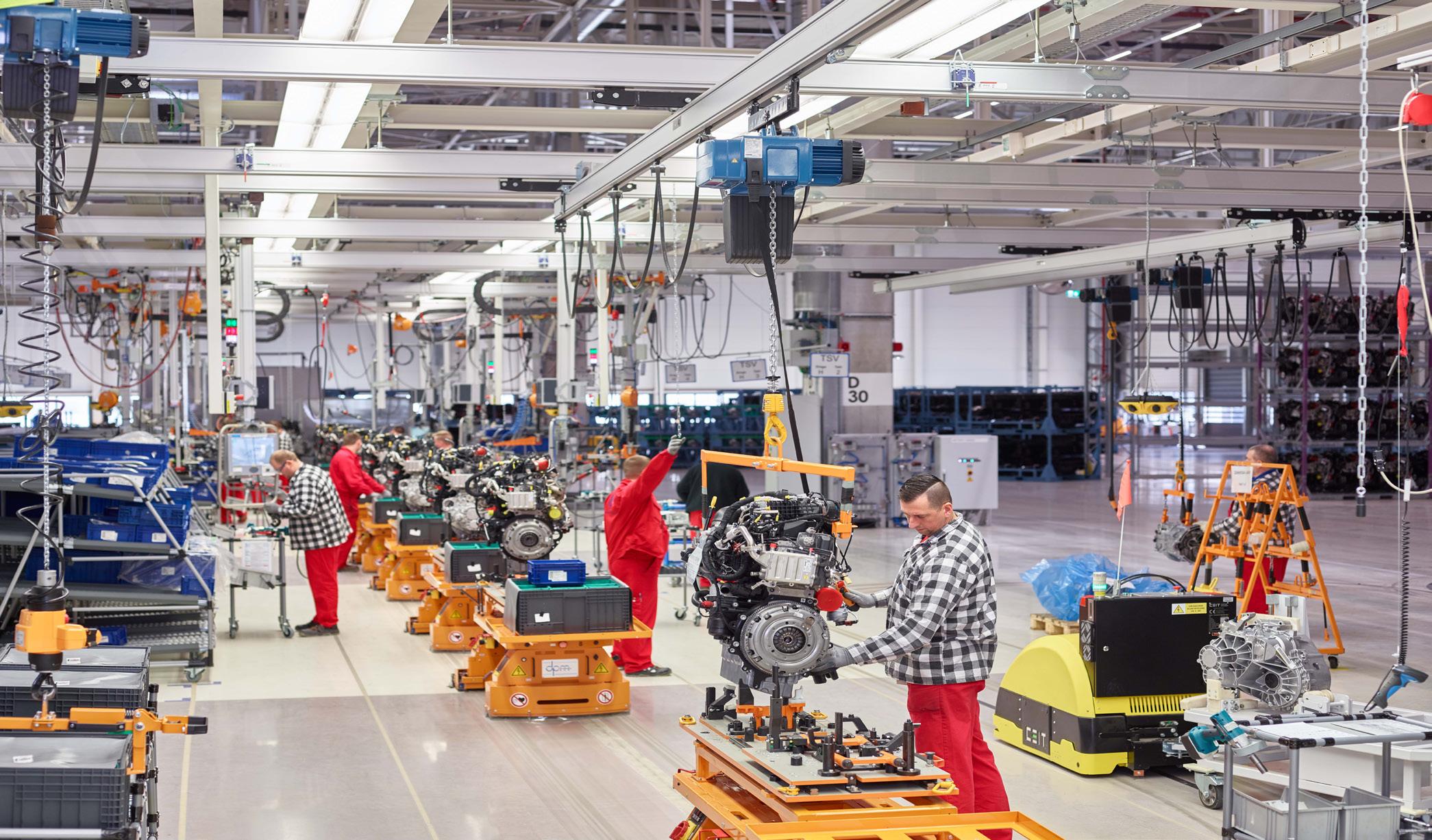
4 minute read
The importance of ergonomics in commercial vehicle production
One hundred and twenty-seven crane bridges, as well as a wide variety of hoist units, manipulators and power screwdrivers, integrated into more than six kilometres of rails in four profile section sizes – that was the scope of the KBK Aluline system that an international Demag project team planned and installed recently.
This extremely smooth-running system improves ergonomics for handling parts and is a key factor for optimised productivity throughout the entire vehicle assembly operation. The Volkswagen AG Polish plant was to manufacture the latest generation of its VW Crafter where more than 3,000 employees manufacture the vehicle and – in the integrated supplier park – many third-party components. The plant, which covers 220 hectares, is designed for an annual capacity of 100,000 light commercial vehicles and has generous workshops for the body line and vehicle assembly as well as a state-of-the-art paint line.
Heavier parts than in car production
On vehicles such as the Crafter, everything is slightly heavier and larger than in a car production line. For this reason, the handling of parts plays a much larger role. Since commercial vehicles are usually made in lower quantities than car volume models, but in larger numbers of variants, many steps in production cannot be fully automated. Due to the weight of the parts, many stations need to be served by manipulators, workplace cranes and other handling equipment. This applies throughout the entire final assembly process, which is divided up into seven production and pre-assembly sections. Parts for a number of variants are also sequenced, picked and staged in several “supermarkets”. Assembly of the VW crafter is implemented in 155 takt cycles. Components are continuously retrieved from load carriers, lifted or assembled into orders, which requires the use of corresponding lifting and transport equipment to provide the best possible ergonomics for the workers at the individual workplaces. Emil Berning, Managing Director, Konecranes and Demag (Pty) Ltd, said “The well-being of workers in large plant environments is an important factor that we at Demag pay close attention to. Our machines have been ergonomically designed in order to ensure ergonomics on the factory floor enhance the worker’s plant experience while maintaining the highest level of safety throughout the production and assembly processes”.
Demag KBK Aluline Provides Full Coverage
Volkswagen’s planners decided in favour of Demag KBK Aluline as a universal system to be used throughout the assembly operation.
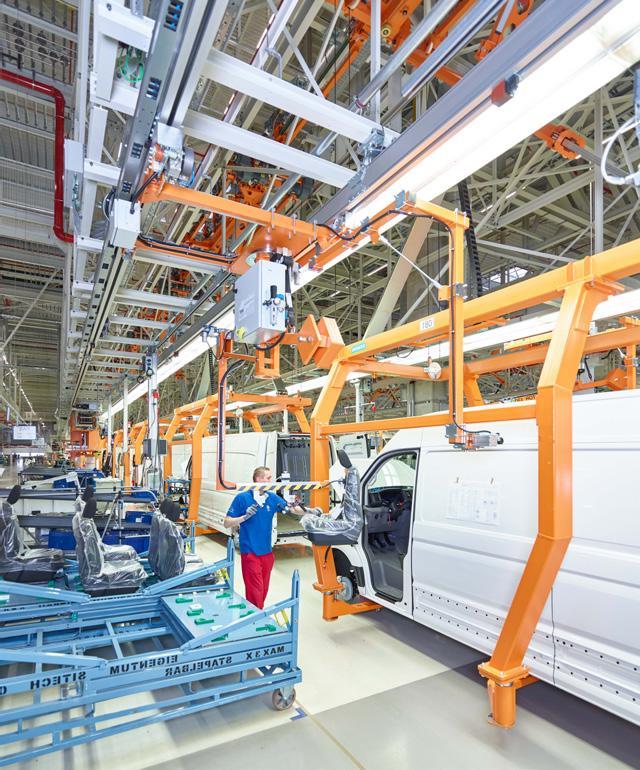
The Demag KBK Aluline crane construction kit has delivered an optimum performance in the entire automotive industry for more than five decades all over the world. The Demag brand aluminium crane construction kit offers particularly smooth running characteristics and low rolling resistance. In combination with its light-weight design, these properties offer direct benefits to
every worker on a daily basis. The bright and modern appearance of the rail system also ideally matches the friendly workplace design of the new VW plant. Besides ergonomic aspects, there was a great emphasis on safety and serviceability. KBK Aluline meets both of these requirements in full due to Demag’s extensive international experience. In addition, the easily assembled and versatile modular system can be simply extended or converted so that processes and the material flow can be modified at any time. “In South Africa, the Demag KBK Aluline system has been installed in a number of our automobile manufacturing plants such as BMW, Ford and Nissan in Gauteng as well as MBSA in East London in the Eastern Cape which featured a number of extending cranes on the KBK Aluline system which provided handling capability outside of the crane runway area," said Berning. On the Polish project, Demag technicians installed more than 6,000 metres of profile-section rails for cranes and crane runways. In total, they installed 127 crane bridges for single and double-girder suspension cranes as well as a wide variety of hoists, manipulators (equipped with lifting columns, pivot arms and balancers) and tools.
For its hoist unit needs, the Demag DC range of chain hoists was selected, which are rated for load capacities between 125 and 315 kg and are used with 2 speeds or variable-speed control, depending on the application. “Every step of the manufacturing process has different handling requirements – which can be met without exception with the KBK Aluline system. This is also applicable for different height levels and types suspension: if they are needed for the horizontal mobility of conventional crane installations that are equipped with chain hoists, suspensions that have articulated joints are used. Rugged ergo suspensions that can accommodate torque and kick-up forces are used for applications with handling equipment and telescoping power screwdrivers” added Berning. Regardless of the type of use case, KBK Aluline system rails always provide optimum load capacity for their given deadweight. Four profile-section sizes make it possible to choose the right solution for the relevant application. The special plastic travel rollers provide for extremely smooth and quiet travel characteristics. This also ensures that only a little force is required to move them – for optimum ergonomics and a low physical load for the worker. Optional integrated conductor lines can eliminate the need for external power supply lines or unwanted trailing cables. The system's bright design, in combination with lighting systems, meet exacting specifications, enables each workstation to be ideally illuminated.
Konecranes,
+27 (0) 11 898 3500, richard.roughly@konecranes. com, www.demagcranes.com
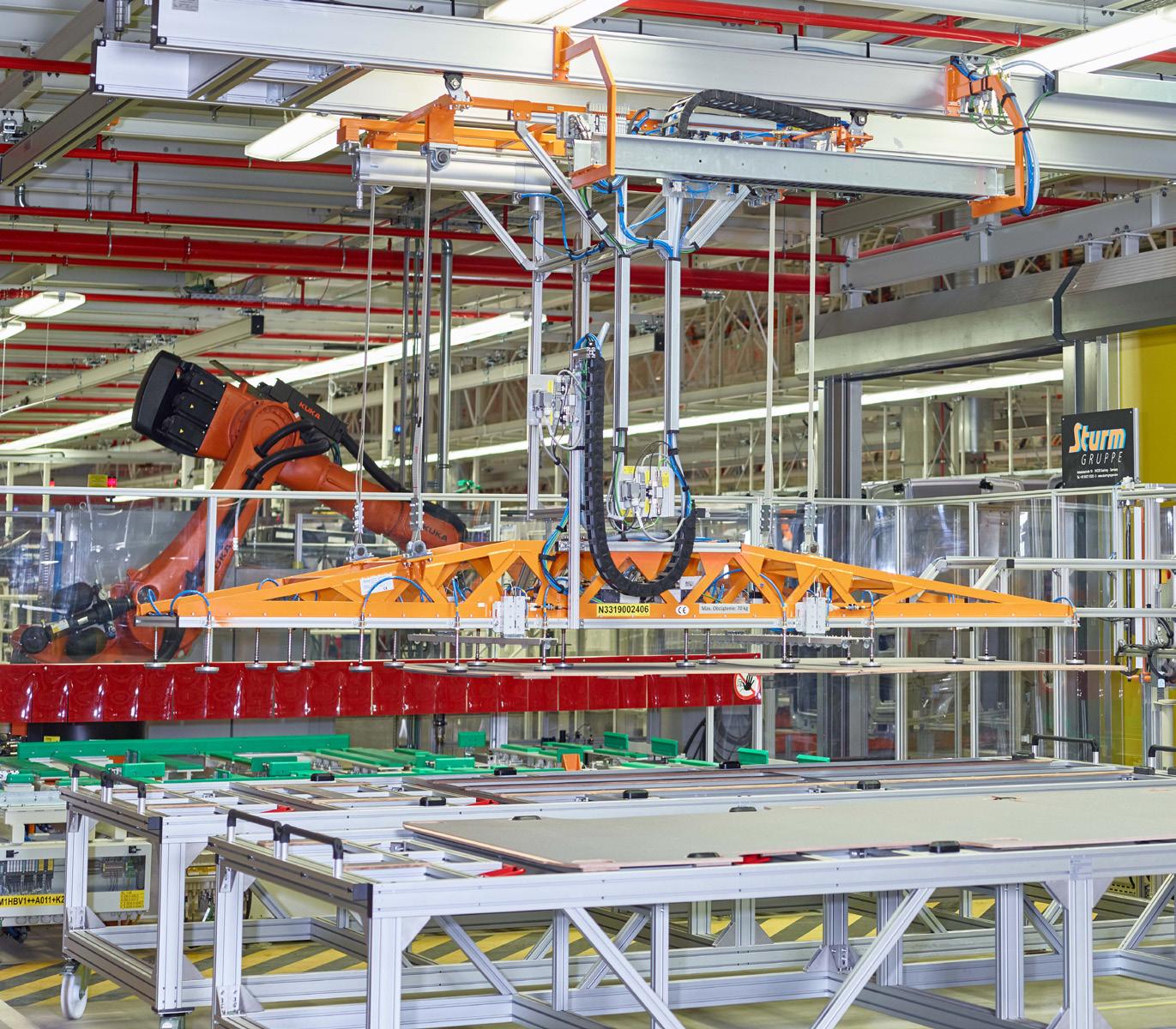
FOR ALL YOUR LIFTING SOLUTIONS

Tel 011 794 2910 Email info@yalelift.co.za (General) crm@yalelift.co.za (Sales)