
3 minute read
SPOTLIGHT ON
Port of Brisbane Bridge Beam Placement An example of good practice
In August 2017, Universal Cranes was engaged by Seymour Whyte to complete the challenging task of lifting and placing Australia’s longest pre-stressed concrete girders on the Lucinda Drive Bridge, part of the Port of Brisbane’s $110 million Port Drive Upgrade. This project provides an example of good practice in utilising safe, efficient and cost-effective lifting ancillary for the job.
Advertisement
Universal Cranes’ scope of work included planning and methodology development, lift plans and lift studies, mobilisation and operation of plant, and installation of 17 girders. They collaborated closely with Seymour Whyte, ALE Transport, and the Port of Brisbane to ensure the complex job was completed within the time constraints and budget.
To achieve Port of Brisbane’s key objectives on safety, efficiency and innovation, Quickcell Technology Products and Arup developed Quickcell Super Girders (QSG) designed to reach spans longer than traditional super T girders (which can only be built to a length of approximately 36m). The QSG design length of 46m provided a solution to overcome a major
project risk associated with the presence of underground utilities, specifically a major Energex power line responsible for suppling the entire port area.
To lift this pioneering girder technology, Universal Cranes utilised an in-house custom designed lattice boom spreader bar with a Manitowoc M16000 and MAX-ER Superlift component.
The crawler was selected for its lifting capacity in combination with the MAX-ER wagon. The boom configuration used was 54m Main Boom (58 HL) with 30m Mast (No. 59A). There was 150.59t of crane counterweight and 54.43t Carbody Counterweight. The MAX-ER was set at 15m radius with the maximum 231.97t of counterweight on the wagon.
The spreader bar was designed in-house, using spare boom sections from Universal Cranes’ fleet of 110t Manitowoc M12000 Crawler Cranes and fabricated end sections. The result was a light weight and strong spreader system that facilitated safe and cost-effective lifting and placement of the record length girders.
The spreader bar used a conventional sling and shackle arrangement for Span 1 and Span 2 of the girders, which were the heaviest and longest of the girders installed (Figure 1). A total length of 42.52m with a Safe Working Limit of 160t
Figure 1: Rigging Arrangement – Span 1 & 2 Girders

was created using 3 x 12m sections, 1 x 3m section, and 2 x end sections. To keep the mass of the rigging down as much as possible, a combination of round slings and twin path slings of various lengths were used, joined together with bow shackles. The lattice boom design enabled quick re-configuration by removing 8 pins to replace or remove a section(s). The spreader could also be used with or without an equaliser plate option (Figure 2). This project used the equaliser plates, distributing the load evenly between the lift points on the girder.
The bespoke spreader bar design weighed 5t (10t with the rigging), which reduced the total load mass by half when compared with using a conventional modular spreader bar.
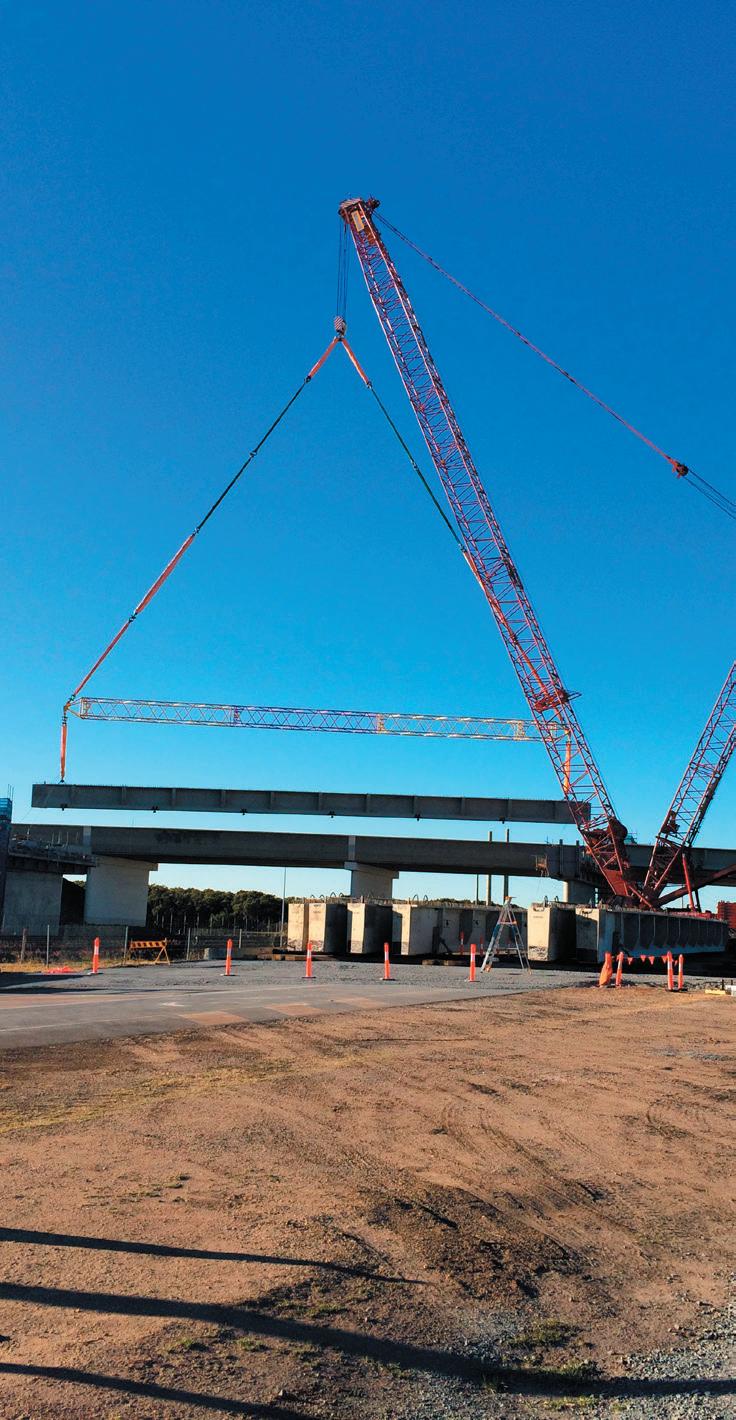
120t SHACKLE
EQUALISER PLATE
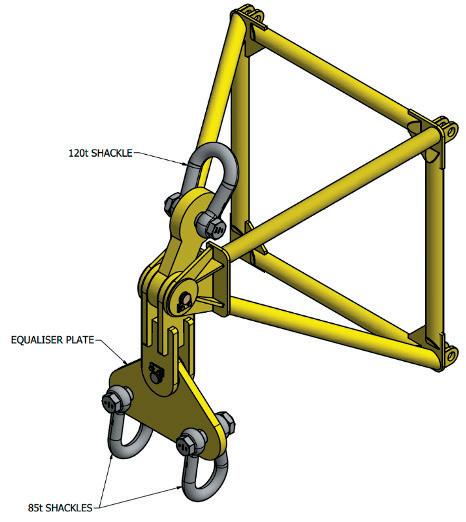
85t SHACKLES
Figure 2: Lattice Boom Spreader End This enabled Universal Cranes to keep the required crane capacity using the M16000 with MAX-ER Superlift component.
All bridge girders were lifted into place incident free, within budget, and on schedule thanks in part to the innovative spreader bar design, resulting in a landmark, record-setting project for the longest girders ever installed in Queensland.
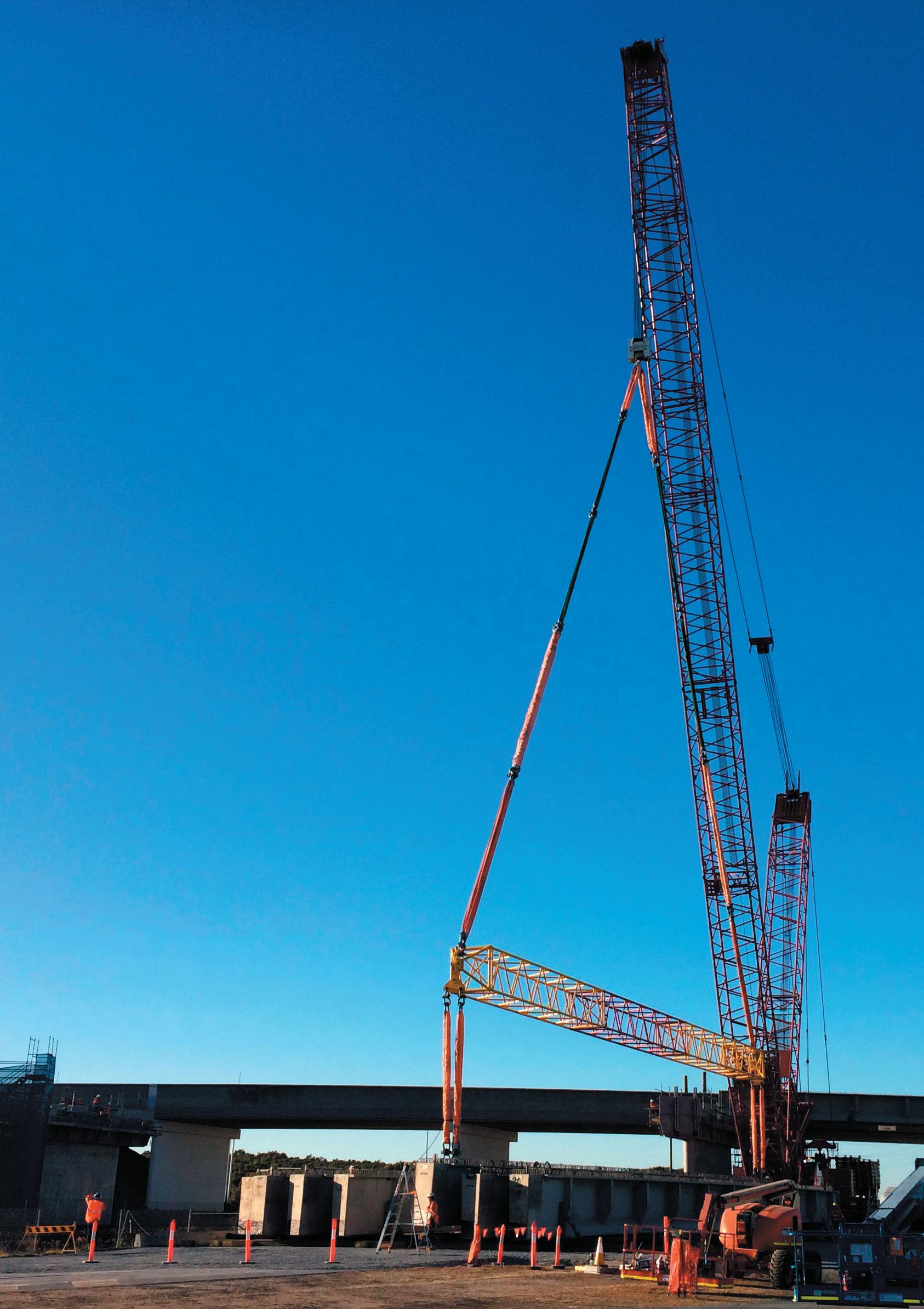