partnership brings and look forward to serving our customers with the exceptional performance and reliability of Hoeflon Compact Cranes. Join us as we continue to elevate the standards in the crane industry in South Africa/Africa and beyond.
For more information about our range of Hoeflon Compact Cranes and how they can benefit your operations, contact us at Fastlift Cranes. Experience the power and versatility of compact lifting with Hoeflon!
Assuring you of our best service and attention at all times.
Eazi Access is excited to announce that we will be exhibiting at this year’s SAPICS Conference & Exhibition which will be taking place at Century City Conference Centre in Cape Town from the 9th - 12th of June 2024.
The theme for the 46th Annual Conference is Supply Chain Metamorphosis, and this is relevant in these times as we see Supply Chains evolving to new markets and new technologies becoming available in the market.
Eazi Access has been a longstanding corporate member with the professional body for Supply Chain Management and is proud to be associated with SAPICS which has worked to elevate, educate, and empower the community of supply
chain professionals in South Africa and across the continent for the past 46 years.
The conference will see hundreds of delegates and exhibitors from around the world gather to network, learn, and share knowledge through panel discussions, presentations, exhibitions, workshops, and case studies presented by local and international experts and industry leaders with the purpose of advancing world class supply chain
practices in South Africa.
According to Tralone Lindiwe Khoza, PR & Communication Specialist at Eazi Access, “We are excited to announce that Karl Thorington, Eazi Access Chief Business Development Officer will be speaking at the SAPICS 2024 conference. Karl comes with a wealth of knowledge and expertise, which he will be sharing at the conference. He has over thirty years operational and strategic experience in Logistics, Manufacturing and Supply Chain from blue chip and renowned US multinational companies. In his senior leadership role, he has looked after end-to-end supply chain design and solutions in the FMCG beverage, pharmaceutical, personal care and cosmetics industry and cold chain frozen foods, with his previous role in Eazi Access being the Chief Operations Officer.”
According to Karl Thorington, Eazi Access Chief Business Development Officer, “I have attended the SAPICS conference over a period spanning nearly twenty years and have watched it evolve in content and format, from the early days where the primary exhibitors ranged from
truck rental companies, warehouse design solutions companies, material handling equipment rental and sales and consultant services to technological enhancements that are data driven to improve productivity, efficiencies and enhance the customer experience while understanding their operational effectiveness.”
Thorington explained that customers have become more savvy through different digital platforms such as LinkedIn and other numerous technological sites which provides insight for their businesses, however there is also a great opportunity to show them how they can improve and enhance their operations and in tandem benefit their customers.
“The race is on to demonstrate and deliver on promises that have historically been pitched by consultants to now being pitched by regular rental and service provider companies,” reiterated Thorington.
Thorington’s views on what customers can expect from Eazi Access at this year’s SAPICS event
includes, “Customers expect greater uptime, lower running costs, greater reliability through service and maintenance from the solutions they procure, so that they can focus on their core businesses. They want proof that you have delivered on what you have promised you would do, or you risk losing the contract. Our innovation in product investment and solutions aims to deliver on this.”
As a Work-At-Height and Material Handling Solutions partner of choice, Eazi Access has been ranked number 1 in Africa for Access Platform and Material Handling rental, sales, and service. Eazi Access provides a variety of innovative safe solutions which cater for the supply chain industry, which will be showcased at the conference. In 2019, Eazi Access walked away with the Best Multiple Exhibition Stand at the SAPICS Annual Conference. In many ways Eazi Access over the past 21 years has emulated the same journey as SAPICS, it has evolved from a rental company to a sales company, to sales and service and now to a
With Kempston Controls Manufacturing
solutions company, across various industries.
“We have moved from providing simple rental options to complex solutions by understanding the customers problems and working with them to solve them through our industry expertise in a safe, effective and productive manner. We deliver on what we say we will do and through strategic alliances with global companies like DP World, we now have the means to extend our technology into our trucking and transport solutions, including field service vehicles, to delight our customers. Like SAPICS, over the years, we too have evolved to meet our ever-changing customer needs because if we stand still, we go backwards”, explained Thorington.
We look forward to networking and exchanging knowledge with delegates across the supply chain sector at this prestigious event.
Eazi Access, +27 (0) 87 086 5039, tralone.khoza@eazi.co.za, www.eazi.co.za
Umholi
T: +27 (0) 11 914 2210/11
F: +27 (0) 11 914 2209
E: umholi@umholi.co.za
W: www.umholi.co.za
Kempston Controls
T: +27 (0) 140 776 2888
E: holyhead@kempstoncontrols.co.uk
W: www.kempstoncontrols.co.uk
Condra Cranes
T: +27 (0) 11 776 6000
E: sales@condra.co.za
W: www.condra.co.za
Cooper & Cooper Group
T: +27 (0) 11 493 4355
E: info@coopergroup.co.za
W: www.coopergroup.co.za
Palfinger Africa
T: +27 (0) 11 608 3670/1/2/3/4
E: sales@palfingerafrica.co.za
W: www.palfinger.co.za
Johnson Crane Hire
T: +27 (0) 11 455 9222
E: PeterY@jch.co.za
W: www.jch.co.za
Liebherr Africa
T: +27 (0) 11 365 2000
E: info.laf@liebherr.com
W: www.liebherr.com
True Lift services
T: +27 (0) 83 710 5390
E: Trueliftservices@gmail.com
W: www.trueliftservices.za.live
Bell Equipment Southern Africa
T: +27 (0) 11 928 9846
E: susanmy@bell.co.za
W: www.bellequipment.com
Jungheinrich
T: +27 (0) 10 596 8460
E: info@jungheinrich.co.za
W: www.jungheinrich.co.za
FB Cranes
T: +27 (0) 11 902 3271
E: info@fbcranes.co.za
W: www.fbcranes.co.za
Kempston Controls
T: +27 (0) 140 776 2888
E: holyhead@kempstoncontrols.co.uk
W: www.kempstoncontrols.co.uk
Morris Material Handling SA
T: +27 (0) 11 748 1000
F: +27 (0) 11 748 1093
E: sales@morris.co.za
W: www.morris.co.za
Rhino Lifting Maintenance
T: +27 (0) 16 971 2348/49
E: sales@rhinolm.co.za
W: www.rhinolm.co.za
Yale Lifting Solutions
T: +27 (0) 11 794 2910
F: +27 (0) 11 794 3560
E: crm@yalelift.co.za
W: www.yale.co.za
Yale Lifting Solutions
T: +27 (0) 11 794 2910
F: +27 (0) 11 794 3560
E: crm@yalelift.co.za
W: www.cmco.com
AND CABLE REELS
DEMAC SRL
T: +39 (0)2 9784488
F: +39 (0)2 97003509
E: info@demac.it
W: www.demac.it
Econo Flex
T: +27 (0) 16 933 5705
E: econoflex@econoflex.co.za
W: www.econoflex.co.za
Econo Flex
T: +27 (0) 16 933 5705
E: econoflex@econoflex.co.za
W: www.econoflex.co.za
GregBev Enterprise
C: +27 (0) 82 854 5143
C: +27 (0) 72 395 4342
T: +27 (0) 53 285 0842
E: admin@gregbev.co.za
W: www.gregbev.co.za
GregBev Enterprise
C: +27 (0) 82 854 5143
C: +27 (0) 72 395 4342
T: +27 (0) 53 285 0842
E: admin@gregbev.co.za
W: www.gregbev.co.za
Yale Lifting Solutions
T: +27 (0) 11 794 2910
F: +27 (0) 11 794 3560
E: crm@yalelift.co.za
W: www.cmco.com
IY Safety & Inspections
T: +27 (0) 82 773 7019
C: +27 (0) 82 956 3176
Morris Material Handling SA
T: +27 (0) 11 748 1000
F: +27 (0) 11 748 1093
E: sales@morris.co.za
E: bianca@iysafetyinspection.co.za W: www.iysafetyinspection.com LOAD
W: www.morris.co.za 3 60 5 Services
T: +27 (0) 72 207 7443
T: +27 (0) 64 687 7270
E: sales@3605services.co.za W: www.3605services.co.za
Econo Flex
T: +27 (0) 16 933 5705
E: econoflex@econoflex.co.za
W: www.econoflex.co.za
GregBev Enterprise
C: +27 (0) 82 854 5143
C: +27 (0) 72 395 4342
T: +27 (0) 53 285 0842
E: admin@gregbev.co.za
W: www.gregbev.co.za
Integrate Lifting Specialist Africa
T: +27 (0) 12 141 3615
T: +27 (0) 86 571 4387
E: info@integrateliftingsa.com
W: www.integrateliftingsa.com
IY Safety & Inspections
T: +27 (0) 82 773 7019
C: +27 (0) 82 956 3176
E: bianca@iysafetyinspection.co.za
W: www.iysafetyinspection.com
Margisia Lifting Solutions
T: +27 (0) 14 763 1849
C: +27 (0) 83 992 2222
E: info@margisia.co.za
W: www.margisia.co.za
Rhino Lifting Maintenance
T: +27 (0) 16 971 2348/49
E: sales@rhinolm.co.za
W: www.rhinolm.co.za
J Express Crane Services
T: +27 (0) 11 864 8402
M: +27 (0) 83 425 5535
F: +27 (0) 11 864 8408
E: jexpress@telkomsa.net
Kempston Controls
T: +27 (0) 140 776 2888
E: holyhead@kempstoncontrols.co.uk
W: www.kempstoncontrols.co.uk
Levi’s Trio Engineering
T: +27 (0) 11 907 9258
F: +27 (0) 86 742 9410
E: admin@levistrio.co.za
W: www.levistrio.co.za
Morris Material Handling SA
T: +27 (0) 11 748 1000
F: +27 (0) 11 748 1093
E: sales@morris.co.za
W: www.morris.co.za
Shosholoza Consulting
T: +27 (0) 14 495 1994
C: +27 (0) 79 391 2990
E: info@shosholoza.africa
W: www.shosholoza.africa
Yale Lifting Solutions
T: +27 (0) 11 794 2910
F: +27 (0) 11 794 3560
E: crm@yalelift.co.za
W: www.cmco.com
Cooper & Cooper Group
T: +27 (0) 11 493 4355
E: info@coopergroup.co.za
W: www.coopergroup.co.za
Liebherr Africa
T: +27 (0) 11 365 2000
E: info.laf@liebherr.com
W: www.liebherr.com
Chimaera
T: +27 (0) 84 506 1209
E: ndt@chimaera.co.za W: www.chimaera.co.za
By Carpel SRL - Italy
T: + 39 (0) 39 532 0952
F: + 39 (0) 39 532 0825
E: info@bycarpel.it
W: www.bycarpel.it
Condra Cranes
T: +27 (0) 11 776 6000
E: sales@condra.co.za
W: www.condra.co.za
Econo Flex
T: +27 (0) 16 933 5705
E: econoflex@econoflex.co.za
W: www.econoflex.co.za
HP Cranes Consulting
T: +27 (0) 11 740-9725/28/33
F: +27 (0) 11 740 8416
E: admin1@hpcranes.co.za
W: www.hpcranes.co.za
IY Safety & Inspections
T: +27 (0) 82 773 7019
C: +27 (0) 82 956 3176
E: bianca@iysafetyinspection.co.za W: www.iysafetyinspection.com
J Express Crane Services
T: +27 (0) 11 864 8402
M: +27 (0) 83 425 5535
F: +27 (0) 11 864 8408
E: jexpress@telkomsa.net
Kempston Controls
T: +27 (0) 140 776 2888
E: holyhead@kempstoncontrols.co.uk
W: www.kempstoncontrols.co.uk
KL Cranes and Lifting Equipment
T: +267 397 4853
C: +267 71344438
E: annelieze@klcranesbot.com
W: www.klcranesbot.com
Morris Material Handling SA
T: +27 (0) 11 748 1000
F: +27 (0) 11 748 1093
E: sales@morris.co.za
V & S Automation/Cranes
T: +27 (0) 10 442 7478
C: +27 (0) 82 787 2343
E: victor@vsautomation.co.za
W: www.vandsautomation-cranes. co.za
ACROW
T: +27 (0) 11 824 1527
E: info@acrow.co.za
W: www.acrow.co.za
Lifting Placements
C: +27 (0) 61 063 1687
E: info@liftingplacements.co.za
W: www.liftingplacements.co.za
Kempston Controls
T: +27 (0) 140 776 2888
E: holyhead@kempstoncontrols.co.uk
W: www.kempstoncontrols.co.uk
T: +39 (0)39 5951 1277 E: giovenzana@giovenzana.com W: www.giovenzana.com
T: +27 (0) 11 864 8402
C: +27 (0) 83 425 5535
F: +27 (0) 11 864 8408
E: jexpress@telkomsa.net
W: www.morris.co.za J Express Crane Services
jexpress@telkomsa.net
Haggie
T: +27 (0) 11 601 8400
E: distribution@haggie.co.za
W: www.scaw.co.za
STEEL WIRE ROPES
CB Lifting
T: +27 (0) 22 719 1437
E: info@cblifting.co.za
W: www.cblifting.co.za
Haggie
T: +27 (0) 11 601 8400
E: distribution@haggie.co.za
W: www.scaw.co.za
Umholi
T: +27 (0) 11 914 2210/11
F: +27 (0) 11 914 2209
E: umholi@umholi.co.za
W: www.umholi.co.za
Combi Lift
T: +27 (0) 11 900 8010
E: victor@solutions-4u.co.za
W: www.combilift.co.za
Kemach Forklifts
T: +27 (0) 11 826 6710
E: info@kemachjcb.co.za
W: www.kemachjcb.co.za
Manitou
T: +27 (0) 10 601 3000
E: info.msa@manitou-group.com
W: www.manitou.com
Liebherr Africa
T: +27 (0) 11 365 2000
E: info.laf@liebherr.com
W: www.liebherr.com
MH Dawood Plant Services
T: +27 (0) 11 496 1007
F: +27 (0) 11 496 1198
E: info@mhdawood.co.za
W: www.mhdawood.co.za
LMI Academy
T: +27 (0) 11 475 5876
E: info@lmi-academy.co.za
W: www.lmi-academy.co.za
MCLS Training
T: +27 (0) 82 506 5899
T: +27 (0) 73 089 0624
E: sinky@mclstraining.co.za
W: www.mclstraining.co.za
Phakamisa Safety Consultants
T: +27 (0) 11 462 9620/1
F: +27 (0) 11 462 9620
E: potto@icon.co.za
W: www.phakamisasafety.co.za
Crane Clinic
T: +27 (0) 11 902 7379
E: reception@craneclinic.co.za
W: www.craneclinic.co.za
Palfinger Africa
T: +27 (0) 11 608 3670/1/2/3/4
E: sales@palfingerafrica.co.za
W: www.palfinger.co.za
Smith Capital Equipment
T: +27 (0) 11 873 9830
E: mail@smithcapital.co.za
W: www.smithcapital.co.za
Dymot Engineering
T: +27 (0) 11 970 1920
F: +27 (0) 11 970 1979
E: pa@dymot.co.za
W: www.dymot.co.za
Unrivaled Reliability
Boom Length
Best in-class reach
Smart Chart
Expands the customary circular work area to take advantage of the maximum available lifting capacity
AML-E
Advanced control system with enhanced features
Unique Quality
Reduced Fuel Consumption
• Fuel Monitoring
• Eco Mode System
• Automatic Pump Disconnect
Take a closer look
Discover how Tadano RT cranes deliver maximum lifting performance with unrivaled reliability.
Tadano RT cranes give your business the next-generation features you need to work safer, faster and more effectively than ever. Tadano View gives your operators a birds-eye view of the crane’s surroundings on a large, multi-function display inside the cab. Reduce fuel consumption with Fuel Monitoring, Eco Mode and Automatic Pump Disconnect. And expand the working area to get the best crane performance in any outrigger extension setup with Smart Chart.
Take a closer look at what Tadano can do for your business. Learn which models are available in your region at tadano.com.